
- Photonics Research
- Vol. 10, Issue 2, 303 (2022)
Abstract
1. INTRODUCTION
In the last two decades, chiral metamaterials with helical structures have attracted significant attention because they exhibit novel optical properties, such as circular dichroism [1], optical activity [2], and negative refractive index [3,4]. Helical structures have many applications including broadband circular polarizers [2,5], circular polarization conversion [6], wave plates [7], and broadband polarization-insensitive absorbers [8]. Helical structures can also be found in microfluidic mixers [9,10], heat diffusors [11,12], and scaffolds for growing cells [13].
Producing helical structures requires nonplanar fabrication methods such as multiphoton polymerization (MPP). MPP is a direct laser writing technique that is increasingly used [1,5,6,14–18] because it provides a means for creating almost arbitrarily shaped, three-dimensional (3D) structures with high resolution. However, MPP is time consuming due to the point-by-point writing strategy. The slow fabrication speed of conventional MPP is the key factor that limits its wider adoption for industrial manufacturing over large surface areas. One approach for increasing fabrication speed is to reshape the laser beam so that one entire layer or even the complete structure could be fabricated with a single exposure. Layer-by-layer fabrication of various extruded tube-like 3D structures has been demonstrated by focusing shaped Bessel beams [19–23]. The fabrication is achieved by scanning the focused beam along the optical axis, but the increase in throughput is limited because axial scanning is still needed. Volumetric fabrication with a single exposure has also been demonstrated, including the fabrication of high-aspect-ratio structures using Bessel [24,25] and axilens beams [26]. However, the shape of the structures is limited by the needle-like focal shape and thus lacks variety. Vortex beams have been used to fabricate 3D helical structures with limited aspect ratios [27–29]. For good optical and mechanical functionality, helical structures are often required to have multiple pitches and high aspect ratios, such as those used as microfluidic mixers [9,10]. Metamaterials consisting of high-aspect-ratio helices with multiple pitches exhibit superior performance [2,5,14,30,31]. However, methods reported in Refs. [27–29] achieved only low-aspect-ratio helical structures with less than one pitch. So far, no method has the throughput required for fabricating over large areas with tall helices that have variable pitch.
This work reports a fabrication approach based on MPP with a single exposure using a new class of self-accelerating beams (SABs) with rotating intensity distribution [32–35]. The proposed SABs are based on the superposition of two high-order Bessel beams. Compared to the existing radial SABs with constant rotation rates, the proposed beams feature tunable angular acceleration (variable pitch). Moreover, the rotation rate (and hence pitch) can be tailored to follow a nearly arbitrary profile within the limit of optical arrangement, while other SABs with angular acceleration reported in Refs. [36–38] follow a specific equation with a single tuning parameter. We have developed an analytical model to describe the generation and propagation of the SABs. A closed-form solution for the intensity distribution and rotation rate is derived, which gives insight into the relationship between the computer-generated hologram (CGH) and the beam profile it generates. The analytic model makes it easier to synthesize 3D beams and contrasts with iterative algorithms used by others, which can produce useful solutions, but yield little intuition into how the beams are generated and are time consuming. Micro-helices with constant and varying pitches are fabricated with single exposures in the forms of individual helices and matrices of helices. With optimization, this method can be used to increase throughput by more than two orders of magnitude over conventional MPP and paves the way for mass microfabrication of helical structures for industrial applications, including metamaterials, microfluidics, and biomaterials.
Sign up for Photonics Research TOC. Get the latest issue of Photonics Research delivered right to you!Sign up now
2. EXPERIMENTAL SETUP
Figure 1(a) shows the fabrication system. The light-source is a femtosecond laser (Pharos, Light Conversion) that generates pulses having a temporal full-width at half-maximum (FWHM) of 170 fs, center wavelength of
Figure 1.High-throughput microfabrication of helical structures using self-accelerating beams (SABs). (a) Experimental setup: BBO, beta barium borate crystal; PBS, polarizing beam splitter; BE, beam expander; BS, non-polarizing beam splitter; SLM, spatial light modulator; M, mirror; L, lens; ID, iris diaphragm; Obj, objective lens; CMOS, complementary metal–oxide-semiconductor. (b) Calculation of a computer-generated hologram (CGH). Phase order
3. THEORY AND CGH DESIGN
A light field with rotating intensity distribution can be generally described as
Various types of beams have been generated with constant rotation rates. Here we present a general method that produces SABs with axially tunable
The foundation of our SABs is the superposition of two high-order Bessel beams and the use of radial-to-axial (“
Superposing two Bessel beams having
The superposition of these two components gives a transmittance function
The encoded phase
Using the Fresnel diffraction theory and the stationary phase method [40,47,48], we can derive a closed-form solution for the intensity distribution at point
The terms on the right-hand side of Eq. (6) differ by
We are more interested in generating an SAB that has a pre-defined
4. CHARACTERIZATION OF SELF-ACCELERATING BEAMS IN FREE SPACE
The SABs generated by the proposed method are measured in free space to validate the theory. A CMOS camera with a
Figure 2.Comparison of simulated and measured helical beams with (a)–(d) constant and (e)–(h) decelerated rotation rate. Phase order
The first example is an SAB with a constant rotation rate
Another class of SAB has rotation rate
5. PROPAGATION THROUGH INTERFACES
The discussion so far is in free space. In actual fabrication, the SABs pass through multiple interfaces (air–glass, glass–SU-8). Therefore, it is important to understand how SABs propagate through a planar interface of two media with different refractive indices
6. FABRICATION OF MICRO-HELICES
Equation (7) was used to design CGHs that generate SABs for fabricating helices in SU-8 (
Figure 3.Comparison between helical beams simulated in SU-8 and fabrication results obtained with five SABs having different types of rotation. The contrast of each SEM image was adjusted individually to improve visibility and aid comparison. Scale bar corresponds to 20 μm.
The left column of Fig. 3 shows the beams used to produce the helical structures. The first two helices [Figs. 3(a) and 3(b)] have constant rotation rate
To examine the shape of fabricated helices quantitatively, we use images of single helices and trace their edges. An example is shown in Fig. 4 for a decelerating helix. We have tested various edge-detection algorithms (see Appendix D) and found that their accuracy varies with the specific SEM images given. Therefore, we have decided to extract the edge manually. Since part of the edge is unseen from the SEM image [Fig. 4(a)], a transmission optical microscopic image is used to perform measurements [Fig. 4(b)]. Then the distance
Figure 4.Characterization of a fabricated helix. (a) SEM image of the helix with one edge highlighted. (b) One edge (red solid curve) of the helix is extracted from the optical microscopic image, and the distance
By performing a series of single exposures with lateral translation, helical matrices can be fabricated. Figure 5 shows several matrices, each consisting of
Figure 5.Matrices of various helical structures fabricated by a combination of exposure and linear translation.
7. CONCLUSION
We have demonstrated a method for rapid microfabrication of helical structures with tunable axial shapes by developing a new class of SABs and adapting them to MPP. The SABs are based on the superposition of high-order Bessel modes and form non-diffracting irradiance profiles that rotate along the optical axis. An algorithm was developed to design CGHs that form the SABs. A closed-form expression was derived that can be used to directly synthesize targeted CGH and SAB without resorting to iterative algorithms that yield non-intuitive results. SABs can be generated with independently adjustable transverse width and rotational pitch. Using the concept of
APPENDIX A: GENERATION AND PROPAGATION OF SABS IN FREE SPACE
An SAB with rotating intensity distribution can be generally described as
A special group of SABs with constant
The superposition
In Eqs. (
A CGH described by Eq. (
Figure 6.Propagation model used in the derivation.
In Eq. (
Equations (
Using the Fresnel diffraction integral in cylindrical coordinates, we can write the complex field at point
Substituting Eqs. (
Using an integral representation of Bessel functions [
Because the phase term
Now we can superpose Eq. (
It is obvious that
Equation (
Substituting Eq. (
When the function
Treating
Equation (
APPENDIX B: TUNING TRANSVERSE BEAM PROFILE
Notice that Eqs. (
Figure 7.Simulation results of two beams with (a) large and (b) small helical diameters generated by changing the phase order
APPENDIX C: PROPAGATION THROUGH AN INTERFACE
Now we consider the situation in which the beam propagates from air through the air–photoresist interface. Here we ignore the glass substrate because it is thin (
Figure 8.Schematic for the propagation of helical beams into photoresist. L2 is the second lens of the
Figure 9.(a) Theory and (b) simulation of intensity distribution on the
APPENDIX D: CHARACTERIZATION OF HELICAL STRUCTURES
To examine the shape of the fabricated helices quantitatively, we use images of single helices and trace their edges. An example is shown in Figs.
Figure 10.Characterization of a fabricated helix from an SEM image. (a) Original image. (b) The edges are detected from the image by edge-detection algorithms. (c) Noise is suppressed and only one edge is displayed. (d) Locations along the edge are plotted.
Figure 11.Characterization of a fabricated helix from a transmissive optical microscopic image. Red curve overlayed on the image is used to illustrate the edge that is extracted.
APPENDIX E: ESTIMATION OF FABRICATION TIME
Here we compare the time required to fabricate one helical structure using the high-throughput method reported in this work to that required for MPP by conventional point-by-point scanning. The scanning rate is the major bottleneck in the fabrication time for MPL, and it can be improved by moving the beam using galvo-mirrors, instead of translating the sample with a piezo-stage [
References
[1] M. Thiel, M. Decker, M. Deubel, M. Wegener, S. Linden, G. von Freymann. Polarization stop bands in chiral polymeric three-dimensional photonic crystals. Adv. Mater., 19, 207-210(2007).
[2] J. K. Gansel, M. Thiel, M. S. Rill, M. Decker, K. Bade, V. Saile, G. von Freymann, S. Linden, M. Wegener. Gold helix photonic metamaterial as broadband circular polarizer. Science, 325, 1513-1515(2009).
[3] J. B. Pendry. A chiral route to negative refraction. Science, 306, 1353-1355(2004).
[4] E. Plum, J. Zhou, J. Dong, V. A. Fedotov, T. Koschny, C. M. Soukoulis, N. I. Zheludev. Metamaterial with negative index due to chirality. Phys. Rev. B, 79, 035407(2009).
[5] J. K. Gansel, M. Latzel, A. Frölich, J. Kaschke, M. Thiel, M. Wegener. Tapered gold-helix metamaterials as improved circular polarizers. Appl. Phys. Lett., 100, 101109(2012).
[6] J. Kaschke, L. Blume, L. Wu, M. Thiel, K. Bade, Z. Yang, M. Wegener. A helical metamaterial for broadband circular polarization conversion. Adv. Opt. Mater., 3, 1411-1417(2015).
[7] C. Wu, H. Li, X. Yu, F. Li, H. Chen, C. T. Chan. Metallic helix array as a broadband wave plate. Phys. Rev. Lett., 107, 177401(2011).
[8] Z. Lu, M. Zhao, Z. Yang, L. Wu, P. Zhang, Y. Zheng, J. Duan. Broadband polarization-insensitive absorbers in 0.3–25 μm using helical metamaterials. J. Opt. Soc. Am. B, 30, 1368-1372(2013).
[9] M. K. S. Verma, S. R. Ganneboyina, , A. Ghatak. Three-dimensional multihelical microfluidic mixers for rapid mixing of liquids. Langmuir, 24, 2248-2251(2008).
[10] C. Shan, F. Chen, Q. Yang, Z. Jiang, X. Hou. 3D multi-microchannel helical mixer fabricated by femtosecond laser inside fused silica. Micromachines, 9, 29(2018).
[11] M. I. Hussain, G. H. Lee, B. Engineering. Numerical thermal analysis of helical-shaped heat exchanger to improve thermal stratification inside solar. International Conference on Agricultural and Environmental Engineering, 6-10(2014).
[12] E. S. Shukri. Numerical comparison of temperature distribution in an annular diffuser fitted with helical screw-tape hub and pimpled hub. Energy Proc., 141, 625-629(2017).
[13] A. V. Do, B. Khorsand, S. M. Geary, A. K. Salem. 3D printing of scaffolds for tissue regeneration applications. Adv. Healthcare Mater., 4, 1742-1762(2015).
[14] M. Thiel, M. S. Rill, G. von Freymann, M. Wegener. Three-dimensional bi-chiral photonic crystals. Adv. Mater., 21, 4680-4682(2009).
[15] J. Kaschke, M. Wegener. Gold triple-helix mid-infrared metamaterial by STED-inspired laser lithography. Opt. Lett., 40, 3986-3989(2015).
[16] Y. Liu, J. Campbell, O. Stein, L. Jiang, J. Hund, Y. Lu. Deformation behavior of foam laser targets fabricated by two-photon polymerization. Nanomaterials, 8, 498(2018).
[17] G. Kumi, C. O. Yanez, K. D. Belfield, J. T. Fourkas. High-speed multiphoton absorption polymerization: fabrication of microfluidic channels with arbitrary cross-sections and high aspect ratios. Lab Chip, 10, 1057-1060(2010).
[18] S. Kawata, H. B. Sun, T. Tanaka, K. Takada. Finer features for functional microdevices. Nature, 412, 697-698(2001).
[19] L. Yang, S. Ji, K. Xie, W. Du, B. Liu, Y. Hu, J. Li, G. Zhao, D. Wu, W. Huang, S. Liu, H. Jiang, J. Chu. High efficiency fabrication of complex microtube arrays by scanning focused femtosecond laser Bessel beam for trapping/releasing biological cells. Opt. Express, 25, 8144-8157(2017).
[20] S. Ji, L. Yang, C. Zhang, Z. Cai, Y. Hu, J. Li, D. Wu, J. Chu. High-aspect-ratio microtubes with variable diameter and uniform wall thickness by compressing Bessel hologram phase depth. Opt. Lett., 43, 3514-3517(2018).
[21] S. Ji, L. Yang, Y. Hu, J. Ni, W. Du, J. Li, G. Zhao, D. Wu, J. Chu. Dimension-controllable microtube arrays by dynamic holographic processing as 3D yeast culture scaffolds for asymmetrical growth regulation. Small, 13, 1701190(2017).
[22] L. Yang, D. Qian, C. Xin, Z. Hu, S. Ji, D. Wu, Y. Hu, J. Li, W. Huang, J. Chu. Two-photon polymerization of microstructures by a non-diffraction multifoci pattern generated from a superposed Bessel beam. Opt. Lett., 42, 743-746(2017).
[23] L. Yang, D. Qian, C. Xin, Z. Hu, S. Ji, D. Wu, Y. Hu, J. Li, W. Huang, J. Chu. Direct laser writing of complex microtubes using femtosecond vortex beams. Appl. Phys. Lett., 110, 221103(2017).
[24] H. Cheng, C. Xia, M. Zhang, S. M. Kuebler, X. Yu. Fabrication of high-aspect-ratio structures using Bessel-beam-activated photopolymerization. Appl. Opt., 58, D91-D97(2019).
[25] J. Jezek, T. Cizmár, V. Nedela, P. Zemánek. Formation of long and thin polymer fiber using nondiffracting beam. Opt. Express, 14, 8506-8515(2006).
[26] D. Pan, B. Xu, S. Liu, J. Li, Y. Hu, D. Wu, J. Chu. Amplitude-phase optimized long depth of focus femtosecond axilens beam for single-exposure fabrication of high-aspect-ratio microstructures. Opt. Lett., 45, 2584-2587(2020).
[27] S.-J. Zhang, Y. Li, Z.-P. Liu, J.-L. Ren, Y.-F. Xiao, H. Yang, Q. Gong. Two-photon polymerization of a three dimensional structure using beams with orbital angular momentum. Appl. Phys. Lett., 105, 061101(2014).
[28] J. Ni, C. Wang, C. Zhang, Y. Hu, L. Yang, Z. Lao, B. Xu, J. Li, D. Wu, J. Chu. Three-dimensional chiral microstructures fabricated by structured optical vortices in isotropic material. Light Sci. Appl., 6, e17011(2017).
[29] Y. Li, L. Liu, D. Yang, Q. Zhang, H. Yang, Q. Gong. Femtosecond laser nano/microfabrication via three-dimensional focal field engineering. Proc. SPIE, 10092, 100920B(2017).
[30] J. Kaschke, J. K. Gansel, M. Wegener. On metamaterial circular polarizers based on metal
[31] J. K. Gansel, M. Wegener, S. Burger, S. Linden. Gold helix photonic metamaterials: a numerical parameter study. Opt. Express, 18, 1059-1069(2010).
[32] C. Vetter, T. Eichelkraut, M. Ornigotti, A. Szameit. Optimization and control of two-component radially self-accelerating beams. Appl. Phys. Lett., 107, 211104(2015).
[33] C. Vetter, T. Eichelkraut, M. Ornigotti, A. Szameit. Generalized radially self-accelerating helicon beams. Phys. Rev. Lett., 113, 183901(2014).
[34] R. Rop, A. Dudley, C. López-Mariscal, A. Forbes. Measuring the rotation rates of superpositions of higher-order Bessel beams. J. Mod. Opt., 59, 259-267(2012).
[35] R. Vasilyeu, A. Dudley, N. Khilo, A. Forbes. Generating superpositions of higher-order Bessel beams. Opt. Express, 17, 23389-23395(2009).
[36] C. Schulze, F. S. Roux, A. Dudley, R. Rop, M. Duparré, A. Forbes. Accelerated rotation with orbital angular momentum modes. Phys. Rev. A, 91, 043821(2015).
[37] C. Vetter, A. Dudley, A. Szameit, A. Forbes. Real and virtual propagation dynamics of angular accelerating white light beams. Opt. Express, 25, 20530-20540(2017).
[38] J. Webster, C. Rosales-Guzmán, A. Forbes. Radially dependent angular acceleration of twisted light. Opt. Lett., 42, 675-678(2017).
[39] H. Cheng, C. Xia, S. M. Kuebler, X. Yu. Aberration correction for SLM-generated Bessel beams propagating through tilted interfaces. Opt. Commun., 475, 126213(2020).
[40] A. Vasara, J. Turunen, A. T. Friberg. Realization of general nondiffracting beams with computer-generated holograms. J. Opt. Soc. Am. A, 6, 1748-1754(1989).
[41] N. Chattrapiban, E. A. Rogers, D. Cofield, W. T. Hill, R. Roy. Generation of nondiffracting Bessel beams by use of a spatial light modulator. Opt. Lett., 28, 2183-2185(2003).
[42] C. Paterson, R. Smith. Higher-order Bessel waves produced by axicon-type computer-generated holograms. Opt. Commun., 124, 121-130(1996).
[43] X. Yu, A. Todi, H. Tang. Bessel beam generation using a segmented deformable mirror. Appl. Opt., 57, 4677-4682(2018).
[44] H. Cheng, C. Xia, S. M. Kuebler, P. Golvari, M. Sun, M. Zhang, X. Yu. Generation of Bessel-beam arrays for parallel fabrication in two-photon polymerization. J. Laser Appl., 33, 012040(2021).
[45] X. Yu, C. A. Trallero-Herrero, S. Lei. Materials processing with superposed Bessel beams. Appl. Surf. Sci., 360, 833-839(2016).
[46] O. Mendoza-Yero, G. Mínguez-Vega, J. Lancis. Encoding complex fields by using a phase-only optical element. Opt. Lett., 39, 1740-1743(2014).
[47] L. B. Felsen, N. Marcuvitz. Radiation and Scattering of Waves(1994).
[48] A. V. Osipov, S. A. Tretyakov. Modern Electromagnetic Scattering Theory with Applications(2017).
[49] J. Arlt, K. Dholakia. Generation of high-order Bessel beams by use of an axicon. Opt. Commun., 177, 297-301(2000).
[50] V. Jarutis, R. Paškauskas, A. Stabinis. Focusing of Laguerre–Gaussian beams by axicon. Opt. Commun., 184, 105-112(2000).
[51] G. Whyte, J. Courtial. Experimental demonstration of holographic three-dimensional light shaping using a Gerchberg–Saxton algorithm. New J. Phys., 7, 117(2005).
[52] B. Hadad, S. Froim, H. Nagar, T. Admon, Y. Eliezer, Y. Roichman, A. Bahabad. Particle trapping and conveying using an optical Archimedes’ screw. Optica, 5, 551-556(2018).
[53] A. Terray. Microfluidic control using colloidal devices. Science, 296, 1841-1844(2002).
[54] P. Galajda, P. Ormos. Rotors produced and driven in laser tweezers with reversed direction of rotation. Appl. Phys. Lett., 80, 4653-4655(2002).
[55] J. W. Goodman. Introduction to Fourier Optics(2005).
[56] H. Lee, K. Lee, B. Ahn, J. Xu, L. Xu, K. W. Oh. A new fabrication process for uniform SU-8 thick photoresist structures by simultaneously removing edge bead and air bubbles. J. Micromech. Microeng., 21, 125006(2011).
[57] W. Zhou. An efficient two-photon-generated photoacid applied to positive-tone 3D microfabrication. Science, 296, 1106-1109(2002).
[58] S. Li, Z. Yang, J. Wang, M. Zhao. Broadband terahertz circular polarizers with single- and double-helical array metamaterials. J. Opt. Soc. Am. A, 28, 19-23(2011).
[59] Y. Yu, Z. Yang, M. Zhao, P. Lu. Broadband optical circular polarizers in the terahertz region using helical metamaterials. J. Opt., 13, 055104(2011).
[61] C. N. LaFratta, L. Li. Making two-photon polymerization faster. Three-Dimensional Microfabrication Using Two-Photon Polymerization, 385-408(2020).
[62] M. A. Skylar-Scott, M. C. Liu, Y. Wu, A. Dixit, M. F. Yanik. Guided homing of cells in multi-photon microfabricated bioscaffolds. Adv. Healthc. Mater., 5, 1233-1243(2016).
[63] B. W. Pearre, C. Michas, J. M. Tsang, T. J. Gardner, T. M. Otchy. Fast micron-scale 3D printing with a resonant-scanning two-photon microscope. Addit. Manuf., 30, 100887(2019).
[64] A. Ovsianikov, A. Deiwick, S. Van Vlierberghe, P. Dubruel, L. Möller, G. Drager, B. Chichkov. Laser fabrication of three-dimensional CAD scaffolds from photosensitive gelatin for applications in tissue engineering. Biomacromolecules, 12, 851-858(2011).
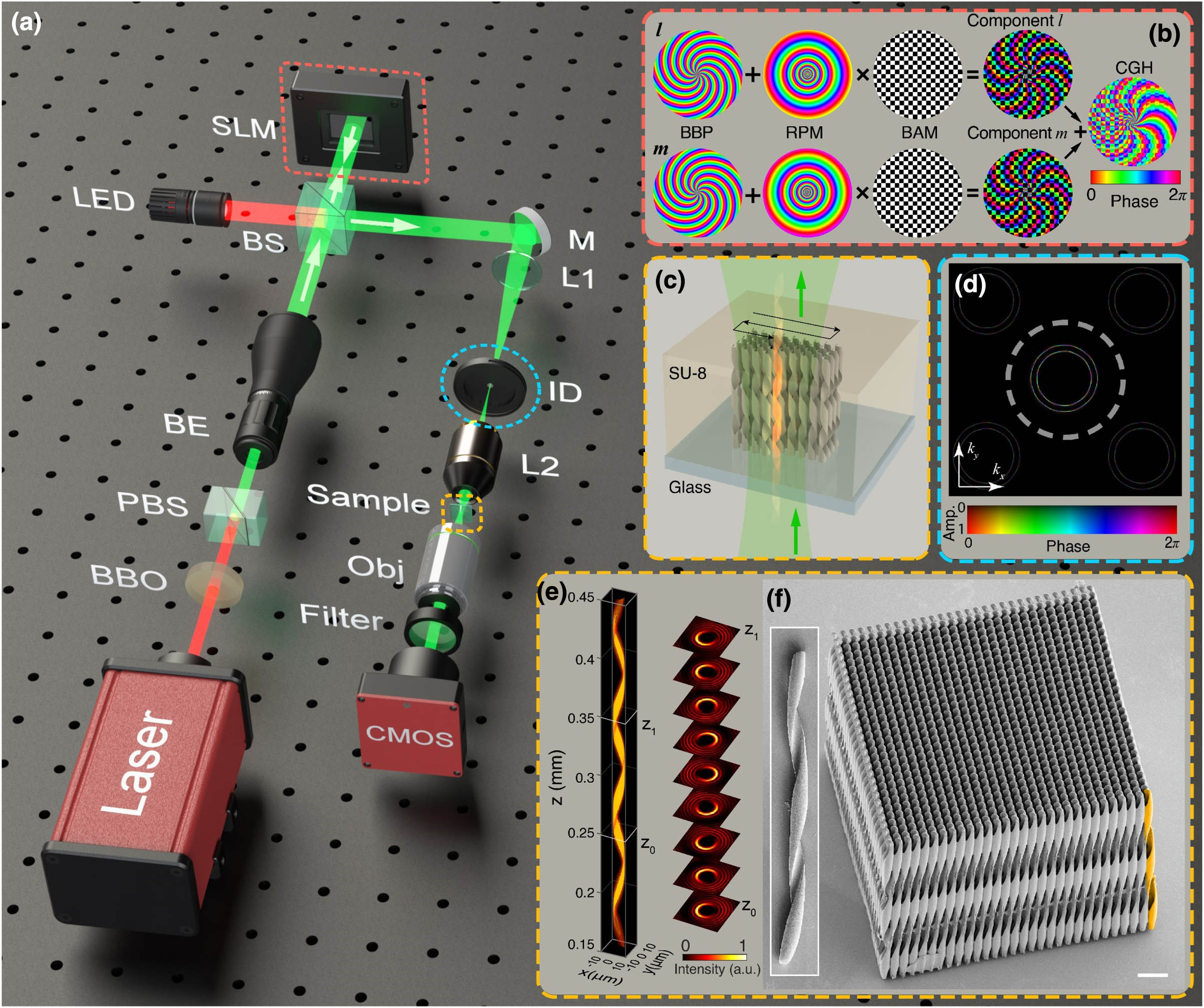
Set citation alerts for the article
Please enter your email address