
- Infrared and Laser Engineering
- Vol. 51, Issue 4, 20210403 (2022)
Abstract
0 Introduction
In three-dimensional (3D) measurement, fringe projection profilometry (FPP) has been widely used in industrial detection, quality control, machine vision, 3D printing, film and television special effects, biomedical industry and other fields because of its rapidity, non-contact, and high accuracy[
PHM or system parameter calibration directly establishes the phase-height mapping relationship through a mathematical model, so there is no need to calibrate the projector. Based on the conventional formula[
Section 1 introduces the principle of PMP method. We describe the principles of the proposed method and traditional method in section 2. Section 3 gives the accuracy evaluation by experiments, and verifies the practicability of the proposed method. Section 4 contains the conclusion of this paper.
1 PMP principle
The light path principle of PMP is shown in Fig.1. A random point
Where,
Figure 1.Schematic diagram of PMP method
By using the projection system of Fig. 1, the sinusoidal fringes with phase shift are projected on the point H of the measured object surface. The encoded sinusoidal fringes are modulated by the measured object surface, and the light intensity can be calculated as follows:
Where,
In this paper, a four
Solving the presented equations uniquely obtains the expression for the phase map
This process is called "phase unwrapping" because the computed phase value has the range
A continuous phase map can be obtained by adopting the three frequency heterodyne phase unwrapping method[
2 Phase-height mapping
2.1 Traditional phase-height mapping
In the measurement system shown in Fig. 1, Eq. (1) is still widely used, and its deformation formula is as follows:
Letting
Where,
Third, because there are two parameters to be determined, the parameters can be estimated from the measurement result when the condition
Figure 2.Schematic diagram of traditional calibration method
2.2 New phase-height mapping
By using the geometric dimension relationship of the electric turntable, the measured surface of the calibration plate passes through the axis of the turntable. A customized calibration plate is placed vertically on the high-precision electric turntable. The process of the new calibration method is shown in Fig. 3.
Figure 3.Schematic diagram of new calibration method
The principle of the new phase-height mapping calibration method is as follows:
Step 1: First, the phase shift method is used to measure the surface of the calibration plane, and the phase information of the measured surface at this time is collected and recorded as
Step 2: The electric turntable drives the calibration plate to rotate at a certain angle, as shown in Fig. 3. We collect the phase information of the calibration plate’s measured plane at this moment and record it as
Step 3: As shown in Fig. 4, Figs. 4(a) and 4(b) are the circle centers of calibration plate image and its partial enlargement, respectively.
Figure 4.Circle marker. (a) Circle center; (b) Partial enlargement of the figure (a)
The camera is used to capture the marker points in the image, and the pixel coordinates of the center of each marker point are identified and saved. After obtaining the pixel coordinates of the marker point, the phase value
Step 4: As shown in Fig. 5, the height
Figure 5.Schematic of the proposed method
Where,
Step 5: The phase difference
As shown in Fig. 1, because the parameters
Where
3 Experiment
To verify the correctness of the proposed method, physical measurements were carried out. As shown in Fig.1, a measurement system based on turntable is established, the measurement system consists of computer, camera, projector and turntable. The projector model is DLP lightcraft 4500 with a resolution of 912×1140 pixel. The camera is an industrial CMOS camera (MER-131-210U3M) with a resolution of 1280×1024 pixel. The model of turntable is RAP125 (repeated positioning accuracy is less than 0.003°), and the control box is SC300. The measured object includes a block and a sphere, the purpose of measuring the calibration plate is to evaluate the measurement accuracy of the proposed method.
First, a four-step phase-shifting fringe patterns are projected onto a calibration plane, also referred to as the reference plane, and a fringe pattern is captured with a camera. Then, the calibration plane is moved 15 mm, 20 mm, 25 mm, 30 mm and 35 mm in turn, and the four-step phase-shifting fringe patterns are projected onto the calibration plane corresponding to the moving position. Finally, the phase values of the 6 calibration planes including the reference plane are obtained, and the phase values of the 5 calibration planes are subtracted from the phase values of the reference plane to obtain the continuous phase differences of the other 5 calibration planes relative to the reference plane. The continuous phase differences of the 5 calibration planes and the heights of the corresponding calibration planes are substituted into Eq. (8), and the traditional phase-height mapping relationship can be established by calculating parameters
The measurement results obtained by the traditional phase-height calibration method are shown in Fig. 6. Figure 6(a) shows a deformed fringe pattern modulated by the block with a height of 10 mm. Figure 6(b) is part of a deformed fringe pattern. Figure 6(c) shows the continuous phase value of a block obtained by PMP. Figure 6(d) is the 3D point cloud data of a block.
Figure 6.Measurement with the traditional method. (a) The deformed fringe pattern modulated by the block; (b) Part of a deformed fringe pattern; (c) The continuous phase value; (d) 3D point cloud data of a block
The measurement results obtained by using the proposed phase-height calibration method are shown in Fig. 7. Figure 7(a) shows the new calibration system, and the distance from the center of the first marker point on the left to the axis of the turntable is 20 mm, the actual distance between the centers of the marker points is 10 mm, and the rotating angle θ of the turntable is 30°. Figure 7(b) shows the 3D point cloud data of the block with a height of 10 mm.
Figure 7.Measurement with the proposed method. (a) The calibration system; (b) 3D point cloud data of a block
In 3D measurement, the root mean square error (RMSE) is commonly used to assess the measurement accuracy
Where h(u,v) is the reconstruction height of the block, A is the height of the white block with a value is of 10 mm, and m is the total number of pixels in the plane. Substituting the measurement results into Eq. (15) shows that the 3D reconstruction of the block with a height of 10 mm using the traditional method has an average height of 10.018 mm, and a RMSE of 0.043 mm. Similarly, the measurement results of the proposed method show an average height of 10.047 mm, and a standard deviation of 0.072 mm.
The traditional phase-height mapping calibration method and the new phase-height mapping calibration method are respectively used to reconstruct the calibration plane with a height of 10 mm. The comparison results are shown in Tab. 1.
Method | Average height/mm | RMSE/mm |
Traditional | 10.018 | 0.043 |
Proposed | 10.047 | 0.072 |
Table 1. Comparison of the measurement results
Table 1 shows that no matter whether the traditional method or the proposed method is used, the 3D information of the measured object can be effectively obtained, and the measurement accuracy can be guaranteed. However, the table shows that the traditional calibration method is superior to the proposed calibration method in terms of average value, or RMSE, while the proposed method is more convenient and saves more time.
To verify the utility of the method, the measurement data of the sphere shown in Fig. 8, Figure 8(a) shows part of a sphere, whose diameter is 60.027 mm. Figure 8(b) shows a frame deformed fringe of the sphere, and Fig. 8(c) shows a phase distribution of the sphere. Figure 9 shows the 3D reconstruction results of the sphere, Figure 9(a) shows 3D shape by the traditional method. And Fig. 9(b) shows 3D shape by the proposed method, Figure 9 shows that both methods are good at restoring the 3D shape of the object.
Figure 8.Measurement data of the sphere. (a) Measured sphere; (b) The deformed fringe pattern modulated by the sphere; (c) Continuous phase distribution
Figure 9.Reconstruction results of the sphere. (a) 3D shape by the traditional method; (b) 3D shape by the proposed method
To compare the difference between the two methods more clearly, the cutaway view of a column in the green circle of Fig. 9 was extracted from the 3D shape recovered by the two methods, and the comparison result is shown in Fig. 10. The measurement results show that the maximum height of the sphere surface is 60.071 mm obtained by the traditional method and 60.095 mm obtained by the proposed method, respectively. For the traditional method, due to need to move the standard plane several times (starting from the h0 position), the measurement data fluctuates greatly due to the influence of dither and mechanical error. The new method only needs to rotate an angle
Figure 10.The part of cutaway view for a column
In addition, another evaluation experiment is carried out by measuring a sculpture using the proposed method, as illustrated in Fig. 11. Figure 11(a) and 11(b) are the captured deformed pattern and the reconstructed 3D shape, respectively. Obviously, the proposed method can obtain satisfactory 3D shape of the measured object.
Figure 11.Reconstruction results of the sphere. (a) Captured deformed pattern; (b) Reconstructed 3D shape
4 Conclusion
The traditional phase-height mapping calibration method generally uses a moving stage to drive the calibration plate to move several times within the depth of field of the camera, but this method has problems of complicated operation and inconvenient carrying. The proposed calibration method only needs to use a turntable to rotate the calibration plane once, the camera only needs to capture two sets of images, greatly improving the calibration speed of the system, but the measurement accuracy of the proposed calibration method is less than the traditional method.
Comparing these two methods, each has several unique advantages. In some fields, to achieve the registration of 3D point cloud, a structured light system based on a turntable is widely applied. In contrast to traditional method, the proposed method can achieve system calibration without the moving stage, and the error is also within tolerance.
Conflict of interest statement
On behalf of all authors, the corresponding author states that there is no conflict of interest.
References
[1] F Chen, G M Brown, M Song. Overview of 3-D shape measurement using optical methods. Optical Engineering, 39, 10-22(2000).
[2] Yongkai Yin, Zonghua Zhang, Xiaoli Liu, et al. Review of the system model and calibration for fringe projection profilometry. Infrared and Laser Engineering, 49, 0303008(2020).
[3] D Hong, H Lee, M Y Kim, et al. Sensor fusion of phase measuring profilometry and stereo vision for three-dimensional inspection of electronic components assembled on printed circuit boards. Applied Optics, 48, 4158-4169(2009).
[4] Chao Zuo, Xiaolei Zhang, Yan Hu, et al. Has 3D finally come of age?——An introduction to 3D structured-light sensor. Infrared and Laser Engineering, 49, 0303001(2020).
[5] M Takeda, K Mutoh. Fourier transform profilometry for the automatic measurement of 3-D object shapes. Applied Optics, 22, 3977-3982(1983).
[6] S Cao, Y Cao, Q Zhang. Fourier transform profilometry of a single-field fringe for dynamic objects using an interlaced scanning camera. Optics Communications, 367, 130-136(2016).
[7] V Srinivasan, H C Liu, M Halioua. Automated phase-measuring profilometry of 3-D diffuse objects. Applied Optics, 23, 3105-3108(1984).
[8] H Zhou, J Gao, H Hu, et al. Fast phase-measuring profilometry through composite color-coding method. Optics Communications, 440, 220-228(2019).
[9] G Sansoni, L Biancardi, U Minoni, et al. A novel, adaptive system for 3-D optical profilometry using a liquid crystal light projector. IEEE Transactions on Instrumentation and Measurement, 43, 558-566(1994).
[10] H Liu, W Su, K Reichard, et al. Calibration-based phase-shifting projected fringe profilometry for accurate absolute 3D surface profile measurement. Optics Communications, 216, 65-80(2003).
[11] W Zhou, X Su. A direct mapping algorithm for phase-measuring profilometry. Journal of Modern Optics, 41, 89-94(1994).
[12] A Asundi, Z Wensen. Unified calibration technique and its applications in optical triangular profilometry. Applied Optics, 38, 3556-3561(1999).
[13] W Li, X Su, Z Liu. Large-scale three-dimensional object measurement: A practical coordinate mapping and image data-patching method. Applied Optics, 40, 3326-3333(2001).
[14] H Du, Z Wang. Three-dimensional shape measurement with an arbitrarily arranged fringe projection profilometry system. Optics Letters, 32, 2438-2440(2007).
[15] Gai S, Da F. Threedimensional surface measurement system based on projected fringe model[C]3rd International Symposium on Advanced Optical Manufacturing Testing Technologies: Optical Test Measurement Technology Equipment, 2007, 6723: 67231X.
[16] Z Zhang, S Huang, S Meng, et al. A simple, flexible and automatic 3D calibration method for a phase calculation-based fringe projection imaging system. Optics Express, 21, 12218-12227(2013).
[17] I Léandry, C Brèque, V Valle. Calibration of a structured-light projection system: development to large dimension objects. Optics and Lasers in Engineering, 50, 373-379(2012).
[18] P Siegmann, L Felipe-Sese, F Diaz-Garrido. Improved 3D displacement measurements method and calibration of a combined fringe projection and 2D-DIC system. Optics and Lasers in Engineering, 88, 255-264(2017).
[19] A Gonzalez, J Meneses. Accurate calibration method for a fringe projection system by projecting an adaptive fringe pattern. Applied Optics, 58, 4610-4615(2019).
[20] J M Huntley, H O Saldner. Temporal phase-unwrapping algorithm for automated interferogram analysis. Applied Optics, 32, 3047-3052(1993).
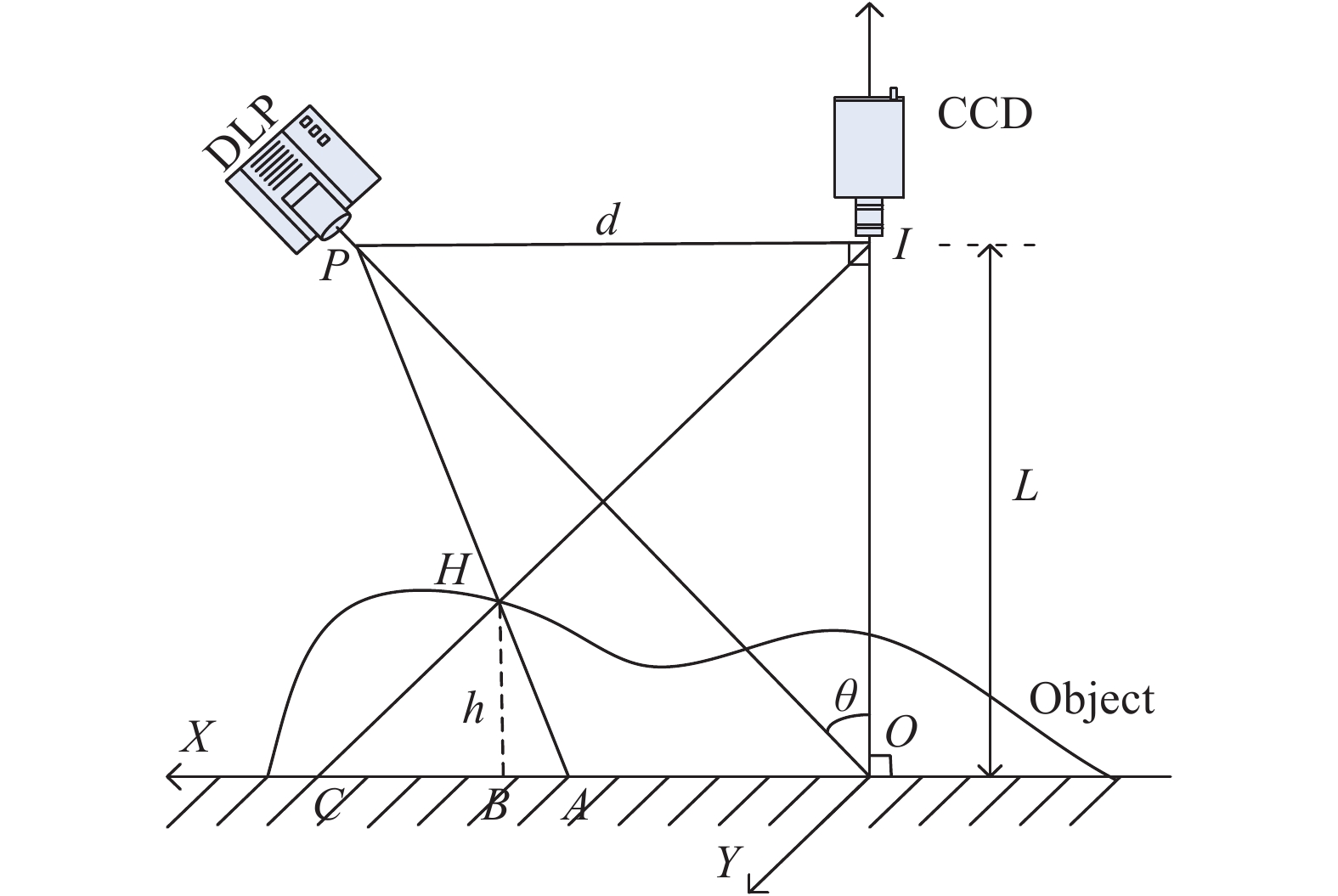
Set citation alerts for the article
Please enter your email address