Wenhe Zhao, Yangyang Bai, Jinkai Wang, Lizhong Zhang. Accuracy analysis of a three-dimensional angle measurement sensor based on dual PSDs[J]. Infrared and Laser Engineering, 2024, 53(2): 20230543

Search by keywords or author
- Infrared and Laser Engineering
- Vol. 53, Issue 2, 20230543 (2024)
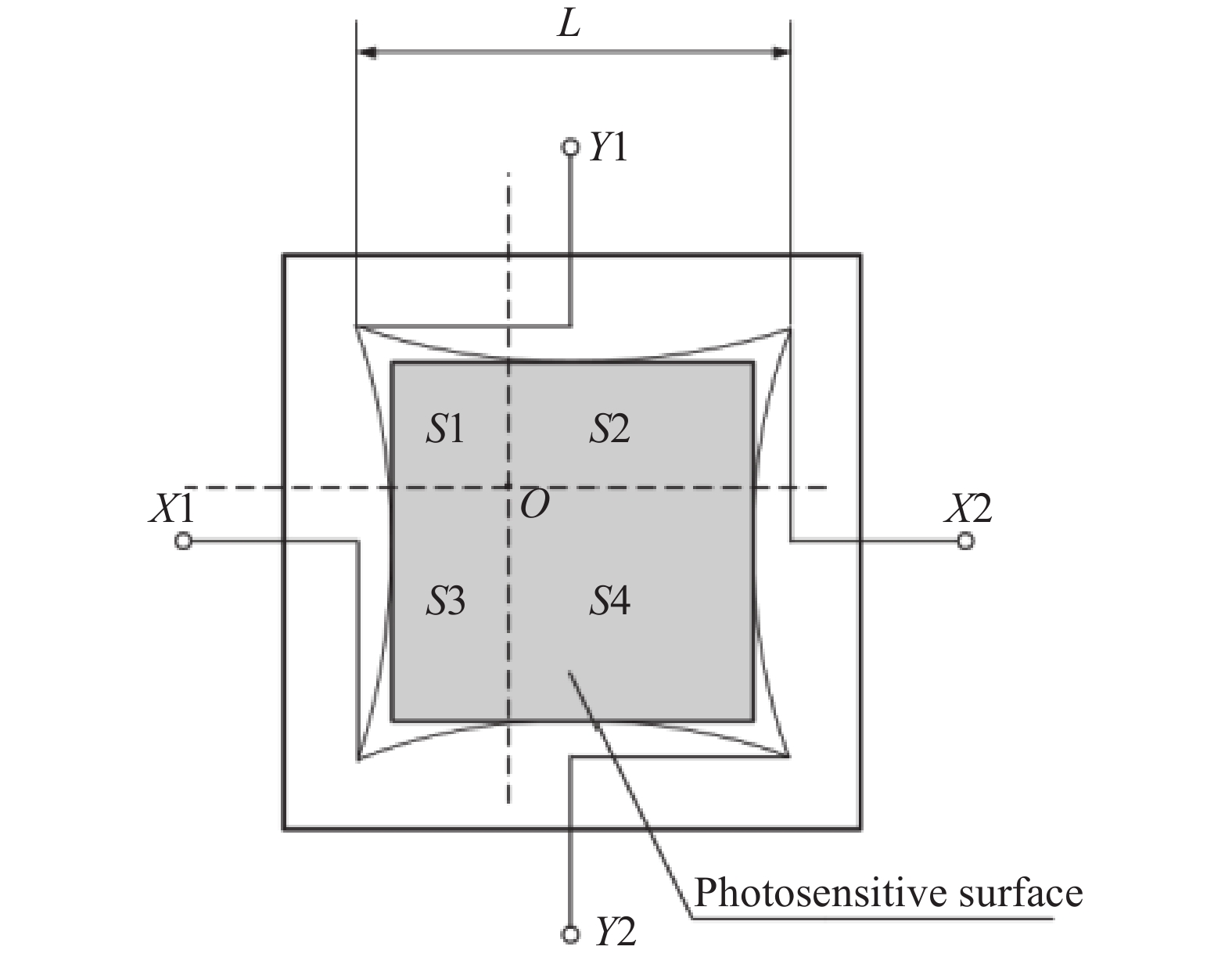
Fig. 1. Schematic diagram of 2D PSD structure
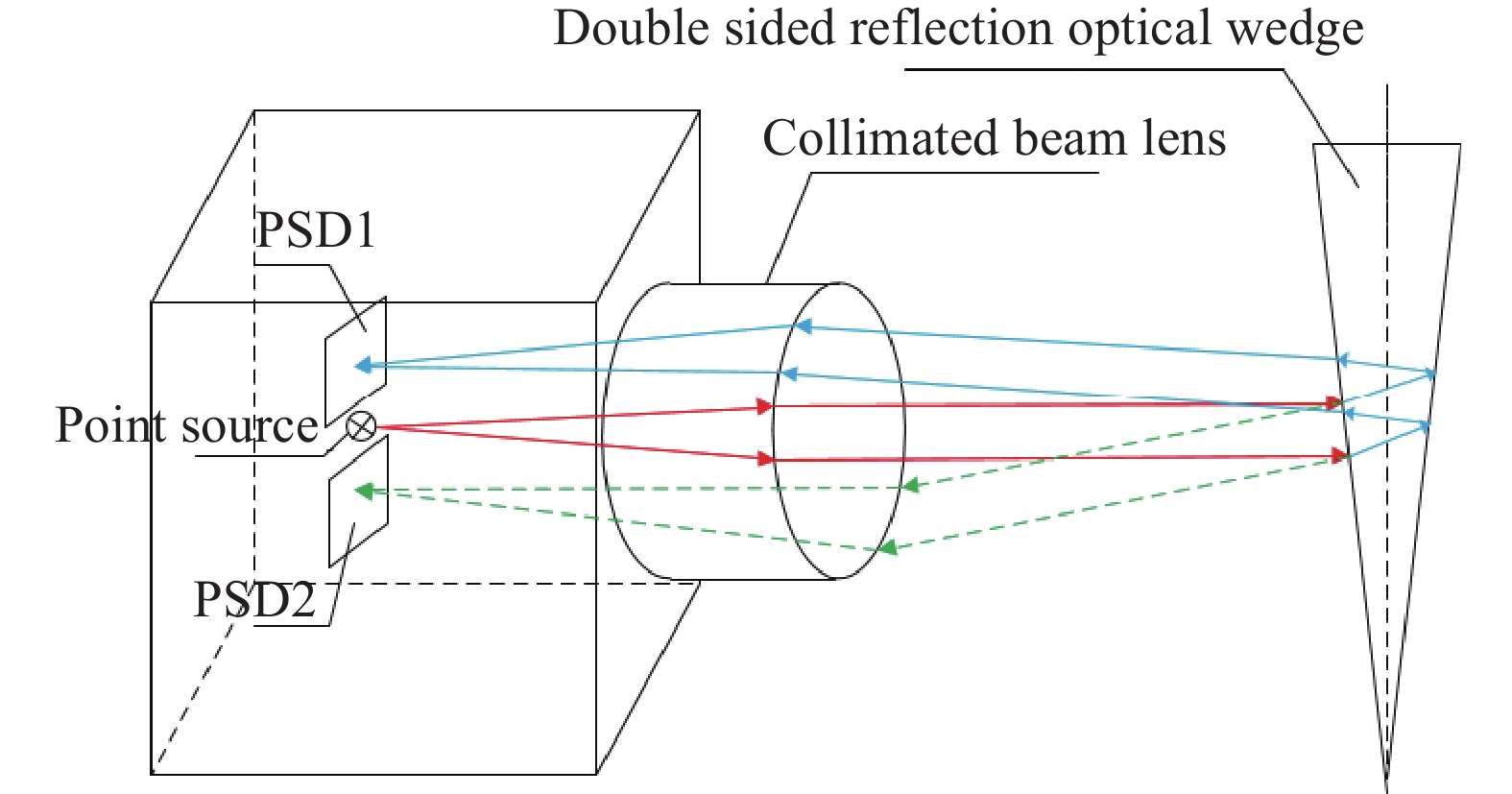
Fig. 2. Schematic diagram of dual PSD 3D angle measurement
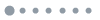
Fig. 3. PSD signal processing circuit diagram
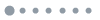
Fig. 4. Schematic diagram of the relative positions of two PSD
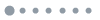
Fig. 5. Two PSD calibration experiments
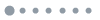
Fig. 6. Two PSD calibration point positions
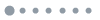
Fig. 7. Extracted analog signal noise signal
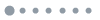
Fig. 8. (a) Noise fitting curve; (b) Curve after filtering with a 34th order FIR filter
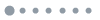
Fig. 9. Curve plot of input signal frequency at (a) 1.00 Hz, (b) 10.00 Hz, (c) 100.00 Hz and (d) 1.00 kHz
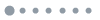
Fig. 10. Curve plot of input signal frequency at (a) 184 Hz and (b) 1.31 kHz
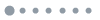
Fig. 11. Comparison diagram between collected data and filtered data
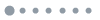
Fig. 12. Comparison diagrams of (a) yaw angle measurement values, (b) pitch angle measurement values, (c) roll angle measurement values before and after filtering
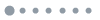
Fig. 13. Angle measurement experimental system
|
Table 1. Performance indicators of each three-axis angle measurement methods
|
Table 2. Performance indicators of six axis hexapod nano displacement table
|
Table 3. Angle measurement error
|
Table 4. Experimental results of the effect of translation on angle measurement
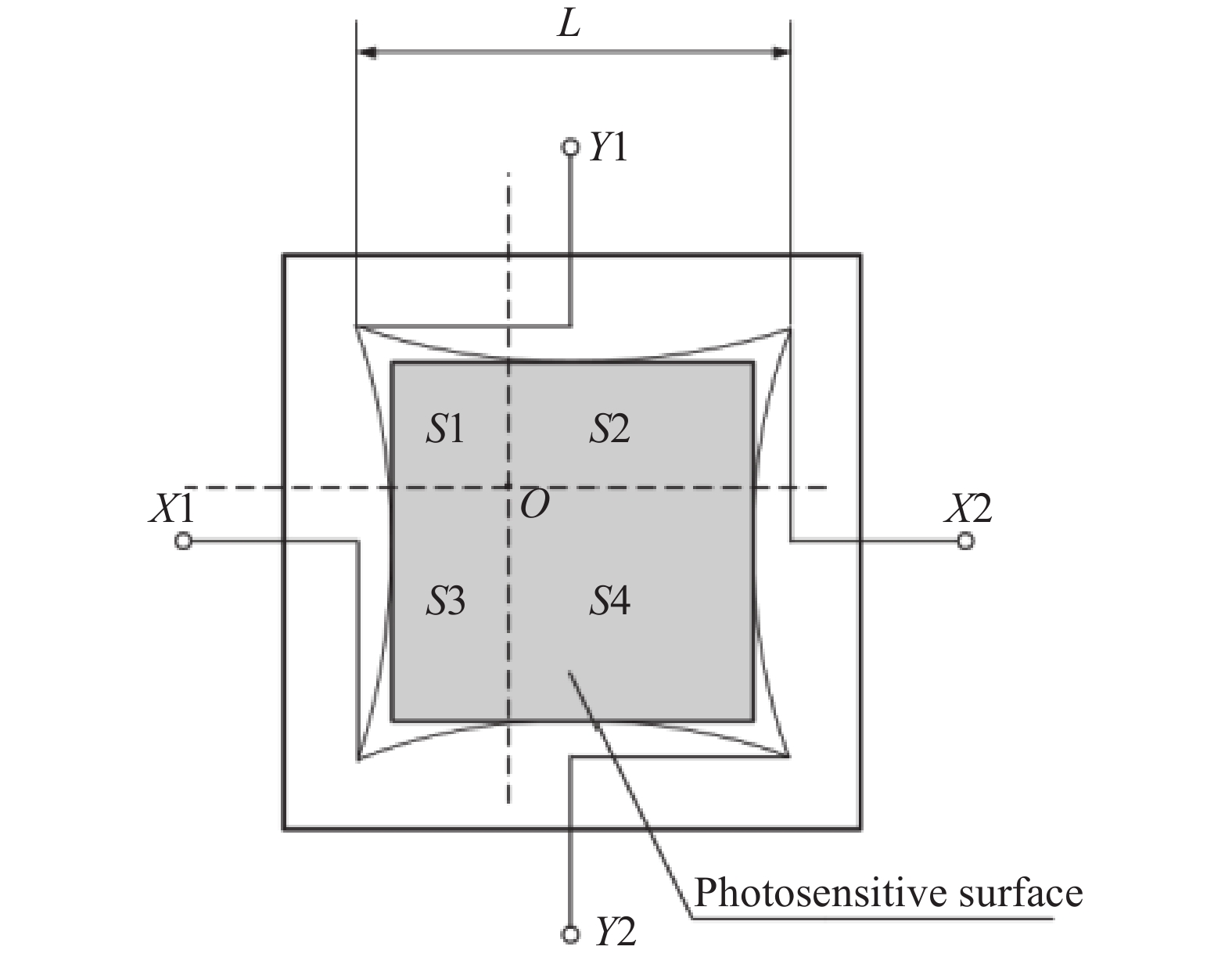
Set citation alerts for the article
Please enter your email address