Ruiwen Geng, Qiming Xie, Wanqing Zhang, Jie Kang, Yueqing Liang, Xiaojing Yang, Rui Li. Study on the material removal mechanism of ZnSe crystal via ultra-precision diamond turning[J]. Infrared and Laser Engineering, 2021, 50(6): 20200403

Search by keywords or author
- Infrared and Laser Engineering
- Vol. 50, Issue 6, 20200403 (2021)

Fig. 1. Experimental step-ups and schematic of cutting experiments. (a) the ultra-precion lathe; (b) enlarged view of workpiece; (c) the machined groove of plunge-cutting test; (d) schematic of machined surface for face-turning test
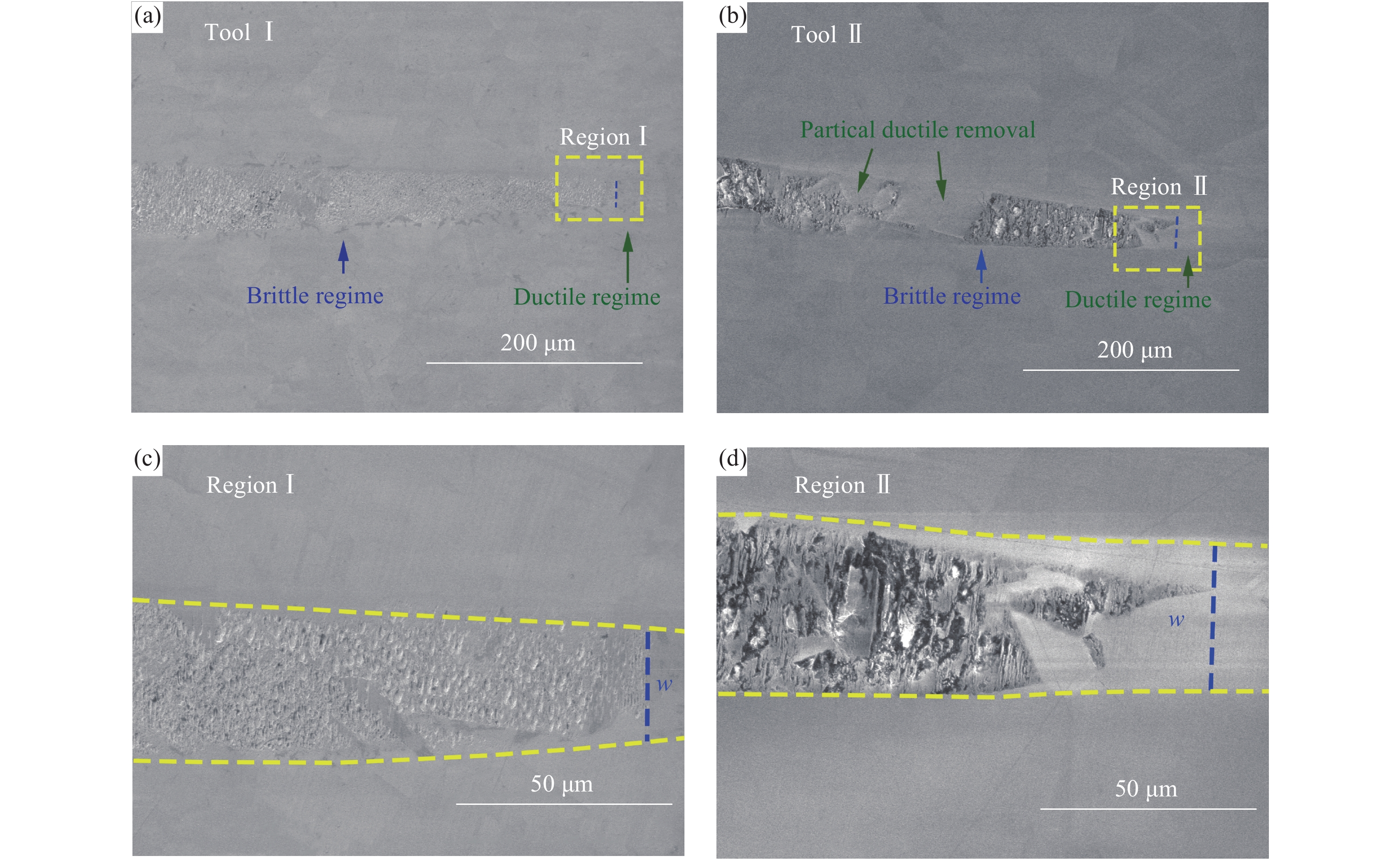
Fig. 2. Typical FESEM image of ZnSe crystal machined groove by using. (a) tool I with 0° rank angle; (b) tool II with −25° rank angle; (c) Enlarged region I; (d) Enlarged region II
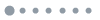
Fig. 3. Ductile-brittle transition depth by using tool I and tool II
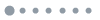
Fig. 4. Schematic of the tool-workpiece contract in ultra-precision machining
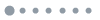
Fig. 5. 2D counter plot of h max vs depth of cut and feed rate
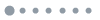
Fig. 6. FESEM image of surface morphology under different feed rates. (a) 2 μm/rev; (b) 1.5 μm/rev; (c) 1 μm/rev; (d) 0.5 μm/rev
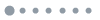
Fig. 7. Mechanism of surface damage formation: (a) Step-liked cracks; (b) Micro-pits
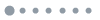
Fig. 8. 3D surface morphany at different feed rates. (a) 2 μm/rev; (b) 1.5 μm/rev; (c) 1 μm/rev; (d) 0.5 μm/rev
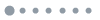
Fig. 9. Surface roughness under different feed rates
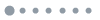
Fig. 10. Raman spectra of the machined surface under different feed rates
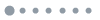
Fig. 11. Raman spectra of the chips under different feed rates
|
Table 1. Material properties of ZnSe crystal[21]
|
Table 2. Cutting tool parameters and experimental condition

Set citation alerts for the article
Please enter your email address