Jianwen Gong, Jian Wang, Junbo Liu, Haifeng Sun, Song Hu. Microlens array machining method based on projection lithography[J]. Opto-Electronic Engineering, 2023, 50(12): 230281-1

Search by keywords or author
- Opto-Electronic Engineering
- Vol. 50, Issue 12, 230281-1 (2023)

Fig. 1. The mask moving method based on projection lithography. (a) Working principle of the projection exposure system; (b) Moving mask graphic structure; (c) 3D Wiener structure after processing

Fig. 2. Principle of mask moving filtering based on projection lithography. (a) The equally divided objective function; (b) Microstrip area outline function; (c) The divided feature pattern; (d) Micrographic structure after exposure
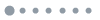
Fig. 3. The micrographics and corresponding mask plate graphics are recovered by using mask moving filtering technology under different conditions when (a), (d) S >> T; (b), (e) S << T; (c), (f) S ≈ T.
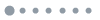
Fig. 4. Mask graphics of two processing methods. (a-d) Mask patterns based on proximity lithography mask moving method, with diameters of 50 μm, 100 μm, 300 μm and 500 μm, respectively; (e-h) Mask patterns based on the projection lithography mask movement method, with diameters of 250 μm, 500 μm, 1500 μm, 2500 μm, respectively
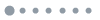
Fig. 5. Surface shape measurement results of microlenses of different calibers processed by traditional methods. (a) 500 μm aperture; (b) 300 μm aperture; (c) 100 μm aperture; (d) 50 μm aperture
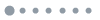
Fig. 6. Surface shape results of microlens with different calibers fabricated by projection lithography. (a) 500 μm aperture; (b) 300 μm aperture; (c) 100 μm aperture; (d) 50 μm aperture
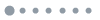
Fig. 7. 3D profilometer scanning results of traditional experimental results. (a-d) are the measurement results of 500 µm, 300 µm, 100 µm and 50 µm, respectively
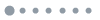
Fig. 8. 3D profilometer scanning results of experimental results of projection lithography method. (a-d) are the measurement results of 500 µm, 300 µm, 100 µm and 50 µm, respectively

Set citation alerts for the article
Please enter your email address