Kuikui HE, Yutang DAI, Chaofan YAN. Ultrasonic Gas Jet Assisted Femtosecond Laser Etching of Quartz Microgrooves[J]. Acta Photonica Sinica, 2022, 51(11): 1114004

Search by keywords or author
- Acta Photonica Sinica
- Vol. 51, Issue 11, 1114004 (2022)
Abstract
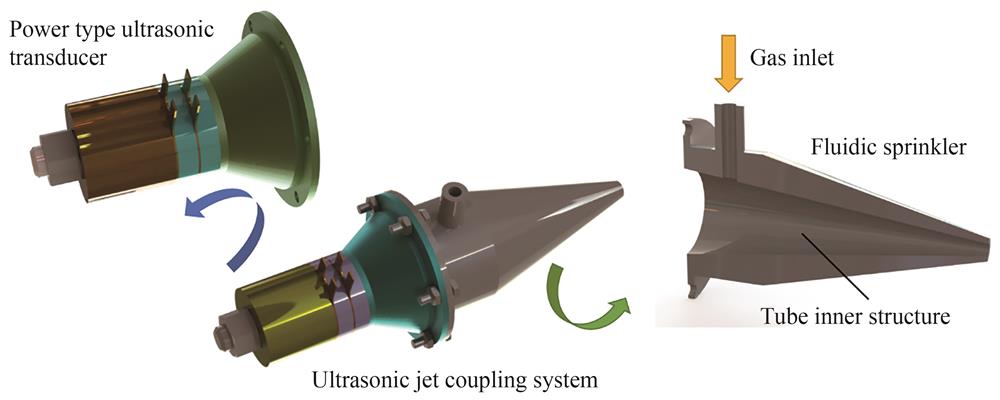
Set citation alerts for the article
Please enter your email address