Tao He, Zhonghua Shen, Fei Chen, Li Chen. Measurement of translucent coating thickness based on pulsed thermography[J]. Infrared and Laser Engineering, 2022, 51(2): 20210890

Search by keywords or author
- Infrared and Laser Engineering
- Vol. 51, Issue 2, 20210890 (2022)
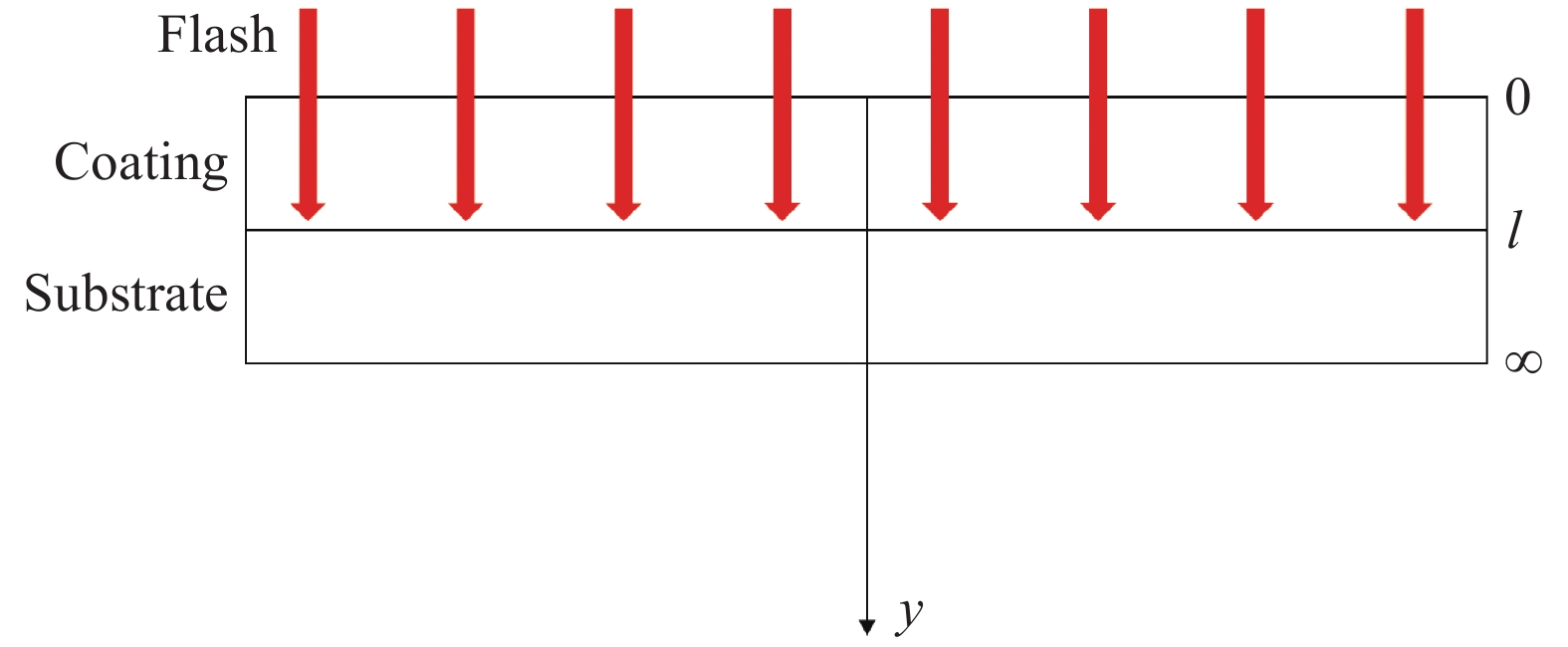
Fig. 1. Schematic diagram of theoretical analysis model
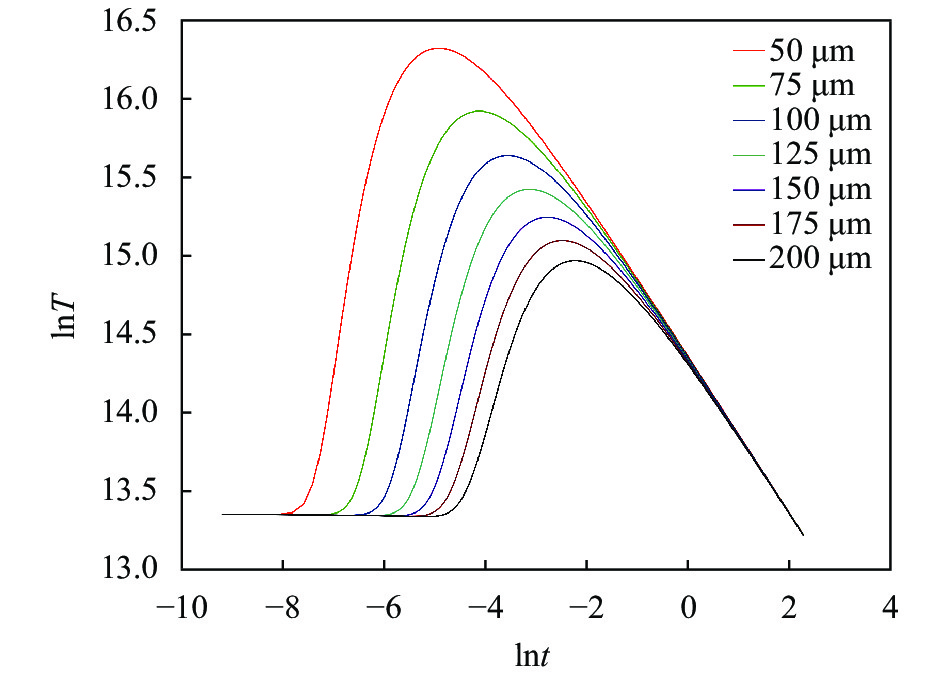
Fig. 2. Analytical surface temperature of samples with different coating thickness vs time in double logarithm scale
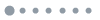
Fig. 3. Coating thickness vs peak time of surface temperature in logarithm scale
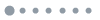
Fig. 4. Schematic diagram of numerical calculation model
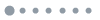
Fig. 5. Coating thickness vs transmittance
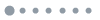
Fig. 6. Simulation surface temperature of samples with different coating thickness vs time in double logarithm scale
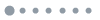
Fig. 7. Coating thickness vs simulation peak time of surface temperature in logarithm scale
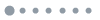
Fig. 8. Schematic diagram of the coating specimen
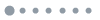
Fig. 9. Selected frames from the IR image sequence
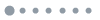
Fig. 10. Experimental surface temperature of samples with different coating thickness vs time in double logarithm scale
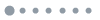
Fig. 11. Thickness vs experimental peak time in double logarithm scale
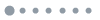
Fig. 12. Test result of thickness distribution of the specimen
|
Table 1. Parameters used in the model
|
Table 2. Measurement result of coating thickness
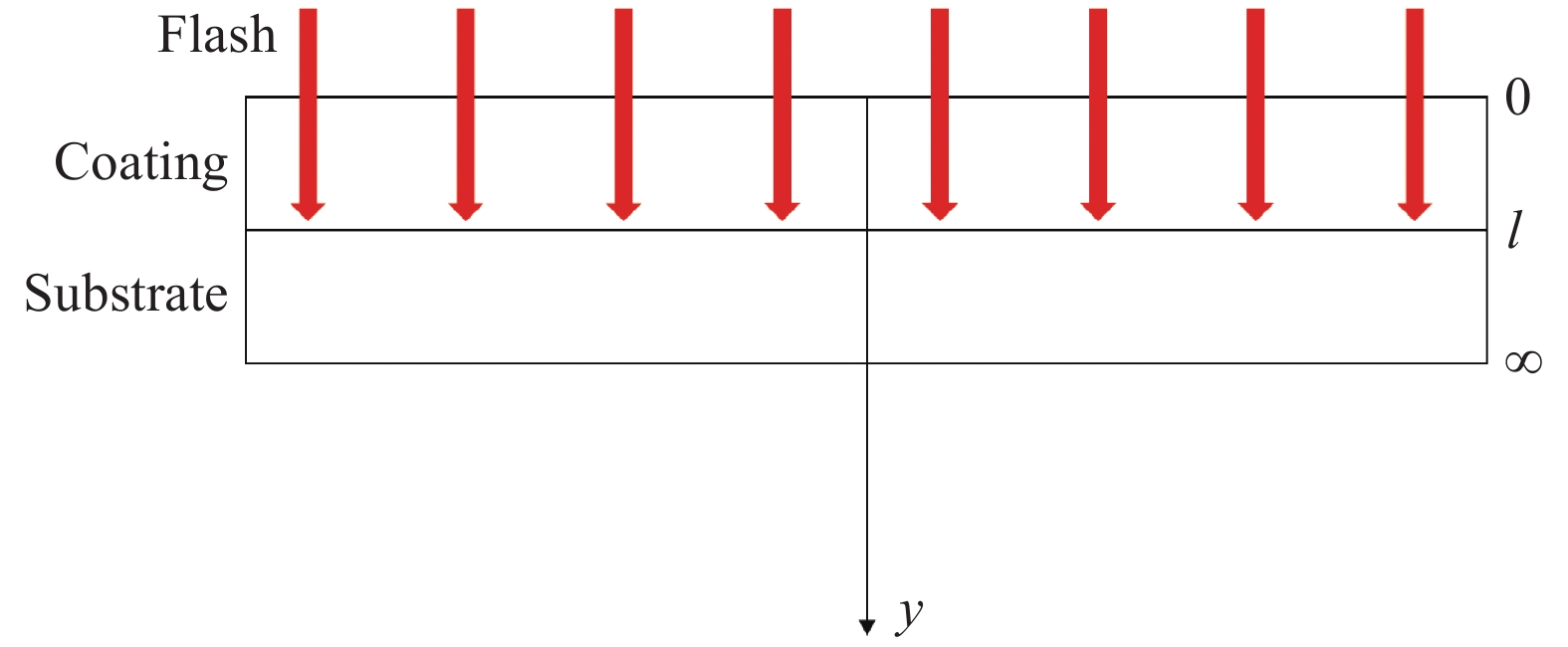
Set citation alerts for the article
Please enter your email address