Mahmoud H. Elshorbagy, Luis Miguel Sánchez-Brea, Jerónimo Buencuerpo, Jesús del Hoyo, Ángela Soria-García, Verónica Pastor-Villarrubia, Alejandro San-Blas, Ainara Rodríguez, Santiago Miguel Olaizola, Javier Alda, "Polarization conversion using customized subwavelength laser-induced periodic surface structures on stainless steel," Photonics Res. 10, 2024 (2022)

Search by keywords or author
- Photonics Research
- Vol. 10, Issue 9, 2024 (2022)
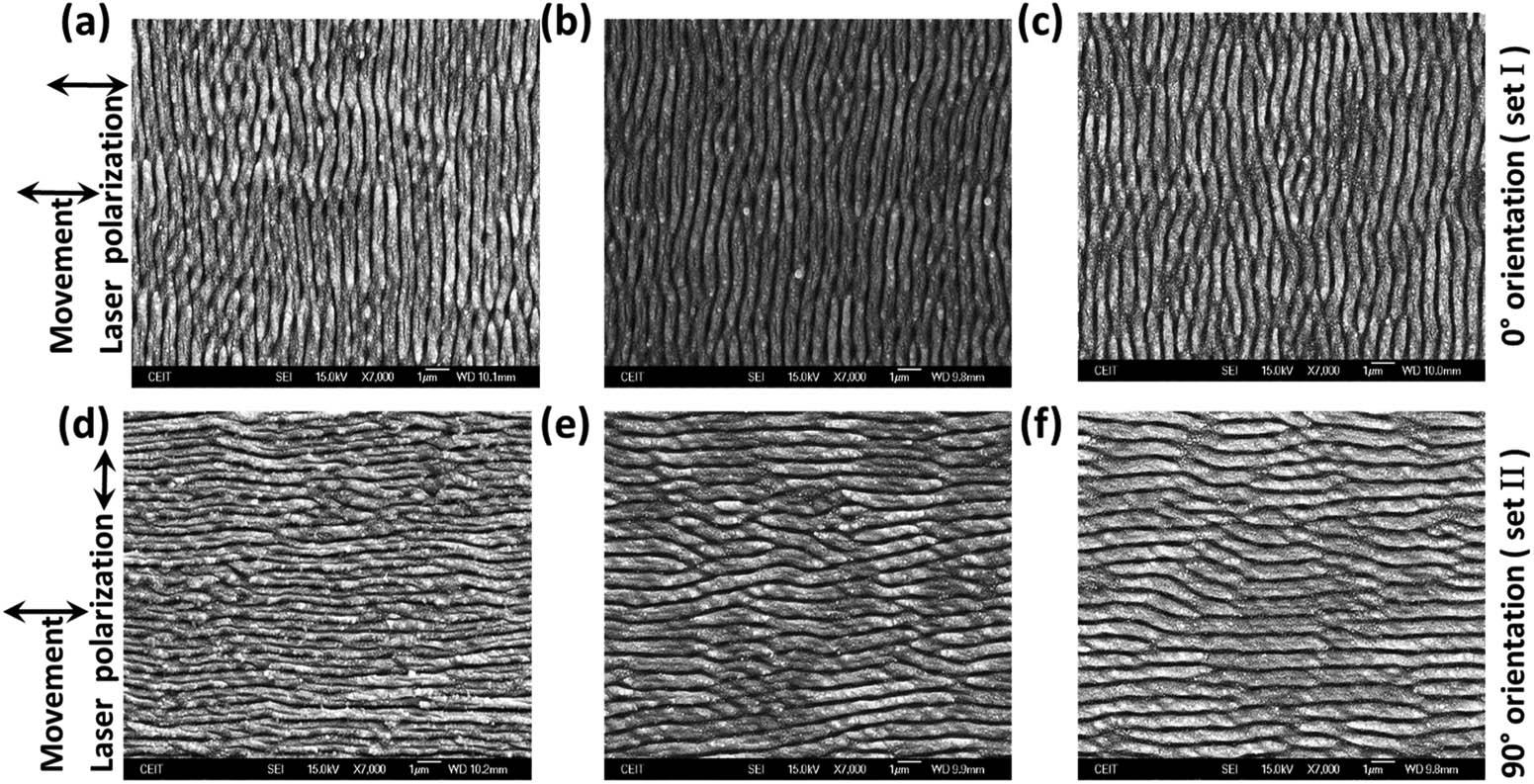
Fig. 1. SEM images for quasi-sinusoidal LIPSS fabricated on top of a steel substrate using femtosecond laser processing. The polarization state of the laser beam is parallel to the direction of the movement during the sample processing for (a)–(c) subplots and perpendicular for (d)–(f).
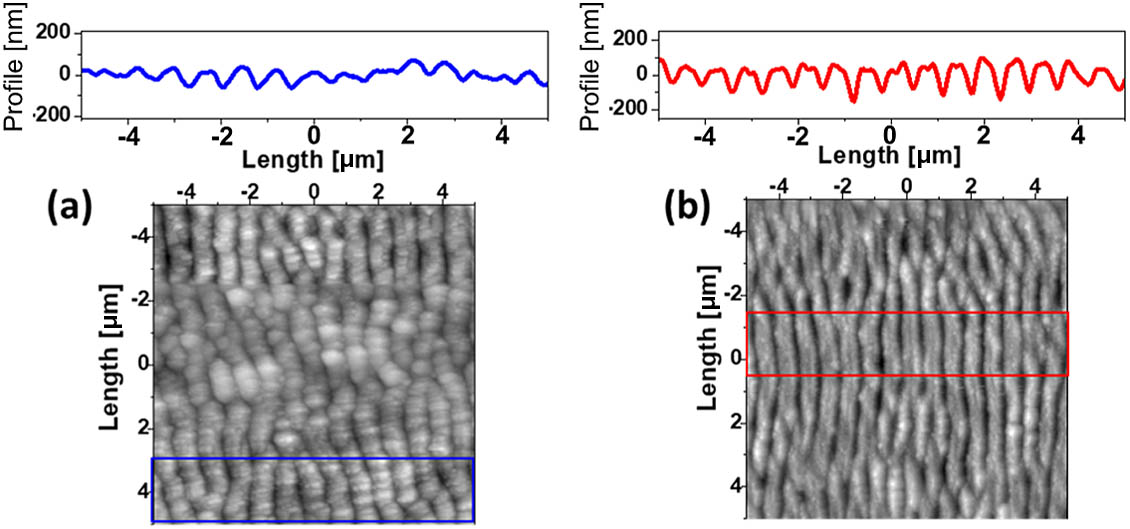
Fig. 2. (a) AFM image and profile for the sample with period P = 631 nm from set I. (b) AFM image and profile for the sample with period P = 606 nm from set II.
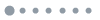
Fig. 3. Subwavelength gratings studied: (a) sinusoidal and (b) binary. They have a period P = 632 nm and are made of stainless steel. (c) Transversal sections showing the geometrical parameters of the profiles. In subplot (a), we have included a graphic layout showing the vector and components of the incoming electric field E , the azimuth angle φ (in our case φ = 45 ° ), the wavevector k , and the X Y Z coordinate system. Note that the incidence angle is α = 0 ° and it is not represented.
![Fitting of the simulated (solid lines) and experimentally measured (symbols) Stokes parameters for samples fabricated using femtosecond laser ablation with polarization (a) parallel and (b) perpendicular to the direction of the movement during the sample fabrication. (c)–(f) Plots show the geometrical parameters GH and β of the profile that best fit the experimental data for the two sets of samples [set I in (c) and (e), and set II in (d) and (f)]. The dashed red circles select the lowest β value on plot (e), and the highest β value on plot (f). The solid lines in plots (c)–(f) represent the cubic polynomial fitting of the geometrical parameters versus P.](/Images/icon/loading.gif)
Fig. 4. Fitting of the simulated (solid lines) and experimentally measured (symbols) Stokes parameters for samples fabricated using femtosecond laser ablation with polarization (a) parallel and (b) perpendicular to the direction of the movement during the sample fabrication. (c)–(f) Plots show the geometrical parameters GH and β of the profile that best fit the experimental data for the two sets of samples [set I in (c) and (e), and set II in (d) and (f)]. The dashed red circles select the lowest β value on plot (e), and the highest β value on plot (f). The solid lines in plots (c)–(f) represent the cubic polynomial fitting of the geometrical parameters versus P .
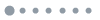
Fig. 5. Maps of the normalized Stokes parameters q , u , and v , and reflectance R , as a function of the geometrical parameters GH and BW for the binary (left) and sinusoidal (right) gratings. The maximum value of reflectivity R max = 0.6 is around the reflectivity value given by a regular, not nanostructured, stainless steel surface.
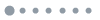
Fig. 6. Maps of the azimuth Ψ and ellipticity χ angles as a function of BW and GH parameters for the binary (left column) and sinusoidal (right column) profiles. The contour lines in the azimuth maps represent the values of Ψ = 45 ° (in magenta), Ψ = − 45 ° = 135 ° (in cyan), and Ψ = 0 ° and Ψ = 180 ° (in yellow). The black contour lines in the ellipticity maps are for a value χ = 0 ° . The locations of the configurations with χ = − 45 ° and χ = + 45 ° are given as white dots in the blue and red regions, respectively.
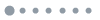
Fig. 7. Full-wave propagation of the electric field on LIPSS for (a), (c), (e) binary grating, and (b), (d), (f) sinusoidal grating. The yellow arrows in (a) define the location of the source, LIPSS, reflection, and PML. The electric field in subplot (c) is linearly polarized and oriented along the 45° direction, being the point of view of the graphical representation almost coincident with the direction of the electric field vector. The labels for each field representation correspond to the cases presented in Table 1 and Fig. 5 . We have also plotted the electric field distributions, along with the field evolution at the output, to help to understand the physical mechanism involved in the conversion.
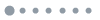
Fig. 8. Maps of the modulus of the elements of the Jones matrix | P x x | and | P y y | , and the relative phase shift between the electric field components of the reflected wave ϕ , in terms of the geometrical parameters GH and BW. The left column is for the binary profile and the right column is for the sinusoidal shape. The yellow line in the phase map corresponds to the configuration that shows an equal value of the modulus of the diagonal elements of the Jones matrix. The dots are the locations on the P x x = P y y line, where ϕ = ± π / 2 ; i.e., the geometries for CP. These dots coincide with those presented in Figs. 6 (c) and 6 (d).
|
Table 1. Geometrical Parameters and Reflectance of the Selected Minima and Maxima for the Binary and Sinusoidal Profilesa
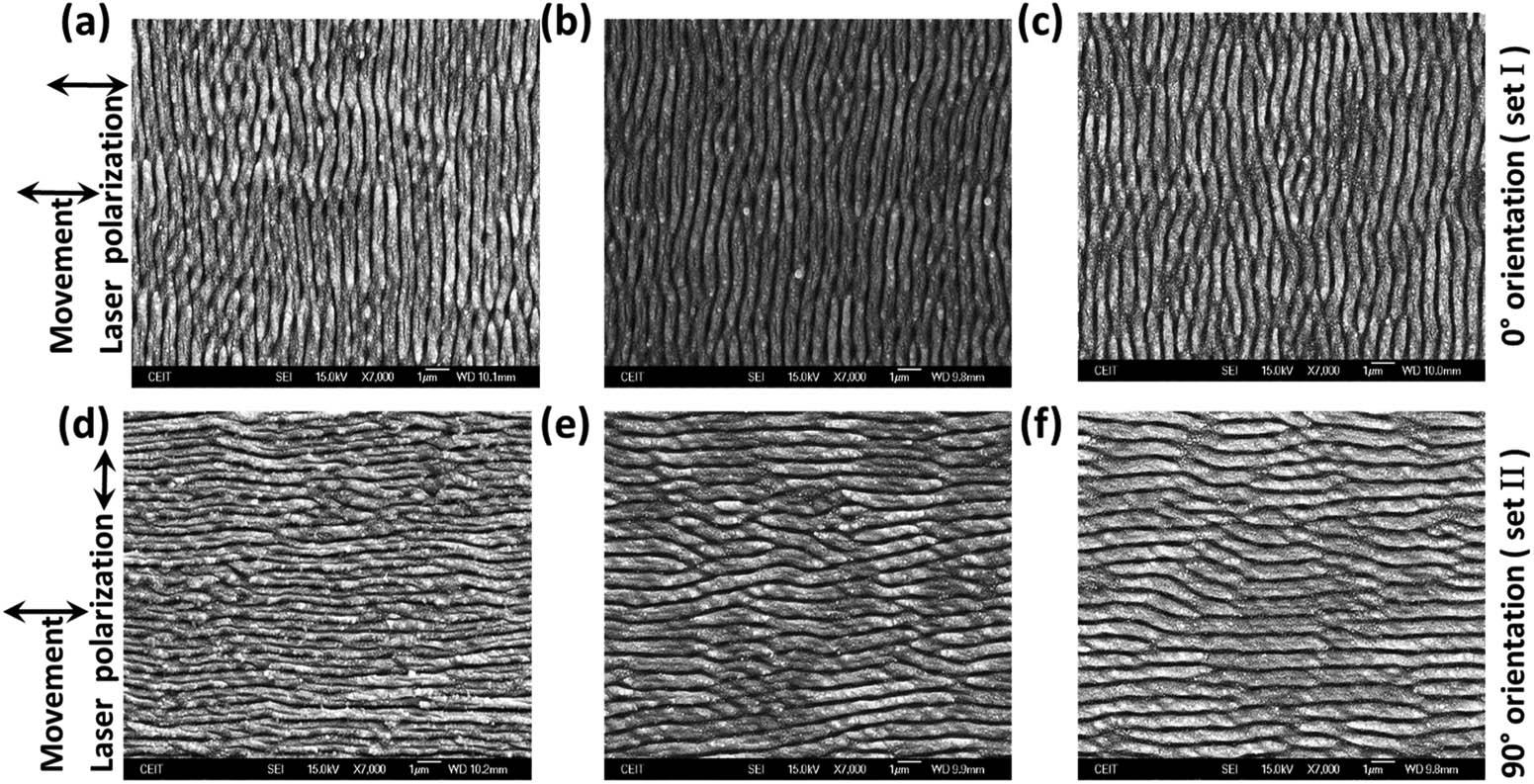
Set citation alerts for the article
Please enter your email address