Meina Zhan, Song Ni, Haijun Yu, Haixia Xie, Fenglin Liu, Hui Tan. Local Accelerator CT Testing of Large-Diameter Rotary Part Shells[J]. Acta Optica Sinica, 2024, 44(22): 2211003

Search by keywords or author
- Acta Optica Sinica
- Vol. 44, Issue 22, 2211003 (2024)

Fig. 1. Schematic diagrams of mL-STCT geometric models. (a) Three-dimensional geometric model; (b) two-dimensional geometric model

Fig. 2. Two-dimensional geometric model under new coordinate system
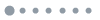
Fig. 3. Projection data distributions of mL-STCT. (a) Single scanning; (b) discontinuous projection; (c) continuous projection
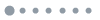
Fig. 4. Simulation phantom and local magnification image. (a) Simulation phantom; (b) local magnification image
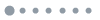
Fig. 5. Reconstruction results of different projection data distributions. (a)‒(d) Reconstruction results of case1; (e)‒(h) reconstruction results of case2; (i)‒(l) reconstruction results of case3
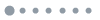
Fig. 6. Magnified ROIs in Fig. 5. (a)‒(d) case1; (e)‒(h) case2; (i)‒(l) case3
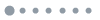
Fig. 7. Reconstruction results of different imaging methods. (a) Phantom; (b)‒(e) reconstruction results; (f)‒(j) magnified ROIs in Figs. 7(a)‒(e)
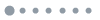
Fig. 8. Profiles along the 26th and 44th rows of reconstruction images of different imaging methods. (a) Profiles along the 26th row; (b) profiles along the 44th row
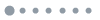
Fig. 9. Projection data distributions of different imaging methods. (a) mL-STCT; (b) TCT
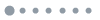
Fig. 10. Experimental system of mL-STCT
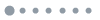
Fig. 11. Reconstruction results of mL-STCT for different scanning times. (a)‒(d) Reconstruction results; (e)‒(h) magnified ROIs in Figs. 11(a)‒(d)
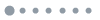
Fig. 12. Reconstruction results of different imaging methods. (a)‒(d) Reconstruction results; (e)‒(h) magnified ROIs in Figs. 12(a)‒(d)
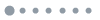
Fig. 13. Scanning schematic and reconstruction result of resolution test card. (a) Scanning schematic; (b) reconstruction result
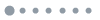
Fig. 14. Reconstruction results of strip defects of different widths. (a) Width is 0.6 mm; (b) width is 1.2 mm; (c) width is 2 mm
|
Table 1. Parameters of simulation
|
Table 2. Rotation angle of object per scan under different projection distributions
|
Table 3. Reconstruction image indexes under different projection distributions
|
Table 4. Reconstruction image indexes of different imaging methods
|
Table 5. Parameters of simulated physical scanning experiment

Set citation alerts for the article
Please enter your email address