Le Wan, Shihong Shi, Zhixin Xia, Xiaozu Zhang, Geyan Fu, Rongwei Zhang, Kuan Li. Laser preheating/fluid cooling assisted laser metal deposition of AlSi10Mg[J]. Infrared and Laser Engineering, 2021, 50(7): 20200365

Search by keywords or author
- Infrared and Laser Engineering
- Vol. 50, Issue 7, 20200365 (2021)
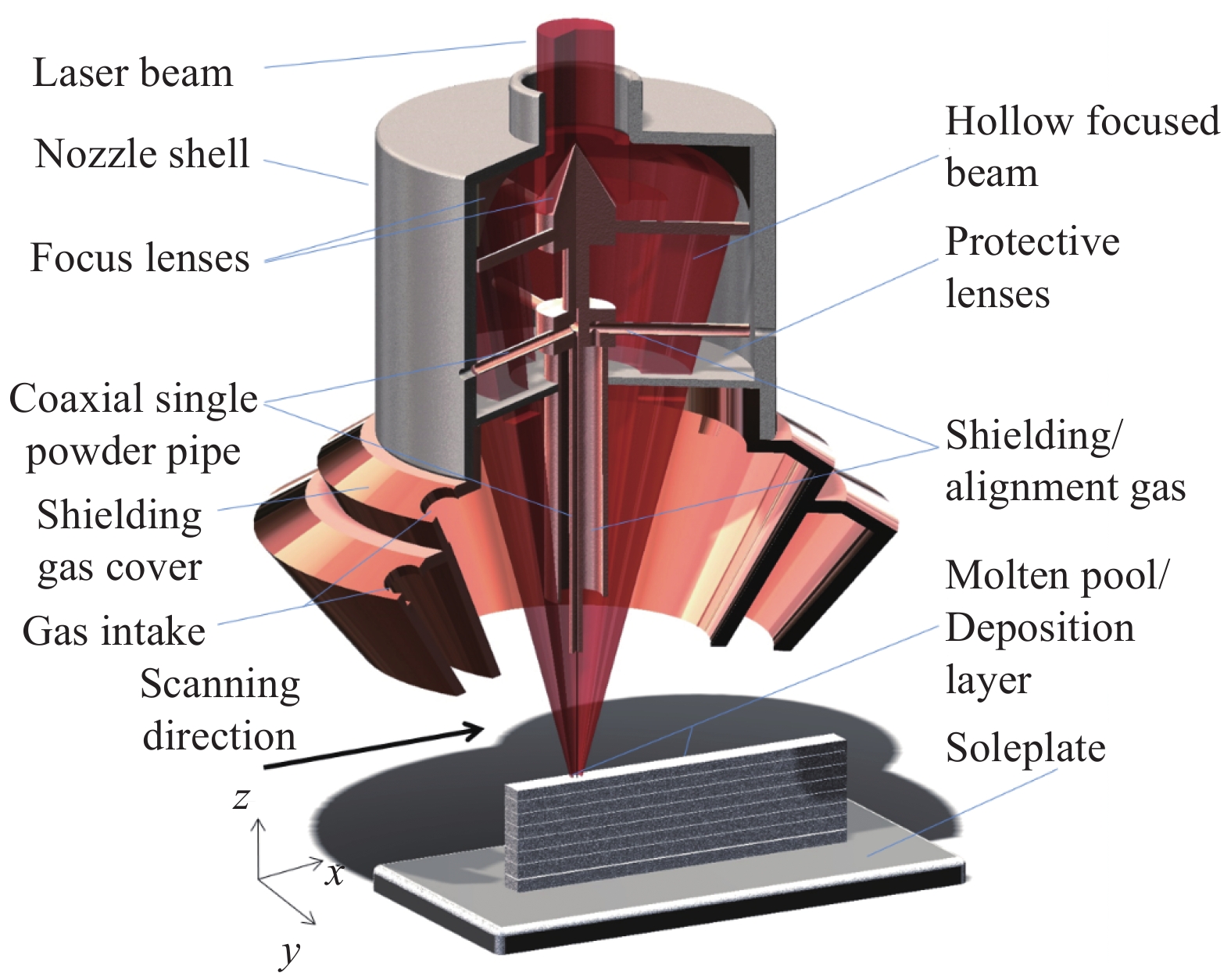
Fig. 1. Schematic of Ar supply protection hollow beam internal powder feeding deposition nozzle
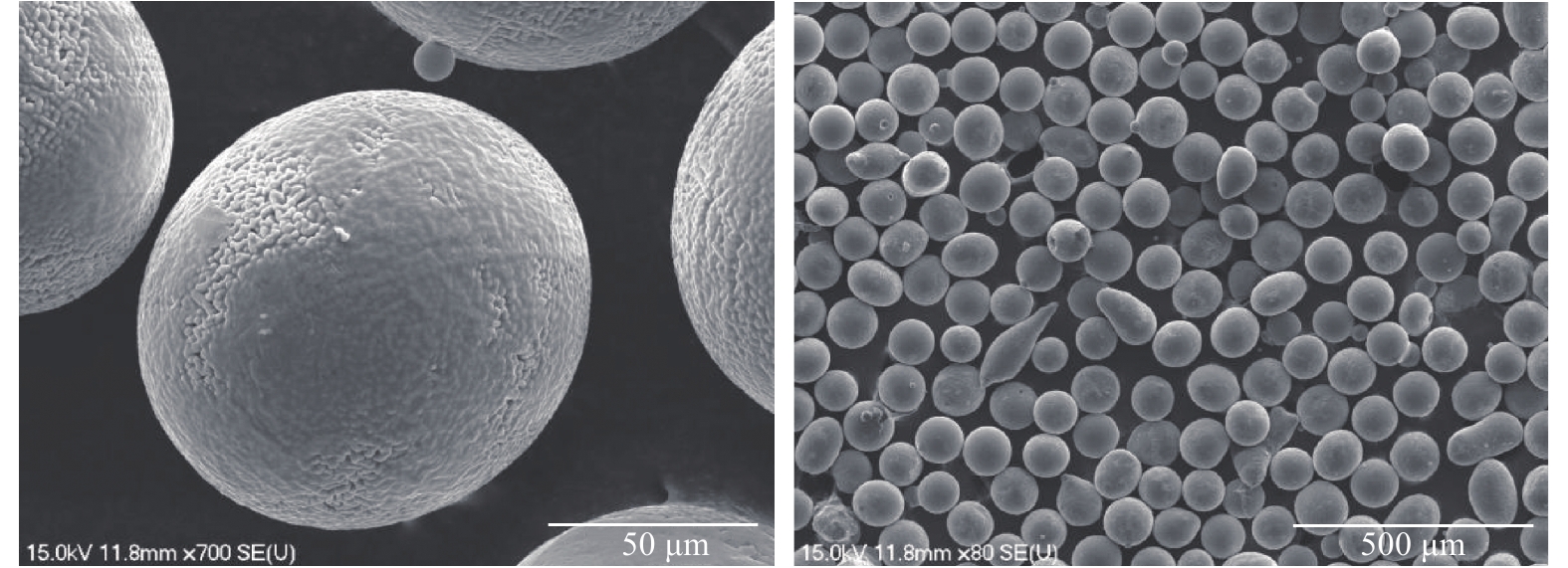
Fig. 2. Micromorphology of AlSi10Mg powder
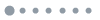
Fig. 3. Schematic of auxiliary temperature control system for laser preheating and fluid cooling
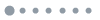
Fig. 4. Temperature control model of preheating and cooling
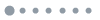
Fig. 5. Temperature curve and fitting equation of sample. (a) Effect of fluid cooling on temperature curve of sample; (b) Fitting of temperature rise section; (c) Fitting of fluid cooling; (d) Fitting of no fluid cooling
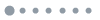
Fig. 6. Schematic of in-situ technique determining laser absorptivity
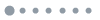
Fig. 7. Experimental measurement results of absorptivity β and the temperature difference between molten pool and preheating
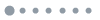
Fig. 8. Infrared thermal image of temperature field distribution of AlSi10Mg aluminium alloy LMD single track with different preheating temperature. (a) 25 ℃; (b) 95 ℃; (c) 150 ℃; (d) 200 ℃
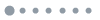
Fig. 9. LMD track cross section and metallography of different preheating temperature. (a) 25 ℃; (b) 45 ℃; (c) 70 ℃; (d) 95 ℃; (e) 120 ℃; (f)-(g) 25 ℃; (h)-(i) 120 ℃
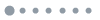
Fig. 10. LMD track cross section and metallography of high preheating temperature. (a) 150 ℃; (b) 200 ℃
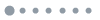
Fig. 11. Curve of grain size (a), surface roughness Ra and micro-hardness Hv0.1 (b) with preheating temperature
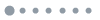
Fig. 12. Cross section of LMD overlap sample. (a) Overlap sample without cooling; (b) Overlap sample of fluid cooling
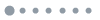
Fig. 13. Cross section of sample of LMD block. (a) Sample without cooling; (b) Sample of cooling every 3 tracks; (c) Sample of assisted cooling forming
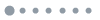
Fig. 14. LMD thin-wall sample. (a) Sample of without cooling; (b) Sample of assisted cooling forming; (c) Sample of some thin-wall parts
|
Table 1. Chemical composition and particle size distribution of AlSi10Mg alloy powder
|
Table 2. Control principles of laser preheating, laser deposition and fluid cooling
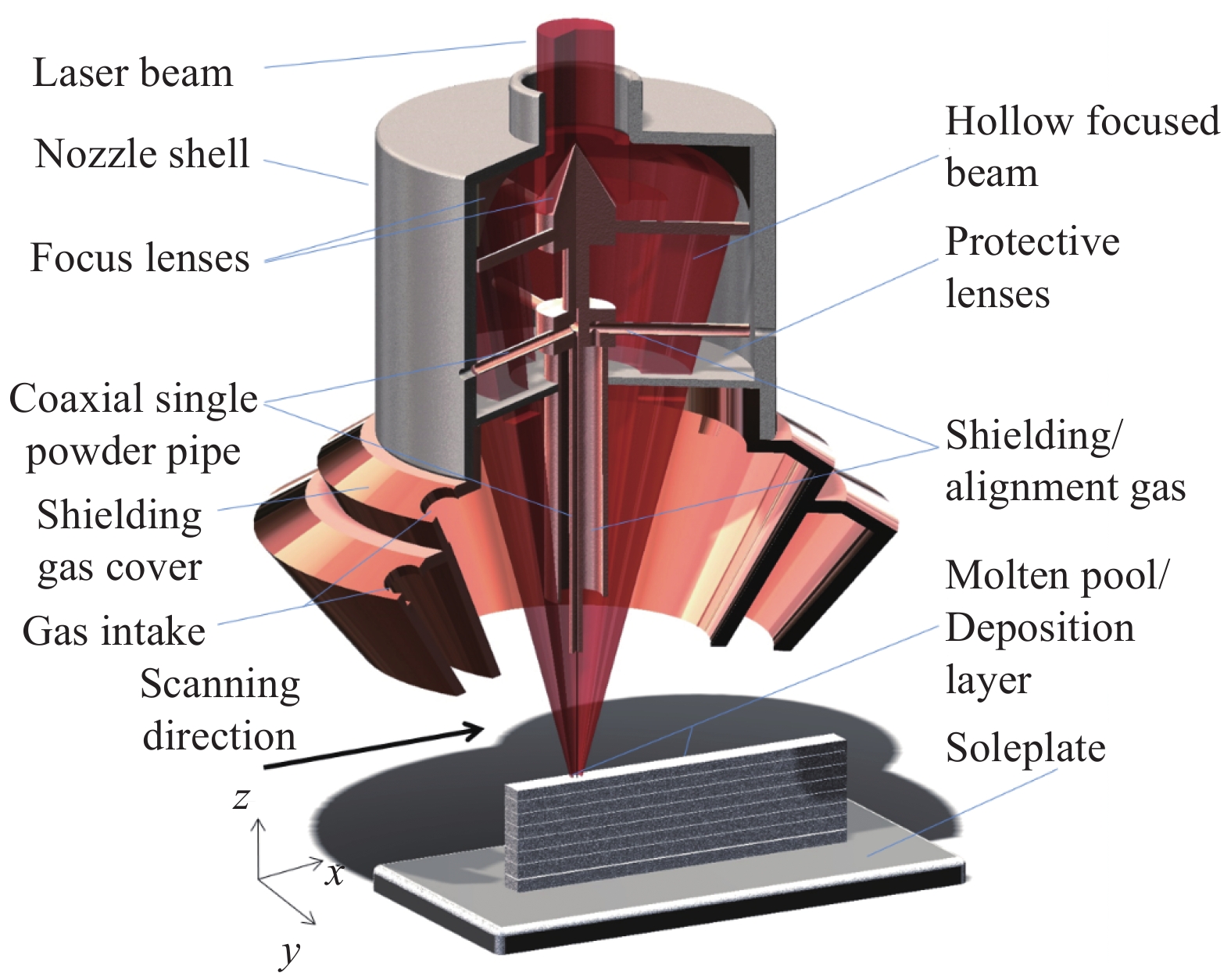
Set citation alerts for the article
Please enter your email address