
- Chinese Optics Letters
- Vol. 19, Issue 10, 101201 (2021)
Abstract
1. Introduction
Three-dimensional (3D) measurement technology[
Many researchers have developed many methods, which can be roughly divided into two categories. The first category is called preprocessing, that is, to change the fringes before projection in order to obtain the ideal phase distribution. One solution is called gamma correction[
The second category is called post-processing. It is to obtain the ideal phase distributions by compensating the nonlinear errors from the distortion fringe[
Sign up for Chinese Optics Letters TOC. Get the latest issue of Chinese Optics Letters delivered right to you!Sign up now
To the best of our knowledge, when the nonlinear errors are periodical, the probability density function (PDF) of the wrapped phase can be used as a criterion to identify the nonlinear effect quantitatively. In Ref. [8], the PDF tool is used to find the systematical gamma to fulfill a pre-correction process. In our previous work[
2. Principle
2.1. Phase error introduced by the nonlinearity
A digital fringe projection system is shown in Fig. 1. The digital projector is used to project the computer-generated fringe to the object surface. The CCD camera is used to capture the fringe patterns modulated by the height of the object.
Figure 1.Fringe projection system.
The computer generates ideal sinusoidal fringes. Its intensity can be expressed as
Because of the intrinsic gamma effect of the commercial projector–camera system, as well as the reflectivity of the object surface and ambient light, in fact, the captured fringe is
We only consider harmonics up to the fifth order when
The measured phase
From Eqs. (4), (5), and (6), the phase error can be derived as the following form:
In order to eliminate the effect of the reflectivity
After Taylor series expansion, Eq. (10) can be expressed as
Obviously, the proposed nonlinear error model is much more accurate than the approximated model in Eq. (12), which is used in our previous work[
2.2. PDF-based algorithm
Let
Figure 2.Nonlinear effect for (a) the wrapped phase and (b) the PDF curves.
In the ideal case, the probabilities of the wrapped phase values are equal, i.e., the PDF value is even[
The PDF curves and partial phase sampling regions with four kinds of different
Figure 3.In the cases of different values of M: (a) PDF curves and (b) partial phase sampling regions.
2.3. Searching process by correlation
The process of finding the best coefficient
Figure 4.Process of finding K2 and compensation.
3. Experiments and Analysis
A digital fringe projection system is used to verify the performance of the proposed algorithm. The system includes a digital light processing (DLP) projector with a resolution of
The measurement results of the reference plane are shown in Fig. 5. Figure 5(a) is the captured fringe image. The real PDF curve is shown in Fig. 5(b), and the comparison result between it and the simulated PDF curves is shown in Fig. 5(c). Here,
Figure 5.Measurement results: (a) captured fringe image, (b) the real PDF, (c) the comparison result of real and simulated PDF curves, and (d) the correlation curve.
For comparison, our previous work[
Figure 6.Comparisons of these two methods: (a) the residual phase error and (b) the PDF curves.
The quantitative comparison of the measurement results by the two methods is shown in Table 1.
Original | Our Previous Work | Proposed Algorithm | |
---|---|---|---|
Coefficients (C1 and C2/K2) | – | (0.2340, −0.0240) | 0.2400 |
STD of the phase errors (rad) | 0.1699 | 0.0129 | 0.0125 |
Processing time (s) | – | 329.36 | 0.12 |
Table 1. Quantitative Comparison Results of the Measurement by Two Methods
Apparently, the proposed algorithm is slightly more accurate than our previous work. While the simulated PDF curves of the proposed method can be produced in advance, it can also dramatically shorten the computation time with the correlation process, from 329.36 s to 0.12 s. Moreover, the proposed correlation process can also be implemented to more coefficient applications when the nonlinearity is much more severe.
Next, a pulp mask is measured, and the results are shown in Fig. 7. The recovered phase before compensation is shown in Fig. 7(a), which shows a lot of significant periodic errors. Figures 7(b) and 7(c) show the compensated results from our previous work and the proposed method, respectively. Also, the quantitative comparison results of the object measurement by the two methods is shown in Table 2. Obviously, the quality of the measured phase is greatly improved. Note that the coefficient
Original | Our Previous Work | Proposed Algorithm | |
---|---|---|---|
Coefficients (C1 and C2/K2) | – | (0.2270, −0.0220) | 0.2300 |
STD of the phase errors (rad) | 0.1662 | 0.0226 | 0.0222 |
Processing time (s) | – | 331.06 | 0.12 |
Table 2. Quantitative Comparison Results of the Object Measurement by Two Methods
Figure 7.Measurement results of a pulp mask: (a) without compensation, (b) compensated by our previous work, and (c) compensated by the proposed method.
4. Conclusions
In conclusion, we established a new single-coefficient error model and proposed a fast and high-accuracy nonlinear error compensation method. Only one coefficient
References
[1] L. Li, Z. Pan, H. Cui, J. Liu, S. Yang, L. Liu, Y. Tian, W. Wang. Adaptive window iteration algorithm for enhancing 3D shape recovery from image focus. Chin. Opt. Lett., 17, 061001(2019).
[2] H. Tu, S. He. Fringe shaping for high-/low-reflectance surface in single-trial phase-shifting profilometry. Chin. Opt. Lett., 16, 101202(2018).
[3] W. Fang, K. Yang, H. Li. Propagation-based incremental triangulation for multiple views 3D reconstruction. Chin. Opt. Lett., 19, 021101(2021).
[4] L. Chen, C. Huang. Miniaturized 3D surface profilometer using digital fringe projection. Meas. Sci. Technol., 16, 1061(2005).
[5] S. Ma, C. Quan, R. Zhu, L. Chen, B. Li, C. J. Tay. A fast and accurate gamma correction based on Fourier spectrum analysis for digital fringe projection profilometry. Opt. Commun., 285, 533(2012).
[6] T. R. Judge, P. J. Bryanston-Cross. A review of phase unwrapping techniques in fringe analysis. Opt. Lasers Eng., 21, 199(1994).
[7] E. Zappa, G. Busca. Comparison of eight unwrapping algorithms applied to Fourier-transform profilometry. Opt. Lasers Eng., 46, 106(2008).
[8] X. Yu, Y. Liu, N. Liu, M. Fan, X. Su. Flexible gamma calculation algorithm based on probability distribution function in digital fringe projection system. Opt Express, 27, 32047(2019).
[9] S. Zhang. Comparative study on passive and active projector nonlinear gamma calibration. Appl. Opt., 54, 3834(2015).
[10] H. Guo, H. He, M. Chen. Gamma correction for digital fringe projection profilometry. Appl. Opt., 43, 2906(2004).
[11] Z. Li, Y. Li. Gamma-distorted fringe image modeling and accurate gamma correction for fast phase measuring profilometry. Opt. Lett., 36, 154(2011).
[12] T. Hoang, B. Pan, D. Nguyen, Z. Wang. Generic gamma correction for accuracy enhancement in fringe-projection profilometry. Opt. Lett., 35, 1992(2010).
[13] K. Liu, Y. Wang, D. Lau, Q. Hao, L. Hassebrook. Gamma model and its analysis for phase measuring profilometry. J. Opt. Soc. Am. A, 27, 553(2010).
[14] D. Zheng, F. Da, Q. Kemao, S. Seah. Phase error analysis and compensation for phase shifting profilometry with projector defocusing. Appl. Opt., 55, 5721(2016).
[15] J. Zhang, Y. Zhang, B. Chen, B. Dai. Full-field phase error analysis and compensation for nonsinusoidal waveforms in phase shifting profilometry with projector defocusing. Opt. Commun., 430, 467(2019).
[16] S. Lei, S. Zhang. Digital sinusoidal fringe pattern generation: defocusing binary patterns VS focusing sinusoidal patterns. Opt. Lasers Eng., 48, 561(2010).
[17] Y. Wang, S. Zhang. Optimal pulse width modulation for sinusoidal fringe generation with projector defocusing. Opt. Lett., 35, 4121(2010).
[18] K. Yatabe, K. Ishikawa, Y. Oikawa. Compensation of fringe distortion for phase-shifting three-dimensional shape measurement by inverse map estimation. Appl. Opt., 55, 6017(2016).
[19] S. Zhang, S. T. Yau. Generic nonsinusoidal phase error correction for three-dimensional shape measurement using a digital video projector. Appl. Opt., 46, 36(2007).
[20] B. Pan, K. Qian, L. Huang, A. Asundi. Phase error analysis and compensation for non-sinusoidal waveforms in phase-shifting digital fringe projection profilometry. Opt. Lett., 34, 416(2009).
[21] Z. Cai, X. Liu, H. Jiang, D. He, X. Peng, S. Huang, Z. Zhang. Flexible phase error compensation based on Hilbert transform in phase shifting profilometry. Opt. Express, 23, 25171(2015).
[22] Y. Liu, X. Yu, J. Xue, Q. Zhang, X. Su. A flexible phase error compensation method based on probability distribution functions in phase measuring profilometry. Opt. Laser Technol., 129, 106267(2020).
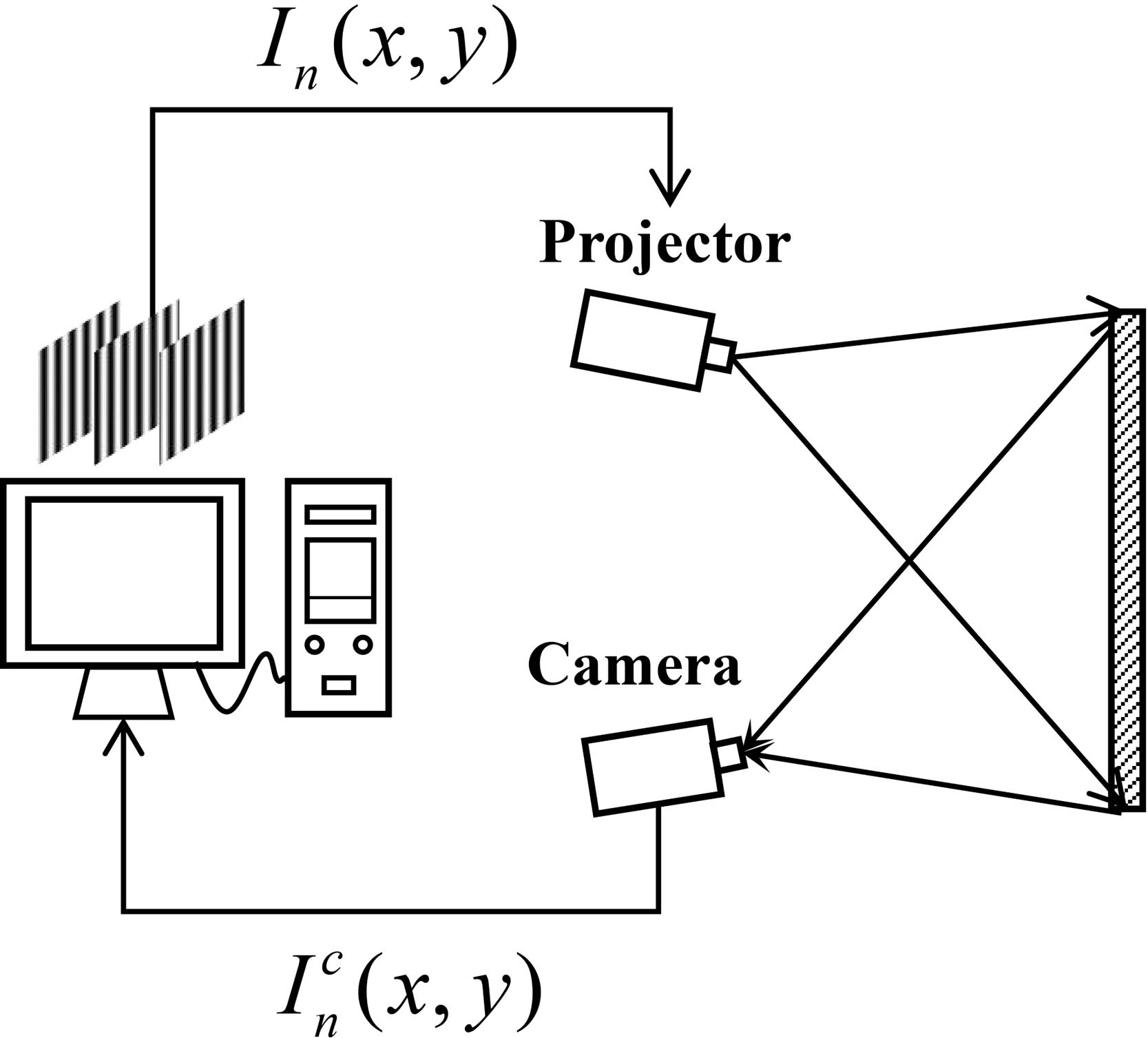
Set citation alerts for the article
Please enter your email address