Jintian Lin, Fang Bo, Ya Cheng, Jingjun Xu, "Advances in on-chip photonic devices based on lithium niobate on insulator," Photonics Res. 8, 1910 (2020)

Search by keywords or author
- Photonics Research
- Vol. 8, Issue 12, 1910 (2020)
![(a) LNOI microring fabricated by Ar ion milling [30]. (b) Scanning electron microscope (SEM) image of the cross section of the ridge waveguide showing relatively rough surface and sidewall. (c) Optical microscope image of a ridge waveguide fabricated by FIB [24]. Inset: SEM image of the cross section of the ridge waveguide showing a rough surface. (d) SEM image of the PhC microcavity fabricated by FIB [104].](/richHtml/prj/2020/8/12/12001910/img_001.jpg)
Fig. 1. (a) LNOI microring fabricated by Ar ion milling [30]. (b) Scanning electron microscope (SEM) image of the cross section of the ridge waveguide showing relatively rough surface and sidewall. (c) Optical microscope image of a ridge waveguide fabricated by FIB [24]. Inset: SEM image of the cross section of the ridge waveguide showing a rough surface. (d) SEM image of the PhC microcavity fabricated by FIB [104].
![Microresonators fabricated by femtosecond laser ablation and FIB polishing: (a) schematic illustration of the process flow of the fabrication [35,39]; (b) SEM image of a single microdisk with Q of 9.61×106 [51] showing smooth sidewall and surface; (c) SEM image of a coupled double-microdisk with 123 nm gap [109]; and (d) enlarged SEM image of the coupled region coated with platinum (Pt) for imaging.](/richHtml/prj/2020/8/12/12001910/img_002.jpg)
Fig. 2. Microresonators fabricated by femtosecond laser ablation and FIB polishing: (a) schematic illustration of the process flow of the fabrication [35,39]; (b) SEM image of a single microdisk with Q of 9.61 × 10 6 [51] showing smooth sidewall and surface; (c) SEM image of a coupled double-microdisk with 123 nm gap [109]; and (d) enlarged SEM image of the coupled region coated with platinum (Pt) for imaging.
![Microresonator fabricated by UV lithography and Ar ion milling [37]: (a) schematic illustration of the process flow of fabrication; and (b), (c) SEM images of the microdisk showing smooth sidewall and surface.](/Images/icon/loading.gif)
Fig. 3. Microresonator fabricated by UV lithography and Ar ion milling [37]: (a) schematic illustration of the process flow of fabrication; and (b), (c) SEM images of the microdisk showing smooth sidewall and surface.
![Microring fabricated by UV lithography and RIE, followed by sidewall polishing by the CMP [100]: (a) schematic illustration of the process flow of fabrication; (b) false-color SEM image of the microring; and enlarged SEM image of the sidewall (c) before and (d) after the CMP.](/Images/icon/loading.gif)
Fig. 4. Microring fabricated by UV lithography and RIE, followed by sidewall polishing by the CMP [100]: (a) schematic illustration of the process flow of fabrication; (b) false-color SEM image of the microring; and enlarged SEM image of the sidewall (c) before and (d) after the CMP.
![(a)–(e) Schematic diagram of the fabrication process with PLACE [33]. (f) Camera photo, (g) optical microscope image, and (h) enlarged image of the fabricated 11-cm-long ridge waveguide with 0.027 dB/cm propagation loss [33]. (i) Microdisk with a Q factor of 4.7×107 [31].](/Images/icon/loading.gif)
Fig. 5. (a)–(e) Schematic diagram of the fabrication process with PLACE [33]. (f) Camera photo, (g) optical microscope image, and (h) enlarged image of the fabricated 11-cm-long ridge waveguide with 0.027 dB/cm propagation loss [33]. (i) Microdisk with a Q factor of 4.7 × 10 7 [31].
![(a) Ring resonator fabricated by ultra-precision cutting and (b) magnified image of (a) [139]. (c) Ridge waveguide fabricated by optical grade dicing [133]. (d) Disk resonator with a diameter of 3 mm fabricated by diamond polishing [108].](/Images/icon/loading.gif)
Fig. 6. (a) Ring resonator fabricated by ultra-precision cutting and (b) magnified image of (a) [139]. (c) Ridge waveguide fabricated by optical grade dicing [133]. (d) Disk resonator with a diameter of 3 mm fabricated by diamond polishing [108].
![Hybrid SiN ridge waveguide on the LNOI [146]. (a) Schematic cross section. (b) SEM image of the cross section. (c), (d) Simulated fundamental transverse electric (TE) mode profiles of the waveguide at 775 and 1550 nm, respectively. Hybrid silicon ridge waveguide on the LNOI [153]. (e) SEM image of the cross section of the Si–LN modulator. (f) Optical micrograph of the Y-junction and modulator electrodes.](/Images/icon/loading.gif)
Fig. 7. Hybrid SiN ridge waveguide on the LNOI [146]. (a) Schematic cross section. (b) SEM image of the cross section. (c), (d) Simulated fundamental transverse electric (TE) mode profiles of the waveguide at 775 and 1550 nm, respectively. Hybrid silicon ridge waveguide on the LNOI [153]. (e) SEM image of the cross section of the Si–LN modulator. (f) Optical micrograph of the Y-junction and modulator electrodes.
![(a) Schematic diagram of the ion slicing thin film from pre-poled LN [130]. Inset: PPLN thin film. Schematic diagrams of the PPLN thin film fabricated by (b) atomic force microscope/piezoelectric force microscopy (AFM/PFM) poling method [164] and (c) microelectrode poling method [148] with a high-voltage (HV) direct-current (DC) source. PFM images of (d) logo of Nankai University and (e) PPLN strips with period of 200 nm width and a duty ratio of 50% [166]. (f) SEM image of a PPLN microring with EBL poling [113]. (g) Second-harmonic confocal microscopy of the PPLN thin film fabricated by microelectrode poling [54].](/Images/icon/loading.gif)
Fig. 8. (a) Schematic diagram of the ion slicing thin film from pre-poled LN [130]. Inset: PPLN thin film. Schematic diagrams of the PPLN thin film fabricated by (b) atomic force microscope/piezoelectric force microscopy (AFM/PFM) poling method [164] and (c) microelectrode poling method [148] with a high-voltage (HV) direct-current (DC) source. PFM images of (d) logo of Nankai University and (e) PPLN strips with period of 200 nm width and a duty ratio of 50% [166]. (f) SEM image of a PPLN microring with EBL poling [113]. (g) Second-harmonic confocal microscopy of the PPLN thin film fabricated by microelectrode poling [54].
![Electro-optically tunable microresonator. (a) Resonant frequency shift with external voltage [37] showing (b) effective efficiency of 3.0 GHz/V. (c) Microdisk integrated with microelectrodes with a tuning efficiency of 3.41 pm/V [199]. (d)–(f) Microdisk integrated with compact out-of-plane microelectrodes with 1 μm gap showing a high efficiency of 29.2 pm/V [202].](/Images/icon/loading.gif)
Fig. 9. Electro-optically tunable microresonator. (a) Resonant frequency shift with external voltage [37] showing (b) effective efficiency of 3.0 GHz/V. (c) Microdisk integrated with microelectrodes with a tuning efficiency of 3.41 pm/V [199]. (d)–(f) Microdisk integrated with compact out-of-plane microelectrodes with 1 μm gap showing a high efficiency of 29.2 pm/V [202].
![(a) Micrograph of the electro-modulator chip consisting of three MZI modulators. Inset: cross-sectional schematic of the modulator. (b) Data-transmission experiments at 70 Gbit/s rate in the modulator driven by (c) CMOS circuit. Measured constellation diagrams obtained with a coherent receiver (left) and reconstructed eye diagrams (right) at peak-to-peak voltages of (d) 200 mV and (e) 60 mV [44].](/Images/icon/loading.gif)
Fig. 10. (a) Micrograph of the electro-modulator chip consisting of three MZI modulators. Inset: cross-sectional schematic of the modulator. (b) Data-transmission experiments at 70 Gbit/s rate in the modulator driven by (c) CMOS circuit. Measured constellation diagrams obtained with a coherent receiver (left) and reconstructed eye diagrams (right) at peak-to-peak voltages of (d) 200 mV and (e) 60 mV [44].
![(a) Schematic of a Si–LN hybrid modulator. (b) Cross section of the Si–LN hybrid waveguide. SEM images of (c) cross section of the LN ridge waveguide and (d) electrodes and the LN waveguide. (e) Schematic of the VAC. (f) SEM images of the cross sections of the VAC at different positions (A, B, and C) and calculated TE mode distributions. Normalized transmission of the devices with (g) 3 mm and (h) 5 mm lengths as a function of the applied voltage showing half-wave voltages of 7.4 V and 5.1 V, respectively. Inset: measured extinction ratio on a logarithmic scale. (i) Optical eye diagrams for the OOK signal at data rates of 100 Gbit/s [71].](/Images/icon/loading.gif)
Fig. 11. (a) Schematic of a Si–LN hybrid modulator. (b) Cross section of the Si–LN hybrid waveguide. SEM images of (c) cross section of the LN ridge waveguide and (d) electrodes and the LN waveguide. (e) Schematic of the VAC. (f) SEM images of the cross sections of the VAC at different positions (A, B, and C) and calculated TE mode distributions. Normalized transmission of the devices with (g) 3 mm and (h) 5 mm lengths as a function of the applied voltage showing half-wave voltages of 7.4 V and 5.1 V, respectively. Inset: measured extinction ratio on a logarithmic scale. (i) Optical eye diagrams for the OOK signal at data rates of 100 Gbit/s [71].
![Large-scale beam splitter [102]. (a) Schematic of the multifunctional beam splitter. (b) Photo image of the photonic chip. (c) Optical micrograph of the region in the red dashed box in (a). (d) SEM image of the region in the red dashed box in (c) before electrode fabrication. (e) Schematic of the 1×6 switch. Normalized output power switching from input ports (f) 1 and (g) 2 to output ports 1 to 6.](/Images/icon/loading.gif)
Fig. 12. Large-scale beam splitter [102]. (a) Schematic of the multifunctional beam splitter. (b) Photo image of the photonic chip. (c) Optical micrograph of the region in the red dashed box in (a). (d) SEM image of the region in the red dashed box in (c) before electrode fabrication. (e) Schematic of the 1 × 6 switch. Normalized output power switching from input ports (f) 1 and (g) 2 to output ports 1 to 6.
![Electro-optic tunable interleaver [213]. (a) Schematic of the reconfigurable 1×4 electro-optic tunable interleaver in an X-cut LN thin film. Measured wavelength switching ports 1−i and i−1 of the interleaver for (b) TE- and (c) TM-polarized input light.](/Images/icon/loading.gif)
Fig. 13. Electro-optic tunable interleaver [213]. (a) Schematic of the reconfigurable 1 × 4 electro-optic tunable interleaver in an X-cut LN thin film. Measured wavelength switching ports 1 − i and i − 1 of the interleaver for (b) TE- and (c) TM-polarized input light.
![SHG and cascaded THG based on the NQPM using d33 in an X-cut LN microdisk [51]. (a) Schematic of the NQPM. (b) SEM image of the X-cut microdisk. (c) deff at every azimuth angle θ. (d) Left: phase mismatching Δk; and right: positive Fourier components of deff. (e) Conversion efficiency as a function of the pump power. Inset: optical micrograph of SHG from the top surface of the microdisk. (f) Power of the THG as a function of the cubic power of the pump power. Inset: optical micrograph of THG.](/Images/icon/loading.gif)
Fig. 14. SHG and cascaded THG based on the NQPM using d 33 in an X-cut LN microdisk [51]. (a) Schematic of the NQPM. (b) SEM image of the X-cut microdisk. (c) d eff at every azimuth angle θ . (d) Left: phase mismatching Δ k ; and right: positive Fourier components of d eff . (e) Conversion efficiency as a function of the pump power. Inset: optical micrograph of SHG from the top surface of the microdisk. (f) Power of the THG as a function of the cubic power of the pump power. Inset: optical micrograph of THG.
![Soliton frequency comb generating a microring [58]. (a) SEM image of the microring. (b) Cross-sectional schematic of mode. (c) Group-velocity dispersion. (d) Soliton comb.](/Images/icon/loading.gif)
Fig. 15. Soliton frequency comb generating a microring [58]. (a) SEM image of the microring. (b) Cross-sectional schematic of mode. (c) Group-velocity dispersion. (d) Soliton comb.
![Electro-optically tunable Raman-assisted frequency comb [250]. (a) SEM image of the microdisk integrated with Cr electrodes (black region). (b) Stokes and anti-Stokes Raman scatterings when pumping at 1552.39 nm wavelength before comb generation. (c) Raman-assisted FWM when pumping at 1552.68 nm wavelength. Comb generation with the spectral space of (d) double FSR of 7.2 nm and (e) single FSR of 3.6 nm when pumping at 1552.72 nm and 1552.74 nm wavelengths, respectively. (f) Electro-optic shifter of the comb line.](/Images/icon/loading.gif)
Fig. 16. Electro-optically tunable Raman-assisted frequency comb [250]. (a) SEM image of the microdisk integrated with Cr electrodes (black region). (b) Stokes and anti-Stokes Raman scatterings when pumping at 1552.39 nm wavelength before comb generation. (c) Raman-assisted FWM when pumping at 1552.68 nm wavelength. Comb generation with the spectral space of (d) double FSR of 7.2 nm and (e) single FSR of 3.6 nm when pumping at 1552.72 nm and 1552.74 nm wavelengths, respectively. (f) Electro-optic shifter of the comb line.
![χ(2) frequency comb observed at (a) degenerate and (b) nondegenerate wavelengths [59]. (c) Micrograph of an electro-optically tunable microring for the electro-optic comb and (d) measured output spectrum of the comb [62].](/Images/icon/loading.gif)
Fig. 17. χ ( 2 ) frequency comb observed at (a) degenerate and (b) nondegenerate wavelengths [59]. (c) Micrograph of an electro-optically tunable microring for the electro-optic comb and (d) measured output spectrum of the comb [62].
![(a) SCG spectra at different pump pulse energies in the thin-film PPLN waveguide. (b) Camera photo of SCG [174]. (c) Single-sideband phase noise of fceo for free-running (red) and locked conditions (blue) showing a large reduction in the phase noise (>100 dB/Hz at 10 Hz) for a locked operation [259].](/Images/icon/loading.gif)
Fig. 18. (a) SCG spectra at different pump pulse energies in the thin-film PPLN waveguide. (b) Camera photo of SCG [174]. (c) Single-sideband phase noise of f ceo for free-running (red) and locked conditions (blue) showing a large reduction in the phase noise (> 100 dB / Hz at 10 Hz) for a locked operation [259].
![Er ion-doped microring [261]: (a) schematic of the cross section of an Er ion-doped microring and fundamental TE mode; (b) non-resonant fluorescence measured at room temperature when pumping at 1480 nm, showing a small peak near 1532 nm due to the Er3+ fluorescence; and (c) Tm3+ ion-doped ridge waveguide [262] and broadband transmission spectrum filtered down to 10 nm through the waveguide with the electric field polarized perpendicular to the optical axis. Inset: SEM image of the waveguide with a grating coupler having 0.1% coupling efficiency.](/Images/icon/loading.gif)
Fig. 19. Er ion-doped microring [261]: (a) schematic of the cross section of an Er ion-doped microring and fundamental TE mode; (b) non-resonant fluorescence measured at room temperature when pumping at 1480 nm, showing a small peak near 1532 nm due to the Er 3 + fluorescence; and (c) Tm 3 + ion-doped ridge waveguide [262] and broadband transmission spectrum filtered down to 10 nm through the waveguide with the electric field polarized perpendicular to the optical axis. Inset: SEM image of the waveguide with a grating coupler having 0.1% coupling efficiency.
![(a) Grating coupler [261]. (b) LN inverse taper covered with an SU8 waveguide for the edge coupler [272]. (c) Bilayer inverse taper for the edge coupler [273] and (d) mode field conversion in space. (e) Fiber taper coupled with ridge waveguide [274]. Inset: SEM image of the cross section of the ridge waveguide. (f) SEM image of the fiber taper with 1.4 μm diameter and TE mode field distributions of the fiber taper (upper inset) and ridge waveguide (lower inset).](/Images/icon/loading.gif)
Fig. 20. (a) Grating coupler [261]. (b) LN inverse taper covered with an SU8 waveguide for the edge coupler [272]. (c) Bilayer inverse taper for the edge coupler [273] and (d) mode field conversion in space. (e) Fiber taper coupled with ridge waveguide [274]. Inset: SEM image of the cross section of the ridge waveguide. (f) SEM image of the fiber taper with 1.4 μm diameter and TE mode field distributions of the fiber taper (upper inset) and ridge waveguide (lower inset).
![Delay line based on the LNOI [32,182]. (a) Illustration of the optical true delay lines (OTDLs) layout. (b) Camera image of the two delay lines on a 3-cm-long chip. (b) Enlarged SEM image of the spiral waveguide. (c) On-chip insertion loss as a function of length of the electro-optically switchable OTDL. (d) Time delay when the signal transmits from the shortest waveguide and the two cascaded OTDLs.](/Images/icon/loading.gif)
Fig. 21. Delay line based on the LNOI [32,182]. (a) Illustration of the optical true delay lines (OTDLs) layout. (b) Camera image of the two delay lines on a 3-cm-long chip. (b) Enlarged SEM image of the spiral waveguide. (c) On-chip insertion loss as a function of length of the electro-optically switchable OTDL. (d) Time delay when the signal transmits from the shortest waveguide and the two cascaded OTDLs.
![Mode (de)multiplexer [65]. (a) Illustration of the (de)multiplexer, including four input ports and four output ports. (b) Fabricated device on the hybrid LNOI. (c) Four-channel TM mode (de)multiplexing at a 40 Gbit/s channel.](/Images/icon/loading.gif)
Fig. 22. Mode (de)multiplexer [65]. (a) Illustration of the (de)multiplexer, including four input ports and four output ports. (b) Fabricated device on the hybrid LNOI. (c) Four-channel TM mode (de)multiplexing at a 40 Gbit/s channel.
![(a) Schematic diagram of the ridge waveguide on the periodically poled LNOI for the electro-optically controlled TE/TM polarization. (b) Output power from the ridge waveguide after the polarizer as a function of the applied power. (c) Polarization state evolution represented on a Poincaré sphere with the applied voltage varying from 0 to 18 V when the input light wavelength is 1595 nm (red curve) or 1550 nm (blue curve) [137].](/Images/icon/loading.gif)
Fig. 23. (a) Schematic diagram of the ridge waveguide on the periodically poled LNOI for the electro-optically controlled TE/TM polarization. (b) Output power from the ridge waveguide after the polarizer as a function of the applied power. (c) Polarization state evolution represented on a Poincaré sphere with the applied voltage varying from 0 to 18 V when the input light wavelength is 1595 nm (red curve) or 1550 nm (blue curve) [137].
![Electro-optic spectrometer [63]. (a) Optical micrograph of the LN‐Si3N4 waveguide device integrated with gold electrodes. The array of EFSs labeled in the black dashed rectangle was used to sample the intensity. (b) SEM image of the ridge waveguide. (c) Cross-sectional schematic of the waveguide–electrode configuration showing the fundamental TE mode and the applied electric field distribution (blue arrows). (d) SEM image of four platinum EFSs on top of the waveguide. (e), (f) Images of the under-sampled interferogram shift at 1550 nm with a changing voltage. (g) Reconstructed spectra for measurements at 1550 nm and 1040 nm. (h) Reconstructed Fourier transform spectrum when inputting dual wavelength of 1480 nm and 1550 nm.](/Images/icon/loading.gif)
Fig. 24. Electro-optic spectrometer [63]. (a) Optical micrograph of the LN ‐ Si 3 N 4 waveguide device integrated with gold electrodes. The array of EFSs labeled in the black dashed rectangle was used to sample the intensity. (b) SEM image of the ridge waveguide. (c) Cross-sectional schematic of the waveguide–electrode configuration showing the fundamental TE mode and the applied electric field distribution (blue arrows). (d) SEM image of four platinum EFSs on top of the waveguide. (e), (f) Images of the under-sampled interferogram shift at 1550 nm with a changing voltage. (g) Reconstructed spectra for measurements at 1550 nm and 1040 nm. (h) Reconstructed Fourier transform spectrum when inputting dual wavelength of 1480 nm and 1550 nm.
|
Table 1. Propagation Losses of Waveguides Fabricated with Different Techniques (SM, single mode)
|
Table 2. Loaded Factors of WGM Microresonators and PhC Cavities
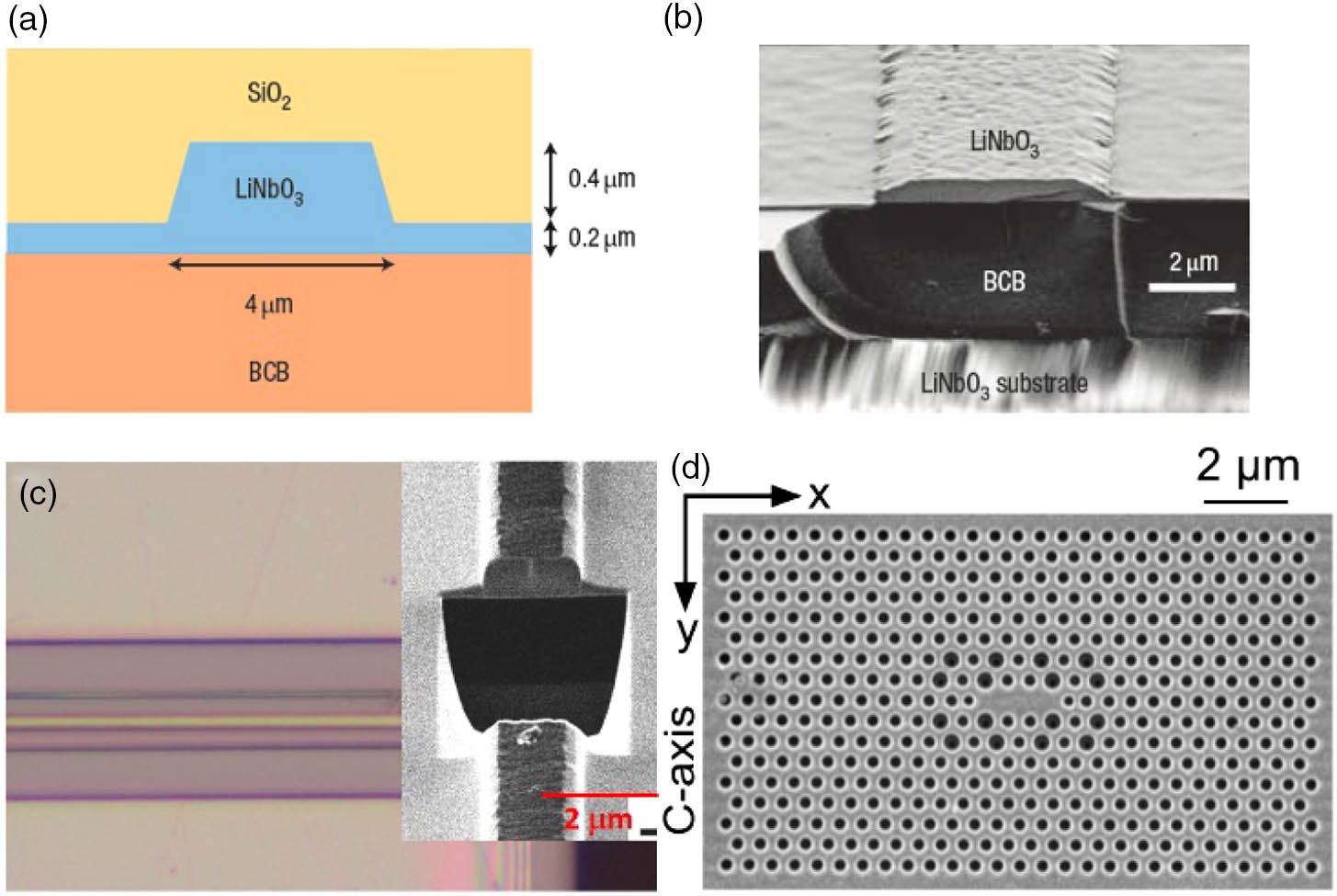
Set citation alerts for the article
Please enter your email address