Jiahe Chai, Mingli Dong, Peng Sun, Bixi Yan. Model and compensation method of image point drift caused by self-heating of industrial camera[J]. Infrared and Laser Engineering, 2021, 50(6): 20200494

Search by keywords or author
- Infrared and Laser Engineering
- Vol. 50, Issue 6, 20200494 (2021)
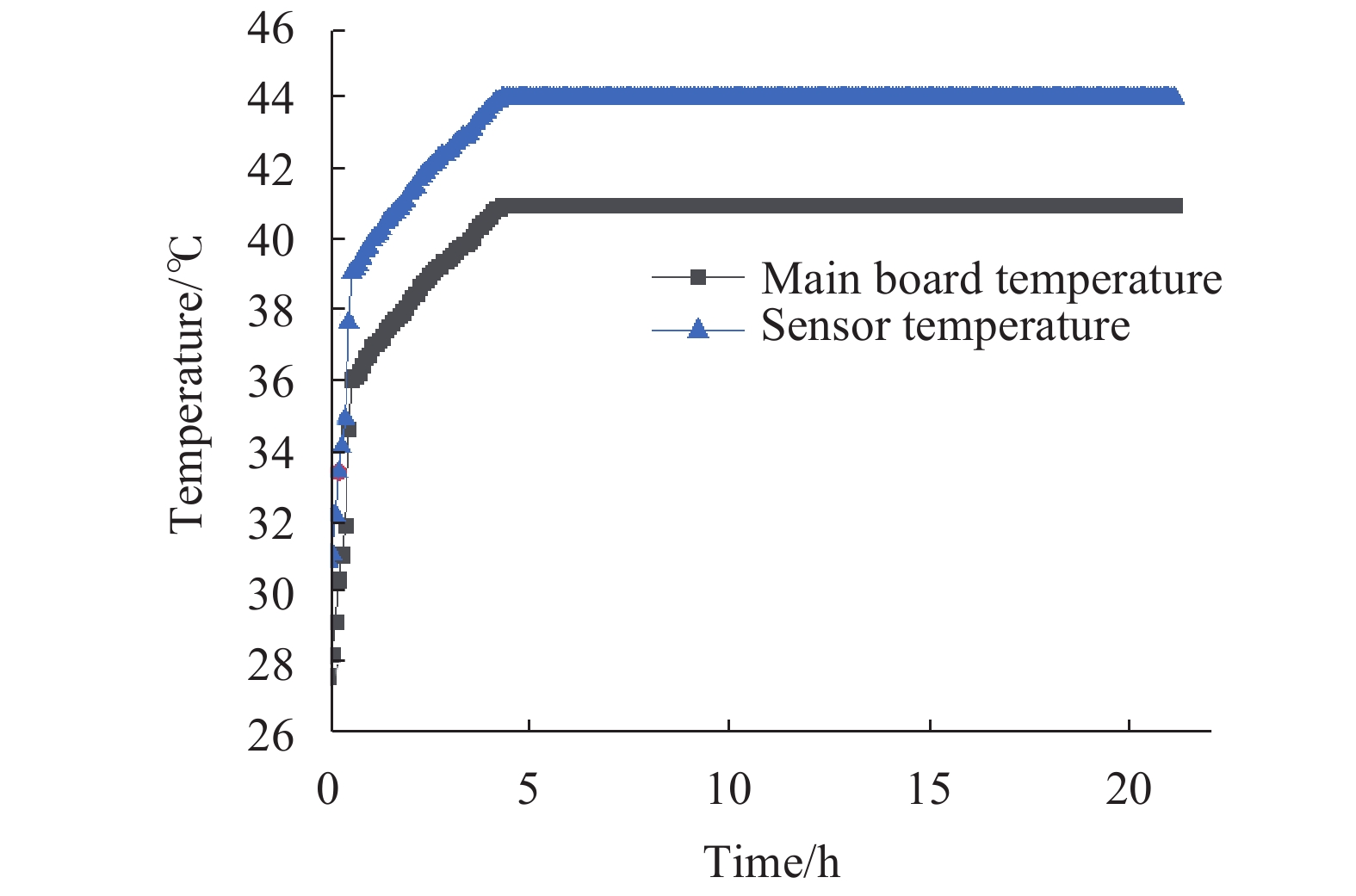
Fig. 1. Temperature change of the imaging device and the main board after turning on
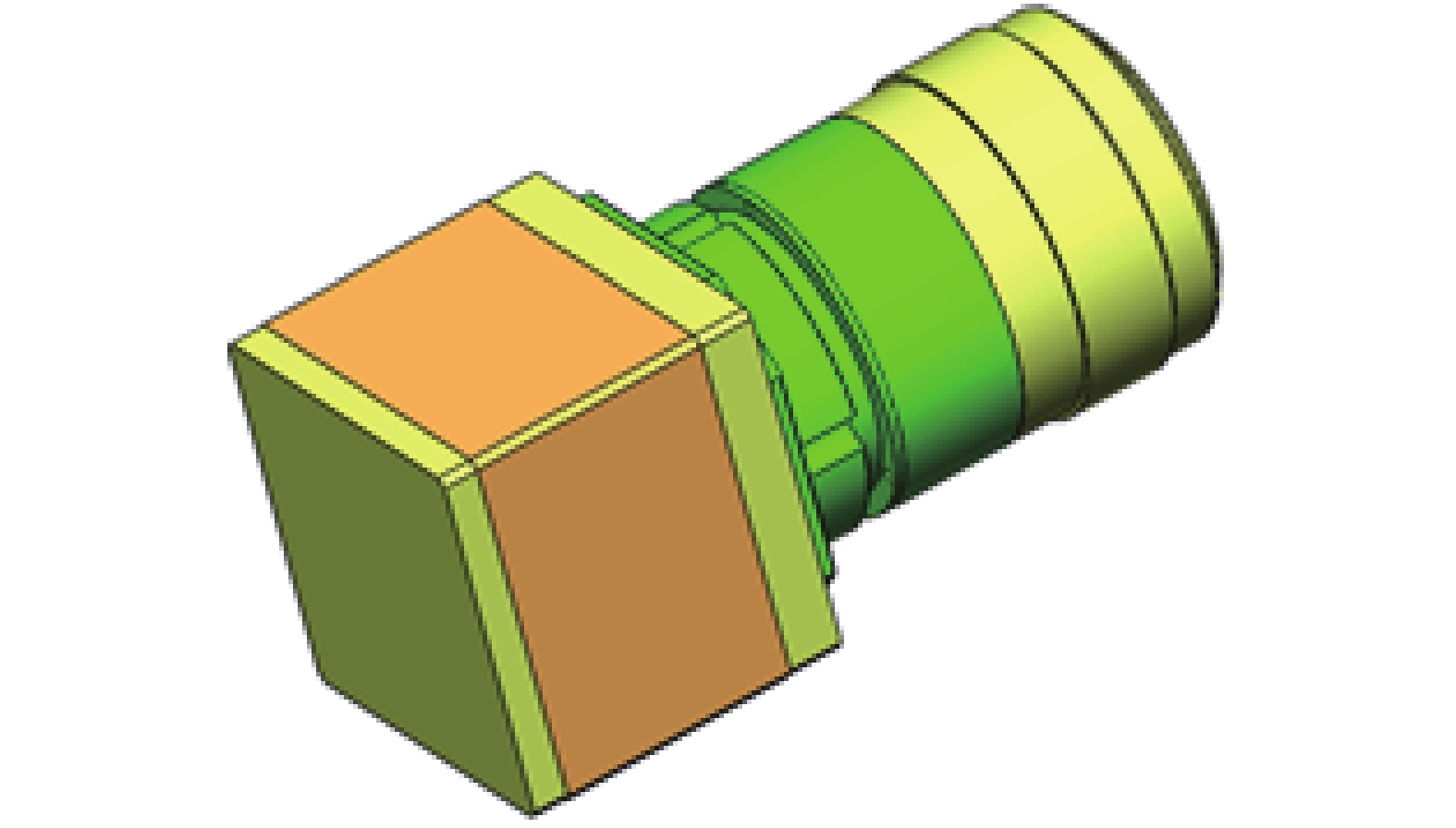
Fig. 2. 3D model of AVT GT5120 camera
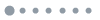
Fig. 3. Camera finite element model
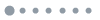
Fig. 4. Camera transient thermal stress analysis results
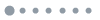
Fig. 5. Axial offset of the camera causes the imaging optical path to change
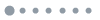
Fig. 6. Image point drift caused by axial optical path changes
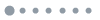
Fig. 7. Schematic diagram of image point shift caused by radial expansion
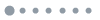
Fig. 8. Temperature changes of the experimental device and its components
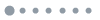
Fig. 9. In the self-heating state, the coordinate value of each quadrant point after compensation is compared with the experimental measurement value
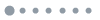
Fig. 10. Camera thermal control system
|
Table 1. Material properties of camera components
|
Table 2. Deformation of the lens and CMOS under different temperature variation
|
Table 3. Pixel drift compensation model error
|
Table 4. Comparison of thermal control device method and image point drift compensation method
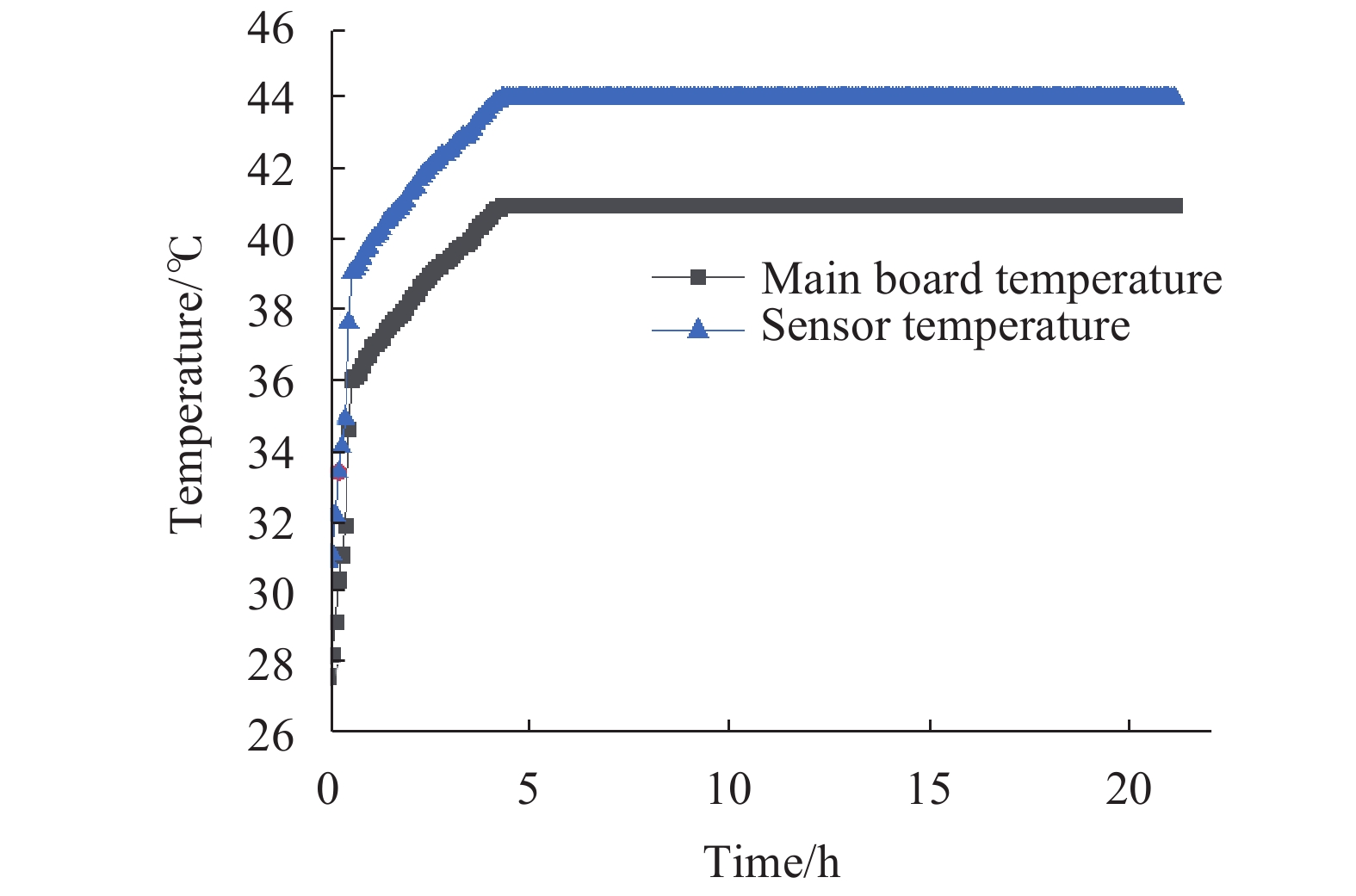
Set citation alerts for the article
Please enter your email address