
- Chinese Optics Letters
- Vol. 19, Issue 12, 121601 (2021)
Abstract
1. Introduction
Plastic is used in a wide range of fields for its transparency and flexibility including portable personal electronics, packaging, biomedical materials, etc. However, due to scattered using sites, poor emission management, high recovery costs, and difficulties in recovery sorting, less than 10% of the world’s plastic is recycled and reused. Most of the remaining plastic waste enters the ocean. As a result, 50%–80% of marine debris is plastic, and presently nearly 8 million tons of plastic garbage is dumped into the ocean every year[
Recently, transparent paper prepared from natural cellulose fibers is considered as a potential substitute for plastic film replacement due to its high transparency, high mechanical strength, flexibility, and biodegradability[
However, the extremely high preparation cost is the main obstacle to the market application of transparent paper. Although plant raw materials are cheap enough, the extraction of their nanofibers is very time-consuming and costly, including chemical methods[
Sign up for Chinese Optics Letters TOC. Get the latest issue of Chinese Optics Letters delivered right to you!Sign up now
2. Experimental Section
2.1. Materials
Basswood, straw, wheat straw, moso bamboo, laurel, and vines were used in this study just for demonstration. Basswood was purchased from Oriental Aolong Wooden Crafts Co., Ltd., Wuhan, Hubei. Straw and wheat straw are planted in Xuzhou, Jiangsu. Moso bamboo was purchased from Credit Department Store Co., Ltd., Suqian, Jiangsu. The laurel branches and vine were all gained from landscape plant of Nanjing University. Sodium hypochlorite [NaClO, 10% (mass fraction), Shanghai Linfeng Chemical Reagent Co., Ltd.] was used to remove the lignin content. The solvents used were deionized (DI) water and ethanol (98%), which was purchased from Yasheng Chemical Co., Ltd., Wuxi, Jiangsu.
2.2. Transparent paper fabrication
Different plants (wood, bamboo, straw, wheat, laurel, vine, etc.) could be made into transparent paper through the same preparation processes. Here, bamboo is used as an example plant material to demonstrate the typical preparation process. Firstly, bamboo was crushed into chips with a size about
2.3. Screen printed circuit
Circuits were screen printed on transparent paper using a stainless steel mask with a mesh count of 325 and a wire diameter of 15 µm[
3. Results and Discussion
The commonality of plant microstructures greatly broadens the selection range of raw materials for preparing transparent paper (Fig. 1). Generally, plants are made up of cells, and the cell walls of most plants have similar composition and cellular hierarchical microstructure[
Figure 1.Schematic of the rapid, universal fabrication process of transparent paper using different plants by lignin removal and cold pressing. (a) Taking the wood cell profile model as an example, plant cell walls have similar microstructures. Plant walls such as vine, bush, wood, bamboo, straw, branch, wheat, and other common plants have similar microstructures. The plant is (b) separated into small pieces and (c) delignified by NaClO subsequently. (d) Transparent paper achieved by cold pressing finally.
In this method, high-quality transparent paper can be obtained in only 42 min. Taking the wood branch as an example to fabricate a transparent paper, the process can be divided into three steps: first, wood branches [Fig. 2(a)] are mechanically disintegrated into wood flour or wood chips [Fig. 2(b)], which takes about 2 min, and then the colored lignin is removed from the wood powder to obtain white nanofibril aggregates solution [Fig. 2(c)], which takes only 20 min. After the lignin removal, the cellulose fibers can move freely and spread out with little applied force. Finally, the micron nanofibril aggregates are washed in the ordinary way of filtration for about 10 min, and excess water is removed by cold pressing for 10 min to obtain a transparent paper [Fig. 2(d)]. Compared with the lengthy preparation process of nanofibers, nanofibril aggregates shorten the time of processing, cleaning, and separation by orders of magnitude. The scanning electron microscope (SEM) image of the sample corresponding to each step shows that there is no nanofiber operation in the process of changing the wood branch to transparent paper [Figs. 2(e)–2(h)]. The surface of the finally obtained transparent paper is flat and smooth, and the traces of the original micron fibers are no longer visible [Fig. 2(h)]. Moreover, from the SEM image and atomic force microscopy (AFM) photos [Fig. 2(j) and 2(k)], the surface of the transparent paper is made to the nanometer level by cold pressing, and the nanofibers in the transparent paper can be observed directly, which are randomly arranged to show the isotropic nature of the paper. The X-ray scattering image of transparent paper in Fig. S1 of Supplementary Materials is a circle at high-intensity diffraction, which indicates the random distribution of cellulose molecular chains and the isotropy of the transparent paper. Other types of plants, such as bamboo, straw, branch, bush, and vine with similar structure and composition, have also been practically shown to produce high-quality transparent paper composed of cellulose nanofibers quickly and efficiently using this method (Figs. S2–S13 in Supplementary Materials). The X-ray diffraction (XRD) patterns of wood chips and wood transparent paper show that peaks corresponding to cellulose crystals change little [Fig. 2(i) and Fig. S14 in Supplementary Materials]. This indicates that the ordered structure of the crystalline region in transparent paper is not disrupted by the delignification and pressing fabrication processes.
Figure 2.Take wood as an example to show the preparation process of transparent paper and the microstructure changes of corresponding materials. (a)–(d) Photos of the main processes of typical transparent paper fabrication and (e)–(h) the corresponding microstructure changes. (i) XRD profiles of wood chips and wood transparent paper, showing its main component of cellulose I, where 2θ of 16.5° and 22.5° correspond to the (110) and (200) planes of the cellulose crystal, respectively. (j) Nanofibrils with a diameter of about 30 nm in the wood cell. (k) AFM photo of transparent paper and the nanofibers can be observed.
In view of the urgent needs of future applications, a film with high light transmittance under visible light is needed[
Figure 3.Excellent homogeneous optical and mechanical properties of transparent paper. (a) Transmittance and haze of the transparent paper with a thickness of about 50 µm. The inset shows that the school badge underneath the transparent paper made of bamboo is clearly seen. (b) Transmittance and haze of different nine points on a piece of wood transparent paper. (c) Graph of the 3D scattered light intensity, showing light is scattered in an isotropic manner. (d) Tensile stress-strain curve for bamboo transparent paper.
Transparent paper from different kinds of plants can be used as a substrate material for biodegradable flexible optoelectronic devices due to its excellent properties such as flexibility, favorable water stability, and thermal stability (Fig. 4). As a demonstration of its biodegradability, transparent paper made from straw was placed in grass soil and exposed to the elements in nature [panel (i), Fig. 4(a)]. After 41 days, it was degraded into pieces by the microorganisms [panel (ii), Fig. 4(a)]. This indicates that transparent paper can be biodegraded in a short period of time and achieve the goal of coming from nature and returning to nature after service. Compared with commonly used plastic such as polyethylene (PE) and poly(ethylene terephthalate) (PET), transparent paper exhibits excellent performance in terms of thermal stability and solvent resistance. It can be seen from Fig. 4(b) that the paper still retained the original morphological characteristics, while PE and PET have softened and crystallized at 150°C for 10 min. Therefore, it proves that the transparent paper can be applied under higher temperatures. Transparent paper can also maintain its intact morphology and structure in commonly used chemical solvents. There was no visible change on the paper, while PE has been dissolved and deformed, and PET has also been swollen when placed in acetone for 15 min. Besides, as shown in Fig. 4(c), the paper can be bended and folded, which enables it be used as a flexible substrate.
Figure 4.Demonstration of transparent paper with good biodegradability, high temperature, and water stability as the substrate for electronic device. (a) Photos of transparent paper: (i) photo in grass soil and (ii) photo of it after 41 days. (b) (i)–(iii) Photos of original transparent paper and paper after treatment of high temperature and immersing chemical solvent, respectively. The paper was unchanged, after continuous treatment above. (b) (iv)–(vi) In contrast, PE deformed and solved after treatment of high temperature and chemical treatment, respectively, and (b) (vii)–(xi) PET crystallized and swelled after treatment of high temperature and chemical treatment, respectively. (c) (i), (ii) Transparent paper also can be bendable and foldable. (d) The bamboo transparent paper as printed circuit substrate. (d) (i)–(iii) Photos of original transparent paper with printed circuit and paper after treatment of high temperature and immersing chemical solvent, respectively. The circuit showed good conductivity. (d) (iv)–(vi) The microscope photos, correspondingly, after water and high-temperature treatment.
As a demonstration, we have shown a printed circuit on a transparent paper made of bamboo. After silk screen printing, it was annealed at 120°C for 10 min. The thickness of the silver electrode is about 6 µm, and the resistance value of the silver circuit is about 2.0 Ω [panel (i), Fig. 4(d)]. The bonding strength between the silver electrode and the transparent paper is strong enough. We soaked the sample in water for 48 h and then dried it. As shown in panel (ii), Fig. 4(d), there was no fracture on the circuit, the printing circuit was still in the path, the binding mode of the circuit with the substrate was not changed, and the wire resistance changed slightly to 2.3 Ω. From the micrograph before and after immersion in water, the fibers did not move or change. The water environment did no harm to the function of the printed circuit. After that, the same sample was placed in an oven at a temperature of 150°C for 10 min [panel (iii), Fig. 4(d)]. The printing circuit based on the transparent paper remained intact, the wires remained in the path, the resistance did not change significantly, and the shape and color of the paper did not change apparently. Obviously, heat treatment does not affect the printing circuit. From the microscope photos, it can be seen that the wire and fiber substrate still bind together tightly, and there was no obvious change on fiber morphology.
4. Conclusion
In summary, we demonstrate ultra-fast and low-cost fabrication of transparent paper based on the commonality of plant microstructures. Only 42 min is needed in the three fabrication steps of plant cell separation, lignin removal, and cold pressing. Cheap raw materials can be used, such as vine, bush, wood, bamboo, straw, branch, wheat, and other common plants. The obtained transparent paper shows high quality with a transparency up to 90.3%. It is a qualified electronic substrate material demonstrated by the circuit on it and has a good working ability after high-temperature and high-humidity treatment. Our method will greatly lower the cost of transparent paper and promote its market applications.
References
[1] J. Lewis. Material challenge for flexible organic devices. Mater. Today, 9, 38(2006).
[2] T. Someya, Z. Bao, G. G. Malliaras. The rise of plastic bioelectronics. Nature, 540, 379(2016).
[3] Y. Xiao, H. Luo, R. Tang, J. Hou. Preparation and applications of electrospun optically transparent fibrous membrane. Polymers, 13, 506(2021).
[4] A. B. Milstein, L. A. Jiang, J. X. Luu, E. L. Hines, K. I. Schultz. Acquisition algorithm for direct-detection ladars with Geiger-mode avalanche photodiodes. Appl. Opt., 47, 296(2008).
[5] H. X. Zhang, L. S. Feng, Y. L. Hou, S. Su, J. Liu, W. Y. Liu, J. Liu, J. J. Xiong. Preparation and characterization of a liquid level sensor based on plastic fibers. Chin. Opt. Lett., 13, 080601(2015).
[6] G. Y. Tang, J. Wei, W. Zhou, R. Q. Fan, M. Y. Wu, X. F. Xu. Multi-hole plastic optical fiber force sensor based on femtosecond laser micromachining. Chin. Opt. Lett., 12, 090604(2014).
[7] J. Brahney, N. Mahowald, M. Prank, G. Cornwell, Z. Klimont, H. Matsui, K. A. Prather. Constraining the atmospheric limb of the plastic cycle. Proc. Natl. Acad. Sci. USA, 118, e2020719118(2021).
[8] Y. S. Wang, M. Li, Y. Wang. Silk: a versatile biomaterial for advanced optics and photonics [Invited]. Chin. Opt. Lett., 18, 080004(2020).
[9] F. Hoeng, A. Denneulin, J. Bras. Use of nanocellulose in printed electronics: a review. Nanoscale, 8, 13131(2016).
[10] H. Zhu, Z. Fang, C. Preston, Y. Li, L. Hu. Transparent paper: fabrications, properties, and device applications. Energy Environ. Sci., 7, 269(2014).
[11] M. Wang, X. Jia, W. Liu, X. Lin. Water insoluble and flexible transparent film based on carboxymethyl cellulose. Carbohydr. Polym., 255, 117353(2021).
[12] S. Tsuneyasu, R. Watanabe, N. Takeda, K. Uetani, S. Izakura, K. Kasuya, K. Takahashi, T. Satoh. Enhancement of luminance in powder electroluminescent devices by substrates of smooth and transparent cellulose nanofiber films. Nanomaterials, 11, 697(2021).
[13] M. Tshwafo. Recent applications and innovations of cellulose based materials: a critical review. Cellul. Chem. Technol., 55, 1(2021).
[14] J. Yang, X. Y. Zhang, P. Wang, H. Meng, Y. X. Wu, J. P. Xie, J. Y. Zhang. Preparation and characterization of SiO2/TiO2/methylcellulose hybrid thick films for optical waveguides. Chin. Opt. Lett., 3, 399(2005).
[15] Y. H. Jung, T. H. Chang, H. Zhang, C. Yao, Q. Zheng, V. W. Yang, H. Mi, M. Kim, S. J. Cho, D. W. Park, H. Jiang, J. Lee, Y. Qiu, W. Zhou, Z. Cai, S. Gong, Z. Ma. High-performance green flexible electronics based on biodegradable cellulose nanofibril paper. Nat. Commun., 6, 7170(2015).
[16] H. Zhu, Z. Xiao, D. Liu, Y. Li, N. J. Weadock, Z. Fang, J. Huang, L. Hu. Biodegradable transparent substrates for flexible organic-light-emitting diodes. Energy Environ. Sci., 6, 2105(2013).
[17] X. Xu, J. Zhou, L. Jiang, G. Lubineau, T. Ng, B. S. Ooi, H. Y. Liao, C. Shen, L. Chen, J. Y. Zhu. Highly transparent, low-haze, hybrid cellulose nanopaper as electrodes for flexible electronics. Nanoscale, 8, 12294(2016).
[18] A. Khan, Z. Abas, H. S. Kim, J. Kim. Recent progress on cellulose-based electro-active paper, its hybrid nanocomposites and applications. Sensors, 16, 1172(2016).
[19] F. Brunetti, A. Operamolla, S. Castro-Hermosa, G. Lucarelli, V. Manca, G. M. Farinola, T. M. Brown. Printed solar cells and energy storage devices on paper substrates. Adv. Funct. Mater., 29, 1806798(2019).
[20] Q. Cheng, D. Ye, W. Yang, S. Zhang, H. Chen, C. Chang, L. Zhang. Construction of transparent cellulose-based nanocomposite papers and potential application in flexible solar cells. ACS Sust. Chem. Eng., 6, 8040(2018).
[21] S. J. Eichhorn, C. A. Baillie, N. Zafeiropoulos, L. Y. Mwaikambo, M. P. Ansell, A. Dufresne, K. M. Entwistle, P. J. Herrera-Franco, G. C. Escamilla, L. Groom, M. Hughes, C. Hill, T. G. Rials, P. M. Wild. Review: current international research into cellulosic fibres and composites. J. Mater. Sci., 36, 2107(2001).
[22] M. Herrera, K. Thitiwutthisakul, X. Yang, P.-O. Rujitanaroj, R. Rojas, L. Berglund. Preparation and evaluation of high-lignin content cellulose nanofibrils from eucalyptus pulp. Cellulose, 25, 3121(2018).
[23] O. Nechyporchuk, M. N. Belgacem, J. Bras. Production of cellulose nanofibrils: a review of recent advances. Indust. Crops Prod., 93, 2(2016).
[24] W. Chen, H. Yu, Y. Liu, P. Chen, M. Zhang, Y. Hai. Individualization of cellulose nanofibers from wood using high-intensity ultrasonication combined with chemical pretreatments. Carbohydr. Polym., 83, 1804(2011).
[25] R. Baati, A. B. Mabrouk, A. Magnin, S. Boufi. CNFs from twin screw extrusion and high pressure homogenization: a comparative study. Carbohydr. Polym., 195, 321(2018).
[26] S. V. Valenzuela, C. Valls, V. Schink, D. Sanchez, M. B. Roncero, P. Diaz, J. Martinez, F. I. J. Pastor. Differential activity of lytic polysaccharide monooxygenases on celluloses of different crystallinity. Effectiveness in the sustainable production of cellulose nanofibrils. Carbohydr. Polym., 207, 59(2019).
[27] S. Fujisawa, Y. Okita, H. Fukuzumi, T. Saito, A. Isogai. Preparation and characterization of TEMPO-oxidized cellulose nanofibril films with free carboxyl groups. Carbohydr. Polym., 84, 579(2011).
[28] M. Nogi, S. Iwamoto, A. N. Nakagaito, H. Yano. Optically transparent nanofiber paper. Adv. Mater., 21, 1595(2009).
[29] M. Zhu, C. Jia, Y. Wang, Z. Fang, J. Dai, L. Xu, D. Huang, J. Wu, Y. Li, J. Song, Y. Yao, E. Hitz, Y. Wang, L. Hu. Isotropic paper directly from anisotropic wood: top-down green transparent substrate toward biodegradable electronics. ACS Appl. Mater. Interfaces, 10, 28566(2018).
[30] M. Zhu, Y. Wang, S. Zhu, L. Xu, C. Jia, J. Dai, J. Song, Y. Yao, Y. Wang, Y. Li, D. Henderson, W. Luo, H. Li, M. L. Minus, T. Li, L. Hu. Anisotropic, transparent films with aligned cellulose nanofibers. Adv. Mater., 29, 1606284(2017).
[31] L. Zhou, M. Yu, X. Chen, S. Nie, W.-Y. Lai, W. Su, Z. Cui, W. Huang. Screen-printed poly(3,4-ethylenedioxy-thiophene):poly(styrenesulfonate) grids as ITO-free anodes for flexible organic light-emitting diodes. Adv. Funct. Mater., 28, 1705955(2018).
[32] Y. Okahisa, H. Sakata. Effects of growth stage of bamboo on the production of cellulose nanofibers. Fibers Polym., 20, 1641(2019).
[33] A. Alemdar, M. Sain. Isolation and characterization of nanofibers from agricultural residues: wheat straw and soy hulls. Bioresour. Technol., 99, 1664(2008).
[34] M. Guo, H. B. He, K. Yi, S. Y. Shao, G. X. Hu, J. D. Shao. Optical characteristics of ultrathin amorphous Ge films. Chin. Opt. Lett., 18, 103101(2020).
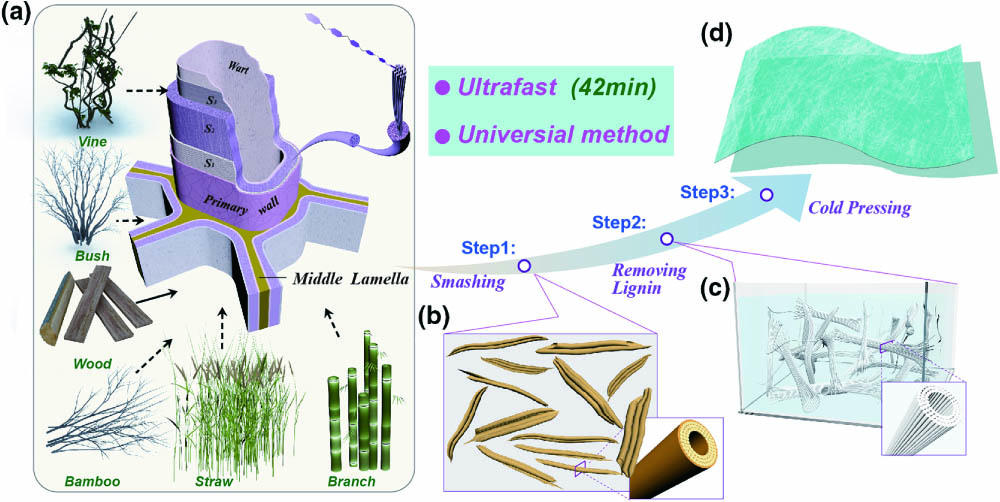
Set citation alerts for the article
Please enter your email address