Jun Ma. Coplanarity evaluation model of long linear LWIR detector[J]. Infrared and Laser Engineering, 2022, 51(3): 20210276

Search by keywords or author
- Infrared and Laser Engineering
- Vol. 51, Issue 3, 20210276 (2022)
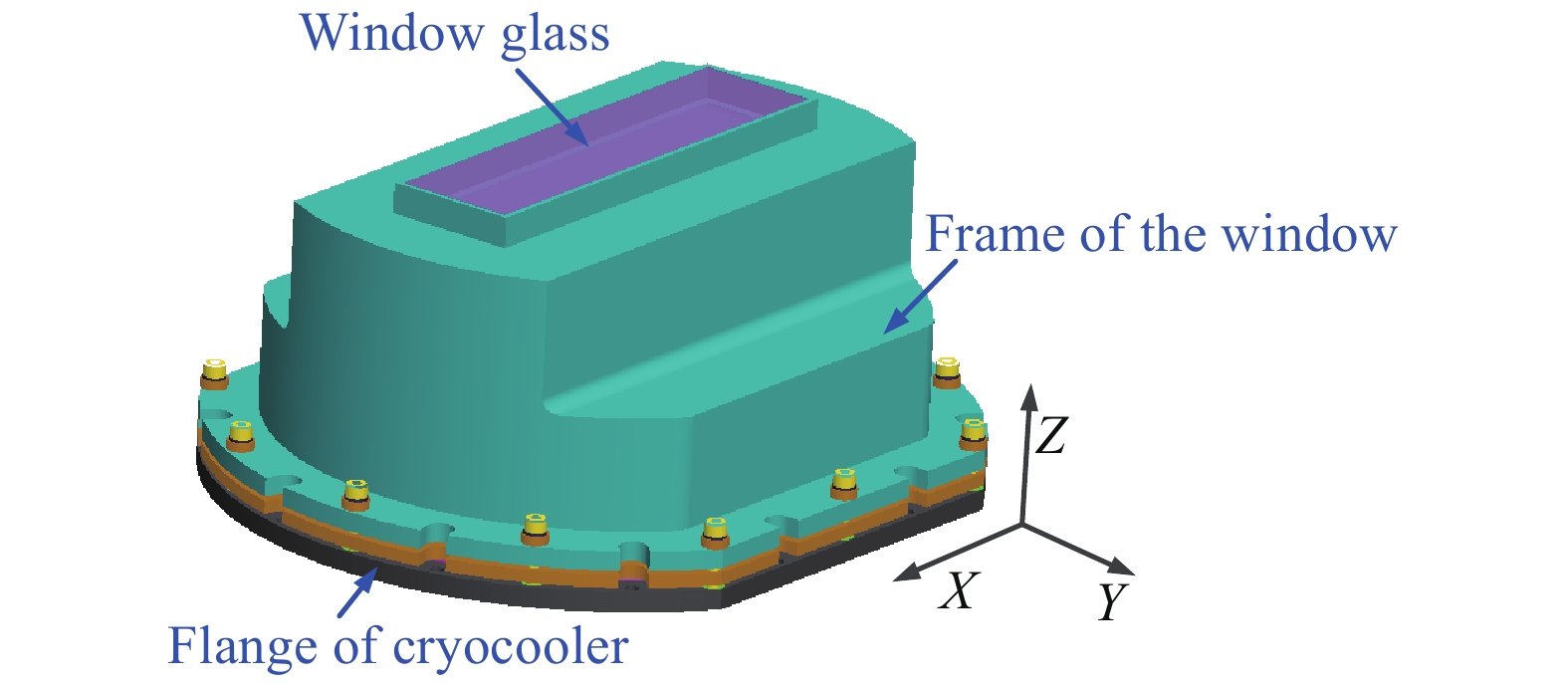
Fig. 1. External configuration of FPA
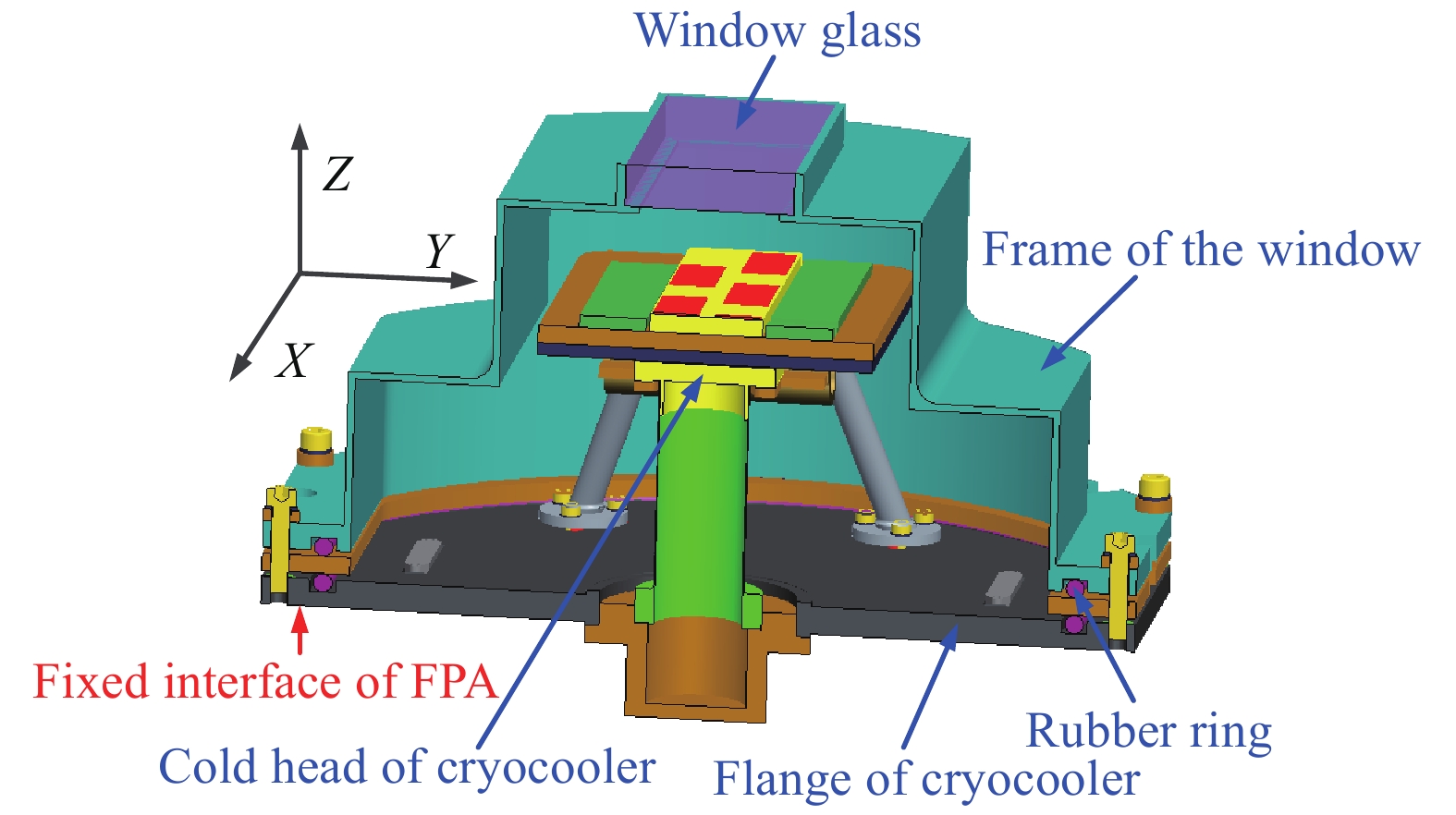
Fig. 2. Section of FPA
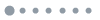
Fig. 3. Internal configuration of FPA
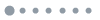
Fig. 4. FEM of FPA
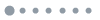
Fig. 5. Internal force of laminates
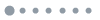
Fig. 6. Structure of isotropic laminates
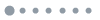
Fig. 7. Curves of laminates flatness with the CTE of laminate 1
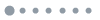
Fig. 8. Schematic of the division of detector area
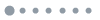
Fig. 9. Curves of the flatness of butting base with the thickness of cold plate
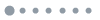
Fig. 10. Curves of the flatness of butting base with the CTE of cold plate
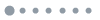
Fig. 11. Schematic of the design improvement of laminated structure
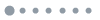
Fig. 12. Curves of the flatness of butting base with the thickness of cold plate after design improvement
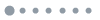
Fig. 13. Curves of the flatness of butting base with the CTE of cold plate after design improvement
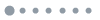
Fig. 14. Deformation of FPA in ground test (Unit: mm)
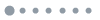
Fig. 15. Schematic of detector flatness test
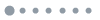
Fig. 16. Location of sample point in the flatness test of detector
|
Table 1. Flatness of butting base under different cases
|
Table 2. Material parameters for verifying analysis
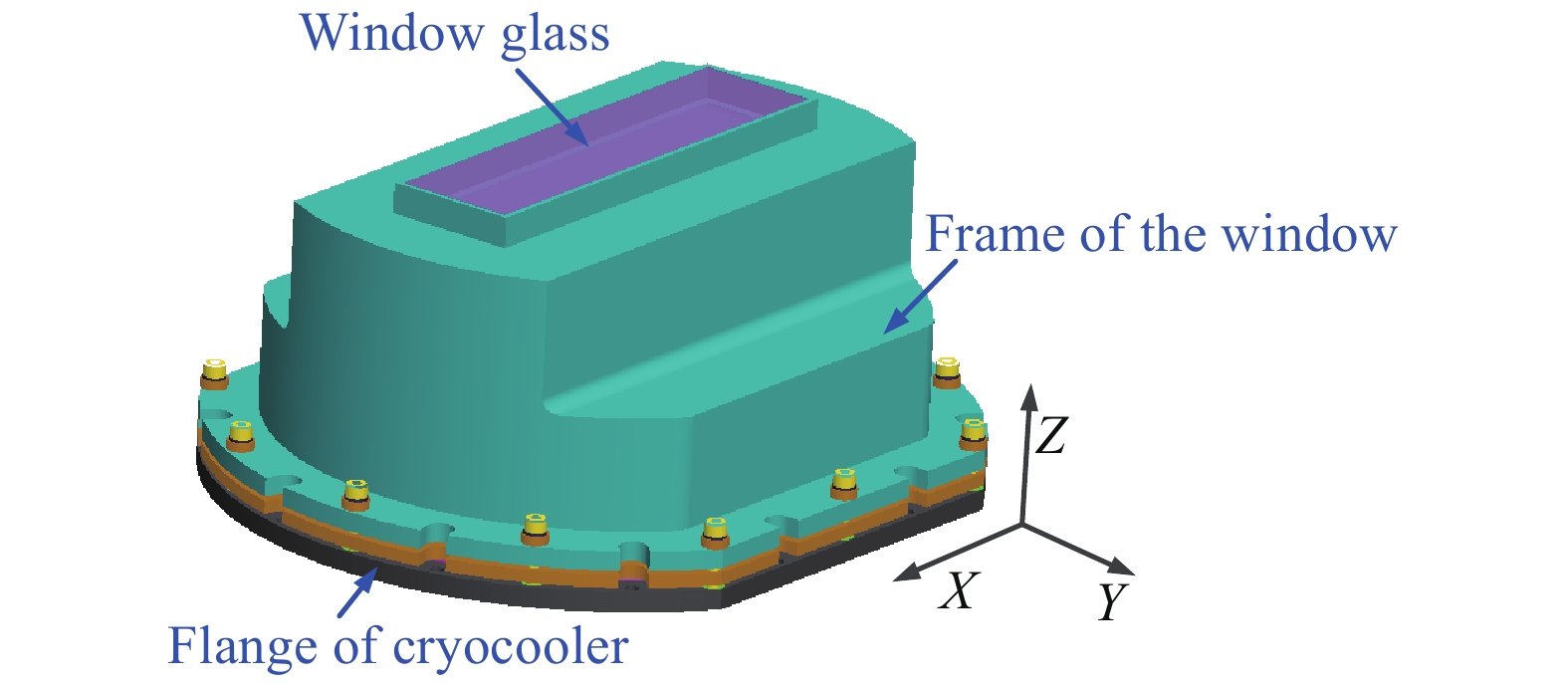
Set citation alerts for the article
Please enter your email address