
- Photonics Research
- Vol. 9, Issue 10, 2016 (2021)
Abstract
1. INTRODUCTION
In optomechanics, the motion of mechanical resonators is typically controlled by using laser light reflected from a mirror [1–7]. Therefore, the optical force that drives these mechanical resonators is the well-known radiation pressure of light incident from free space. However, light can also exert forces while it is propagating inside materials, and in particular, when it is crossing material interfaces. Mostly, these forms of optical forces are studied in liquids by observing the deformation or movement of liquid surfaces under optical excitation [8–13]. There also exist measurements of the steady-state radiation pressure on mirrors immersed in liquids [14,15]. Experiments on the forces of light in lossless solids have been very scarce and rather qualitative or hindered by the lossy nature of solids [16–23]. From literature, one can conclude that previous works have used neither mechanical resonators nor optical fibers to quantitatively measure optical forces inside materials. This is surprising and calls for a change since optical forces have an important role, e.g., in whispering gallery mode resonators [24,25] and as a source of cross talk in multi-core fibers [26].
Among solid dielectric media, silica optical fiber is considered to be de facto the lowest-loss medium with the highest uniformity along its length [27], yet the forces of light carried by the optical fiber have not been quantified in experiments yet. In this work, we propose a macroscopic oscillator platform to interferometrically quantify the forces of light, which is being guided through a silica optical fiber for the first time to the best knowledge of the authors. We used cleaved optical fiber strands bonded to a macroscopic oscillator to make the light propagating through the optical fiber the only driving force of the oscillator. Our platform is schematically illustrated in Fig. 1. A 3D printed mass was suspended by a spring at the center and, on both sides, the cleaved optical fibers were glued. Our experiment leaves no room for different interpretations of the origin of the oscillator signal but the forces of light propagating through the optical fibers. In particular, heating effects, whose consequences in many prior cases have dominated over the optical momentum transfer, are negligible, because light propagating inside a commercial multimode optical fiber of less than a meter experiences a loss less than 0.002 dB. Thermal effects are also hindered by the large thermal time constant of the macroscopic oscillator [4,28].
Figure 1.(a) Mechanical oscillator was driven by optical interface forces
A 3D printed mass was designed to be held by a spring at the center and balanced by optical fiber strands glued at both ends, as illustrated in Fig. 1(a). A laser was split into four strands of commercial 0.22 NA multimode optical fibers (Thorlabs, FG105LCA) with equal optical power using a
Sign up for Photonics Research TOC. Get the latest issue of Photonics Research delivered right to you!Sign up now
2. OPTICAL FORCES
The optical forces induced by the light guided in the optical fiber can be divided into the force at the air–silica interface of the optical fiber facet and the tension along the fiber strands as schematically shown by
Positive and negative values of
When light propagates along a bent fiber, the optical force pushes the fiber walls unequally at different sides, and the net momentum flux of light changes its direction. This is a direct consequence of the momentum conservation law. The optical force on the fiber walls points in the direction of the positive curvature, which is always normal to the fiber as indicated by the small arrows in Fig. 1(a). From the elasticity theory (see Appendix A), it follows that this normal force gives rise to tension in the longitudinal direction of the fiber. The net tension of the four fibers is given by
Here
From the optical interface force in Eq. (1) and the tension along fibers in Eq. (2), the net time-dependent driving force of the mechanical oscillator is given by
The net force in Eq. (3) is interestingly independent of the value of the momentum of light inside the fiber since the dependence on
3. MECHANICAL OSCILLATOR
For the mechanical oscillator used to detect the net laser-induced force, we write Newton’s equation of motion as [29]
The net force due to a laser beam harmonically modulated with angular frequency
Here
4. RESULTS AND DISCUSSION
The refractive index of the pure silica core of the fiber is
Figure 2 presents the experimental results. In Fig. 2(a), the measured displacement amplitude of the first oscillator driven at 808 nm is plotted as a function of the modulation frequency of the driving laser field. Figure 2(b) presents the same plot for the second oscillator driven at 915 nm. The net peak-to-peak power amplitude of the four fibers used in these plots is
Figure 2.Displacement amplitude of the mechanical oscillator is plotted as a function of the laser modulation frequency (a) for the first oscillator at the wavelength of 808 nm and (b) for the second oscillator at the wavelength of 915 nm. The net peak-to-peak power amplitude of the driving field in the four fibers together is
In Figs. 2(a) and 2(b), one can see that the fitted harmonic oscillator response function of Eq. (5) accurately describes the experimental results of both oscillators. One can also observe the mechanical resonance peak in the noise spectrum that appears below the fitted response function. In the presence of photothermal effects, the response function would be modified from the ideal harmonic oscillator form as described, e.g., in Refs. [4,32]. In accordance with the results for the free space laser driven oscillator in Ref. [28], the photothermal effects are determined to be negligible for our macroscopic oscillator.
The fitting of the harmonic oscillator response function in the experimental data of the first oscillator in Fig. 2(a) gives the undamped frequency of the oscillator equal to
Figures 2(c) and 2(d) present the measured peak-to-peak force amplitudes of the two oscillators following Eq. (6) as a function of the peak-to-peak laser power amplitude. The slope of the regression line of the first oscillator is
To the best knowledge of the authors, the only previous measurement of forces of light exiting from a solid medium is in Ref. [18]. In their measurements, She
For a more detailed investigation of the refractive index dependence of the total oscillator force, the present experiment could be carried out by using optical fibers with different refractive indices. The refractive index would need to deviate from that of fused silica by an amount that would change the experimental results sufficiently compared to the error bars of the experiment. Presently, there are no such solid-core optical fibers available that would also have low loss. The experiment could also be carried out by using a hollow-core photonic crystal fiber.
5. CONCLUSION
In summary, we have demonstrated that optical forces of light in an optical fiber can be quantitatively measured
Acknowledgment
Acknowledgment. The authors acknowledge support from the National Research Foundation of Korea (NRF) grant by the Korea government (MSIT) under Contract No. 2019R1A2C2011293. M.P. acknowledges support from the European Union’s Horizon 2020 Marie Skłodowska-Curie Actions (MSCA) individual fellowship under Contract No. 846218.
APPENDIX A
The mechanical oscillator masses were fabricated by 3D printing using the fused deposition modeling (FDM) technique. The printing material was polylactic acid, commonly known as PLA. As illustrated in Fig.
The driving laser beam at 808 nm was generated by a multimode laser diode module (Box Optronics, BLD-F808-06-22N0), and the laser beam at 915 nm was generated by a multimode laser diode module (Box Optronics, BLD-F915-10-22N0). The laser beams were coupled to a commercial low-loss 0.22 NA silica core multimode fiber (Thorlabs, FG105LCA). The core diameter of the fiber was
The laser power was measured at the ends of the optical fibers by using an optical power meter (Thorlabs, PM400) with an integrating sphere sensor (Thorlabs, S145C). The nonzero reflectivity (
In the experimental setup, the mechanical oscillator was hanging on three hard extension springs used in series to obtain a relatively small total spring constant. The springs were made of music wire, and they had crossover-type hooks at their ends. The upper and lower springs were of equal type (Acxess Spring, PE016-312-129000-MW-2500-MH-N-IN) having a mass of
The experimental setup was mounted on an actively damped optical table for isolating it against acoustic and seismic vibrations. The mechanical oscillator part of the setup was also protected against air flows by covering it with plastic walls. To minimize any disturbances in the surroundings of the laboratory, the measurements were carried out at nighttime.
The motion of the mechanical oscillator was detected by a Michelson interferometer. The interferometer was used to monitor the motion of the oscillator by setting the oscillator mirror in one of the two interferometer arms. The arm length of the interferometer was about 10 cm. One of the interferometer arm mirrors was motorized, and it could be used for tuning the interference fringe spacing remotely. However, the fringe spacing was adjusted only before each measurement, and it was not actively changed during the experiments. All mirrors in the interferometer arms (Thorlabs, BB1-E02) had a reflectivity of more than 99%. The interferometer laser was a 5 mW continuous-wave
The horizontal movement of the interference fringes was tracked from the recorded video files by monitoring the positions of the intensity maxima and minima in each frame. The fringes are illustrated in the computer screen of Fig.
This section describes how the elasticity theory calculations are used to verify the accuracy of the analytic result in Eq. (
Figure 3.Illustration of the fiber path and the related horizontal and vertical distance parameters
Figure 4.Elasticity theory simulation of the total tension force of four fibers on the oscillator as a function of the total incident optical power propagating through the fibers. The dots represent the simulation results obtained by using the expression on the left-hand side of Eq. (
We have also made simulations for several values of loose in the fiber in the range
References
[1] S. Gigan, H. R. Böhm, M. Paternostro, F. Blaser, G. Langer, J. B. Hertzberg, K. C. Schwab, D. Bäuerle, M. Aspelmeyer, A. Zeilinger. Self-cooling of a micromirror by radiation pressure. Nature, 444, 67-70(2006).
[2] D. Kleckner, D. Bouwmeester. Sub-kelvin optical cooling of a micromechanical resonator. Nature, 444, 75-78(2006).
[3] D. M. Weld, A. Kapitulnik. Feedback control and characterization of a microcantilever using optical radiation pressure. Appl. Phys. Lett., 89, 164102(2006).
[4] D. Ma, J. L. Garrett, J. N. Munday. Quantitative measurement of radiation pressure on a microcantilever in ambient environment. Appl. Phys. Lett., 106, 091107(2015).
[5] D. R. Evans, P. Tayati, H. An, P. K. Lam, V. S. J. Craig, T. J. Senden. Laser actuation of cantilevers for picometre amplitude dynamic force microscopy. Sci. Rep., 4, 5567(2014).
[6] R. Wagner, F. Guzman, A. Chijioke, G. K. Gulati, M. Keller, G. Shaw. Direct measurement of radiation pressure and circulating power inside a passive optical cavity. Opt. Express, 26, 23492-23506(2018).
[7] P. R. Wilkinson, G. A. Shaw, J. R. Pratt. Determination of a cantilever’s mechanical impedance using photon momentum. Appl. Phys. Lett., 102, 184103(2013).
[8] N. G. C. Astrath, L. C. Malacarne, M. L. Baesso, G. V. B. Lukasievicz, S. E. Bialkowski. Unravelling the effects of radiation forces in water. Nat. Commun., 5, 4363(2014).
[9] A. Ashkin, J. M. Dziedzic. Radiation pressure on a free liquid surface. Phys. Rev. Lett., 30, 139-142(1973).
[10] A. Casner, J.-P. Delville. Giant deformations of a liquid–liquid interface induced by the optical radiation pressure. Phys. Rev. Lett., 87, 054503(2001).
[11] H. Choi, M. Park, D. S. Elliott, K. Oh. Optomechanical measurement of the Abraham force in an adiabatic liquid-core optical-fiber waveguide. Phys. Rev. A, 95, 053817(2017).
[12] F. A. Schaberle, L. A. Reis, C. Serpa, L. G. Arnaut. Photon momentum transfer at water/air interfaces under total internal reflection. New J. Phys., 21, 033013(2019).
[13] L. Zhang, W. She, N. Peng, U. Leonhardt. Experimental evidence for Abraham pressure of light. New J. Phys., 17, 053035(2015).
[14] R. V. Jones, J. C. S. Richards. The pressure of radiation in a refracting medium. Proc. R. Soc. London A, 221, 480-498(1954).
[15] R. V. Jones, B. Leslie. The measurement of optical radiation pressure in dispersive media. Proc. R. Soc. London A, 360, 347-363(1978).
[16] A. Kundu, R. Rani, K. S. Hazra. Graphene oxide demonstrates experimental confirmation of Abraham pressure on solid surface. Sci. Rep., 7, 42538(2017).
[17] A. F. Gibson, M. F. Kimmitt, A. C. Walker. Photon drag in germanium. Appl. Phys. Lett., 17, 75-77(1970).
[18] W. She, J. Yu, R. Feng. Observation of a push force on the end face of a nanometer silica filament exerted by outgoing light. Phys. Rev. Lett., 101, 243601(2008).
[19] I. Brevik. Analysis of recent interpretations of the Abraham–Minkowski problem. Phys. Rev. A, 98, 043847(2018).
[20] M. Partanen, J. Tulkki. Comment on ‘Analysis of recent interpretations of the Abraham–Minkowski problem,’. Phys. Rev. A, 100, 017801(2019).
[21] I. Brevik. Reply to ‘Comment on “Analysis of recent interpretations of the Abraham–Minkowski problem,”’. Phys. Rev. A, 100, 017802(2019).
[22] I. Brevik. Comment on ‘Observation of a push force on the end face of a nanometer silica filament exerted by outgoing light,’. Phys. Rev. Lett., 103, 219301(2009).
[23] M. Mansuripur. Comment on ‘Observation of a push force on the end face of a nanometer silica filament exerted by outgoing light’. Phys. Rev. Lett., 103, 019301(2009).
[24] A. Schliesser, G. Anetsberger, R. Rivière, O. Arcizet, T. J. Kippenberg. High-sensitivity monitoring of micromechanical vibration using optical whispering gallery mode resonators. New J. Phys., 10, 095015(2008).
[25] I. Brevik, S. A. Ellingsen. Possibility of measuring the Abraham force using whispering gallery modes. Phys. Rev. A, 81, 063830(2010).
[26] H. H. Diamandi, Y. London, A. Zadok. Opto-mechanical inter-core cross-talk in multi-core fibers. Optica, 4, 289-297(2017).
[27] K. Oh, U.-C. Paek. Silica Optical Fiber Technology for Devices and Components: Design, Fabrication, and International Standards(2012).
[28] M. Partanen, H. Lee, K. Oh. Radiation pressure measurement using a macroscopic oscillator in an ambient environment. Sci. Rep., 10, 20419(2020).
[29] M. Aspelmeyer, T. J. Kippenberg, F. Marquardt. Cavity optomechanics. Rev. Mod. Phys., 86, 1391-1452(2014).
[30] W. T. Thomson, M. Dahleh. Theory of Vibration with Applications(1998).
[31] I. H. Malitson. Interspecimen comparison of the refractive index of fused silica. J. Opt. Soc. Am., 55, 1205-1209(1965).
[32] D. Ma, J. N. Munday. Measurement of wavelength-dependent radiation pressure from photon reflection and absorption due to thin film interference. Sci. Rep., 8, 15930(2018).
[33] M. Abraham. Zur Elektrodynamik bewegter Körper. Rend. Circ. Mat. Palermo, 28, 1(1909).
[34] M. Abraham. Sull’elettrodinamica di Minkowski. Rend. Circ. Mat. Palermo, 30, 33-46(1910).
[35] H. Minkowski. Die Grundgleichungen für die elektromagnetischen Vorgänge in bewegten Körpern. Nachrichten von der Gesellschaft der Wissenschaften zu Göttingen, Mathematisch-Physikalische Klasse, 53(1908).
[36] U. Leonhardt. Momentum in an uncertain light. Nature, 444, 823-824(2006).
[37] R. N. C. Pfeifer, T. A. Nieminen, N. R. Heckenberg, H. Rubinsztein-Dunlop. Colloquium: momentum of an electromagnetic wave in dielectric media. Rev. Mod. Phys., 79, 1197-1216(2007).
[38] S. M. Barnett. Resolution of the Abraham–Minkowski dilemma. Phys. Rev. Lett., 104, 070401(2010).
[39] S. M. Barnett, R. Loudon. “The enigma of optical momentum in a medium. Philos. Trans. R. Soc. A, 368, 927-939(2010).
[40] M. Partanen, T. Häyrynen, J. Oksanen, J. Tulkki. Photon mass drag and the momentum of light in a medium. Phys. Rev. A, 95, 063850(2017).
[41] K. Y. Bliokh, A. Y. Bekshaev, F. Nori. Optical momentum, spin, and angular momentum in dispersive media. Phys. Rev. Lett., 119, 073901(2017).
[42] K. Y. Bliokh, A. Y. Bekshaev, F. Nori. Optical momentum and angular momentum in complex media: from the Abraham–Minkowski debate to unusual properties of surface plasmon-polaritons. New J. Phys., 19, 123014(2017).
[43] M. Partanen, J. Tulkki. Mass-polariton theory of light in dispersive media. Phys. Rev. A, 96, 063834(2017).
[44] B. A. Kemp. Resolution of the Abraham–Minkowski debate: implications for the electromagnetic wave theory of light in matter. J. Appl. Phys., 109, 111101(2011).
[45] M. Partanen, J. Tulkki. Lorentz covariance of the mass-polariton theory of light. Phys. Rev. A, 99, 033852(2019).
[46] M. Partanen, J. Tulkki. Lagrangian dynamics of the coupled field-medium state of light. New J. Phys., 21, 073062(2019).
[47] U. Leonhardt. Abraham and Minkowski momenta in the optically induced motion of fluids. Phys. Rev. A, 90, 033801(2014).
[48] P. W. Milonni, R. W. Boyd. Momentum of light in a dielectric medium. Adv. Opt. Photon., 2, 519-553(2010).
[49] I. Brevik. Experiments in phenomenological electrodynamics and the electromagnetic energy-momentum tensor. Phys. Rep., 52, 133-201(1979).
[50] M. Partanen, J. Tulkki. Light-driven mass density wave dynamics in optical fibers. Opt. Express, 26, 22046-22063(2018).
[51] R. Brückner. Properties and structure of vitreous silica. I. J. Non-Cryst. Solids, 5, 123-175(1970).
[52] B. H. W. S. De Jong, R. G. C. Beerkens, P. A. van Nijnatten. Glass. Ullmann’s Encyclopedia of Industrial Chemistry(2000).
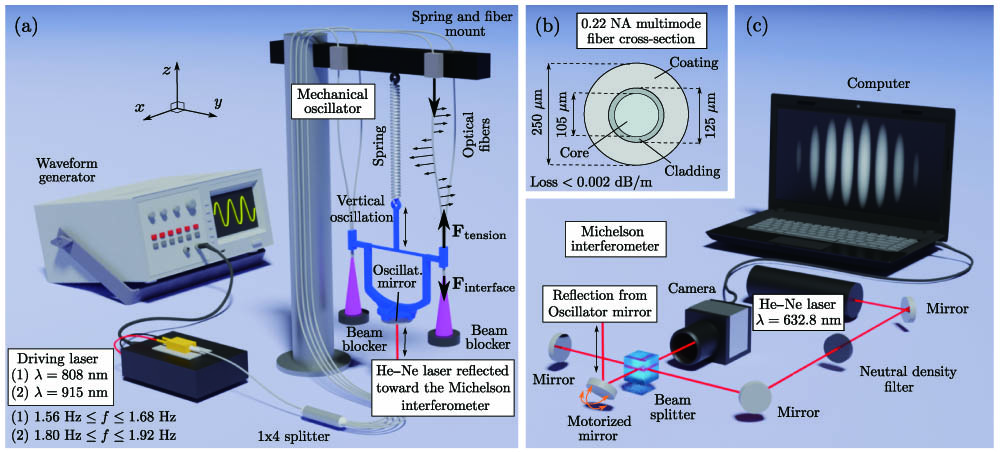
Set citation alerts for the article
Please enter your email address