
- Chinese Optics Letters
- Vol. 19, Issue 11, 114001 (2021)
Abstract
1. Introduction
Nowadays, the fascinating thin films for photovoltaic generation are
However, a low-temperature deposition process often produces an inferior device performance due to the poor crystallinity of CIGS films with the absence of the
In this work, we investigate the effects of different Ag treatment processes (the Ag precursor and the Ag surface treatment process) on the material and the corresponding device properties during low-temperature processes. First, the material properties of different Ag treatment processes are investigated. Subsequently, the correlation with device performance, such as short-circuit current density (
Sign up for Chinese Optics Letters TOC. Get the latest issue of Chinese Optics Letters delivered right to you!Sign up now
2. Experimental Methods
2.1. Preparation of CIGS films and solar cells
In this study, the solar cell has a Ni-Al/Al-ZnO/i-ZnO/CdS/CIGS/Mo/SLG structure with the active area of
Figure 1.Sketch diagram of the absorber layer deposition process. The PRE-Ag process is referring to the Ag–Se precursor deposition process, which was prepared before the CIGS deposition process. In addition, the Ag surface treatment process carried out on the surface of CIGS films is denoted as the PDT-Ag process.
In this work, three group samples were prepared to study the characteristics of Ag-doped CIGS films in a low-temperature deposition process. The detailed deposition conditions of different samples are supplied in Table 1. Here, the CIGS sample without any treatment was used as the reference sample. Then, the influence of Ag on CIGS material properties was compared by the samples, A, B, and C. For all samples, the molar ratio of Ga and In + Ga (GGI) is in the range of 0.32–0.33. In addition, the thickness of all films ranges from 2.0 to 2.2 µm.
Sample | PRE-Ag (50 nm) | PDT-Ag (50 nm) |
---|---|---|
A | No | No |
B | Yes | No |
C | No | Yes |
Table 1. Deposition Conditions of Different Samples with Ag
Ag-Treated Sample | ||
---|---|---|
B | 13.5 | 12 |
C | 14.7 | 12 |
Table 2. Statistics of Different CIGS Samples in the Δ
2.2. Characterization
The integral compositions of CIGS films with Ag were determined by X-ray fluorescence spectroscopy (XRF), which was calibrated by inductively coupled plasma (ICP). A scanning electron microscope (SEM) was used to show the cross sections of Ag-treated films. The crystallinities of absorber layers were characterized by a Philips X-pert pro X-ray diffractometer (XRD) with a
3. Result and Discussion
3.1. Independently controlling material properties of CIGS films with Ag
Figure 2(a) shows the XRD patterns of CIGS films to explore the phase transition of Ag-treated CIGS films. Except for the Mo peak (about 40°), all XRD patterns of the three samples (A, B, and C) are consistent with chalcopyrite CIGS phases[
Figure 2.(a) XRD patterns of the CIGS films with Ag. (b) The corresponding grazing incident X-ray diffraction (GIXRD) patterns of absorber layers.
Cross-sectional SEM images of CIGS films are given in Fig. 3. Clearly, the crystallinity of the reference CIGS film, grown in a low-temperature process, is poor in Fig. 3(a). The grain sizes in the upper part of the film are larger than that near the Mo layer owing to the Ga distribution in the absorber layer. For the Ag precursor-treated sample B, its crystallinity is improved obviously, and the fine grain layer near the Mo layer disappears. In addition, the grains in the upper part of sample B also become better. Currently, two possible explanations can be considered for this phenomenon. First, the melting temperature of the whole films is decreased after the incorporation of Ag, which can enhance the recrystallization. In addition, it has been demonstrated that the Cu–Se phases are also observed in the Cu-poor condition during the second stage[
Figure 3.Cross-sectional SEM images of CIGS films of (a) A, (b) B, and (c) C.
3.2. Device performance of Ag-treated CIGS solar cells
The photovoltaic parameters of Ag-treated CIGS films are shown in Fig. 4. It can be observed that the conversion efficiency of Ag-treated CIGS samples increases from 14.0% to 15.1%, mostly because of the enhanced short-circuit current density (
Figure 4.(a) J-V curves of the best CIGS solar cells fabricated from the different absorber samples. Statistic boxes for the (b) VOC, (c) JSC, and (d) FF and each box contains over 10 solar cells.
Figure 5.(a) External quantum efficiency (EQE) spectrum. (b) The band gap value obtained by EQE fitting curve. (c) Doping concentration (Na) of different samples. (d) ln(EQE) as a function of photon energy to determine the Urbach energy (EU) values.
In addition, adding Ag into CIGS films also increases the
From previous work[
Exploring the reason for the slightly improved
Figure 6.Charge barrier height Φb of different samples.
4. Conclusion
In this paper, different Ag treatment processes were utilized to improve the CIGS material properties and the corresponding device performance in a low-temperature process. The incorporation of Ag into CIGS films can not only reduce the melting temperature of the absorber layer but also enhance the element diffusion. Simultaneously, it leads to a lower surface energy and generates a strong (112) preferred orientation. Furthermore, according to the XRD results, we can observe the larger lattice constant of the CIGS films compared with the reference sample, which suggests that the addition of Ag can increase the lattice constant of CIGS films. In contrast to the reference film, the values of
References
[1] M. Nakamura, K. Yamaguchi, Y. Kimoto, Y. Yasaki, T. Kato, H. Sugimoto. Cd-free Cu(In,Ga)(Se,S)2 thin-film solar cell with record efficiency of 23.35%. IEEE J. Photovoltaics, 9, 1863(2019).
[2] Y. Wang, S. Lv, Z. Li. Review on incorporation of alkali elements and their effects in Cu(In,Ga)Se2 solar cells. J. Mater. Sci. Technol., 96, 179(2021).
[3] H. Fan, Y. Mu, C. Liu, Y. Zhu, G. Liu, S. Wang, Y. Li, P. Du. Random lasing of CsPbBr3 perovskite thin films pumped by modulated electron beam. Chin. Opt. Lett., 18, 011403(2020).
[4] P. Liang, C. Chueh, T. S. Williams, K.-Y. Alex. Roles of fullerene-based interlayers in enhancing the performance of organometal perovskite thin-film solar cells. Adv. Energy Mater., 5, 1402321(2015).
[5] Z. Zhang, Z. Lü, X. Yang, H. Chai, L. Meng, T. Yang. 25 Gb/s directly modulated ground-state operation of 1.3 µm InAs/GaAs quantum dot lasers up to 75°C. Chin. Opt. Lett., 18, 071401(2020).
[6] B. S. Tosun, R. Feist, A. Gunawan, K. Mkhoyan, S. A. Campbell, E. Aydil. Improving the damp-heat stability of copper indium gallium diselenide solar cells with a semicrystalline tin dioxide overlayer. Sol. Energy Mater. Sol. Cells, 101, 270(2012).
[7] M. Schmidt, D. Braunger, R. Schäffler, H. W. Schock, U. Rau. Influence of damp heat on the electrical properties of Cu(In,Ga)Se2 solar cells. Thin Solid Films, 361–362, 283(2000).
[8] H. Y. Sun, P. H. Li, Y. M. Xue, Z. X. Qiao, S. Liu. Effect of MoSe2 on the performance of CIGS solar cells. Optoelectron. Lett., 15, 428(2019).
[9] Y. Zhang, S. Lin, Z. Hu, S. Cheng, Z. He, Z. Zhou, W. Liu, Y. Sun. Towards an optimized gallium gradient for Cu(In,Ga)Se2 thin film via an improved constant low-temperature deposition process. Sol. Energy Mater. Sol. Cells, 209, 110425(2020).
[10] P. Jackson, D. Hariskos, R. Wuerz, O. Kiowski, A. Bauer, T. M. Friedlmeier, M. Powalla. Properties of Cu(In,Ga)Se2 solar cells with new record efficiencies up to 21.7%. Rapid Res. Lett., 9, 28(2015).
[11] L. Zhang, Q. He, W. L. Jiang, F. F. Liu, C. J. Li, Y. Sun. Effects of substrate temperature on the structural and electrical properties of Cu(In,Ga)Se2 thin films. Sol. Energy Mater. Sol. Cells, 93, 114(2009).
[12] W. Li, L. Yao, K. Li, X. Li, B. Yang, S. Xu, S. Shi, C. Yi, M. Chen, Y. Feng, W. Li, Z. Lu, C. Yang. Enabling low-temperature deposition of high-efficiency CIGS solar cells with a modified three-stage co-evaporation process. ACS Appl. Energy Mater., 3, 4201(2020).
[13] A. Chirila, D. Guettler, D. Brémaud, S. Buecheler, R. Verma, S. Seyrling, S. Nishiwaki, S. Haenni, G. Bilger, A. N. Tiwari. CIGS solar cells grown by a three-stage process with different evaporation rates. 2009 34th IEEE Photovoltaic Specialists Conference (PVSC), 11152452(2009).
[14] V. Achard, M. Balestrieri, S. Béchu, M. Jubault, M. Bouttemy, L. Lombez, T. Hildebrandt, N. Naghavi, A. Etcheberry, D. Lincot, F. Donsanti. Effect of Ga introduction during the second stage of a coevaporation process of Cu(In,Ga)Se2 layers at low temperature on polyimide substrates. Thin Solid Films, 669, 494(2019).
[15] X. Liang, H. Zhu, J. Chen, D. Zhou, C. Zhang, Y. Guo, X. Niu, Z. Li, Y. Mai. Substrate temperature optimization for Cu(In,Ga)Se2 solar cells on flexible stainless steels. Appl. Surf. Sci., 368, 464(2016).
[16] V. Glazov, A. Pashinkin, V. Fedorov. Phase equilibria in the Cu-Se system, inorganic materials. Inorg. Mater., 36, 641(2000).
[17] W. N. Shafarman, J. Zhu. Effect of substrate temperature and deposition profile on evaporated Cu(InGa)Se2 films and devices. Thin Solid Films, 361–362, 473(2000).
[18] K. Kim, J. W. Park, J. S. Yoo, J.-S. Cho, H.-D. Lee, J. H. Yun. Ag incorporation in low-temperature grown Cu(In,Ga)Se2 solar cells using Ag precursor layers. Sol. Energy Mater. Sol. Cells, 146, 114(2016).
[19] N. Valdes, J. Lee, W. Shafarman. Comparison of Ag and Ga alloying in low bandgap CuInSe2-based solar cells. Sol. Energy Mater. Sol. Cells, 195, 155(2019).
[20] J. Zhai, H. Cao, M. Zhao, C. Wang, Y. Li, H. Tong, Z. Li, S. Yin, D. Zhuang. Smooth and highly-crystalline Ag-doped CIGS films sputtered from quaternary ceramic targets. Ceram. Int., 47, 2288(2021).
[21] Y. Zhao, S. Yuan, D. Kou, Z. Zhou, X. Wang, H. Xiao, Y. Deng, C. Cui, Q. Chang, S. Wu. High efficiency CIGS solar cells by bulk defect passivation through Ag substituting strategy. ACS Appl. Energy Mater., 12, 12717(2020).
[22] T. Adhikari, D. Pathak, T. Wagner, R. Jambor, U. Jabeen, M. Aamir, J. M. Nunzi. Structural, optical, electrochemical and photovoltaic studies of spider web like silver indium diselenide quantum dots synthesized by ligand mediated colloidal sol-gel approach. Opt. Mater., 73, 70(2017).
[23] D. Pathak, R. K. Bedi, D. Kaur. Growth of AgInSe2 on Si(100) substrate by pulse laser ablation. Surf. Rev. Lett., 16, 917(2010).
[24] X. Xu, J. Li, X. Yang, S. Pan, Y. Bi. Introduction of Ag nanoparticles by picosecond LIFT to improve the photoelectric property of AZO films. Chin. Opt. Lett., 18, 043101(2020).
[25] G. Kim, W. M. Kim, J. K. Park, D. Kim, H. Yu, J. H. Jeong. Thin Ag precursor layer-assisted co-evaporation process for low-temperature growth of Cu(In,Ga)Se2 thin film. ACS Appl. Mater. Interfaces, 11, 31923(2019).
[26] Y. Zhang, Z. Hu, S. Lin, C. Wang, S. Cheng, Z. He, Z. Zhou, Y. Sun, W. Liu. Silver surface treatment of Cu(In,Ga)Se2 (CIGS) thin film: a new passivation process for the CdS/CIGS heterojunction. Solar RRL, 4, 2000290(2020).
[27] B. Guo, Y. Wang, X. Zhu, M. Qin, D. Wan, A. F. Huang. Molybdenum thin films fabricated by RF and dc sputtering for Cu(In,Ga)Se2 solar cell applications. Chin. Opt. Lett., 14, 043101(2016).
[28] Z. Wang, D. Wan, F. Huang, F. Xu. Highly surface-textured and conducting ZnO:Al films fabricated from oxygen-deficient target for Cu(In, Ga)Se2 solar cell application. Chin. Opt. Lett., 12, 093101(2014).
[29] S. Lin, W. Liu, Y. Zhang, S. Cheng, Y. Fan, Z. Zhou, Q. He, Y. Zhang, Y. Sun. Adjustment of alkali element incorporations in Cu(In,Ga)Se2 thin films with wet chemistry Mo oxide as a hosting reservoir. Sol. Energy Mater. Sol. Cells, 174, 16(2018).
[30] J. H. Boyle, B. E. McCandless, W. N. Shafarman, R. W. Birkmire. Structural and optical properties of (Ag,Cu)(In,Ga)Se2 polycrystalline thin film alloys. J. Appl. Phys., 115, 223504(2014).
[31] V. Achard, M. Balestrieri, M. Jubault, J. Posada, T. Hildebrandt, N. Naghavi, L. Lombez, D. Lincot, F. Donsanti. Study of Cu(In,Ga)Se2 thin film growth at low temperature on polyimide substrate in a multi-stage coevaporation process for photovoltaic applications. ACS Appl. Energy Mater., 1, 5257(2018).
[32] K. V. Sopiha, J. K. Larsen, O. Donzel-Gargand, F. Khavari, J. Keller, M. Edoff, C. Platzer-Björkman, C. Persson, J. S. Scragg. Phase separation and Ag grading in (Ag,Cu)(In,Ga)Se2 solar absorbers. J. Mater. Chem. A, 8, 8740(2020).
[33] S. Essig, S. Paetel, T. M. Friedlmeier, M. Powalla. Challenges in the deposition of (Ag,Cu)(In,Ga)Se2 absorber layers for thin-film solar cells. J. Phys. Mater., 4, 024003(2021).
[34] Y. Zhang, Z. Hu, S. Lin, S. Cheng, Z. He, C. Wang, Z. Zhou, Y. Sun, W. Liu. Facile silver-incorporated method of tuning the back gradient of Cu(In,Ga)Se2 films. ACS Appl. Energy Mater., 3, 9963(2020).
[35] J. Chantana, T. Nishimura, Y. Kawano, S. Teraji, T. Watanabe, T. Minemoto. Examination of relationship between Urbach energy and open-circuit voltage deficit of flexible Cu(In,Ga)Se2 solar cell for its improved photovoltaic performance. ACS Appl. Energy Mater., 2, 7843(2019).
[36] F. Pianezzi, P. Reinhard, A. Chirilă, S. Nishiwaki, B. Bissig, S. Buecheler, A. N. Tiwari. Defect formation in Cu(In,Ga)Se2 thin films due to the presence of potassium during growth by low temperature co-evaporation process. J. Appl. Phys., 114, 194508(2013).
[37] Y. Zhang, S. Lin, S. Cheng, Z. He, Z. Hu, Z. Zhou, W. Liu, Y. Sun. Boosting Cu(In,Ga)Se2 thin film growth in low-temperature rapid-deposition processes: an improved design for the single-heating knudsen cell. Engineering, 7, 534(2020).
[38] X. Zhang, M. Kobayashi, A. Yamada. Comparison of Ag(In,Ga)Se2/Mo and Cu(In,Ga)Se2/Mo interfaces in solar cells. ACS Appl. Mater. Interfaces, 9, 16215(2017).
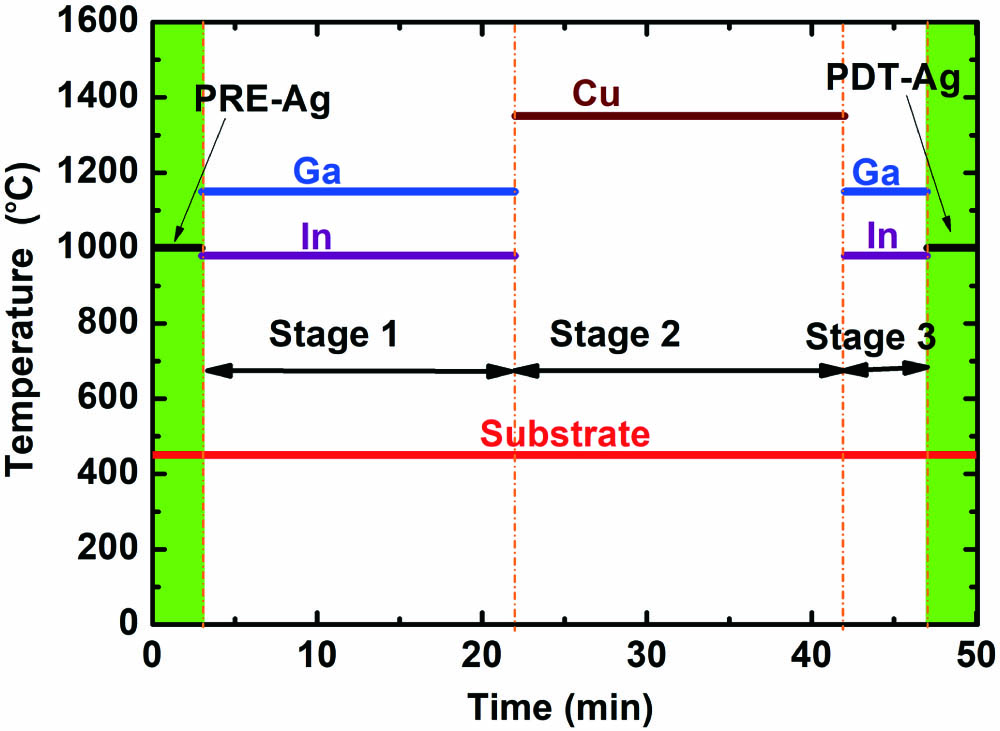
Set citation alerts for the article
Please enter your email address