Tingting Yuan, Xiaotong Zhang, Xinghua Yang, Libo Yuan. Microfluidic Fiber Optic Sensors: from Functional Integration to Functional Design (Invited)[J]. Laser & Optoelectronics Progress, 2024, 61(1): 0106004

Search by keywords or author
- Laser & Optoelectronics Progress
- Vol. 61, Issue 1, 0106004 (2024)
![Schematic diagram of optical microfluidic system[2]. (a) Demodulation channel (red arrow) and one of the six microlens arrays (blue arrow); (b) embedded optical fiber (red line is the optical path)](/richHtml/lop/2024/61/1/0106004/img_01.jpg)
Fig. 1. Schematic diagram of optical microfluidic system[2]. (a) Demodulation channel (red arrow) and one of the six microlens arrays (blue arrow); (b) embedded optical fiber (red line is the optical path)
![SPR temperature meter[10]. (a) Hollow fiber filled with liquid crystal medium; (b) structure of the silver coated hollow fiber; (c) cross section of the hollow fiber after filling uniform liquid](/richHtml/lop/2024/61/1/0106004/img_02.jpg)
Fig. 2. SPR temperature meter[10]. (a) Hollow fiber filled with liquid crystal medium; (b) structure of the silver coated hollow fiber; (c) cross section of the hollow fiber after filling uniform liquid
![Photos of various micro-structured optical fibers cross section with holes[19]](/Images/icon/loading.gif)
Fig. 3. Photos of various micro-structured optical fibers cross section with holes[19]
![Schematic diagram of the buffer-modulated optofluidic chip with an integrated interferometer and optical trap[46]](/Images/icon/loading.gif)
Fig. 4. Schematic diagram of the buffer-modulated optofluidic chip with an integrated interferometer and optical trap[46]
![Diagram of gas sensor pipeline[60]](/Images/icon/loading.gif)
Fig. 5. Diagram of gas sensor pipeline[60]
![Micro flow detection platform for ARROW[76]. (a) Fluorescence cross-correlation spectroscopy detection platform; (b) cross-correlation solid core ARROW; (c) cross-correlation liquid core ARROW](/Images/icon/loading.gif)
Fig. 6. Micro flow detection platform for ARROW[76]. (a) Fluorescence cross-correlation spectroscopy detection platform; (b) cross-correlation solid core ARROW; (c) cross-correlation liquid core ARROW
![Configuration of the fiber-based fluorescence sensing system (inset: liquid column in fiber)[2]](/Images/icon/loading.gif)
Fig. 7. Configuration of the fiber-based fluorescence sensing system (inset: liquid column in fiber)[2]
![Microflow laser biosensing based on hollow core fiber[80]](/Images/icon/loading.gif)
Fig. 8. Microflow laser biosensing based on hollow core fiber[80]
![Chip used for SERS detection[90]. (a) Schematic of hybridization reaction; (b) schematic of chip structure](/Images/icon/loading.gif)
Fig. 9. Chip used for SERS detection[90]. (a) Schematic of hybridization reaction; (b) schematic of chip structure
![In vivo, chloroplasts are trapped and arranged by non-contact laser (OFP is optical fiber probe)[109]. (a1) (b1) Multi-particle capture diagram; (a2) (b2) photograph of multiple chloroplasts captured by OFP; (c1) (c2) two rows of chloroplasts arranged by OFP](/Images/icon/loading.gif)
Fig. 10. In vivo, chloroplasts are trapped and arranged by non-contact laser (OFP is optical fiber probe)[109]. (a1) (b1) Multi-particle capture diagram; (a2) (b2) photograph of multiple chloroplasts captured by OFP; (c1) (c2) two rows of chloroplasts arranged by OFP
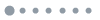
Fig. 11. Hollow suspended core fiber. (a) Photo of cross section; (b) refractive index profile
![Schemetic of microfluidc chemical reactor based on hollow optical fiber with a suspended core and photo of the corresponding area (inset: microhole and fiber core melt collapse)[115]](/Images/icon/loading.gif)
Fig. 12. Schemetic of microfluidc chemical reactor based on hollow optical fiber with a suspended core and photo of the corresponding area (inset: microhole and fiber core melt collapse)[115]
![Dynamic response of the in-fiber analyzing system. (a) Relationship between duration of chemical reactions inside optical fibers and chemiluminescence intensity[116]; (b) relationship between Vc concentration in optical fibers and chemiluminescence intensity[115]](/Images/icon/loading.gif)
Fig. 13. Dynamic response of the in-fiber analyzing system. (a) Relationship between duration of chemical reactions inside optical fibers and chemiluminescence intensity[116]; (b) relationship between Vc concentration in optical fibers and chemiluminescence intensity[115]
![Cross section and refractive index profile[117]. (a) Cross section of HTCF; (b) 3D refractive index profile; (c) one dimensional refractive index profile along the line passes through the two cores](/Images/icon/loading.gif)
Fig. 14. Cross section and refractive index profile[117]. (a) Cross section of HTCF; (b) 3D refractive index profile; (c) one dimensional refractive index profile along the line passes through the two cores
![Device and experimental schematic diagram[117]. (a) Optofluidic optical fiber Michelson interferometer; (b) process of the experiment; (c) cross section of the fiber with Au film; (d) microhole on the surface of the fiber](/Images/icon/loading.gif)
Fig. 15. Device and experimental schematic diagram[117]. (a) Optofluidic optical fiber Michelson interferometer; (b) process of the experiment; (c) cross section of the fiber with Au film; (d) microhole on the surface of the fiber
![Correspondence between the interference spectrum and the concentration of Vc solution[117]](/Images/icon/loading.gif)
Fig. 16. Correspondence between the interference spectrum and the concentration of Vc solution[117]
![Schematic diagram of integrated optical fiber flow control ethanol detection device[118]](/Images/icon/loading.gif)
Fig. 17. Schematic diagram of integrated optical fiber flow control ethanol detection device[118]
![Photo of the optical fiber[118]. (a) Microscope image of a hollow suspended core fiber without graphene oxide (GO) film; (b) SEM images of the optical fiber containing GO films; (c) SEM of the suspended core coated with GO film; (d) Raman spectroscopy of GO](/Images/icon/loading.gif)
Fig. 18. Photo of the optical fiber[118]. (a) Microscope image of a hollow suspended core fiber without graphene oxide (GO) film; (b) SEM images of the optical fiber containing GO films; (c) SEM of the suspended core coated with GO film; (d) Raman spectroscopy of GO
![Dynamic response of sensor[118]. (a) Response of different concentrations of ethanol for optofluidic sensor with and without the GO coated on the fiber core; (b) dynamic response of an integrated opto-fluidic fiber sensor device based on GO to the corresponding ethanol concentration](/Images/icon/loading.gif)
Fig. 19. Dynamic response of sensor[118]. (a) Response of different concentrations of ethanol for optofluidic sensor with and without the GO coated on the fiber core; (b) dynamic response of an integrated opto-fluidic fiber sensor device based on GO to the corresponding ethanol concentration
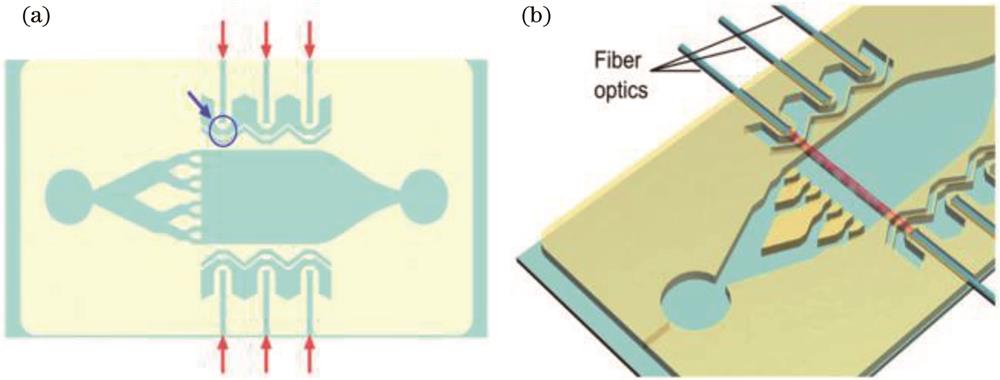
Set citation alerts for the article
Please enter your email address