Rui Chen, Jincheng Wang, Wenzhuo Zhang, Dongsheng Ji, Xinning Zhu, Tao Luo, Jing Wang, Wei Zhou. Research progress of laser manufacturing technology for microstructure sensor[J]. Opto-Electronic Engineering, 2023, 50(3): 220041

Search by keywords or author
- Opto-Electronic Engineering
- Vol. 50, Issue 3, 220041 (2023)

Fig. 1. Application of the microstructure sensor for bioelectricity, pressure and temperature detection

Fig. 2. Classification of microstructures
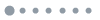
Fig. 3. Laser manufacturing method of microstructure
![Laser manufacturing pressure sensor. (a) Image of the sensor and microstructure super-depth maps, response time testing, speech recognition applications[66]; (b) SEM images of three microstructures and performance test of sensors[67]; (c) Schematic diagram of microstructure sensor, SEM image, sensitivity and pulse performance test[71]; (d) Schematic diagram of sensor microstructure and SEM image[72]](/Images/icon/loading.gif)
Fig. 4. Laser manufacturing pressure sensor. (a) Image of the sensor and microstructure super-depth maps, response time testing, speech recognition applications[66]; (b) SEM images of three microstructures and performance test of sensors[67]; (c) Schematic diagram of microstructure sensor, SEM image, sensitivity and pulse performance test[71]; (d) Schematic diagram of sensor microstructure and SEM image[72]
![Temperature sensor based on the laser reduction of graphene oxide. (a) Image of the sensor, SEM image of the reduced graphene oxide, sensitivity, bending test hysteresis test, blowing and breathing performance test and curved surface test of the sensor[51]; (b) Laser reduced graphene oxide sensor diagram[76]; (c) Reduction of graphene oxide by laser[77]; (d) Sensor manfacturing process[78]](/Images/icon/loading.gif)
Fig. 5. Temperature sensor based on the laser reduction of graphene oxide. (a) Image of the sensor, SEM image of the reduced graphene oxide, sensitivity, bending test hysteresis test, blowing and breathing performance test and curved surface test of the sensor[51]; (b) Laser reduced graphene oxide sensor diagram[76]; (c) Reduction of graphene oxide by laser[77]; (d) Sensor manfacturing process[78]
![Temperature sensor based on the laser-induced graphene. (a) TEM image of the typical layered morphology of NMP-passivated BP nanosheet and Photograph illustrating location of sensor for jugular vein pulse measurement[81]; (b) Device photograph and SEM images of cross-sectional view of the ZIS nanosheets on porous graphene electrodes[82]; (c) Photograph of the 3 × 3 sensor and response curves for temperature monitoring[83]; (d) Leaf surface induced graphene patterning for temperature sensors[84]](/Images/icon/loading.gif)
Fig. 6. Temperature sensor based on the laser-induced graphene. (a) TEM image of the typical layered morphology of NMP-passivated BP nanosheet and Photograph illustrating location of sensor for jugular vein pulse measurement[81]; (b) Device photograph and SEM images of cross-sectional view of the ZIS nanosheets on porous graphene electrodes[82]; (c) Photograph of the 3 × 3 sensor and response curves for temperature monitoring[83]; (d) Leaf surface induced graphene patterning for temperature sensors[84]
![Microneedle Array Bioelectric Sensors. (a) SEM image of an array of microneedles on the sensor and top views of the microneedle sensor equipped with an adhesive film[87]; (b) Scanning electron microscope image of the PDMS microneedle before Au deposition[88]; (c) Dry electrode manufacturing process and SEM image of microneedle array[36, 89]; (d) Electrode optical image[91]; (e) Photograph of the sensor and SEM image of the microneedle[92]](/Images/icon/loading.gif)
Fig. 7. Microneedle Array Bioelectric Sensors. (a) SEM image of an array of microneedles on the sensor and top views of the microneedle sensor equipped with an adhesive film[87]; (b) Scanning electron microscope image of the PDMS microneedle before Au deposition[88]; (c) Dry electrode manufacturing process and SEM image of microneedle array[36, 89]; (d) Electrode optical image[91]; (e) Photograph of the sensor and SEM image of the microneedle[92]
|
Table 1. Performance comparison of laser-manufactured pressure sensors
|
Table 2. Performance comparison of laser-manufactured temperature sensors

Set citation alerts for the article
Please enter your email address