Zhao Zhang, Maomao Cui, Xiao Wang, Wenkai Shen, Tao Wang, Huixia Liu. Parameter Modeling and Optimization of Laser Stereolithography Process for Alumina Ceramics[J]. Laser & Optoelectronics Progress, 2024, 61(21): 2114005

Search by keywords or author
- Laser & Optoelectronics Progress
- Vol. 61, Issue 21, 2114005 (2024)

Fig. 1. Morphology of alumina powder, rheological properties curve of ceramic slurry and particle size distribution of Al2O3 powder with different particle sizes. (a) SEM image of Al2O3 particle; (b) rheological properties curve of ceramic slurry; (c) particle size distribution of 5 μm Al2O3 powder; (d) particle size distribution of 2 μm Al2O3 powder

Fig. 2. SLA ceramic forming equipment and laser scanning stereolithography process. (a) Schematic diagram of SLA ceramic forming equipment; (b) schematic diagram of laser scanning stereolithography ceramic slurry curing principle; (c) schematic diagram of stereolithography ceramic green body forming principle
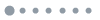
Fig. 3. Cross-sectional morphology of bending specimens of stereolithography alumina ceramics in green, degreased and sintered bodies. (a) Cross-sectional morphology of green bodies; (b) cross-sectional morphology of sintered bodies; (c) cross-sectional morphology of degreased body; (d) localized enlargement diagram of cross-section morphology of degreased body
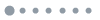
Fig. 4. Residual analysis results. (a) Comparation of actual value with predicted value of flexural strength; (b) normal distribution of standardized residuals; (c) comparation of standardized residual with predicted value
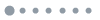
Fig. 5. Influence curve of each process parameter on flexural strength of bending specimens
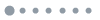
Fig. 6. Response surface plot of the interaction between process parameters. (a) Interaction of scanning speed and scanning spacing (AB); (b) interaction of scanning speed and slice thickness (AC); (c) interaction of scanning speed and laser power (AD); (d) interaction of scanning spacing and slice thickness (BC); (e) interaction of scanning spacing and laser power (BD); (f) interaction of slice thickness and laser power (CD)
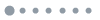
Fig. 7. Contour plot of the interaction between process parameters. (a) Interaction of scanning speed and scanning spacing (AB); (b) interaction of scanning speed and slice thickness (AC); (c) interaction of scanning speed and laser power (AD); (d) interaction of scanning spacing and slice thickness (BC); (e) interaction of scanning spacing and laser power (BD); (f) interaction of slice thickness and laser power (CD)
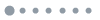
Fig. 8. Schematic diagram of overcuring of cured layer inside specimen by subsequent irradiation and changes in layer spacing between adjacent layers. (a) Overcuring induced by high exposure energy; (b) overcuring induced by low exposure energy; (c) variation of layer spacing between adjacent layers within specimen
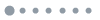
Fig. 9. Cross-section of bending specimen at different stages of ceramic stereolithography process. (a) Delamination in bending specimens made at a scanning speed of 3000 mm/s; (b) delamination in bending specimens made at a hatching spacing of 0.14 mm; (c) bending specimens made at a scanning speed of 3000 mm/s produce laminar gaps at debinding stage; (d) bending specimens made at a hatching spacing of 0.14 mm produce laminar gaps at debinding stage; (e) (f) crack defects within sintered body of a bending specimens
|
Table 1. Experimental factors and levels
|
Table 2. Box-Behnken experimental design scheme and results
|
Table 3. Analysis of variance
|
Table 4. Optimization criteria and weights
|
Table 5. Validation of optimization results

Set citation alerts for the article
Please enter your email address