GUAN Yingjun, XU Hong, LI Zhilai, GAO Xijun, YANG Liwei. Design of Truss Support Structure for Large Off-axis Space Camera[J]. Opto-Electronic Engineering, 2014, 41(12): 7

Search by keywords or author
- Opto-Electronic Engineering
- Vol. 41, Issue 12, 7 (2014)
Abstract
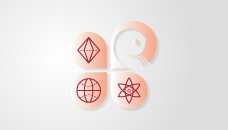
Set citation alerts for the article
Please enter your email address