
- Photonics Research
- Vol. 10, Issue 5, 1202 (2022)
Abstract
1. INTRODUCTION
Length is one of the fundamental physical quantities. The capability of its precise measurement has a strong impact on diverse areas in science and technology [1,2]. Rapid and precise measurements of extremely small displacements are indispensable for the observation of optomechanical dynamical motion [3–7], Brownian motion [8–10], high-resolution metrology for forces and fields [11], and calibration of ultraprecise length standards [12,13]. Laser interferometry through heterodyne and homodyne principles for subwavelength precision has led the displacement measurement toward high precision and minimizing periodic error [14]. Recent research in the laser interferometric distance measurement, determining a target distance with single operation, has shown a kilometer-scale distance measurement with nanometer precision by aid of frequency comb using its direct traceability to the microwave time standard with various methods [15–18]. However, these laser-interferometric-based displacement or distance measurements are practically bounded at subpicometer sensitivities due to the precision limitation of interferometric phase measurement [19]. Alternatively, cavity Fabry–Perot (FP) interferometry, based on tracking the resonance of an FP cavity, is capable of measuring subpicometer level displacement without periodic errors [20]. The FP cavity has usually been used to stabilize a laser frequency by synchronizing the laser carrier frequency to a resonance frequency of an FP cavity through a Pound–Drever–Hall (PDH) locking scheme [21]. Isolated high-finesse FP cavities have played a key role in ultrastable optical frequency generation and slave clocks for optical lattice clocks [22–24]. Over the last decade, high-Q whispering-gallery-mode (WGM) microcavities, tolerant to mechanical noise, have been developed for achieving high-performance optical clocks [25–27], low-noise microwave oscillators [28,29], and optical frequency combs with miniaturized system formats [27,30–32]. Complementing and somewhat contrary to laser stabilization, cavity locking measures displacement on the optical cavity, which is converted into a resonance frequency change of the cavity, by measuring the beat frequency with a stabilized laser [33]. This technique demonstrates ultraprecision fiber-optic strain sensing. Furthermore, a PDH locking scheme facilitates measurement of Brownian and optomechanical motion of microscale optics as the PDH error signal converts frequency fluctuations into an electrical signal, which enables fast dynamic measurement [34–36].
Here we present real-time measurements of femtometer displacement on an ultrahigh-Q WGM
2. RESULTS
A. Measurement of Sub-
Figure 1 shows the schematic of subfemtometer displacement measurement for the
Sign up for Photonics Research TOC. Get the latest issue of Photonics Research delivered right to you!Sign up now
Figure 1.Conceptual image of sub-
Figure 2 depicts the experimental setup of the subfemtometer displacement measurement of the
Figure 2.Sub-
The PDH error signal, demodulated by a double-balanced RF mixer and RF low-pass filter, is generated near the
B. Dynamical Measurement of the
To minimize the influence of technical noise from the surrounding environment, the vacuum chamber is evacuated to
Figure 3.Frequency noise and displacement on the
For verification of the measured power spectral density from the control signal, the power spectral density, analyzed by the PDH error signal without frequency synchronization, is also plotted as the yellow line in Fig. 3 [35]. This reflects solely the fluctuation of the
The orange line shows the theoretically estimated thermodynamical noise level of our
Figure 4 illustrates the real-time traces of the resonance frequency and the corresponding displacement variations. Figure 4(a) shows a typical time-series trace of the
Figure 4.Real-time trace of frequency shift and displacement on
For further long-term measurement [Fig. 4(b)], we set the RF synthesizer voltage-controlled input port to 30 MHz with a
Figure 5 illustrates the real-time dynamic motion measurement of the
Figure 5.Real-time measurement of the response dynamics of the
Tracing a resonance frequency of an optical cavity can be applied in an axial displacement measurement using Fabry–Perot cavities [44–47]. Figure 6 shows a conceptual view of axial motional displacement measurement using a Fabry–Perot cavity. One of mirror of the Fabry–Perot cavity can be mounted to a target surface. As demonstrated in the main text, our proposed scheme has a capability of sub-
Figure 6.Conceptual schematic of resonance tracking-based subfemtometer motional displacement measurements in linear Fabry–Perot cavities and interferometry. The red line and blue line correspond to the optical and electrical lines, respectively. The right mirror of the ultrahigh-
3. CONCLUSION
In summary, we have shown an observation of subfemtometer dynamics on the ultrahigh-Q single-crystal
Acknowledgment
Acknowledgment. The authors acknowledge discussions with Jaime Flor Flores. Y.-S.J. acknowledges the support of the Korea Research Institute of Standards and Science. S.-W.K. acknowledges the support of the National Research Foundation of the Republic of Korea. The reported research performed by A.M was carried out at the Jet Propulsion Laboratory, California Institute of Technology, under a contract with the National Aeronautics and Space Administration.
APPENDIX A: DISPLACEMENT MEASUREMENT BY PDH ERROR SIGNAL ANALYSIS
A linear part of the PDH error signal converts the resonance frequency shift to a DC voltage in the time domain. The PDH error signal is not only used for the frequency stabilization but also the high-speed tracking of the resonance frequency shift. In this study, we use the DC voltage of the PDH error signal to analyze the resonance frequency shift. First we tune the reference laser to the resonance mode of the
APPENDIX B: DISPLACEMENT MEASUREMENT BY CONTROL SIGNAL ANALYSIS
The reference laser, which provides a fixed reference point in the frequency domain, is frequency shifted by the SSB modulator to be synchronized to the microcavity resonance. The modulation frequency of about 5 GHz (
APPENDIX C: THERMODYNAMICAL NOISE LIMITS OF THE CYLINDRICAL WGM RESONATOR
The thermodynamical noise limits of the cylindrical WGM resonator are calculated by our theoretical model [
APPENDIX D: THERMAL MODULATION OF THE MgF2 WGM MICROCAVITY
The
References
[1] B. P. Abbott, R. Abbott, T. D. Abbott, M. R. Abernathy, F. Acernese, K. Ackley, C. Adams, T. Adams, P. Addesso, R. X. Adhikari, V. B. Adya. Observation of gravitational waves from a binary black hole merger. Phys. Rev. Lett., 116, 061102(2016).
[2] P. Trocha, M. Karpov, D. Ganin, M. H. P. Pfeiffer, A. Kordts, S. Wolf, J. Krockenberg, P. Marin-Palmo, C. Weimann, S. Randel, W. Freude, T. J. Kippenberg, C. Koos. Ultrafast optical ranging using microresonator soliton frequency combs. Science, 359, 887-891(2018).
[3] S. Gigan, H. R. Böhm, M. Paternostro, F. Blaser, G. Langer, J. B. Hertzberg, K. C. Schwab, D. Bäuerle, M. Aspelmeyer, A. Zeilinger. Self-cooling of a micromirror by radiation pressure. Nature, 444, 67-70(2006).
[4] J. Chan, T. P. Mayer Alegre, A. H. Safavi-Naeini, J. T. Hill, A. Krause, S. Groblacher, M. Aspelmeyer, O. Painter. Laser cooling of a nanomechanical oscillator into its quantum ground state. Nature, 478, 89-92(2011).
[5] Y.-C. Liu, X. Luan, Y.-F. Xiao, C. W. Wong. Dynamic dissipative cooling of a mechanical oscillator in strong-coupling optomechanics. Phys. Rev. Lett., 110, 153606(2013).
[6] M. Aspelmeyer, T. J. Kippenberg, F. Marquardt. Cavity optomechanics. Rev. Mod. Phys., 86, 1391-1452(2014).
[7] J. Cripe, N. Aggarwal, R. Lanza, A. Libson, R. Singh, P. Heu, D. Follman, G. D. Cole, N. Mavalvala, T. Corbitt. Measurement of quantum back action in the audio band at room temperature. Nature, 568, 364-367(2019).
[8] Z. Wang, J. Lee, P. X.-L. Feng. Spatial mapping of multimode Brownian motions in high-frequency silicon carbide microdisk resonators. Nat. Commun., 5, 5158(2014).
[9] S. Groblacher, A. Trubarov, N. Prigge, G. D. Cole, M. Aspelmeter, J. Eisert. Observation of non-Markovian micromechanical Brownian motion. Nat. Commun., 6, 7606(2015).
[10] R. Leijssen, G. R. La Gala, L. Freisem, J. T. Muhonen, E. Verhagen. Nonlinear cavity optomechanics with nanomechanical thermal fluctuations. Nat. Commun., 8, 6024(2017).
[11] F. J. Giessibl. Advances in atomic force microscopy. Rev. Mod. Phys., 75, 949-983(2003).
[12] H. Haitjema, P. H. J. Schellekens, S. F. C. L. Wetzels. Calibration of displacement sensors up to 300 μm with nanometre accuracy and direct traceability to a primary standard of length. Metrologia, 37, 25-33(2000).
[13] J. Jin, Y.-J. Kim, Y. Kim, S.-W. Kim, C.-S. Kang. Absolute length calibration of gauge blocks using optical comb of a femtosecond pulse laser. Opt. Express, 14, 5968-5974(2006).
[14] N. Bobroff. Recent advances in displacement measuring interferometry. Meas. Sci. Technol., 4, 907-926(1993).
[15] I. Coddington, W. C. Swann, L. Nenadovic, N. R. Newbury. Rapid and precise absolute distance measurements at long range. Nat. Photonics, 3, 351-356(2009).
[16] J. Lee, Y.-J. Kim, K. Lee, S. Lee, S.-W. Kim. Time-of-flight measurement with femtosecond light pulses. Nat. Photonics, 4, 716-720(2010).
[17] S. A. van den Berg, S. T. Persijn, G. J. P. Kok, M. G. Zeitouny, N. Bhattacharya. Many-wavelength interferometry with thousands of lasers for absolute distance measurement. Phys. Rev. Lett., 108, 183901(2012).
[18] Y.-S. Jang, H. Liu, J. Yang, M. Yu, D.-L. Kwong, C. W. Wong. Nanometric precision distance metrology via hybrid spectrally resolved and homodyne interferometry in a single soliton frequency microcomb. Phys. Rev. Lett., 126, 023903(2021).
[19] Y.-S. Jang, G. Wang, S. Hyun, H. J. Kang, B. J. Chun, Y.-J. Kim, S.-W. Kim. Comb-referenced laser distance interferometer for industrial nanotechnology. Sci. Rep., 6, 31770(2016).
[20] T. R. Schibli, K. Minoshima, Y. Bitou, F.-L. Hong, H. Inaba, A. Onae, H. Matsumoto. Displacement metrology with sub-pm resolution in air based on a fs-comb wavelength synthesizer. Opt. Express, 14, 5984-5993(2006).
[21] R. W. P. Drever, J. L. Hall, F. V. Kowalski, J. Hough, G. M. Ford, A. J. Munley, H. Ward. Laser phase and frequency stabilization using an optical resonator. Appl. Phys. B, 31, 97-105(1983).
[22] D. G. Matei, T. Legero, S. Häfner, C. Grebing, R. Weyrich, W. Zhang, L. Sonderhouse, J. M. Robinson, J. Ye, F. Riehle, U. Sterr. 1.5 μm lasers with sub-10 mHz linewidth. Phys. Rev. Lett., 118, 263202(2017).
[23] M. Takamoto, F.-L. Hong, R. Higashi, H. Katori. An optical lattice clock. Nature, 435, 321-324(2005).
[24] B. J. Bloom, T. L. Nicholson, J. R. Williams, S. L. Campbell, M. Bishof, X. Zhang, W. Zhang, S. L. Bromley, J. Ye. An optical lattice clock with accuracy and stability at the 10−18 level. Nature, 506, 71-75(2014).
[25] H. Lee, M.-G. Suh, T. Chen, J. Li, S. A. Diddams, K. J. Vahala. Spiral resonators for on-chip laser frequency stabilization. Nat. Commun., 4, 2468(2013).
[26] J. Lim, A. A. Savchenkov, E. Dale, W. Liang, D. Eliyahu, V. Ilchenko, A. B. Matsko, L. Maleki, C. W. Wong. Chasing the thermodynamical noise limit in whispering-gallery-mode resonators for ultrastable laser frequency stabilization. Nat. Commun., 8, 8(2017).
[27] D. T. Spencer, T. Drake, T. C. Briles, J. Stone, L. C. Sinclair, C. Fredrick, Q. Li, D. Westly, B. R. Ilic, A. Bluestone, N. Volet, T. Komljenovic, L. Chang, S. H. Lee, D. Y. Oh, M.-G. Suh, K. Y. Yang, M. H. P. Pfeiffer, T. J. Kippenberg, E. Norberg, L. Theogarajan, K. Vahala, N. R. Newbury, K. Srinivasan, J. E. Bowers, S. A. Diddams, S. B. Papp. An optical-frequency synthesizer using integrated photonics. Nature, 557, 81-85(2018).
[28] J. Li, X. Yi, H. Lee, S. A. Diddams, K. J. Vahala. Electro-optical frequency division and stable microwave synthesis. Science, 345, 309-313(2014).
[29] W. Liang, D. Eliyahu, V. S. Ilchenko, A. A. Savchenkov, A. B. Matsko, D. Seidel, L. Maleki. High spectral purity Kerr frequency comb radio frequency photonic oscillator. Nat. Commun., 6, 7957(2015).
[30] B. C. Yao, S.-W. Huang, Y. Liu, A. K. Vinod, C. Choi, M. Hoff, Y. Li, M. Yu, Z. Feng, D.-L. Kwong, Y. Huang, Y. Rao, X. Duan, C. W. Wong. Gate-tunable frequency combs in graphene-nitride microresonators. Nature, 558, 410-414(2018).
[31] B. Stern, X. Ji, Y. Okawachi, A. L. Gaeta, M. Lipson. Battery-operated integrated frequency comb generator. Nature, 562, 401-405(2018).
[32] Y. Li, Y. Li, S.-W. Huang, B. Li, H. Liu, J. Yang, A. K. Vinod, K. Wang, M. Yu, D.-L. Kwong, H. Wang, K. K.-Y. Wong, C. W. Wong. Real-time transition dynamics and stability of chip-scale dispersion-managed frequency microcombs. Light Sci. Appl., 9, 52(2020).
[33] G. Gagliardi, M. Salza, S. Avino, P. Ferraro, P. De Natale. Probing the ultimate limit of fiber-optic strain sensing. Science, 330, 1081-1084(2010).
[34] O. Arcizet, P.-F. Cohadon, T. Briant, M. Pinard, A. Heidmann, J.-M. Mackowski, C. Michel, L. Pinard, O. Francais, L. Rousseau. High-sensitivity optical monitoring of a micromechanical resonator with a quantum-limited optomechanical sensor. Phys. Rev. Lett., 97, 133601(2006).
[35] O. Arcizet, P.-F. Cohadon, T. Briant, M. Pinard, A. Heidmann. Radiation-pressure cooling and optomechanical instability of a micromirror. Nature, 444, 71-74(2006).
[36] G. Anetsberger, R. Riviere, A. Schliesser, O. Arcizet, T. J. Kippenberg. Ultralow-dissipation optomechanical resonators on a chip. Nat. Photonics, 2, 627-633(2008).
[37] J. Lim, A. A. Savchenkov, A. B. Matsko, S.-W. Huang, L. Maleki, C. W. Wong. Microresonator-stabilized extended-cavity diode laser for supercavity frequency stabilization. Opt. Lett., 42, 1249-1252(2017).
[38] J. Lim, W. Liang, A. B. Matsko, L. Maleki, C. W. Wong. Probing 10 μK stability and residual drifts in the cross-polarized dual-mode stabilization of single-crystal ultrahigh-
[39] K. Jung, J. Kim. Characterization of timing jitter spectra in free-running mode-locked lasers with 340 dB dynamic range over 10 decades of Fourier frequency. Opt. Lett., 40, 316-319(2015).
[40] A. B. Matsko, A. A. Savchenkov, N. Yu, L. Maleki. Whispering-gallery-mode resonators as frequency references. I. Fundamental limitations. J. Opt. Soc. Am. B, 24, 1324-1335(2007).
[41] A. A. Savchenkov, A. B. Matsko, V. S. Ilchenko, N. Yu, L. Maleki. Whispering-gallery-mode resonators as frequency references. II. Stabilization. J. Opt Soc. Am. B, 24, 2988-2997(2007).
[42] J. Alnis, A. Matveev, N. Kolachevsky, T. Udem, T. W. Hansch. Subhertz linewidth diode lasers by stabilization to vibrationally and thermally compensated ultralow-expansion glass Fabry-Pérot cavities. Phys. Rev. A, 77, 053809(2008).
[43] Z. Li, W. Ma, W. Yang, Y. Wang, Y. Zheng. Reduction of zero baseline drift of the Pound–Drever–Hall error signal with a wedged electro-optical crystal for squeezed state generation. Opt. Lett., 41, 3331-3334(2016).
[44] J. R. Lawall. Fabry–Perot metrology for displacements up to 50 mm. J. Opt. Soc. Am. A, 22, 2786-2798(2005).
[45] M. Zhu, H. Wei, X. Wu, Y. Li. Fabry–Perot interferometer with picometer resolution referenced to an optical frequency comb. Opt. Laser Eng., 67, 128-134(2015).
[46] M. Zhu, H. Wei, S. Zhao, X. Wu, Y. Li. Subnanometer absolute displacement measurement using a frequency comb referenced dual resonance tracking Fabry–Perot interferometer. Appl. Opt., 54, 4594-4601(2015).
[47] N. M. R. Hoque, L. Duan. Picostrain-resolution fiber-optic sensing down to sub-10 mHz infrasonic frequencies. J. Opt. Soc. Am. B, 37, 2773-2778(2020).
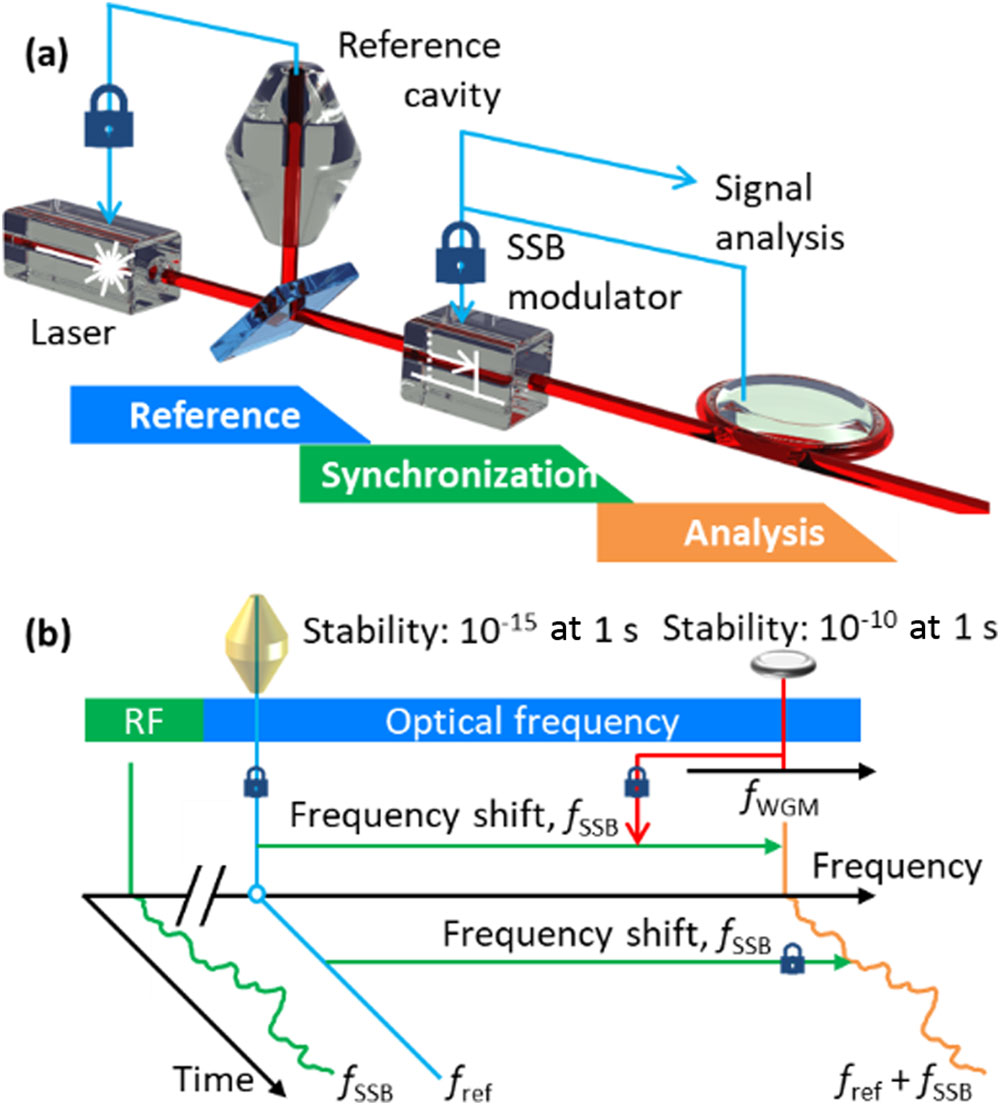
Set citation alerts for the article
Please enter your email address