
- Journal of Inorganic Materials
- Vol. 36, Issue 11, 1231 (2021)
Abstract
ZrO2 has intriguing advantages including excellent mechanical properties, high temperature endurance, outstanding chemical stability and good ionic conductivity. ZrO2- based ceramics are industrially important and widely applied as the structural and functional materials, including cutting tools, bearing parts, thermal barrier and solid oxide fuel cells. It is well known that ZrO2 is polymorphs and exists in monoclinic (m), tetragonal (t) or cubic (c) crystal phases at different temperatures or sizes[
In order to stabilize the cubic structure of ZrO2 at room temperature, pure ZrO2 materials are doped by oxides. The cations with a radius larger than Zr4+ are introduced to replace Zr4+ lattice points, forming a substitute solid solution, thereby maintaining the obtained doped solid solution at room temperature. Commonly used stabilizing cations include Y3+[
Composite materials are expected to overcome the inherent shortcomings of single-phase ceramics and bring about an overall improvement in structure and functional characteristics[
Aluminum nitride (AlN) has high thermal conductivity (320 W/(m·K))[
Motivated by the above mentioned, herein AlN was introduced and the corresponding ZrO2-AlN composite ceramics were prepared successfully at 1350 ℃ by microwave sintering. Compared with conventional sintering, the microwave sintering can cause internal molecular vibrations under electromagnetic radiation, further leading to self-heating from the core, resulting in lower sintering temperature and finer microstructure of specimen. The phase composition and morphology evolution were identified by X-ray diffraction (XRD) and scanning electron microscope (SEM), respectively. Furthermore, the effect of the AlN on the thermal and mechanical properties was investigated and discussed. Optimal ZrO2-AlN composite owns thermal conductivity up to 41.3 W/(m·K).
1 Experimental
Raw materials ZrO2 and AlN were commercially available and used as received. Commercially available Y2O3 (8mol% of ZrO2), Al, CaF2, TiO2 and B (5wt% of AlN and the proportion of each part is 3 : 3 : 1 : 0.08) were used as sintering additives[
Specimen | Composition |
---|---|
ZAN-0 | 100%ZrO2 |
ZAN-1 | 95wt%ZrO2+5wt%AlN |
ZAN-2 | 90wt%ZrO2+10wt%AlN |
ZAN-3 | 85wt%ZrO2+15wt%AlN |
ZAN-4 | 80wt%ZrO2+20wt%AlN |
Table 1.
Compositions of samples
Figure 1.Sintering process of ZrO2-AlN composite ceramic
The density of ceramics was measured by the Archimedes method. Vickers hardness was measured on polished surface with a load of 9.8 N for 15 s using a micro- hardness tester (HX-1000TM). Fracture toughness measurement was performed using indentation method, and results were obtained by the formula (1)[
where E and Hv are elastic modulus and Vickers hardness of the sample, while c and a are the half-length of crack cracking and the half-length of diagonal indentation of the sample. Standard test pieces (3 mm×4 mm×36 mm) were obtained by using cutting machine and polishing. Three-point-bending method was used to measure the flexure strength on an electronic universal testing machine (UTM17093) with a span of 20 mm at a crosshead speed of 0.5 mm/min. X-ray diffractometer (CuKα, 30 kV/10 mA, Rigaku Miniflex-600, Tokyo, Japan) and SEM (Helios, G4 CX, Germany) were employed to study the surface and fracture morphology, respectively. The samples for the analyses of thermal diffusivity were in the dimension of 10 mm×10 mm×2 mm. The thermal conductivity was measured using a laser thermal conductivity meter (Netzsch, LFA457, Germany) and calculated[
2 Results and discussion
2.1 Phase analyses
As shown in Fig. 2, the powders are mixed, containing some AlN and a large amount of ZrO2 with monoclinic and tetragonal phases as received. As shown in Fig. 3, the EDS mapping reflects that the powder has been mixed evenly after ball milling. The XRD patterns of samples sintered at 1350 ℃ are shown in Fig. 4(a). For ZAN-0, c-ZrO2 is the predominant phase with a bit t-ZrO2. ZrO2- AlN composite ceramics are composed of ZrO2 and AlN, and the intensity of the diffraction peak of AlN phase increases with its content increasing. The monoclinic zirconia existing in the raw material powder is converted into a tetragonal or cubic phase at high temperature and keeps stable at room temperature after cooling. The XRD patterns of ZAN-2 with WZrO2/WAlN=9 : 1 sintered from 1300 to 1400 ℃ are shown in Fig. 4(b). c-ZrO2 and AlN are the only two phases at 1300 and 1350 ℃. With the temperature increasing to 1400 ℃, two byproducts including ZrN and Al2O3 appear, which are attributed to the reaction of ZrO2 and AlN[
Figure 2.XRD pattern of raw material powder after ball milling and mixing
Figure 3.EDS mapping images of mixed powder after ball milling
Figure 4.XRD patterns of ZrO2-AlN composite ceramics sintered at 1350 ℃ (a) and at different temperatures (b)
ZrO2 and AlN are the major phases in the specimens sintered at 1350 ℃ (Fig. 4(a)), while trace amount of ZrN and Al2O3 emerged at higher sintering temperature (Fig. 4(b)).
2.2 Mechanical properties
The relative densities of the composites with different AlN contents are shown in Fig. 5(a). The relative density of all samples is higher than 99%, and the pure zirconia has the highest relative density of 99.7%. With the increase of AlN content, the relative density of composites decreases gradually. As shown in Table 2, the relative density of the ZAN-2 samples prepared under different ball milling processes and cold isostatic pressing (CIP) pressures showed different changes, and the ZAN-2 samples prepared by the 1# process had the highest relative density. The sintering temperature is 1350 ℃, which is higher than the melting point of Al. During the sintering process, Al is molten and further transient liquid phase sintered, promotes the densification of the composites. With the increase of AlN, AlN grains are not uniformly distributed in the matrix, which weakens the inhibition effect on ZrO2 grains in the matrix, leading to the abnormal growth of some ZrO2 grains. In addition, AlN also affects the contact between ZrO2 grains and affects the shrinkage which plays an inhibiting role in the sintering. Thus, the relative density of composite ceramic decreases with the increase of AlN.
Figure 5.Relative density and mechanical behavior of different ZrO2-AlN composite ceramics (a) Relative density; (b) Vickers hardness; (c) Fracture toughness; (d) Flexural strength
Sample | Rotating speed/(r·min-1) | Rotating time/h | Pressure/MPa | Relative density/% |
---|---|---|---|---|
1# | 250 | 24 | 200 | 99.3 |
2# | 250 | 12 | 200 | 98.5 |
3# | 200 | 24 | 200 | 98.9 |
4# | 250 | 24 | 100 | 98.1 |
Table 2.
Relative density of ZAN-2 sample prepared by different CIP pressure and ball milling processes
Fig. 5(b) demonstrates the change of Vickers hardness of ZrO2-AlN composite ceramics with different AlN contents. With the increase of AlN, the Vickers hardness of composite ceramics decrease from 14.3 GPa (0) to 9.8 GPa (20wt%) due to the hardness of AlN being lower than that of matrix ZrO2. According to the composite law of mechanical properties, the higher content of AlN, the lower hardness of composite is. At the same time, hardness is a very sensitive property to compactness. With the further increase of AlN, the compactness decreases and the hardness decreases correspondingly.
Fig. 5(c,d) display the changes of fracture toughness and flexural strength of ZrO2-AlN composite ceramics with AlN contents. With the increase of AlN addition, both fracture toughness and bending strength of ZrO2-AlN composite ceramics show a decreasing trend. This can be assigned to the fact that the sintering temperature of AlN is higher than that of ZrO2. Some AlN particles stacked with each other grow abnormally, while ZrO2 particles in the matrix grow to a certain extent at high temperature due to the lack of effective inhibition originating from AlN grains around. Therefore, with AlN content in the matrix increasing, fracture toughness and bending strength of composites decrease.
2.3 Microstructural characterization
In order to investigate the microstructure evolution of ZrO2-AlN composite ceramics, SEM images of the ZAN-2 sample after acid corrosion were shown in Fig. 6(a,b). The sample only displays ZrO2 and AlN phases without any impurity phases, which is consistent with the XRD results. The brighter areas are ZrO2 phases and the darker areas are AlN phases. Furthermore, the ZrO2 phase is well developed, and AlN phase is distributed at the boundaries of ZrO2, which is helpful to maintain lattice integrity of ZrO2 and reduce lattice defects. The AlN is distributed orderly in ZrO2 substrate, which can improve the microstructure uniformity of composite ceramics. It is noteworthy that a small number of pores exist in the SEM image, which confirms the fact of low relative density. Fig. 6(c,d) are the cross-section SEM images. It can be found that the particles are tightly packed with intact grains and clean grain boundaries. At the same time, the fracture mode of ZrO2-AlN composite ceramics is mainly transcrystalline fracture, and the fracture toughness is lower than that of pure ZrO2 ceramics. The crack propagated at the grain boundary with microscopical deflection and grain pullout. The crack deflection may be favorable for the toughening of composites. As a result, the incorporation of AlN makes the microstructure of ZrO2 matrix composites passivating and heterogeneity. Thus, the mechanical properties of the composites are reduced in comparison with that of pure ZrO2.
Figure 6.SEM images of the polished surfaces (a, b) and fracture surfaces (c, d) of ZAN-2 sample
2.4 Thermal analysis
The concept of phonon can be adopted to explain the heat conduction phenomenon of materials[
Figure 7.Thermal performance of ZrO2-AlN composite ceramics with different AlN contents (a) Thermal conductivity; (b) Thermal diffusion coefficient; (c) Thermal capacity
3 Conclusions
AlN was introduced into zirconia matrix as the toughening phases by novel microwave sintering. The mechanical and thermal property of the obtained ZrO2-AlN composite ceramics were analyzed. With the increase of AlN content, the relative density of ZrO2-AlN composite ceramic gradually decreases. ZrO2-AlN composite ceramics with 20wt% AlN obtains the highest thermal conductivity (41.3 W/(m·K)), the maximum thermal diffusion coefficient (15.2 mm2/s) at room temperature and the best thermal capacity (0.6 J/(g·K)).
References
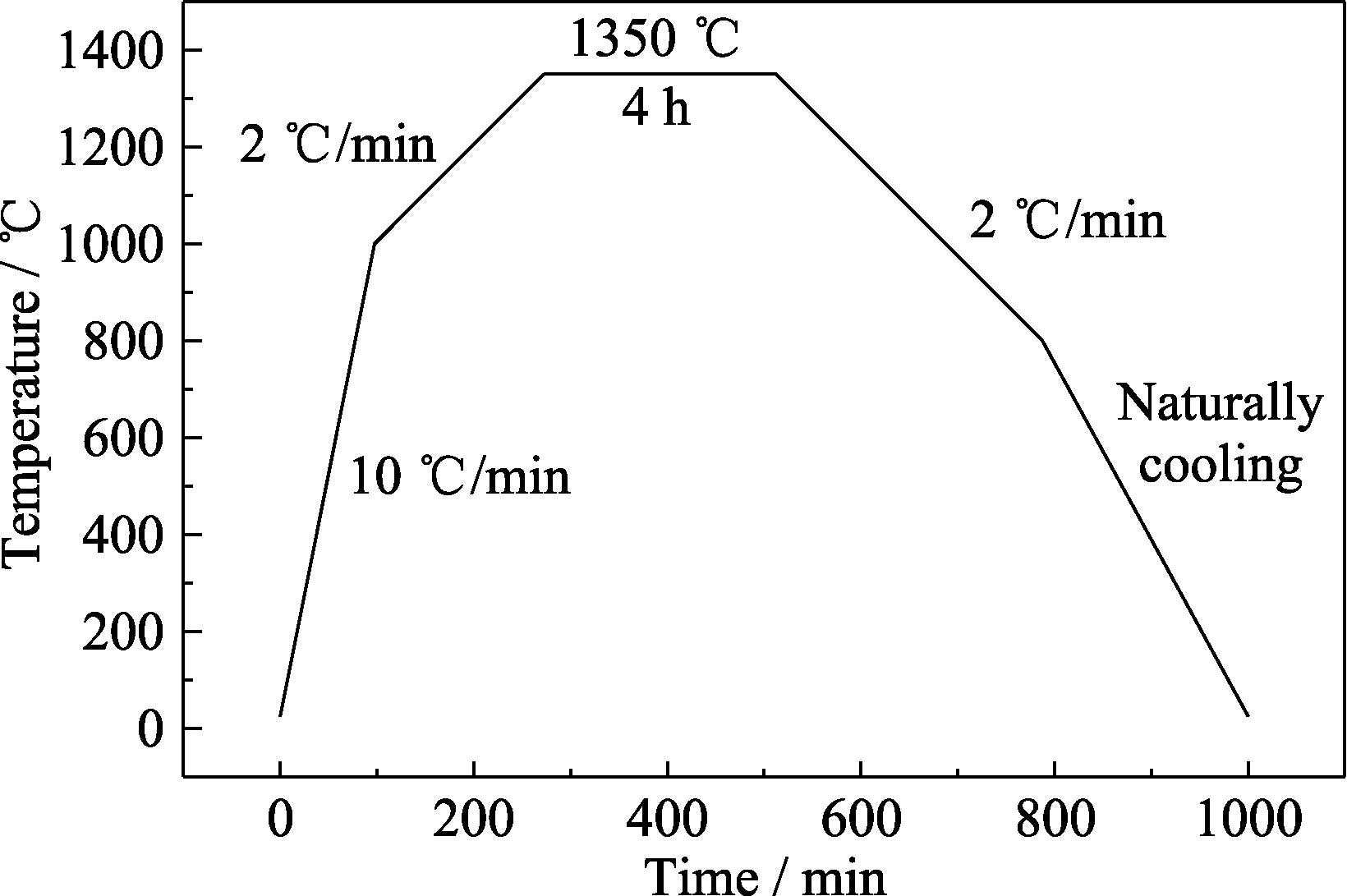
Set citation alerts for the article
Please enter your email address