
- Chinese Optics Letters
- Vol. 21, Issue 4, 041204 (2023)
Abstract
Keywords
1. Introduction
Thanks to its intrinsic advantages of high simplicity, low cost, and the same resolution as that of the typical Michelson interferometer, self-mixing interferometry (SMI), also named optical feedback interferometry (OFI), has been well-established in various metrology applications, and not only in traditional industrial fields, such as vibration displacement, velocimetry, and absolute distance finding[1–5], but also in laser welding monitoring, particle sizing, or label-free biomedical sensing[6–8].
Currently, SMI has attracted much attention in microparticle detection in chemical and biomedical fields, since this simple technique is very suitable for an integrated platform with microfluidic chip and other devices like fuel nozzles[9–14]. Particularly, SMI can be a promising candidate for real-time single-particle detection for small dosage agent experiments in flow cytometry or particle mixing. Moreira et al., for the first time, observed the presence of single submicroscale particles in a 320 µm channel using SMI technology. They applied a simple bandpass filter to visualize the particle bursts in the noisy raw signal and measured the single-particle velocity by fast Fourier transform (FFT)[15]. Contreras et al. managed to classify the single polystyrene sphere size for a higher signal-to-noise ratio (SNR). They developed a novel SMI scheme with edge-filter-enhanced self-mixing interferometry (ESMI)[16], and they approached around 2 orders of magnitude, even at a 10 m operating distance. Zhao et al. presented a fringe counting method for single-microparticle sizing based on the Hilbert transform (HT)[17]; the resolution was still a half wavelength. Unlike the continuous SMI signal from a bulk translating target, particle-induced signals represent a discrete waveform burst. This innovative topic is still challenging: the SMI signal is lower in amplitude and temporally discrete on a millisecond scale. The noises from the measurement environment can significantly reduce SNR and spoil the performance of the sensor system. The resolution in this specific scenario is limited to a basic half wavelength; what is more, the retrieved fringe pattern still presents the signal ambiguity in the waveform edge, where some fringes are missing.
Besides measuring temporal signal waveform fringe number[18] and frequency spectral width[7], novel precise alternatives for particle detection are still required. As a kind of phase observation tool, the phase-unwrapping method (PUM) has been exhaustively studied in SMI sensor systems[19–27], and the spatial resolution even can reach
Sign up for Chinese Optics Letters TOC. Get the latest issue of Chinese Optics Letters delivered right to you!Sign up now
The paper is organized as follows. First, a theoretical framework of SMI effect in the presence of a translating particle is demonstrated, and during the particle passage, the dependence of SMI signal phase variation on particle size is investigated. Second, for effective noise elimination and phase retrieval, continuous wavelet transform (CWT) is directly applied to the original SMI signal. And then a simple HT-based PUM is employed for phase calculation and unwrapping, with the resultant phase variation corresponding to single particle extraction. Finally, using a 532 nm solid-state laser SMI system, signal bursts induced by different-sized polymer beads are acquired and processed by our algorithm, and the measured phase variation values are compared with the simulation results.
2. Theory
When a laser shoots a beam onto a remote target and a portion of the backreflected or backscattered light re-enters the laser cavity, the interaction between the coupled feedback light and the emitting laser field evokes a laser output power fluctuation. The modulated laser output power
Considering that the incident laser beam exhibits a Gaussian spatial intensity profile, and the scattering intensity properties of the particle are also strongly dependent on its position during the flight, both phenomena influence the modulation index
During the signal burst period
From Eqs. (6) and (7), the phase variation
The particle diameter
We simulate the signal burst and the phase variation with the parameters in Table 1. The simulation results are shown in Fig. 1. Within the signal burst period (dashed line), the phase increases linearly as Eq. (7). The signal burst region can be exactly distinguished by the phase profile.
Figure 1.Simulated signal from a 5 µm diameter particle. (a) Temporal signal; (b) phase profile.
Parameter | λ | θinc | D | K |
Value | 532 nm | 25° | 5 µm | 1 µm |
Table 1. Parameters for Simulation
3. Data Processing Method
According to the above-mentioned section, the particle-induced SMI signal is in a temporally intermittent form during the particle passage. Moreover, the signal burst normally is affected by white Gaussian noise, impulsive noise, and DC pedestal[34,35]. The signal burst of each particle is ambiguous and merged in the noises, so an efficient method of burst identification and denoising is demanded. The CWT is a well-established method for investigation of time and frequency details of signals whose frequency content varies over time[23,36,37]. Eventually, this technique performs a correlation between a scaled/shifted wavelet basis and the SMI signal. Because the resultant amplitude corresponding to the uncorrelated and random noise is much lower than that of the desired signal, CWT can implement noise removal in a single step without additive complicated processing.
In this paper, CWT is applied to the SMI signal
The HT can represent a signal in its analytical form over the orthogonal plane and retrieve the phase information very conveniently without modifying the amplitude. So HT is very suitable for phase unwrapping in SMI measurements[17,19].
The original signal function
Finally, the instant phase
After the HT, using a MATLAB-customized phase-unwrapping routine, the realistic phase
The data processing flow chart is illustrated in Fig. 2. The algorithm involves two steps: first, CWT for raw signal noise elimination and burst retrieval; second, HT for phase estimation and unwrapping function.
Figure 2.Chart diagram of CWT-HT signal processing algorithm for particle-induced SMI signal.
4. Experiment and Results
To validate the simulation and the capability of our algorithm, a series of particle sizing measurements are performed with the setup shown in Fig. 3. We select a compact diode-pumped solid-state laser (DPSS) at 532 nm wavelength (Thorlabs, DJ532-10) as the SMI laser source in the system. Due to the higher ratio of fluorescence-to-photon lifetime, a DPSS SMI configuration has higher sensitivity than the typical laser diode (LD) setup[39]. The laser is controlled by a laser controller (Thorlabs, ITC4001), and the injection current and the laser package temperature are kept to be 240 mA and
Figure 3.Schematic of SMI system.
Thousands of monodispersed signal bursts in different particle sizes are captured and processed by our above-mentioned algorithm. The raw signal burst without processing in 2 µm is denoted by the black line in Fig. 4(a). As the figure shows, the signal burst is merged in the strong noise floor, leading to great difficulty in interference fringe observation. To reduce the noise, we applied both bandpass filter (BPF) and Morlet-based CWT upon the raw signal, respectively. Firstly, we analyze the signal by CWT, and the scalogram of the real part of the CWT coefficient
Figure 4.Signal burst of 2 µm PS particle. (a) Raw SMI signal (black), denoised SMI signals by BPF (red) and CWT (blue); (b) scalogram of CWT.
We set the threshold to be 0.2 of the maximum
From the figures, it can be seen that even though the BPF can eliminate the noise effectively in the red line, the burst margin regions are still greatly ambiguous. There are some supernumerary noise fluctuations remaining in the dashed line circles, which can be mistaken for extra signal interference fringes. Compared with the BPF, a well-defined impulse waveform corresponding to a single particle can be distinguished easily by CWT (blue line) without margin ambiguity.
Afterward, the denoised signals are processed by the HT-PUM algorithm to calculate the phase profile. As shown in Fig. 5, obviously, both phase profiles present good linear trend as the simulation. However, compared with the one from the BPF, the linear profile CWT bends at the burst period endpoint, which is exactly the same as in the scalogram in Fig. 4(b). The total phase variation from the starting point
Figure 5.Phase profiles of the 2 µm PS particle SMI signal by BPF (red) and CWT (blue).
By using the threshold CWT algorithm, the particle signals in other different particle sizes are also illustrated in Fig. 6, indicating the robustness of denoising ability with CWT.
Figure 6.Signal bursts of the PS particles in different diameters after CWT denoising. (a) 500 nm; (b) 3 µm; (c) 4 µm; (d) 5 µm.
Signal burst retrievals from each particle size are repeated around 30 times; the mean values of the measured phase
Figure 7.Phase curve as a function of the particle diameter. The blue circle marks represent the mean values and the standard deviations of the measured value of phase
5. Conclusion
In this work, we present a simple and capable PUM algorithm for single-particle size characterization. CWT and HT are involved for noise elimination, individual particle-induced burst retrieval, and phase calculation. The resultant phase variation corresponding to single-particle modulation is extracted efficiently compared with the typical bandpass filtering. The experimental results showed good linear trend of SMI signal phase variation with the particle size over a practical valuable measurement range from 100 nm to 6 µm, which corresponds to typical living cells and bacteria. The good consistency between the simulation results and measured signals has proven the reliability of our theoretical model and the capability of phase observation method in microparticle detection. Thus, the advantage of the new approach with our CWT-HT-PUM algorithm can be more pronounced for particle sizing in the biomedical and chemical fields. Unlike in displacement or vibration measurements, a piezoelectric translator (PZT) enables ultraprecise target motion on a 0.1 nm scale. In our measurement, the artificial particle diameter cannot be regulated less than 1 µm, and the particle dimension inhomogeneity is inevitable during fabrication. So the minimum particle sizing limitation of our method cannot be validated perfectly for the moment. More experiments with finer particle size deviation could be performed in future.
References
[1] Y. Tan, S. Zhang, Z. Ren, Y. Zhang, S. Zhang. Real-time liquid evaporation rate measurement based on a microchip laser feedback interferometer. Chin. Phys. Lett., 30, 124202(2013).
[2] Z. Zhang, L. Sun, C. Li, Z. Huang. Laser self-mixing interferometry for micro-vibration measurement based on inverse Hilbert transform. Opt. Rev., 27, 90(2020).
[3] P. Qi, J. Cheng, S. Li, Z. Zhang, G. Song, J. Weng, J. Zhong. Experimental observation of differential self-mixing interference signals using a randomly polarized laser: a differential self-mixing interferometry. Opt. Lett., 45, 1858(2020).
[4] S. Donati, M. Norgia. Native signal self-mix interferometer has less than 1-nm noise-equivalent-displacement. Opt. Lett., 46, 1995(2021).
[5] M. Veng, F. Bony, J. Perchoux. Disappearance of fringes in the self-mixing interferometry sensing scheme: impact of the initial laser mode solution. Opt. Lett., 46, 1991(2021).
[6] J. Zou, J. Gong, X. Han, Y. Zhao, Q. Wu. In situ detection of plume particles in intelligent laser welding. Mater. Des., 217, 110633(2022).
[7] C. Wang, K. Kou, J. Yan. Frequency-shifted nano-particle sizing using laser self-mixing interferometry. Laser Phys. Lett., 19, 066202(2022).
[8] Z. Dai, X. Xu, Y. Wang, M. Li, K. Zhou, L. Zhang, Y. Tan. Surface plasmon resonance biosensor with laser heterodyne feedback for highly-sensitive and rapid detection of COVID-19 spike antigen. Biosens. Bioelectron., 206, 114163(2022).
[9] C. Zakian, M. Dickinson, T. King. Dynamic light scattering by using self-mixing interferometry with a laser diode. Appl. Opt., 45, 2240(2006).
[10] K. Otsuka, T. Ohtomo, H. Makino, S. Sudo, J.-Y. Ko. Net motion of an ensemble of many Brownian particles captured with a self-mixing laser. Appl. Phys. Lett., 94, 241117(2009).
[11] Y. Zhao, J. Perchoux, L. Campagnolo, T. Camps, R. Atashkhooei, V. Bardinal. Optical feedback interferometry for microscale-flow sensing study: numerical simulation and experimental validation. Opt. Express, 24, 23849(2016).
[12] H. Wang, J. Shen. Size measurement of nano-particles using self-mixing effect. Chin. Opt. Lett., 6, 871(2008).
[13] J. Zou, Z. Huang, J. Gong, Y. Zhao, Z. Wang, Q. Wu. Characterization of micron-sized particles in the focused laser beam during fiber laser keyhole welding. Opt. Laser Technol., 156, 108463(2022).
[14] J. Zou, Z. Wang, Y. Zhao, X. Han, J. Gong. In situ measurement of particle flow during fiber laser additive manufacturing with powder feeding. Results Phys., 37, 105483(2022).
[15] R. da Costa Moreira, J. Perchoux, Y. Zhao, C. Tronche, F. Jayat, T. Bosch. Single nano-particle flow detection and velocimetry using optical feedback interferometry(2017).
[16] V. Contreras, J. Lönnqvist, J. Toivonen. Detection of single microparticles in airflows by edge-filter enhanced self-mixing interferometry. Opt. Express, 24, 8886(2016).
[17] Y. Zhao, M. Zhang, C. Zhang, W. Yang, T. Chen, J. Perchoux, E. E. Ramírez-Miquet, R. da Costa Moreira. Micro particle sizing using Hilbert transform time domain signal analysis method in self-mixing interferometry. Appl. Sci., 9, 5563(2019).
[18] Y. Zhao, X. Shen, M. Zhang, J. Yu, J. Li, X. Wang, J. Perchoux, R. da Costa Moreira, T. Chen. Self-mixing interferometry-based micro flow cytometry system for label-free cells classification. Appl. Sci., 10, 478(2020).
[19] S. Amin. Implementation of Hilbert transform based high-resolution phase unwrapping method for displacement retrieval using laser self mixing interferometry sensor. Opt. Laser Technol., 149, 107887(2022).
[20] Z. Huang, B. Du, Z. Zhang, Y. Ye, S. He, Z. Li, S. He, X. Hu, D. Li. Compact photothermal self-mixing interferometer for highly sensitive trace detection. Opt. Express, 30, 1021(2022).
[21] D. Li, Q. Li, X. Jin, B. Xu, D. Wang, X. Liu, T. Zhang, Z. Zhang, M. Huang, X. Hu, C. Li, Z. Huang. Quadrature phase detection based on a laser self-mixing interferometer with a wedge for displacement measurement. Measurement, 202, 111888(2022).
[22] Z. Wu, W. Guo, L. Lu, Q. Zhang. Generalized phase unwrapping method that avoids jump errors for fringe projection profilometry. Opt. Express, 29, 27181(2021).
[23] Y. Zhao, B. Zhang, L. Han. Laser self-mixing interference displacement measurement based on VMD and phase unwrapping. Opt. Commun., 456, 124588(2020).
[24] S. Amin, U. Zabit, O. D. Bernal, T. Hussain. High resolution laser self-mixing displacement sensor under large variation in optical feedback and speckle. IEEE Sens. J., 20, 9140(2020).
[25] C. Jiang, X. Wen, S. Yin, Y. Liu. Multiple self-mixing interference based on phase modulation and demodulation for vibration measurement. Appl. Opt., 56, 1006(2017).
[26] Z. Zhang, C. Li, Z. Huang. Vibration measurement based on multiple Hilbert transform for self-mixing interferometry. Opt. Commun., 436, 192(2019).
[27] J.-H. Kim, C.-H. Kim, T.-H. Yun, H.-S. Hong, K.-M. Ho, K.-H. Kim. Joint estimation of self-mixing interferometry parameters and displacement reconstruction based on local normalization. Appl. Opt., 60, 2282(2021).
[28] X. Wan, D. Li, S. Zhang. Quasi-common-path laser feedback interferometry based on frequency shifting and multiplexing. Opt. Lett., 32, 367(2007).
[29] S. Blaize, B. Bérenguier, I. Stéfanon, A. Bruyant, G. Lérondel, P. Royer, O. Hugon, O. Jacquin, E. Lacot. Phase sensitive optical near-field mapping using frequency-shifted laser optical feedback interferometry. Opt. Express, 16, 11718(2008).
[30] T. Taimre, M. Nikolić, K. Bertling, Y. L. Lim, T. Bosch, A. D. Rakić. Laser feedback interferometry: a tutorial on the self-mixing effect for coherent sensing. Adv. Opt. Photonics, 7, 570(2015).
[31] R. Lang, K. Kobayashi. External optical feedback effects on semiconductor injection laser properties. IEEE J. Quantum Electron., 16, 347(1980).
[32] C. Yáñez, F. J. Azcona, S. Royo. Confocal flowmeter based on self-mixing interferometry for real-time velocity profiling of turbid liquids flowing in microcapillaries. Opt. Express, 27, 24340(2019).
[33] Y. Tao, M. Wang, W. Xia. Semiconductor laser self-mixing micro-vibration measuring technology based on Hilbert transform. Opt. Commun., 368, 12(2016).
[34] Z. A. Khan, U. Zabit, O. D. Bernal, T. Hussain. Adaptive estimation and reduction of noises affecting a self-mixing interferometric laser sensor. IEEE Sens. J., 20, 9806(2020).
[35] Y. Zhao, T. Camps, V. Bardinal, J. Perchoux. Optical feedback interferometry based microfluidic sensing: impact of multi-parameters on Doppler spectral properties. Appl. Sci., 9, 3903(2019).
[36] O. D. Bernal, H. C. Seat, U. Zabit, F. Surre, T. Bosch. Robust detection of non-regular interferometric fringes from a self-mixing displacement sensor using bi-wavelet transform. IEEE Sens. J., 16, 7903(2016).
[37] Y. Wei, Y. Wei, W. Huang, Z. Wei, J. Zhang, T. An, X. Wang, H. Xu. Double-path acquisition of pulse wave transit time and heartbeat using self-mixing interferometry. Opt. Commun., 393, 178(2017).
[38] A. Jha, F. J. Azcona, C. Yañez, S. Royo. Extraction of vibration parameters from optical feedback interferometry signals using wavelets. Appl. Opt., 54, 10106(2015).
[39] K. Kou, C. Wang, T. Lian, J. Weng. Fringe slope discrimination in laser self-mixing interferometry using artificial neural network. Opt. Laser Technol., 132, 106499(2020).
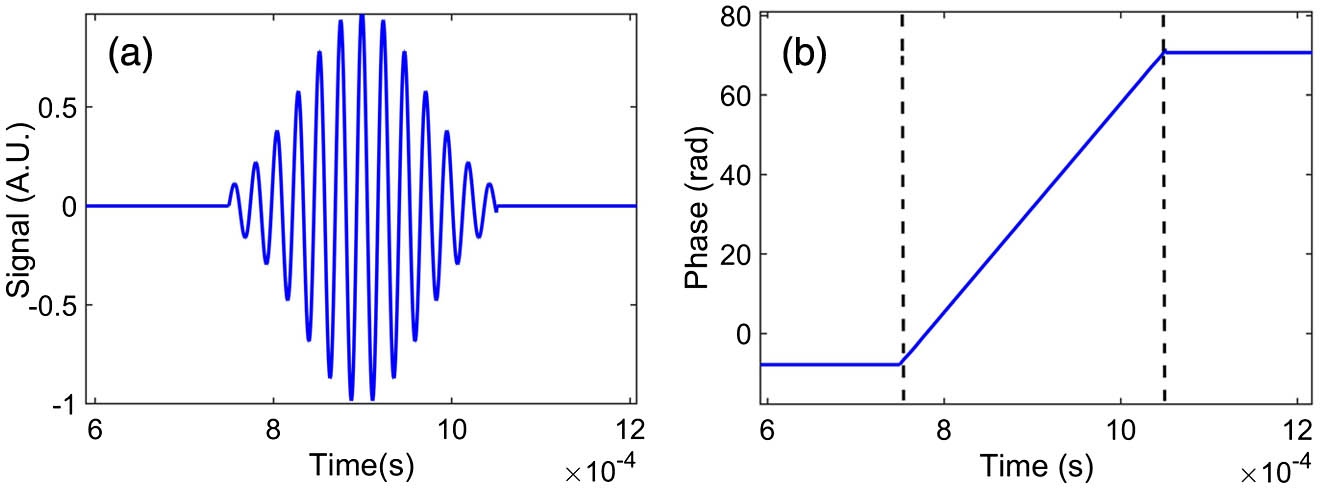
Set citation alerts for the article
Please enter your email address