Shoujin Zeng, Qirui Wu, Jianhua Ye. Mechanical properties of 316L stainless steel porous structure formed by selective laser melting[J]. Infrared and Laser Engineering, 2020, 49(8): 20190523

Search by keywords or author
- Infrared and Laser Engineering
- Vol. 49, Issue 8, 20190523 (2020)
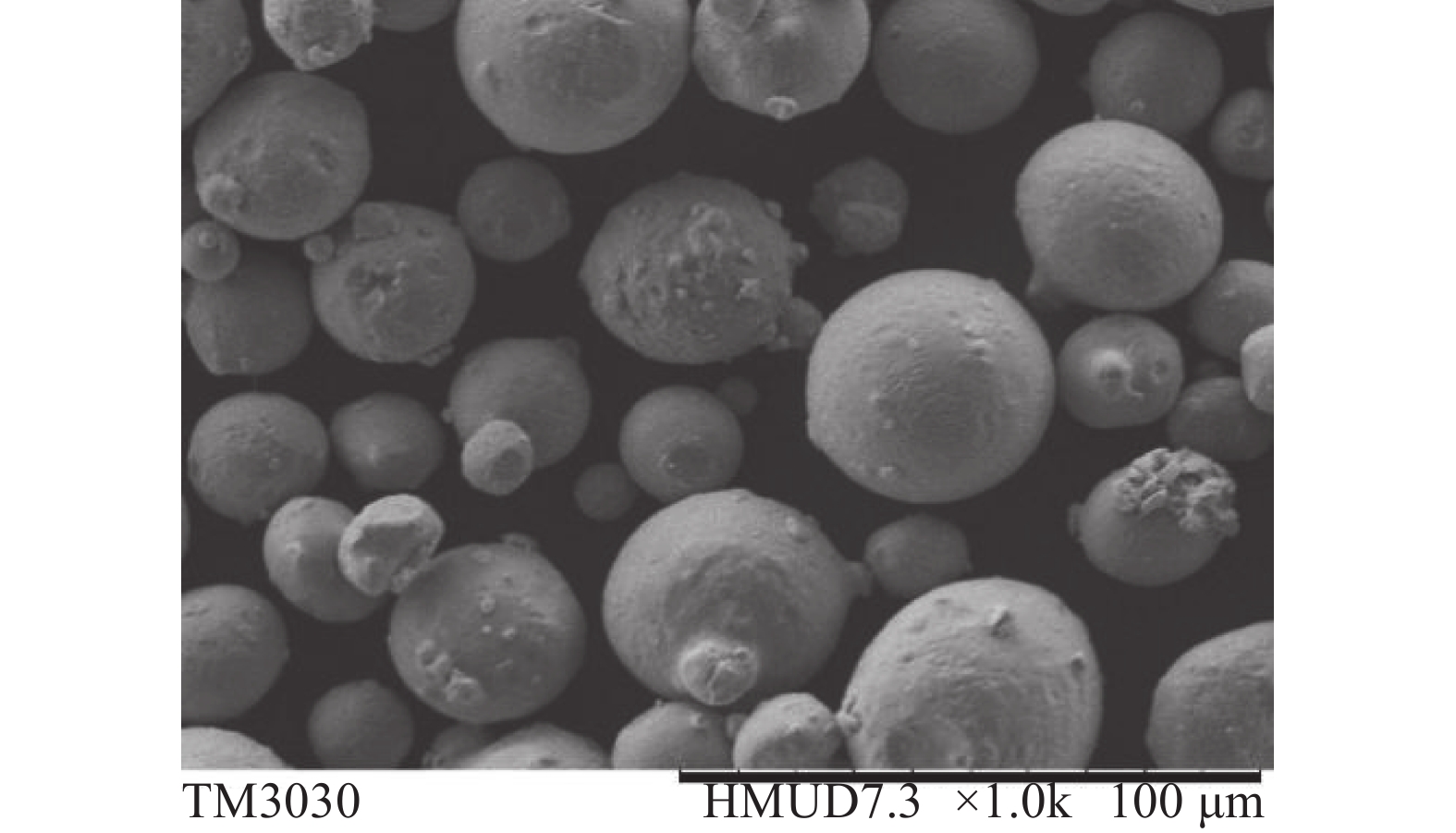
Fig. 1. 316L stainless steel powder particles
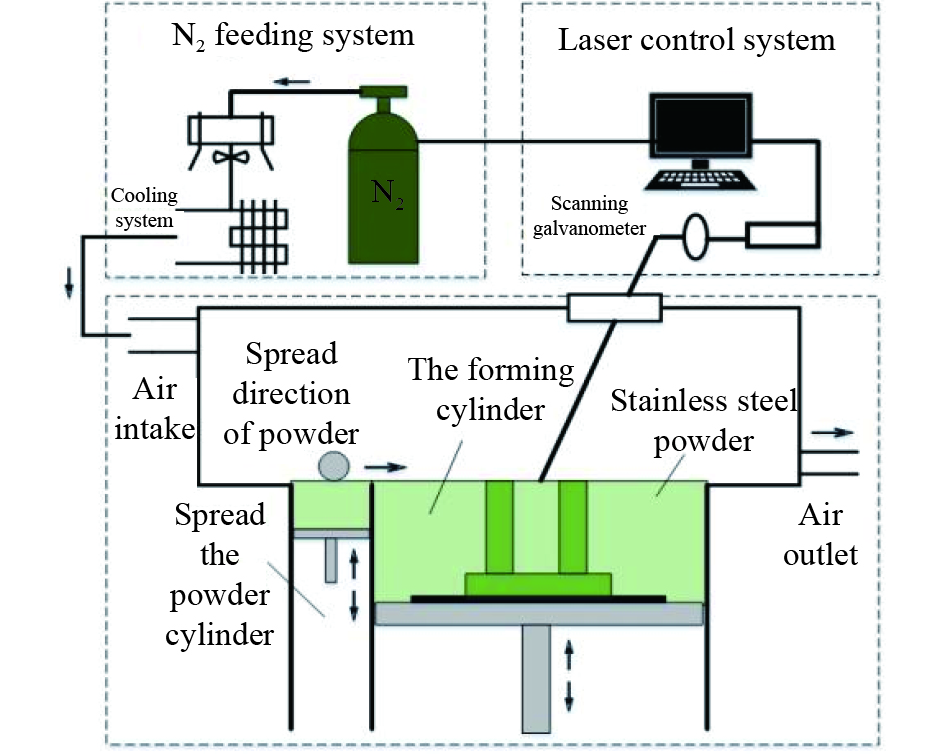
Fig. 2. Selective laser melting system
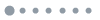
Fig. 3. Porous unit. (a) Regular dodecahedron unit; (b) Body centered cubic structural unit
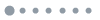
Fig. 4. Porous samples. (a) Regular dodecahedron sample; (b) Body centered cubic sample
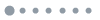
Fig. 5. SLM shaped porous structure sample. (a) Regular dodecahedron porous structure; (b) Body centered cubic porous structure
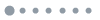
Fig. 6. Microscopic features of SLM formed porous structure. (a) Regular dodecahedron porous structure; (b) Body centered cubic porous structure
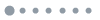
Fig. 7. Compression stress and strain curves of porous 316L stainless steel. (a) Regular dodecahedron porous structure; (b) Body centered cubic porous structure
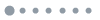
Fig. 8. (a) Relationship between porosity and elastic modulus; (b) Relationship between porosity and compressive strength (RD: porous structure of regular dodecahedron; BCC: body centered cubic porous structure)
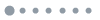
Fig. 9. (a) Relation between average pore diameter and elastic modulus; (b) Relation between average pore diameter and compressive strength (RD: porous structure of regular dodecahedron; BCC: body centered cubic porous structure)
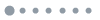
Fig. 10. (a) Relationship between volume to area ratio and elastic modulus ; (b) Relationship between volume to area ratio and compressive strength
|
Table 1.
Chemical composition of 316L stainless power (wt.%)
316L不锈钢粉末化学成分(质量分数%)
|
Table 2.
Technological parameter
工艺参数
|
Table 3.
Parameter design of porous element
多孔单元参数设计
|
Table 4.
Compressive strength calculated by compression test
压缩试验计算的抗压强度
|
Table 5.
Elastic modulus calculated by compression test
压缩试验计算的弹性模量
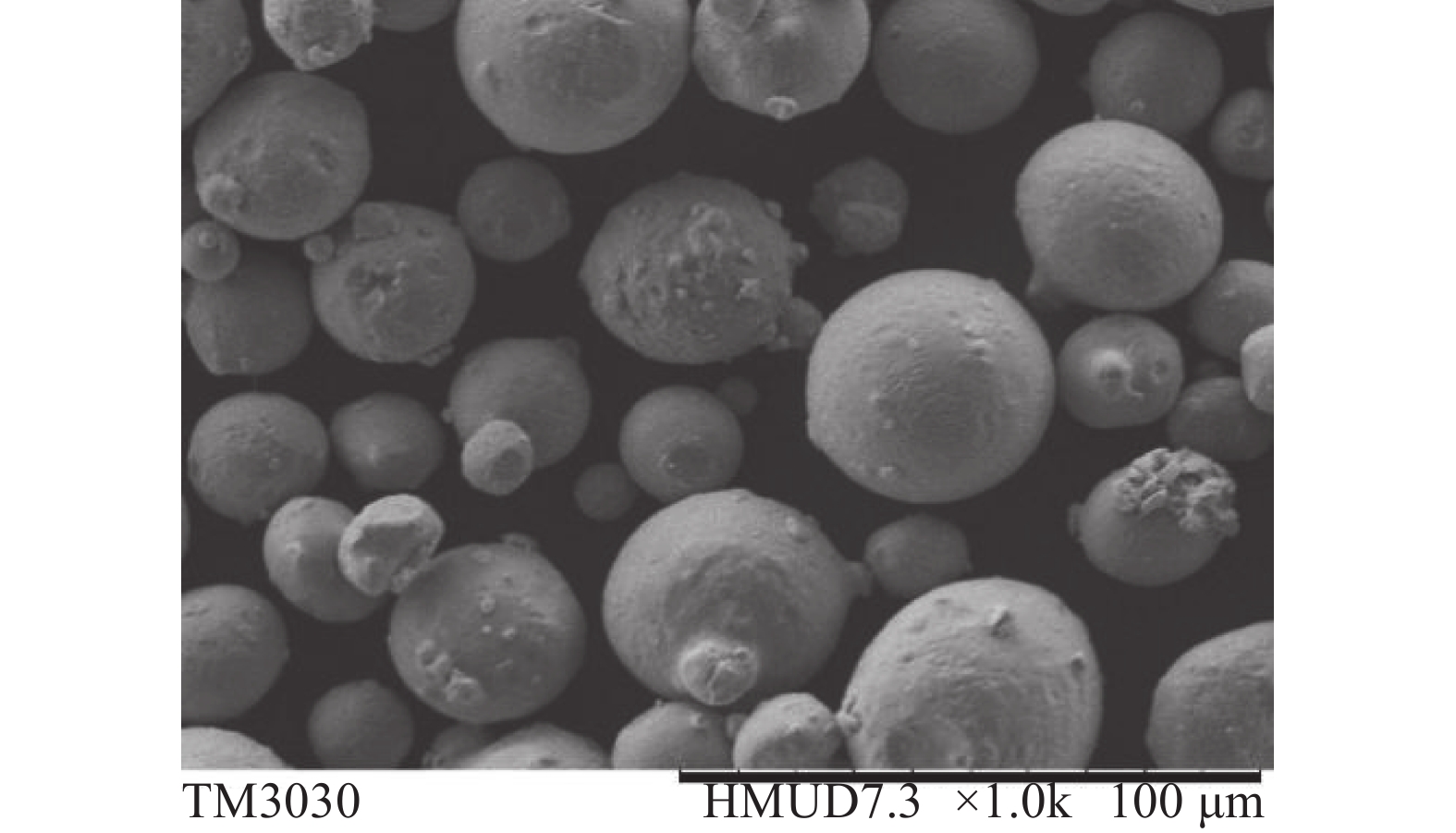
Set citation alerts for the article
Please enter your email address