Cheng-Jian Xiao, Guang-Wei Meng, Ying-Kui Zhao. Theoretical model of radiation heat wave in two-dimensional cylinder with sleeve[J]. Matter and Radiation at Extremes, 2023, 8(2): 026901

Search by keywords or author
- Matter and Radiation at Extremes
- Vol. 8, Issue 2, 026901 (2023)
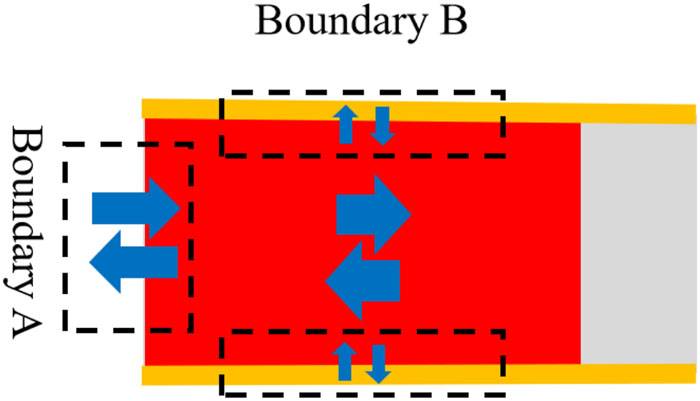
Fig. 1. Energy transport of a two-dimensional Marshak wave. Boundary A corresponds to the source surface and boundary B to the interface between the low-Z and high-Z materials. The red and gray regions are the heated and unheated low-Z foam, respectively. The yellow region is the high-Z material.
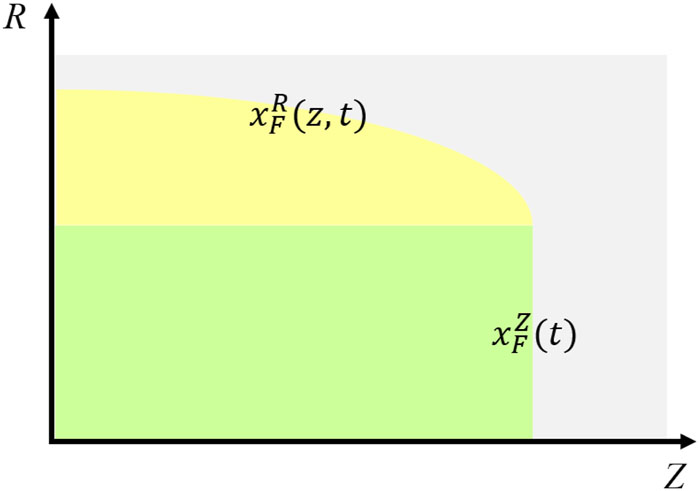
Fig. 2. Schematic of the Marshak waves in the cylinder at time t , where the R –Z profile is chosen. The gray part corresponds to the unheated material. The green and yellow parts correspond to the heated low-Z foam and the high-Z wall, respectively. The heat front positions of the Marshak waves in the low-Z foam and high-Z wall are x F Z ( t ) and x F R ( z , t ) , respectively.
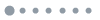
Fig. 3. Heat front position x F as a function of time t . The black dashed and red solid curves show the results with and without a lossy wall, respectively.
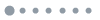
Fig. 4. Simulation results for the energy deposited in the low-Z foam per unit cross-sectional area of the foam cylinder, E ̃ Foam , for the process with a lossy wall and T Drive = 150 eV.
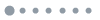
Fig. 5. Effective drive temperature for the process without a lossy wall. With this drive source, the E ̃ Foam of the process without a lossy wall is the same as that for the process with a lossy wall and T Drive = 150 eV.
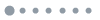
Fig. 6. Error due to the Hammer–Rosen solutions. Here, Ratio and τ ′ are defined as x F HR / x F MULTI and x F MULTI / l R ′ , respectively, where x F HR and x F MULTI are the heat front positions from the Hammer–Rosen solutions and the MULTI2D code, and l R ′ is the Rosseland free path of the heated material with temperature that at the source position.
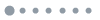
Fig. 7. Numerical results in the case of a constant drive temperature for (a) energy loss E Wall, (b) deposited energy E Foam, and (c) heat front position x F from the simulations (black dashed curves) and our model (red solid curves).
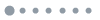
Fig. 8. Time-dependent drive temperature, which first increases and then decreases.
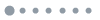
Fig. 9. Numerical results in the case of a time-dependent drive temperature for (a) energy loss E Wall, (b) deposited energy E Foam, and (c) heat front position x F from simulations (blue dotted curves), our model (red solid curves), and Ref. 38 (black dashed curves).
|
Table 1. Numerical results of the energy loss EWall, the deposited energy EFoam and the heat front position xF. The parameters in the square bracket are the material of the filled low-Z foam MFoam, the drive temperature TDrive (eV), the density of the filled foam ρ (g/cm3), and the radius of the foam cylinder R (cm).
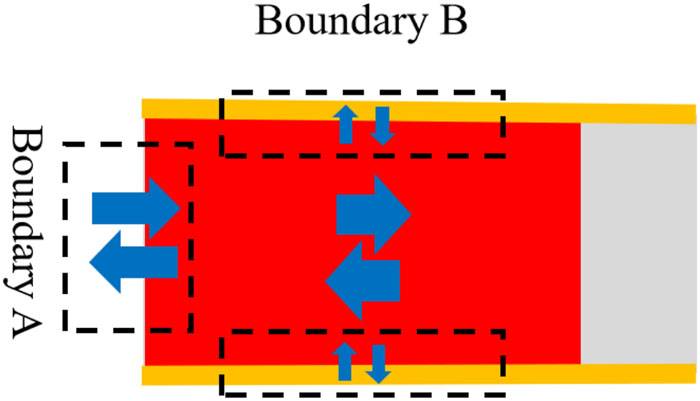
Set citation alerts for the article
Please enter your email address