Fig. 1. Piezoresistive designs for engineering electronic skin. (
a) Developmental history of flexible skin-like electronics (e.g. milestones in the shear force measurement, large-area manufacturing, spatial mapping, bioinspired manufacturing, interconnection between e-skin and live neurons, and self-healing capability)
10-17 . (
b) Scheme illustrating the design and applications of piezoresistive sensors.
Fig. 2. Principles of piezoresistive effect. (
a) Piezoresistance based on the geometric changes of metals and conducting polymers. i and ii represent the block and planar material geometries, respectively
41,47. (
b) Piezoresistance of semiconductor. Scheme illustrating the changes of charge carrier and energy band upon traction along the [111] direction in p–Si
47. (
c) Piezoresistance of composite materials based on the changes of conducting filler concentration and inter-filler distance
48. (
d) Structural piezoresistance based on the contact area and point changes of conducting architecture. Figure reproduced with permission from: (b) ref.
47, Elsevier.
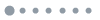
Fig. 3. Development of piezoresistive sensors based on various materials. (
a) Fabrication scheme and optical images of a hybrid metallic foam
46. (
b) Schematic illustrating the fabrication of CNTs/FKM nanocomposite
50. FKM, fluoroelastomer; CNTs, carbon nanotubes; and TAIC, 1,3,5-triallyl-1,3,5-triazine-2,4,6 (1H,3H,5H)-trione. (
c) Scheme illustrating the assembly of a MG/PU piezoresistive sensor
51. MG, modified-graphite; PU, polyurethane; and PDMS, polydimethylsiloxane. (
d) A flexible tactile sensor assembled from the 8x8 array of Si-strain gauges and the Si thin film transistors
64. (
e) Scheme illustrating the sandwich-structure of a PEDOT:PSS/Ag NW/PDMS component film
74. PEDOT:PSS, poly(3,4-ethylenedioxythiophene):poly(styrenesulfonate); and Ag NWs: Ag nanowires. (f) mGN fillers form new conducting paths under pressure
80. mGN, magnetic reduced graphene oxide@nickel nanowire. Figure reproduced with permission from: (a) ref.
46, (f) ref.
80, American Chemical Society; (c) ref.
51, under a Creative Commons Attribution 4.0 International License; (d) ref.
64, AIP Publishing.
Fig. 4. Piezoresistive design and manufacture with singular structure. (
a) Piezoresistance of an artificial structured sensor based on contact area changes
91. ITO, indium tin oxide; PET, polyethylene terephthalate; SWCNTs, single-walled carbon nanotube; PDMS, polydimethylsiloxane. (
b) Scheme illustrating the lotus-leaf-inspired piezoresistive design and assembly
98. (
c) Scheme illustrating the rose-petal-inspired piezoresistive design and assembly
99 and the shark-skin-inspired piezoresistive design and assembly
101. (
d) Scheme illustrating the spider-leg-joint-inspired piezoresistive design with plenty of cracks
102. Figure reproduced with permission from: (a) ref.
91, (d) ref.
102, Elsevier; (c) ref.
101, Elsevier and ref.
99, Royal Society of Chemistry.
Fig. 5. Sensitivities of different microstructure sensors. ITO, indium tin oxide; MWNT, multiwalled carbon nanotubes; and PDMS, polydimethylsiloxane. Figure reproduced with permission from ref.
94, under a Creative Commons Attribution 4.0 International License.
Fig. 6. Piezoresistive design and manufacture with hierarchical structure. (
a) Multiple dome structures as piezoresistance sensing layer
86. (
b) Multiple structure comprising of dense protuberances and porous structure as piezoresistance sensing layer
106. HPM, hybrid porous microstructure; and CNT, carbon nanotubes. (
c) Piezoresistive sensitivities based on the sensing layers comprising of rough-to-rough, rough-to-flat and flat-to-rough surfaces
107. Figure reproduced with permission from: (a) ref.
86, (b) ref.
106, (c) ref.
107, American Chemical Society.
Fig. 7. Design and manufacture of fibre piezoresistive sensor. (
a) Schematic of a rGO-Ag NW@cotton fibre, through immersion of cotton fibres in a reductive solution containing GO and AgNW
112. GO, graphene oxide; rGO, reduced GO; and AgNW, Ag nanowires. (
b) Scheme of an electrospun fibre piezoresistive sensor and its sensing mechanisms during pressure and blending
110. KL, kraft lignin. (
c) Scheme of a wet-spinning single-fibre piezoresistive sensor
122. Figure reproduced with permission from: (a) ref.
110, (b) ref.
112, Elsevier; (c) ref.
122, American Chemical Society.
Fig. 8. Piezoresistive design and manufacture with spongy structure. (
a) Freeze drying for the fabrication of piezoresistive sponge
68. (
b) Directional freeze drying of the fabrication of piezoresistive wave-shaped sensing layers
127. CNC, cellulose nanocrystals. (
c) Dip coating of as-fabricated sponge with conducting materials
130. PU, polyurethane; and MWCNT, multiwalled carbon nanotubes. (
d) Sacrificial template for the fabrication of piezoresistive sponge
131. (
e) Sponge-based hierarchical structure (e.g. cracks) for piezoresistive sensor
134. Figure reproduced with permission from: (a) ref.
68, (d) ref.
131, (e) ref.
134, American Chemical Society; (b) ref.
127, (c) ref.
130, Royal Society of Chemistry.
Fig. 9. Additive manufacturing for piezoresistive sensor. (
a) Drop-on-demand material jetting for the facial fabrication of piezoresistive structures
143. MCF, milled carbon fibers; and SR, silicone rubber. (
b) 3D printing of human-skin-inspired texture as piezoresistive sensing layers
144. CNT, carbon nanotube. (
c) Application of a 3D printed piezoresistive sensor for robotic fingertips to sense force
145. (
d) 3D printing of conducting composite for piezoresistive sensor
148. SIS, polystyrene–polyisoprene–polystyrene. (
e,
f) 3D printing of different structure parameters (e.g. diameter, interaxial angle, and interlayer space) for piezoresistive sensor
149. GF, gauge factor. Figure reproduced with permission from: (a) ref.
143, (e, f) ref.
149, Elsevier; (c) ref.
145, American Chemical Society; (d) ref.
148, Royal Society of Chemistry.
Fig. 10. Piezoresistive sensor for health monitoring. (
a) Detection of physical activities by piezoresistive sensor, including the swallowing (A and B: the pharyngeal and esophageal phase, respectively) and the posture of human back
152. (
b) Detection of physiological activities (e.g. wrist and jugular venous pulse) at high sensitivities
153. (
c) Detection of myocardic activities (e.g. heartbeats at breathing and not breathing) by a piezoresistive sensor
154. (
d) Identification of different mechanical stimuli, including pressure, shear and torsion force
132. Figure reproduced with permission from: (a) ref.
152, (d) ref.
132, Elsevier; (b) ref.
153, (c) ref.
154, American Chemical Society.
Fig. 11. Piezoresistive sensor for intelligent healthcare. (
a) Piezoresistance for visiual, alarm, wireless and implanted applications
35. (
b) Triode-mimicking pressure sensor for intelligent shoe pad
159. (
c) Scheme illustrating a monitoring system developed based on the intelligent shoe pad in (b)
159. (
d) Continuous and multiple signals from the integrated gait monitoring system in (c)
159. Figure reproduced with permission from: (a) ref.
35; (b–d) ref.
159, American Chemical Society.
Fig. 12. Piezoresistive sensor for intelligent speech recognition. (
a) Piezoresistive detection of sound (e.g. word recognition, volume detection, and voice recognition)
68. (
b) Response of a MXene-based piezoresistive sensor to the audio outputs at different volumes
162. (
c) Anti-interference voice recognition by a skin-attachable piezoresistive sensor
165. Figure reproduced with permission from: (a) ref.
68, (b) ref.
162, (c) ref.
165, American Chemical Society.
Fig. 13. Piezoresistive sensor for prosthetics and robots. (
a) Manipulating the robot arm by a piezoresistive sensor for music playing
169. (
b) Large-area force distribution detected by fibre piezoresistive sensor array
171. (
c) Piezoresistive sensor for the real-time monitoring of robot−tissue collision/interaction in surgical robots
173. (
d) Development of an artificial afferent nerve based on multiple piezoresistive sensors
175. Figure reproduced with permission from: (a) ref.
169, (b) ref.
171, (c) ref.
173, American Chemical Society.
| Structure | Materials | Sensor thickness | Performance | Flexible/ stretchable | Application/ Force application | Fabrication technique | Ref. | Sensitivity
or GF | Sensing range | Response time | Cyclic test | GF: gauge factor (in some case just a single-point value).
CNTs: carbon nanotubes; FKM: fluoroelastomer; SiC: silicon carbide; MWCNTs: multi-walled carbon nanotubes; Si: silicone; CB: carbon black; PDMS: polydimethylsiloxane; rGO: reduced graphene oxide; PS: polystyrene; VGr: vertical graphene; Ag NW: silver nanowire; PI: polyimide; Ag: silver; CSilkNM: carbonized silk nanofiber membranes; PPy: polypyrrole; EVOH: poly(vinyl alcohol-co-ethylene); POE: polyolefin elastomer; NiNWs: nickel nanowires; SWCNTs: single walled carbon nanotubes; Gr: graphene; ACNT: aligned carbon nanotub; Pt: platinum; PUA: polyurethane acrylate; PU: polyurethane; CNCs: cellulose nanocrystals; SiNPs: silica nanoparticles; TPU: thermoplastic polyurethane; CB: carbon black; PANI: polyaniline; PEDOT:PSS: poly(3,4-ethylenedioxythiophene):poly(styrenesulfonate); WGF: wrinkled graphene film; and PVA: polyvinyl alcohol | Simple “bulk” | Simple “bulk” | CNTs/FKM | 100 ~ 300 mm | 1.3 ×105 (ε = 100%) | 232% ε | | 500 times
Hysteresis (0~150% ε) | Yes/Yes | Strain/Human motion monitoring and Stretchable LEDs | Internal melt-mixer | ref.50 | Simple “bulk” | SiC/Ecoflex | | 2.47×105 (ε = 2.5%) | 0.05% ~ 5% ε | | 10000 times
Consistent (0~4% ε) | Yes/Yes | Strain and pressure/Health and motion monitoring | Laser direct writing | ref.65 | Simple “bulk” | rGO/PS | ~ 60 mm | 250
(ε = 1.05%) | | 100 ms | 2000 times
Consistent (0~0.7% ε) | Yes/Yes | Pressure/Human movement behaviors | Laser scribe | ref.152 | Simple “bulk” | VGr/PDMS | | 72(ε = 20%)
22000
(ε = 100%) | ε = 100%
(Max) | | 1000 times
Consistent (0~40% ε) | Yes/Yes | Strain/Human’s activities and timbres | Deposition | ref.164 | Fibre | Fibre | rGO-Ag NW@cotton fiber | | 4.23 kPa−1 (P =2.0 kPa) | | 220 ms | | Yes/Yes | Pressure, bending and twisting/Finger
motion and pulse monitoring | Coating | ref.112 | Nano fibre | PI@Ag | | 1400 kPa−1 (5~100 kPa) | 100 Pa ~ 100 kPa | 200 ms | 1000 times
Consistent (5 kPa) | Yes/Yes | Pressure/Movement of body and
temperature | Electrospinning and in
situ growth | ref.66 | Nano fibre | CSilkNM | 0.63 ± 0.14 mm | 34.47 kPa−1 (0.8 ~ 400 Pa) | 0.8 Pa ~ 5 kPa | 16.6 ms | 10000 times
Consistent (2.5 kPa) | Yes/Yes | Pressure/Human physiology monitoring
and pressure distribution | Electrospinning | ref.115 | Fibre | MWCNT/Si /EcoFlex | 1.35 mm | 1378
(ε=330%) | 50% ~ 300% ε | 295ms | 10000 times
Consistent (0~1000% ε) | Yes/Yes | Strain, bending and torsion /Human
motion detection | Wet spinning | ref.122 | Nano fibre | PPy/EVOH/ POE | ~ 70 μm | 2.83 kPa−1 (0 ~17 kPa) | Upper limit 80 kPa | 3 ms | 4500 times
Consistent (0~10 kPa) | Yes/Yes | Pressure/Large area pressure sensing | Direct melt extrusion | ref.171 | Surface structure | Micro-dome | rGO@NiNWs/ EcoFlex | | 1302.1 kPa−1 (0 ~ 2.5 kPa) | 72 Pa ~ 20 kPa | 6 ms | 20000 times
Consistent | Yes/Yes | Pressure/Health and motion monitoring | Hot embossing | ref.80 | Pyramid | SWCNTs/ PDMS | ~ 700 mm | 8655.6 kPa−1 (400 ~ 800 Pa) | Lower limit 7.3 Pa | 4 ms | 10000 times
Consistent | Yes/No | Pressure/Health care | Photolithography | ref.91 | Pyramid | PDMS/Carbon | ~ 1 mm | −2.5 kPa−1 (0 ~ 160 Pa) | 15 Pa ~ 9 kPa | ~20 ms | | Yes/No | Pressure/Human movement behaviors | Laser | ref.7 | Hierarchical | PDMS/Gr | ~ 1 mm | 1.2 kPa−1 (0.2 ~ 25 kPa) | 5 Pa ~12 kPa | | 1000 times
Consistent (1, 5, and 10 kPa) | Yes/No | Pressure /Human movement behaviors
and voice recognition | Soft lithography | ref.98 | Micro-papillae | Cu - Ag NWs/ PDMS | ~ 1 mm | 1.35 kPa−1 (0 ~ 2.0 kPa) | 2 Pa ~ 20 kPa | 36 ms | 5000 times
Consistent (0 ~2 kPa) | Yes/No | Pressure/Human physiology monitoring | Soft lithography | ref.99 | Hierarchical | ACNT/Gr/ PDMS | ~ 500 mm | 19.8 kPa−1 (0.6 ~ 300 Pa) | 0.6 Pa ~ 5.8 kPa | 16.7 ms | 35000 times
Consistent (0~ 150 Pa) | Yes/No | Pressure, bending and torsional/Voice recognition | Soft lithography | ref.100 | Surface structure | Crack | Pt/PUA | ~ 10 mm | 2, 000 (ε = 2%) | | | | Yes/Yes | Strain/Human movement behaviors and voice recognition | Depositing/Stretching | ref.15 | Crack | Gold/PDMS | 100 μm | 200 (ε <0.5)
1000 (0.5% < ε < 0.7%)
5000 (0.7% < ε < 1%) | 2% ε | | | Yes/Yes | Strain and pressure/Human physiology monitoring and sound vibrations | Depositing/ Stretching | ref.104 | Skin Texture | CNTs/PDMS | | 2.08 kPa−1 (0.12 kPa) | | 50 ms | 8000 times
Consistent | Yes/Yes | Pressure/Human movement behaviors | 3D-printing | ref.144 | Papillae | SWNT- MXene | | 11.47 kPa−1 (13 Pa ~ 0.77 kPa) | (13 Pa ~ 10 kPa) | 20 ms | 10000 times
Consistent (0~ 1 kPa) | Yes/No | Voice recognition (different volumes)/Pressure | Etching and exfoliation | ref.162 | Cracks | rGO/PDMS | ~ 300 μm | 8699
(0.8 ~ 1.0% ε) | 0.000064%
(Mim) | 107 ms | 1000 times
Consistent (0~0.35% ε) | Yes/Yes | Anti-interference voice recognition/Pressure | Femtosecond laser direct writing | ref.165 | Porous | Porous | PU/Liquid metal | | > 25 | | 202 ms | | Yes/Yes | Pressure/Electronic protection foam for transportation | Coating | ref.46 | Porous | Mxenes /rGO | | 22.56 kPa−1 (1 kPa ~ 3.5 kPa) | Lower limit 10 Pa | <200 ms | 1000 times
Consistent (0~ 0.81 kPa) | Yes/Yes | Pressure/Human physiology monitoring and voice recognition | Ice - template freezin | ref.68 | Multilayer | Mxenes/CNCs | | 114.6 kPa −1 (0.05 ~ 10 kPa) | Lower limit 1.0 Pa | 189 ms | 2000 times
Consistent (0~50% ε) | Yes/Yes | Pressure/Human physiology monitoring and voice recognition | Directional freezing | ref.127 | Porous | Gr/PDMS | | 0.09 kPa−1 (0 ~ 1000 kPa) | Upper limit 2000 kPa | 100 ms | | Yes/Yes | Pressure/Human physiology and motion monitoring | Sacrificial template | ref.131 | Porous | Gr/PDMS | ~0.3 mm | 15.9 kPa−1 (0 ~ 60 kPa) | | 1.2 ms | | Yes/Yes | Pressure and bending/Human physiology monitoring and intelligent robots | Sacrificial
template | ref.82 | Porous | CNTs/ SiNPs/ Si elastomer polymer | 9.5 mm | 0.096 kPa−1 (0 ~ 175 kPa) | | | 10000 times
Consistent (0~ 20 kPa) | Yes/No | Pressure/Human movement behaviors and intelligent robots | 3D - printing | ref.145 | Porous | TPU/CB | | 5.54 kPa−1 (10 Pa ~ 800 kPa) | 10 Pa ~ 800 kPa | 20 ms | 10000 times
Consistent (40~200 kPa) | Yes/No | Pressure/Human physiology monitoring and voice recognition | 3D - printing | ref.147 | Porous | TPU/CB | | 1.12 kPa−1 (20 Pa ~ 60 kPa) | 20 Pa ~ 1.2 MPa | 15 ms | 10000 times
Consistent (0~ 30 kPa) | Yes/Yes | Pressure/Human health and intelligent robots | Sacrificial template | ref.153 | Porous | Multilayer | Gr/Ecoflex | | 4.68 kPa−1 (0 ~ 150 kPa)
11.09 kPa−1 (150 ~ 200 kPa) | Upper limit 200 kPa | | 1000 times
Consistent (0~ 200 kPa) | Yes/Yes | Pressure/Physiological signal detection | Laser scribe | ref.159 | Multilayer | Ti3C2 -MXene/PI | | 180.1 ~ 94.8
(0.19 ~ 0.82% ε) | | 30 ms | 4000 times
Consistent (0~ 7.5 kPa) | Yes/Yes | Pressure and strain/Human’s activities | Etching | ref.160 | Multilayer | GO/Gr | | 0.032 kPa−1 (< 1 kPa) | | | 8000 times
Consistent | Yes/Yes | Human computer interaction/Pressure | Ultrasonic | ref.169 | Combined structures | Hybrid | AgNWs/ PDMS | | 128.29 kPa−1 (0 ~ 200 Pa)
1.28 kPa−1 (0.2 ~ 10 kPa) | 2.5 Pa ~ 8 0 kPa | <100 ms | 10000 times
Consistent (0~ 10 kPa) | Yes/No | Pressure/Human physiology monitoring and voice recognition | Laser etching | ref.86 | Textured@Porous | CNTs/PDMS | ~ 1 mm | 83.9 kPa −1 (<140 Pa) | 0.5 Pa ~ 10 kPa | 170 ms | 29000 times
Consistent | Yes/No | Pressure/Human physiology monitoring and voice recognition | Soft lithography/ sacrificial
template | ref.106 | Conical frustum-like structures | Ag/PDMS | | 259.32 kPa −1 (0.36 Pa ~ 2.5 kPa) | 0.36 Pa - 54 kPa | 200 μs | 1000 times
Consistent (0~ 0.47 kPa) | Yes/No | Pressure/Health monitoring and intelligent robots | Lithography/Deposition | ref.107 | Crack @Porous | PANI/PDMS | ~ 300 mm | ~0.055 kPa−1 (4 Pa ~ 5 kPa)
10
(ε = 25%) | Lower limit 4 Pa | 60 ms | 500 times
Hysteresis (0~5% ε) | Yes/Yes | Pressure, strain, shear and torsion/Human movement behaviors | Sacrificial
template /Stretching | ref.132 | Crack @Porous | Gold@PU | | 59 ~ 122 Pa−1 (0 ~ 14.2 kPa) | Lower limit 0.568 Pa | 9 ms | 1000 times
Consistent (0~45% ε) | Yes/Yes | Pressure/Voice recognition and vehicle speed calculation | Ion sputtering/ Compress | ref.134 | Others | Sandwich | PEDOT:PSS/ AgNWs/ PDMS | 1 mm | 8.0
(ε = 40%) | 50% ε (Max) | | 300 times
Consistent (0~30% ε) | Yes/Yes | Strain/Finger motions | Transfer - printing technique | ref.74 | Sandwich | WGF/PVA/PI | | 4.52kPa−1 (0 ~ 3 kPa)
28.34kPa−1 (3 ~ 10 kPa) | 2.24 Pa ~14 kPa | 87 ms | 6000 times
Consistent | Yes/Yes | Pressure/Human movement behaviors | Electrospinning and ink - jet print | ref.117 |
|
Table 1. Summary on the parameters of current piezoresistive sensors.