Xiaoshuai An, Hongying Yang, Yumeng Luo, Zhiqin Chu, Kwai Hei Li, "Ultrafast miniaturized GaN-based optoelectronic proximity sensor," Photonics Res. 10, 1964 (2022)

Search by keywords or author
- Photonics Research
- Vol. 10, Issue 8, 1964 (2022)
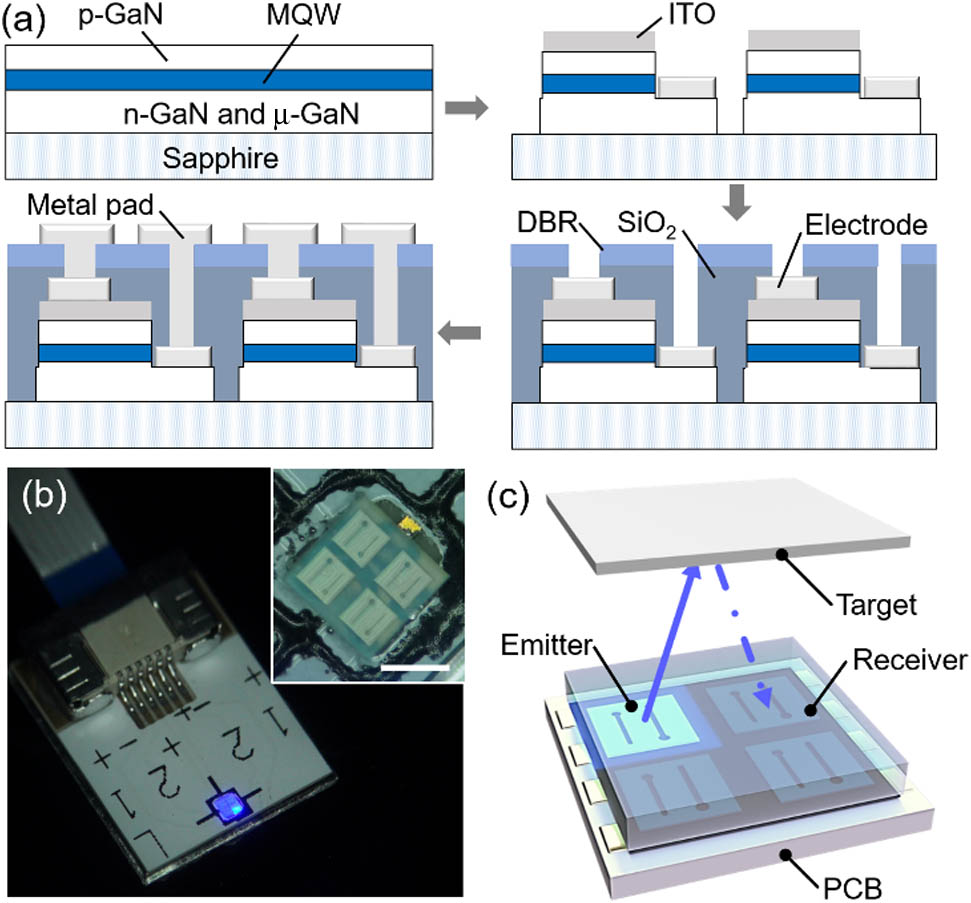
Fig. 1. (a) Schematic diagrams showing the fabrication process flow of the GaN chip. (b) Optical image of the packaged chip; inset shows the enlarged image of the chip. Scale bar is 500 μm. (c) Schematic diagram depicting the operating principle of the proximity sensor.
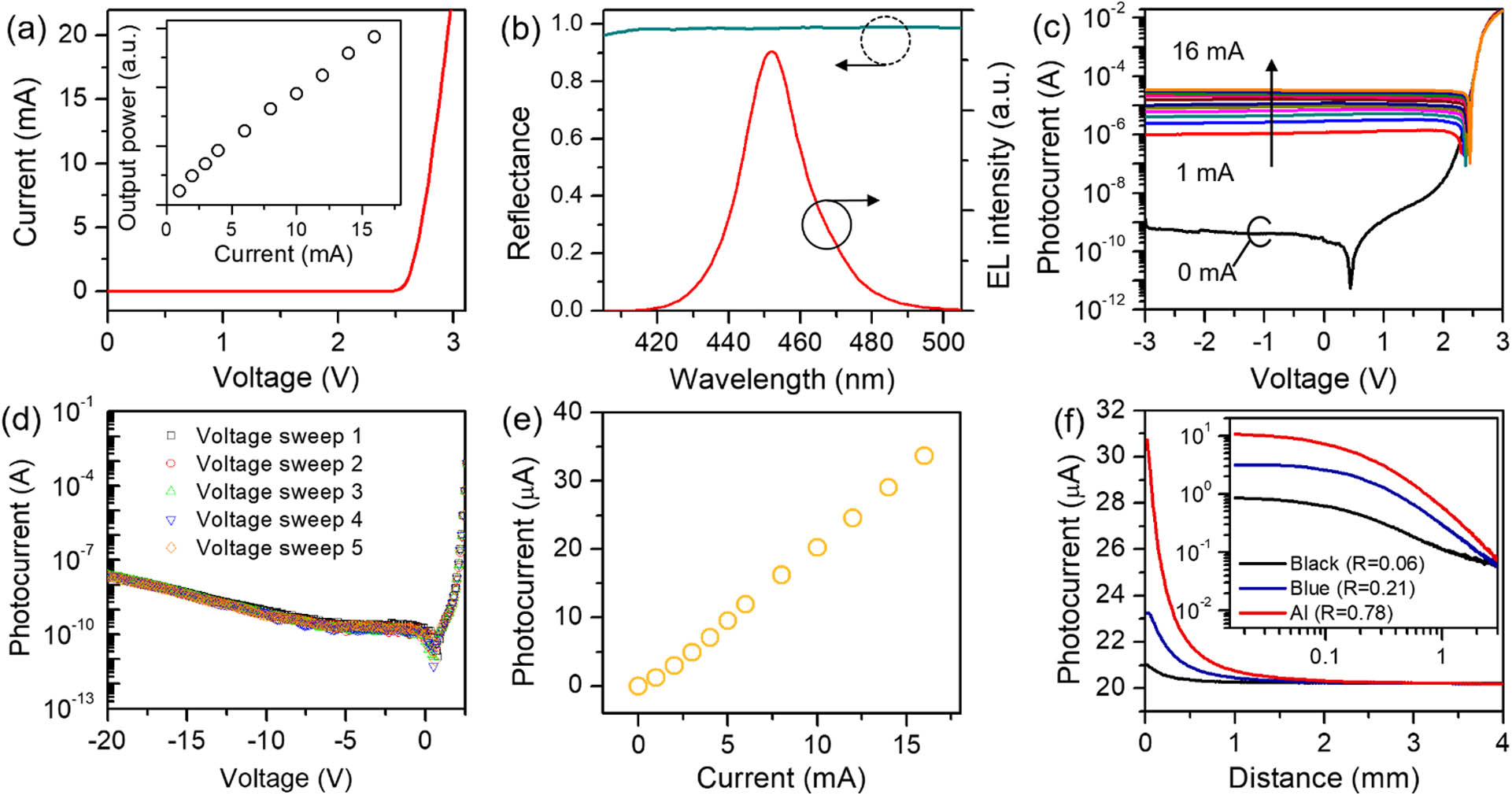
Fig. 2. (a) I-V characteristic of the on-chip unit as an emitter. Inset shows the light output intensity as a function of injection current. (b) Emission spectrum of the emitter operating at 10 mA and reflectance plot of the DBR measured at normal incidence; (c) I-V characteristic of the on-chip unit as a receiver when the emitter operates at different currents; (d) I-V characteristic of the receiver measured at reverse bias voltages of up to − 20 V ; (e) plot of photocurrent of the receiver versus driving current of the emitter; (f) photocurrent as a function of the distance of the sensor from the films with varying reflectance; inset shows photocurrent change versus the distance of the sensor from the films on a logarithmic scale.
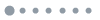
Fig. 3. (a) Transient response of the sensor. The emitter is biased with square waves with high voltage levels of 2.8 V, 3.0 V, and 3.2 V. (b) Optical image of the experimental setup used to measure the dynamic response of the sensor. The inset shows a close-up image. (c) Dynamic response measured from an Al foil moving back and forth repeatedly at different distances from the surface of the sensor. Inset shows the schematic of experimental measurement. (d) Measured photocurrent under one cyclic movement of Al foil between d = 0.035 mm and d = 3 mm at different speeds; (e) measured photocurrent distribution of the sensor over 8000 cycles under the conditions of back-and-forth motion between d = 0.015 m m and d = 0.4 mm and a speed of 1 m/s. The emitter current is fixed at 10 mA for the measurement for (c)–(e).
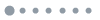
Fig. 4. Sensor for real-time monitoring. Optical images of the sensor mounted on (a) volunteer’s neck, and close to (b) mechanical pump, (c) speaker diaphragm; (d)–(f) photocurrent profiles measured from the corresponding conditions in (a)–(c); the driving current of the emitter is fixed at 10 mA.
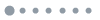
Fig. 5. (a) Optical image of the sensor mounted close to rotating disk half-painted in black and white; (b) photocurrent profiles measured from the disk at different rotating speeds when the emitter current is 10 mA.
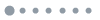
Fig. 6. (a) Optical images showing the selective area coverage of the Al foils on the sensor using the micropositioners; distributions of photocurrent changes of units acting as receivers when Al foil is overlaid on (b)–(d) single, (e), (f) double, and (g) triple units. The emitter operates at a low current of 1 mA.
|
Table 1. Comparison with Other Reported Work and Commercial Products
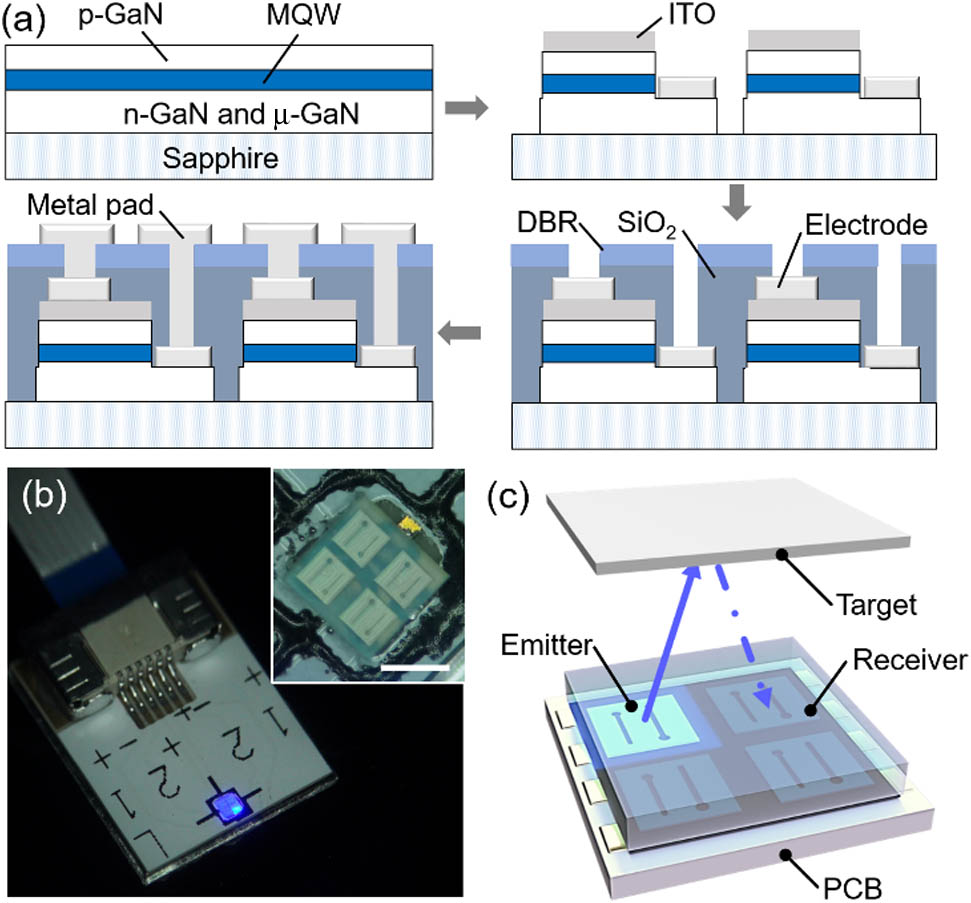
Set citation alerts for the article
Please enter your email address