
- Photonics Research
- Vol. 10, Issue 2, 444 (2022)
Abstract
1. INTRODUCTION
Due to high conversion efficiency, good beam quality, convenient thermal management, and compact structure, high power fiber lasers have been widely required in industrial and scientific applications [1–3]. However, power scaling of single-fiber laser sources beyond multi-kilowatt faces various physical challenges, such as thermal damage, nonlinear effects, fiber end-face damage, and thermal effects [4–6]. Coherent beam combination (CBC) by active phase-locking technology can scale the fiber power with the spatial and spectral brightness increasing and is a promising way to overcome the aforementioned limitation [2,7], which has no established channel limit, but constraints due to cost, complexity, and packaging will ultimately bound channel counts [8]. The multi-kilowatt narrow linewidth excellent laser beam has already been demonstrated in free-space CBC architecture [9,10], and CBC of more than 100 fiber lasers has also been demonstrated [11]. However, the free-space architecture generally needs large space and is suspect to environment perturbations [12]. Stray light management is another engineering problem, especially for CBC technology, where the accidental coupling of stray light into narrow linewidth fiber amplifiers may cause catastrophic damages [13]. All-fiber architectures can offer a compact and robust solution, which has a great resistance to disturbance. The all-fiber structure is a coherent combination method with a filling aperture. In 2012, researchers demonstrated CBC by a fiber combiner, and a perfect beam with
In this paper, based on the self-imaging effect in the square core fiber, an all-fiber combiner for high power CBC has been proposed and analyzed numerically. The structure of the all-fiber CBC system based on the principle of the self-imaging effect is firstly introduced, and then the beam combining device based on a square fiber is introduced in detail. The principle and the numerical design of the coherent signal laser combiner have been carried out, which is verified by theoretical research and experiment.
2. SIMULATION AND DESIGN OF ALL-FIBER COHERENT BEAM COMBINER
A. Principle of Coherent Signal Laser Combiner
A glass capillary has been employed as a re-imaging waveguide, which produced more than 100 W of coherent output with 80% combining efficiency and excellent beam quality in free-space configurations [20]. To minimize the length of the glass capillary, the fiber array was composed of thermally collapsed, polished, and AR-coated photonic crystal fiber (PCF) ports to reduce the lateral size of the capillary. There is an air-glass interface, which means that it is hard for the fiber array to achieve several kilowatt operations due to surface damage limit [21]. For the all-fiber signal combiner, the fiber bundle or array is spliced to the output combining fiber directly, which can eliminate the interface between the fiber array and the hollow re-imaging waveguide and avoid the surface damage limit. The fiber can also be shaped in a square, which can act as the re-imaging waveguide, and the light is confined in the square by the total reflection interface between the core and cladding.
Sign up for Photonics Research TOC. Get the latest issue of Photonics Research delivered right to you!Sign up now
It is shown that strongly confined waveguides are required to achieve the perfect beam combination [20,22]. For practical fibers, the cladding is generally doped with F to reduce the refractive index, while the core is doped with Ge to raise the refractive index [23], and the core NA is about 0.2–0.3, which means that the confining capability is not strong as those in Refs. [20,22]. To evaluate whether the square core fiber is suitable for CBC application, the self-imaging effect of the square fiber is numerically investigated firstly. For high power fiber lasers, large mode area (LMA) fibers are employed, and a core diameter of 25 μm has been used to achieve a multi-kilowatt narrow linewidth fiber laser, which are a compromise between nonlinear stimulated Brillouin scattering (SBS) and mode instability (MI) effects to achieve maximum output power with good beam quality and narrow linewidth [24,25]. In the simulation, the fundamental mode of fiber with the core diameter being 25 μm and core NA being 0.065 acted as the input field, which was injected into a 200 μm square core fiber with the core NA being 0.22 and core refractive index being 1.457. The wavelength was set to be 1064 nm. The self-imaging length, which corresponds to the waveguide length, where distinct beams reform into one beam, can be calculated by the following analytical formula [22,26]:
Figure 1.(a) Schematic diagram of a square core fiber waveguide. (b) Diagram of the transmission results and the beam spots.
It is known that the input beam can reform into one beam at the integer multiple of the imaging length [29]. The beam quality and beam profile at different integer multiples of the imaging length have been calculated, which are shown in Fig. 2. In the results, the beam spot at the length of zero is the output laser beam spot from the fiber laser, and L is the length of the square fiber when the first self-image appears. One can see that, as the multiples increase, the re-imaged beam distorts obviously, and side-lobes show up. This is due to the square core fiber not being a strongly confined waveguide, and some excited modes leak out of the core. Although there is the self-imaging effect, the effects deteriorate as more modes leak out with the increasing length of the fiber. To achieve the best self-imaging performance, the fiber length should just be the imaging length.
Figure 2.Diagram of the beam quality and beam profile at different integer multiple of the imaging length.
Based on the above results, an all-fiber combiner has been proposed, and the schematic diagram of the all-fiber combiner based on the square fiber is shown in Fig. 3(a), which takes the
Figure 3.(a) Schematic diagram of the beam combining device. (b) Schematic diagram of the all-fiber CBC system with a square fiber combiner.
B. Numerical Design of Coherent Signal Laser Combiner
For all-fiber CBC systems, the key component is the all-fiber combiner, which needs to be analyzed in detail. For the sake of simplicity, the
The influence of the NA on the beam combining effect has been calculated, and the results are shown in Fig. 4. It is assumed that the core size of the square fiber is 150 μm, and the core diameter of the fibers of the
Figure 4.(a) Beam quality as a function of NA. (b) Beam efficiency as a function of NA.
Next, the core size of the square fiber and the size of the fiber array are discussed and simulated, and the results are shown in Fig. 5. According to the results in Fig. 4, the NA is set to 0.5. To avoid the inter-fiber mode cross coupling, the minimal sizes of the cladding diameter are taken to be about three times the core diameter, corresponding to
Figure 5.(a) Beam quality as a function of fiber core size and square fiber core size. (b) Beam efficiency as a function of fiber core size and square fiber core size.
It is shown in Fig. 5(a) that the optimal beam quality achieved for each case is different, which needs to be analyzed further. The optimal beam quality that can be achieved for different input fiber core diameters has been calculated, which is shown in Fig. 6. The NA is set to 0.5. The core diameter of the input fiber of the fiber array is set from 20 to 50 μm. In order to compare the best combining effect at different core diameters of the fiber array, for each core diameter of the input fiber, according to the results in Fig. 5, the smallest size of the square fiber that can achieve combination is selected, which is equal to six times the core diameter of the input fiber. So, the core size of the square fiber is in a range of 120–300 μm, as the core diameter of the input fiber of the fiber array changes. One can see that, as the input fiber core diameter increases, the achievable maximal combining performance becomes better. However, the combining performance degrades as the input fiber core diameter increases beyond 30 μm, and the
Figure 6.(a) Optimal beam quality as a function of fiber core size. (b) Beam efficiency as a function of fiber core size with
In the above simulations, the
Figure 7.(a) Beam quality as a function of NA with different fiber arrays. (b) Beam efficiency as a function of NA with different fiber arrays. (c) Diagram of typical intensity distribution of a
Based on the above results, one can conclude that, to achieve the best combining performance under the present conditions, the combiner should be composed of a
Figure 8.(a) Input intensity distribution with the
C. Discussion
In Section 2.B, the fibers are arranged into an array and then fused with the square fiber, which results in the coherent combination efficiency being above 97%. For comparison, the coherent combination of the fiber array without a square fiber, similar to the lens arrays, has been simulated, as shown in Fig. 9, and the results of those with the square fiber have also been listed. The
Figure 9.(a) Diagram of output intensity distribution from the
It is known that the broadening of the laser linewidth can result in reduction of combining efficiency [41]. This can be eliminated through employing optical delay lines, and fiber sources with several tens of nanometers linewidth have been coherently combined with high efficiency [2,42]. On the other hand, the self-imaging length is dependent on center wavelength, as shown in Eq. (3), which means that the broadband linewidth may cause efficiency loss due to the mismatch of self-imaging length for different wavelength components. To analyze the effect quantitatively, the combining of two different wavelengths has been calculated with the self-imaging length chosen to correspond to only one wavelength. The calculation is still based on the
Figure 10.(a) Beam quality as a function of wavelength. (b) Beam efficiency as a function of wavelength.
Then, the influence of the vibration and thermal effect on beam combination of the square fiber is analyzed. As described in Section 2.A, the scheme of coherent beam combining using the self-imaging effect of the square fiber is a coherent combining scheme of all optical fibers, and the advantages of the all-fiber system lie in its compact structure and great anti-disturbance ability. For the thermal effect on the combination, the influence on the square fiber is mainly discussed. According to the thermal expansion formula, the change in the size of the square fiber when the temperature is increased by 100°C is calculated. The formula can be expressed as follows [44]:
Figure 11.Diagram of the comparison and data fitting of the combining efficiency of different fiber arrays.
3. DEMONSTRATION OF COHERENT BEAM DE-COMBINATION IN SQUARE CORE FIBER
A. Experimental Setup
Experimental study has been carried out to verify the self-imaging effect in the square fiber. According to the results of the simulation above, LMA fibers with the core/cladding diameters being 25 μm/400 μm were chosen to deliver the laser. To match the output fiber and follow the principle of choosing the least square fiber core size, a square fiber with 200 μm core size and 440 μm cladding size was used. The core NA of the square fiber is 0.22. The cross section of the square fiber observed under the microscope is shown in Fig. 12. One can see that the shape of the cladding of the square fiber is a circle, which makes the connection between the laser delivering fiber and the square fiber more convenient. Under the microscope, the actual size of the cross section of the square fiber is measured, and the side length of the square fiber is measured as 200 μm. It can be seen from Fig. 12 that the four corners of the square fiber are not right angles but rounded corners. The radius of the rounded corners is measured to be 18 μm. The angles between the adjacent sides of the square fiber are also measured and marked in Fig. 12.
Figure 12.Diagram of the cross section of the square fiber.
The experimental setup is shown in Fig. 13. The laser source is a linearly polarized single-frequency distributed feedback (DFB) laser, which was boosted by a piece of LMA polarization-maintaining ytterbium-doped fiber with the core/cladding diameter being 10 μm/125 μm. An isolator (ISO) has been employed to protect the seed from the influence of backward light. The amplifier was co-pumped, and the pump power was injected into the amplifier through a
Figure 13.Diagram of the experimental structure.
B. Results and Analysis
The laser beam from MFA was measured first, which is shown in Fig. 14. With the MFA to match the mode field, near single-mode beam quality has been achieved, and, according to the instruction of the
Figure 14.(a) Diagram of the beam spot from MFA. (b)
The fiber had an index of approximately 1.457 and an aperture of approximately 200 μm, which results in the self-imaging length of the square fiber being calculated to be 5.5 cm from Eq. (3). The output fiber of the MFA has been spliced to the square fiber carefully to avoid lateral offset error, and the side view of the splice point between the output fiber and the square core fiber is shown in Fig. 15.
Figure 15.Diagram of the side view of the splice point between the output fiber and the square core fiber.
The beam spots at 5.5 cm and 11 cm were measured and are shown in Fig. 16. One can see that the Gaussian beam has been achieved at the self-imaging length, which degrades dramatically as the length is taken to be two times that of the self-imaging length. The
Figure 16.(a) Diagram of the beam spot at the 5.5 cm length of the square fiber. (b) Diagram of the beam spot at the 11 cm length of the square fiber. (c)
Regardless of the specific optical realization, one component can act as splitter, and it can be used as combiner in reverse, which means that the split properties of the square fiber can be a good guide for its performance in combination. Then, the square fiber was used as a beam splitter, and the square core fiber was cut into a half length of 2.75 cm, which was then shortened to 1.83 cm to create the
Figure 17.Theoretical and experimental comparison of the self-imaging effect in the square fiber.
4. CONCLUSION
In this paper, the self-imaging effect of the square fiber has been investigated, and an all-fiber combiner for coherent combining applications has been proposed. The influence of various parameters has been studied numerically. From the results, it can be seen that the NA and the core size of the square fiber, the size, and the number of the fiber array all affect the beam combining effect. The degradation of beam quality in the combined beam is mainly due to the generation of side-lobes. If the side-lobes are truncated, the beam quality is close to the diffraction limit. By simulating different parameters of the beam combiner, good performance parameters and optimized directions of the beam combiner can be obtained.
An experiment is carried out to verify the self-imaging of the square fiber. The experimental results show that the square fiber can act as a self-imaging waveguide, but the performance degrades as the imaging length increases. The energy loss and the appearance of side spots are also analyzed by detecting the beam spots in different positions. The experimental results agree well with the theoretical results, which further prove the feasibility of the square fiber for CBC. In the future, experiments on an all-fiber combiner will be carried out.
References
[1] D. J. Richardson, J. Nilsson, W. A. Clarkson. High power fiber lasers: current status and future perspectives. J. Opt. Soc. Am. B, 27, B63-B92(2010).
[2] Z. Liu, X. Jin, R. Su, P. Ma, P. Zhou. Development status of high power fiber lasers and their coherent beam combination. Sci. China Inf. Sci., 62, 1-32(2019).
[3] W. Shi, A. Schulzgen, R. Amezcua, X. Zhu, S.-U. Alam. Fiber lasers and their applications: introduction. J. Opt. Soc. Am. B, 34, FLA1(2017).
[4] J. Zhu, P. Zhou, Y. Ma, X. Xu, Z. Liu. Power scaling analysis of tandem-pumped Yb-doped fiber lasers and amplifiers. Opt. Express, 19, 18645-18654(2011).
[5] R. Tao, X. Wang, P. Zhou. Comprehensive theoretical study of mode instability in high-power fiber lasers by employing a universal model and its implications. IEEE J. Sel. Top. Quantum Electron., 24, 0903319(2018).
[6] M. N. Zervas. Transverse mode instability, thermal lensing and power scaling in Yb3+-doped high-power fiber amplifiers. Opt. Express, 27, 19019-19041(2019).
[7] Z. Liu, P. Ma, R. Su, R. Tao, Y. Ma, X. Wang, P. Zhou. High-power coherent beam polarization combination of fiber lasers: progress and prospect [Invited]. J. Opt. Soc. Am. B, 34, A7-A14(2017).
[8] T. Y. Fan. Laser beam combining for high-power, high-radiance sources. IEEE J. Sel. Top. Quantum Electron., 11, 567-577(2005).
[9] A. Flores, I. Dajani, R. Holten, T. Ehrenreich, B. Andersona. Multi-kilowatt diffractive coherent combining of pseudorandom-modulated fiber amplifiers. Opt. Eng., 55, 096101(2016).
[10] P. Ma, H. Chang, Y. Ma, R. Su, J. Zhou. 7.1 kW coherent beam combining system based on a seven-channel fiber amplifier array. Opt. Laser Technol., 140, 107016(2021).
[11] H. Chang, Q. Chang, J. Xi, T. Hou, R. Su, P. Ma, J. Wu, C. Li, M. Jiang, Y. Ma, P. Zhou. First experimental demonstration of coherent beam combining of more than 100 beams. Photon. Res., 8, 1943-1948(2020).
[12] S. Chen, Y. Li, K. Lu. Branch arm filtered coherent combining of tunable fiber lasers. Opt. Express, 13, 7878-7883(2005).
[13] M. Karow, J. Neumann, D. Kracht, P. Wessels. Impact of amplified spontaneous emission on Brillouin scattering of a single-frequency signal. Opt. Express, 20, 10572-10582(2012).
[14] E. A. Shcherbakov, V. V. Fomin, A. A. Abramov, A. A. Ferin, D. V. Mochalov, V. P. Gapontsev. Industrial grade 100 kW power CW fiber laser. Advanced Solid-State Lasers Congress, ATh4A.2(2013).
[15] P. Zhou, L. Huang, J. Leng, H. Xiao, J. Xu, T. Yao. High-power double-clad fiber lasers: 30 years of development. Sci. Chin. Technol., 50, 123-135(2020).
[16] J. E. Rothenberg. All-fiber integrated high power coherent beam combination. U.S. patent(2012).
[17] J. E. Rothenberg, E. C. T. Cheung. Integrated spectral and all-fiber coherent beam combination. U.S. patent(2012).
[18] J. Li, H. Zhao, Z. Chen, X. Wang, X. Xu. All-fiber active coherent combining via a fiber combiner. Opt. Commun., 286, 273-276(2013).
[19] B. Yang, X. Wang, P. Ma, Z. Pu, X. Xu. Active phase locking of four Yb-doped fiber amplifiers with a multi-mode fiber combiner. International Photonics and OptoElectronics Meetings, JF2A.6(2014).
[20] R. Uberna, A. Bratcher, T. G. Alley, A. D. Sanchez, A. S. Flores, B. Pulford. Coherent combination of high power fiber amplifiers in a two-dimensional re-imaging waveguide. Opt. Express, 18, 13547-13553(2010).
[21] J. W. Dawson, M. J. Messerly, R. J. Beach, M. Y. Shverdin, E. A. Stappaerts, A. K. Sridharan, P. H. Pax, J. E. Heebner, C. W. Siders, C. P. J. Barty. Analysis of the scalability of diffraction-limited fiber lasers and amplifiers to high average power. Opt. Express, 16, 13240-13266(2008).
[22] R. Tao, L. Si, Y. Ma, P. Zhou, Z. Liu. Coherent beam combination of fiber lasers with a strongly confined waveguide: numerical model. Appl. Opt., 51, 5826-5833(2012).
[23] C. K. Jen, J. E. B. Oliveira, N. Goto, K. Abe. Role of guided acoustic-wave properties in single-mode optical fiber design. Electron. Lett., 24, 1419-1420(1988).
[24] H. Lin, R. Tao, C. Li, B. Wang, C. Guo, Q. Shu, P. Zhao, L. Xu, J. Wang, F. Jing, Q. Chu. 3.7 kW monolithic narrow linewidth single mode fiber laser through simultaneously suppressing nonlinear effects and mode instability. Opt. Express, 27, 9716-9724(2019).
[25] R. Tao, R. Su, P. Ma, X. Wang, P. Zhou. Suppressing mode instabilities by optimizing the fiber coiling methods. Laser Phys. Lett., 14, 025101(2017).
[26] R. Tao, X. Wang, P. Zhou, L. Si. Analysis of the effects of mismatched errors on coherent beam combining based on a self-imaging waveguide. Quantum Electron., 46, 61-67(2016).
[27] R. Scarmozzino, A. Gopinath, R. Pregla, S. Helfert. Numerical techniques for modeling guided-wave photonic devices. IEEE J. Sel. Top. Quantum Electron., 6, 150-162(2000).
[28] R. Scarmozzino, R. M. Osgood. Comparison of finite-difference and Fourier-transform solutions of the parabolic wave equation with emphasis on integrated-optics applications. J. Opt. Soc. Am. A, 8, 724-731(1991).
[29] O. Bryngdahl. Image formation using self-imaging techniques. J. Opt. Soc. Am. B, 63, 416-419(1973).
[30] I. Dajani, A. Flores, R. Holten, B. Anderson, B. Pulford, T. Ehrenreich. Multi-kilowatt power scaling and coherent beam combining of narrow-linewidth fiber lasers. Proc. SPIE, 9728, 972801(2016).
[31] Y. Ma, P. Zhou, X. Wang, H. Ma, X. Xu, L. Si, Z. Liu, Y. Zhao. Coherent beam combination with single frequency dithering technique. Opt. Lett., 35, 1308-1310(2010).
[32] R. Tao, Y. Ma, L. Si, X. Dong, P. Zhou, Z. Liu. Target-in-the-loop high-power adaptive phase-locked fiber laser array using single-frequency dithering technique. Appl. Phys. B, 105, 285-291(2011).
[33] M. Bachmann, P. A. Besse, H. Melchior. General self-imaging properties in
[34] R. Tao, X. Wang, H. Xiao, P. Zhou, L. Si. Coherent beam combination of fiber lasers with a strongly confined tapered self-imaging waveguide: theoretical modeling and simulation. Photon. Res., 1, 186-196(2013).
[35] M. C. Paul, R. Sen, T. Bandyopadhyay. Fluorine incorporation in silica glass by MCVD process—a critical study. J. Mater. Sci., 32, 3511-3516(1997).
[36] S. R. Nagel, J. B. Macchesney, K. L. Walker. An overview of the modified chemical vapor-deposition (MCVD) process and performance. IEEE J. Quantum Electron., 18, 459-476(1982).
[37] A. E. Siegman. How to (maybe) measure laser beam quality. DPSS (Diode Pumped Solid State) Lasers: Applications and Issues, MQ1(1998).
[38] R. Tao, L. Si, Y. Ma, P. Zhou, Z. Liu. Propagation of coherently combined truncated laser beam arrays with beam distortions in non-Kolmogorov turbulence. Appl. Opt., 51, 5609-5618(2012).
[39] I. Fsaifes, L. Daniault, S. Bellanger, M. Veinhard, J. Bourderionnet, C. Larat, E. Lallier, E. Durand, A. Brignon, J. C. Chanteloup. Coherent beam combining of 61 femtosecond fiber amplifiers. Opt. Express, 28, 20152-20161(2020).
[40] P. Zhou, X. Wang, Y. Ma, H. Ma, Z. Liu, X. Xu. Optimal truncation of element beam in a coherent fiber laser array. Chin. Phys. Lett., 26, 044206(2009).
[41] G. D. Goodno, C. C. Shih, J. E. Rothenberg. Perturbative analysis of coherent combining efficiency with mismatched lasers. Opt. Express, 18, 25403-25414(2010).
[42] M. Muller, C. Aleshire, A. Klenke, E. Haddad, F. Legare, A. Tunnermann, J. Limpert. 10.4 kW coherently combined ultrafast fiber laser. Opt. Lett., 45, 3083-3086(2020).
[43] X. Wang, P. Zhou, R. Su, P. Ma, R. Tao, Y. Ma, X. Xu, Z. Liu. Current situation, tendency and challenge of coherent combining of high power fiber lasers. Chin. J. Lasers, 44, 0201001(2017).
[44] Y. S. Touloukian, R. K. Kirby, R. E. Taylor, P. D. Desai. Thermal Expansion: Metallic Elements and Alloys. Thermophysical Properties of Matter, 12(1975).
[45] https://www.ipgphotonics.com. https://www.ipgphotonics.com
[47] Y. Wang, Y. Sun, W. Peng, Y. Feng, J. Wang, Y. Ma, Q. Gao, R. Zhu, C. Tang. 3.25 kW all-fiberized and polarization-maintained Yb-doped amplifier with a 20 GHz linewidth and near-diffraction-limited beam quality. Appl. Opt., 60, 6331-6336(2021).
[48] Z. Huang, Q. Shu, R. Tao, Q. Chu, Y. Luo, D. Yan, X. Feng, Y. Liu, W. Wu, H. Zhang, H. Lin, J. Wang, F. Jing. > 5 kW record high power narrow linewidth laser from traditional step-index monolithic fiber amplifier. IEEE Photon. Technol. Lett., 33, 1181-1184(2021).
[49] Y. Liu, S. Huang, W. Wu, P. Zhao, X. Tang, X. Feng, M. Li, B. Shen, H. Song, R. Tao, J. Wang. 2 kW high stability robust fiber cladding mode stripper with moderate package temperature rising. IEEE Photon. Technol. Lett., 32, 1151-1154(2020).
[50] B. Yang, W. Peng, H. Zhang, X. Xi, X. Xu. 6 kW single mode monolithic fiber laser enabled by effective mitigation of the transverse mode instability. Opt. Express, 29, 26366-26374(2021).
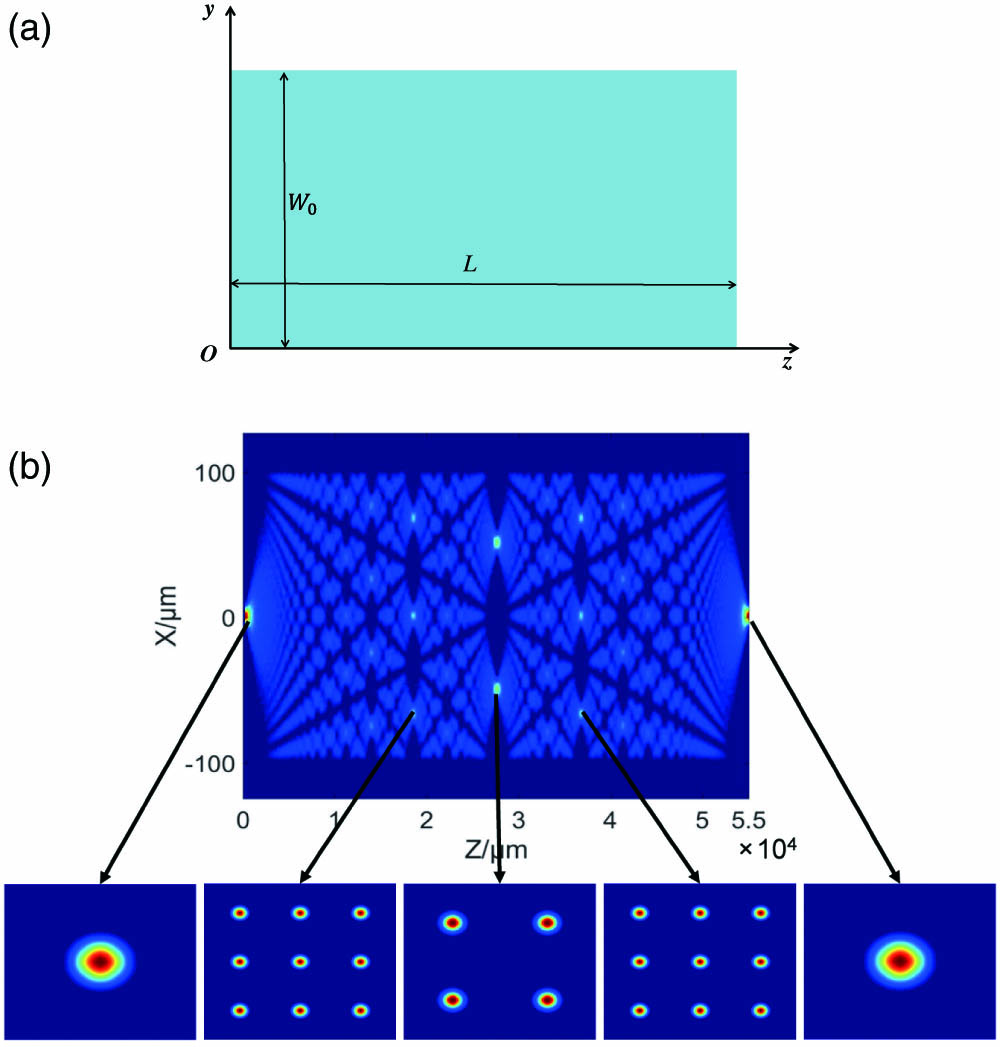
Set citation alerts for the article
Please enter your email address