Fig. 1. Strategy for the development of intrinsically stretchable optoelectronics, based on intrinsically stretchable materials and novel fabrication techniques.
Fig. 2. Constituents of intrinsically stretchable conducting and semiconducting nanocomposites. Various (
a–
d) electronic filler materials, (
e) elastomers, and (
f) surfactants are employed to develop intrinsically stretchable conducting/semiconducting nanocomposites. Figure reproduced with permission from: (a) ref.
63, RSC Publishing, ref.
64, IOP Publishing, ref.
65, under a Creative Commons Attribution-Non Commercial 3.0 Unported License; (
b) ref.
66, 67, under a Creative Commons Attribution 4.0 International License, ref.
68, RSC Publishing; (
c) ref.
80, 82, John Wiley and Sons, ref.
81, under a Creative Commons Attribution 4.0 International License.
Fig. 3. Various conducting/semiconducting nanocomposites with intrinsic stretchability.Intrinsically stretchable conducting nanocomposites based on: (
a) CB and silica particles; (
b) SWCNTs and PU-PEDOT:PSS; (
c,
d) Ag-Au NWs and SBS; and (
e,
f) PEDOT:PSS incorporated with STEC enhancer. Intrinsically stretchable semiconducting nanocomposites based on: (
g) ZNS:Cu microparticles and PDMS; (
h) MAPbBr3 microparticles and PEO; (
i–
k) P3HT nanofibers and SEBS; and (
l) DPPT-TT nanofibers and SEBS. Figure reproduced from: (a) ref.
121, (b) ref.
150, American Chemical Society; (c, d) ref.
111, Springer Nature; (e, f) ref.
125, under a Creative Commons Attribution-NonCommercial 4.0 International License; (g) ref.
151, (i) ref.
141, (j, k) ref.
142, John Wiley and Sons; (l) ref.
143, American Association for the Advancement of Science.
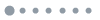
Fig. 4. Representative fabrication methods of intrinsically stretchable electronic materials.(
a) Schematic describing stencil printing method and (
b) optical image of the patterned Ag flake nanocomposite. Scale bar: 10 mm. (
c) Schematic of a soft lithography method for patterning intrinsically stretchable materials. (
d) Schematic showing inkjet printing of intrinsically stretchable materials. (
e) Schematic description of 3D printing process for intrinsically stretchable materials. (
f) Optical image of 3D-printed graphene/PDMS composite. (
g) Schematic for laser patterning of intrinsically stretchable materials. (
h) Optical image of the laser-patterned Ag NW/TPU nanocomposite, laminated on a textile with different line widths. Inset shows an SEM image of the Ag NW/TPU pattern. Scale bar: 5 mm. (
i) Digital image of a deformed textile patch. (
j) Schematics describing the photolithography process. (
k) Optical image of the Ag NW-based micropatterns on polyethylene glycol. Scale bar: 5 mm. (
l) An SEM image of the Ag NW micropatterns on a glass substrate. Figure reproduced with permission from: (b) ref.
154, under a Creative Commons Attribution-NonCommercial-NoDerivs 4.0 International License; (f) ref.
158, (h, i) ref.
160, American Chemical Society; (k, l) ref.
162, Creative Commons Attribution 4.0 International License.
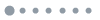
Fig. 5. Optically active materials with intrinsic stretchability.(
a) PeNCs mixed in SEBS and its (
b) PL intensity and (
c) PL quantum yield with respect to various applied strains. (
d) Intrinsically stretchable emitting layer based on perovskite microcrystals in PEO. (
e) SEM images of the layer before and during stretching with different strains. (
f) PL intensity of the layer before and during stretching with 50% strain. (
g) Photo-absorbing blended film of PBDTTTPD:P(NDI2HD-T) with intrinsic stretchability. (
h) Stress-strain curve showing the elastic modulus and (
i) toughness measurement results of the blend film. (
j) Schematic of photo-absorbing layer fabrication based on mixture of PTB7-Th, IEICO-4F, and PDMS. (
k) Schematic showing the role of PDMS for intrinsic stretchability. (
l) The crack onset strain and elastic modulus of the film with respect to different PDMS concentrations. Figure reproduced with permission from: (a–c) ref.
163, (d–f) ref.
152, John Wiley and Sons; (g–i) ref.
164, under a Creative Commons Attribution 4.0 International License; (j–l) ref.
165, John Wiley and Sons.
Fig. 6. Charge transport materials with intrinsic stretchability. (
a) Intrinsically stretchable hole transport layer of Triton X-added PEDOT:PSS. (
b) Young’s modulus and crack onset strain (COS) of pristine and Triton X-added PEDOT:PSS layer. (
c) Raman spectroscopy analysis. (
d) SEM and (
e) AFM images of the film after applying strain of 160%. (
f) Intrinsically stretchable electron transport layer based on NBR and PFN. (
g) Optical microscope image showing clean film without any cracks developed after applying 60% strain. (
h) Current-voltage characteristics of the hybrid film. Figure reproduced with permission from: (a–e) ref.
108, under a Creative Commons Attribution NonCommercial License 4.0. (f–h) ref.
166, American Chemical Society.
Fig. 7. Intrinsically stretchable conductors in optoelectronic applications. (
a) AFM image of SWCNT-based elastomeric composite electrode. (
b) Optical transmittance of the electrode. Electrical performance of the electrode during (
c) different stretching strains and (
d) cyclic stretching test. (
e) Changes in surface morphology of intrinsically stretchable electrodes fabricated by mixing PEDOT:PSS, PEO, and Zonyl with different ratios. (
f) Change in resistance of the electrodes with respect to increasing the applied strain. (
g) Stability of the optimized electrode during cyclic stretching. Figure reproduced with permission from: (a–d) ref.
168, (e–g) ref.
170, John Wiley and Sons.
Fig. 8. LECs with intrinsic stretchability. (
a) Exploded view of hyperelastic LEC based on ZnS phosphor-doped stretchable EML and stretchable hydrogel electrodes. (
b) Stress-strain curves and (
c) relative illuminance measurements of the stretchable LEC. (
d) Photographs of the hyperelastic LEC during stretching. (
e) Multipixel display and (
f) bio-inspired skin display based on the hyperelasitc LEC. Figure reproduced with permission from: (a–f) ref.
175, American Association for the Advancement of Science.
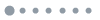
Fig. 9. LEDs with intrinsic stretchability.(
a) Structure of the intrinsically stretchable LED based on Go-soldered Ag NW/PUA composite electrodes and OXD-7 mixed white-light-emitting layer. (
b) Photographs of the stretchable LED before and during stretching. (
c) Stability of the stretchable LED after cyclic stretching tests. (
d) Chemical structure of a stretchable EML of PF-
b-OU copolymer. (
e) Photograph of the stretchable LED during stretching with 150% strain. (
f) Change in luminance of the LED after stretching cycles. (
g) Structure of the stretchable LED based on small-molecule surfactant added stretchable layers. (
h) Luminescence and current density of the stretchable LED. Change in luminescence with respect to (
j) increasing strain and (j) stretching cycles. (
k) Photographs of the stretchable LED working after poking with a ballpoint pen. Figure reproduced from: (a–c) ref.
176, American Chemical Society; (d–f) ref.
177, John Wiley and Sons; (g–k) ref.
109, under a Creative Commons Attribution NonCommercial License 4.0.
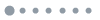
Fig. 10. PDs and PVs with intrinsic stretchability.(
a) Photograph of the intrinsically stretchable PD based on Zn
2SnO
4 NW/PDMS composite and Ag NW electrodes. (
b) Current-voltage characteristic of the PD. (
c) Photographs of the PD during stretching with different strains. (
d) Photoresponses of the PD with respect to applied strains with different amounts. (
e) Photograph of the intrinsically stretchable PD based on ZnO NW/PDMS composite and Ag NWs. (
f) Schematic showing the effect of stretching on the NW surface. Changes in (
g) on/off ratio and (
h) response time of the PD array at different stretching strains. (
i) Structure of intrinsically stretchable solar cell based on SWCNT/Ag NW-PUA composite electrodes and (PTB7)/PC
71BM photo-absorbing layer. (
j) Photographs of the solar cell before and during stretching. Stability of the stretchable solar cell in terms of (
k)
J-
V characteristics and (
l) PCE during stretching. (
m) Structure of the intrinsically stretchable solar cell based on Ag NW/TPU composite electrodes and PTB7-Th:IEICO-4F heterojunction film. (
n) Schematic showing the adhesion of photo-absorbing layer and HTL. (
o) Optical image of the photo-absorbing layer under 20% strain. (
p) PCE of the solar cell during stretching. Figure reproduced with permission from: (a–d) ref.
178, The Royal Society of Chemistry; (e–h) ref.
179, John Wiley and Sons; (i–l) ref.
180, American Chemical Society; (m–p) ref.
165, John Wiley and Sons.
Fig. 11. Intrinsically stretchable optoelectronic systems. (
a) Photographs of an intrinsically stretchable alternating current EL display stably operating before and after stretching. (
b) Photographs of the intrinsically stretchable display mounted on hand skin. (
c) Photographs showing an intrinsically stretchable display being distorted by stretching. Figure reproduced with permission from: (a, b) ref.
62, (c) ref.
182, American Chemical Society.
Materials | Conductivity | Max. stretchability | Changes in electrical performance
under applied strains | Application | Reference | Metal-based
nanomaterials | Ag NW/SBS | 12000
S cm–1 | 100% | Maintained up to 100% strain | Wearable heater | ref.110 | Ag–Au NW/SBS | 41850
S cm–1 | 266% | σ/σ0= 0.1 at 266% strain | Heater, sensors,
cardiac mesh | ref.111 | Au-TiO2 NW/PDMS | 0.63 Ω sq–1 | 150–200% | 7 Ω sq–1 at 100% strain | Neural electrode | ref.112 | Ag NW–Ag NP/SBS | 2450 S cm–1 | 220% | σ/σ0 = 4.4% at 100% strain | Strain sensor | ref.113 | Cu-Ag NW/PDMS | 2040 S cm–1 | 250–350% | ΔR/R0 = 1.46 at 150% strain | Interconnection | ref.114 | Ag flake–Ag NP/PDMS | 5695 S cm–1 | 50% | 300 S cm–1 at 50% strain | Strain sensor | ref.115 | Ag flakes/silicone adhesive | 15100 S cm–1 | 240% | 1110 S cm–1 at 240% strain | Conductor | ref.116 | Ag flake/fluorinated rubber | 6168 S cm–1 | 400% | 935 S cm–1 at 400% strain | Interconnection | ref.117 | Ag flake-EGaInPs/EVA | 8331 S cm–1 | 1000% | ΔR/R0 = 6.2 at 1000% strain | Touch sensor,
interconnection | ref.118 | Ag flake/Ecoflex | 542 S cm–1 | 1780% | ΔR/R0 = 154 at 1780% strain | Interconnection | ref.119 | Ag flake/Ecoflex | 1428 S cm–1 | 500% | ΔR/R0 = 9 at 500% strain | Interconnection | ref.120 | Carbon-based
nanomaterials | Carbon black/SBS | 0.4 S cm–1 | 200% | Maintained up to 50% strain | Pressure sensor | ref.121 | CNT/fluorinated rubber | 57 S cm–1 | 134% | 8 S cm–1 at 134% strain | Interconnection | ref.122 | CNT/fluorinated rubber | 100 S cm–1 | 118% | Maintained up to 29% strain | Active matrix organic
light-emitting diodes | ref.10 | Graphene/PDMS | 10 S cm–1 | 90% | ΔR/R0 = 1.8 at 90% strain | Interconnection | ref.123 | Graphene/PMMA | 1994 Ω sq–1 | 40% | ΔR/R0 = 0.5 at 20% strain | Temperature sensor | ref.124 | Graphene, CNT/PDMS | 0.01 S cm–1 | 100% | 100 Ω cm over 100% strain | ECG sensor | ref.125 | Polymers | PEDOT:PSS/ionic compounds | 3100 S cm–1 | 800% | 4100 S cm–1 at 100% strain | Interconnection | ref.126 | PEDOT:PSS/WPU,
d-sorbitol | 545 S cm–1 | 38% | ΔR/R0 = 0.11 at 30% strain | Electrophysiology
sensor | ref.127 | PEDOT:PSS/hydrogel | 23 S m–1 | 100% | 10 S m–1 at 100% strain | Interconnection | ref.128 | PEDOT:PSS/PUD | 168 S cm–1 | 100% | ΔR/R0 = 1.5 at 100% strain | Pressure sensor | ref.129 | PAAMPSA/PANI/PA | 2 S m–1 | 1935% | ΔR/R0 = 3.7 at 300% strain | Strain sensor | ref.130 | PEDOT:PSS-reduced GO/PDMS | 1010 S cm–1 | 20% | Maintained up to 15% strain | Conductor | ref.131 | PEDOT/PU/hydrogel | 40 S cm–1 | 100% | 120 S cm–1 at 100% strain | Stimulator | ref.132 |
|
Table 0. Electrical/mechanical performances of intrinsically stretchable conducting materials.
Materials | Mobility | Max. stretchability | Changes in mobility
under applied strains | Application | Reference | Carbon-based
nanomaterials | SWCNT/SEBS | 6.18 cm2 V–1 s–1 | 60% | – | Transistor | ref.133 | Polymers | DPP2TTVT-PDCA | 1.32 cm2 V–1 s–1 | 110% | 0.74 cm2 V–1 s–1 | Transistor | ref.96 | after 100 cycles of 25% strain | DPP-10C5DE | 0.25 cm2 V–1 s–1 | 100% | 0.2 cm2 V–1 s–1 at 100% strain | Transistor | ref.134 | P3HpT | 0.00055 cm2 V–1 s–1 | 54% | – | Transistor, PV | ref.135 | P3HT-PMA | 0.0009 cm2 V–1 s–1 | 140% | – | Transistor | ref.136 | DPP | > 0.1 cm2 V–1 s–1 | 100% | 0.07 cm2 V–1 s–1at 100% strain | Transistor | ref.137 | P3HT-PE | 0.05 cm2 V–1 s–1 | 660% | – | Transistor | ref.138 | C12-DPP | 0.463 cm2 V–1 s–1 | 100% | 0.1 cm2 V–1 s–1 at 100% strain | Transistor | ref.139 | 20D PPTTEC/PDMS | 0.66 cm2 V–1 s–1 | 150% | 0.4 cm2 V–1 s–1 | Transistor | ref.140 | after 500 cycles of 20% strain | P3HT/SEBS | < 0.006 cm2 V–1 s–1 | 50% | > 0.002 cm2 V–1 s–1 at 50% strain | Transistor | ref.141 | P3HT/PDMS | 0.00785 cm2 V–1 s–1 | 100% | 0.000374 cm2 V–1 s–1 at 100% strain | Transistor | ref.142 | DPPT-TT/SEBS | 0.59 cm2 V–1 s–1 | 100% | 0.55 cm2 V–1 s–1 at 100% strain | Transistor | ref.143 | 29-DPP-SVS/SEBS | 1.37 cm2 V–1 s–1 | 600% | 0.99 cm2 V–1 s–1 at 100% strain | Transistor | ref.144 | PCDTPT/P3HT | 0.09 cm2 V–1 s–1 | 75% | 0.16 cm2 V–1 s–1 at 75% strain | Transistor | ref.145 | P3HT/PDMS | 1.4 cm2 V–1 s–1 | 50% | – | Transistor | ref.87 | P3HT/PDMS | 3.3 cm2 V–1 s–1 | 50% | 1.7 cm2 V–1 s–1 at 50% strain | Transistor | ref.146 | P3HT/CNT/PDMS | 7.46 cm2 V–1 s–1 | 50% | 3.57 cm2 V–1 s–1 at 50% strain | Transistor | ref.147 | P3HT/PDMS | 0.18 cm2 V–1 s–1 | 120% | – | Transistor | ref.86 | DPP-DTT/PDMS | 1.23 cm2 V–1 s–1 | 100% | < 1 cm2 V–1 s–1 at 100% strain | Transistor | ref.148 | IDTBT | 1.8 cm2 V–1 s–1 | 100% | 0.6 cm2 V–1 s–1 at 100% strain | Transistor | ref.149 |
|
Table 0. Electrical/mechanical performances of intrinsically stretchable semiconducting materials.