Jiaxuan Cai, Tuo Shi, Shihong Shi, Rongwei Zhang, Guang Liu, Yu Wang, Rui Zhuang. Research on laser melting deposition forming process and accuracy of thin-walled hollow bending and torsion structural parts with variable cross-section[J]. Infrared and Laser Engineering, 2023, 52(3): 20220436

Search by keywords or author
- Infrared and Laser Engineering
- Vol. 52, Issue 3, 20220436 (2023)

Fig. 1. Principle diagram of hollow ring power feeding in laser

Fig. 2. Physical drawing of powder feeding cladding nozzle in laser
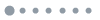
Fig. 3. Geometric model of frame member. (a) Axonometric drawing; (b) Schematic diagram of end face torsion; (c) Bottom end face; (d) Top end face
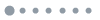
Fig. 4. Schematic diagram of laser melting deposition with different ways. (a) Diagram of horizontal layers; (b) Diagram of normal layers
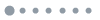
Fig. 5. Method of layering frame members. (a) The structural member is divided into two parts; (b) Getting slice layer; (c) Discreting sedimentary unit
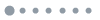
Fig. 6. Transformation process of base coordinate system and tool coordinate system
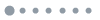
Fig. 7. Schematic diagram of curve motion path fitting of nozzle
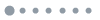
Fig. 8. Schematic diagram of nozzle spot position before compensation. (a) Completing the deposition of the n th layer; (b) Attitude change base point offset
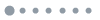
Fig. 9. Schematic diagram of compensation adjustment. (a) Geometric schematic diagram of variable attitude base point offset; (b) Schematic diagram of nozzle spot position after compensation
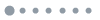
Fig. 10. Schematic diagram of spatial variable angle growth of sedimentary layer. (a) Growth process of sedimentary layer; (b) Completing the deposition of layer n +1
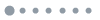
Fig. 11. Forming process. (a) "Laser leakage"; (b) Panorama of forming process; (c) Front view of forming process; (d) Side view of forming process
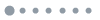
Fig. 12. Physical drawing of formed structural parts
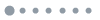
Fig. 13. Comparison diagram of space variable attitude base point offset compensation technology. (a) Not used; (b) Used
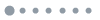
Fig. 14. Schematic diagram of actual dimensions of structural members
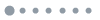
Fig. 15. Actual wall thickness measurement of structural members. (a) Sampling diagram of measuring points; (b) Wall thickness sampled at different locations
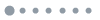
Fig. 16. Microhardness measurement of structural parts. (a) Sampling diagram of measuring points; (b) Microhardness of samples taken at different locations
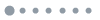
Fig. 17. Microstructure diagram
|
Table 1. Chemical compositions and content of 304 stain-less steel (mass fraction,wt.%)
|
Table 2. Chemical compositions and content of Fe314 alloy powder(mass fraction,wt.%)

Set citation alerts for the article
Please enter your email address