Xiaming Chen, Xiaonan Wang, Qipeng Dong, Zhen Zhu, Nagaumi Hiromi. Effect of Filling Material with Different Si Content on Microstructure and Properties of Laser-CMT Aluminum Alloy Joints[J]. Chinese Journal of Lasers, 2021, 48(22): 2202003

Search by keywords or author
- Chinese Journal of Lasers
- Vol. 48, Issue 22, 2202003 (2021)
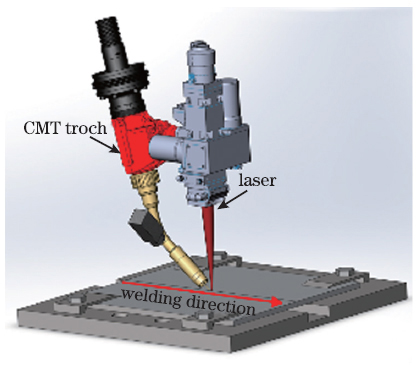
Fig. 1. Schematic of laser-CMT welding

Fig. 2. Microstructure and grain morphologies of weld center. (a)(c) Al-Si5; (b)(d) Al-Si10
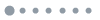
Fig. 3. Grain size and thermal conductivity of weld seam. (a) Grain size; (b) thermal conductivity
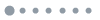
Fig. 4. KAM maps and KAM distribution of weld seam. (a) Al-Si5; (b) Al-Si10; (c) KAM distribution
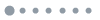
Fig. 5. Mircrohardness distribution of welded joints and comparison between microhardness of weld seams. (a) Microhardness distribution of welded joints; (b) comparison between microhardness of weld seams
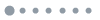
Fig. 6. Macroscopic morphology of welded joint and stress-strain curve. (a) Macroscopic morphology; (b) engineering stress-strain curve; (c) fracture morphology
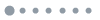
Fig. 7. Yield strength and its increment of the two welds
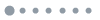
Fig. 8. Droplet transfer and keyhole morphology. (a) Current waveform; (b) stage B amplification; (c) droplet transfer and keyhole morphology
|
Table 1. Mass fraction of chemical compositions of base metal and filling materials unit: %
|
Table 2. Element mass fraction of EDS analysis of weld microstructure unit: %
|
Table 3. Mass fraction of chemical composition of weld seam with different filling materials unit: %
|
Table 4. KAM and dislocation density of both welds
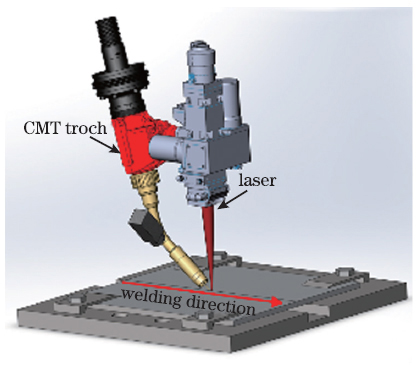
Set citation alerts for the article
Please enter your email address