High-Q lithium niobate (LN) optical micro-resonators are an excellent platform for future applications in optical communications, nonlinear optics, and quantum optics. To date, high-Q factors are typically achieved in LN using either dielectric masks or femtosecond laser ablation, while the more standard and commonly available lift-off metallic masks are often believed to lead to rough sidewalls and lowered Q factors. Here, we show that LN microring resonators with strong light confinement and intrinsic Q factors over 1 million can be fabricated using optimized lift-off metallic masks and dry etching processes, corresponding to a waveguide propagation loss of

- Chinese Optics Letters
- Vol. 19, Issue 6, 060010 (2021)
Abstract
1. Introduction
Lithium niobate (
To date, the majority of high-
The origins for exacerbated roughness in lift-off metallic masks are mainly two-fold. First, an unoptimized lithography process could cause mask fencing or even bridging at the lift-off edges, if the resist is not carefully tailored to have the desired undercut profile[
Sign up for Chinese Optics Letters TOC. Get the latest issue of Chinese Optics Letters delivered right to you!Sign up now
In this article, we show that, contrary to common beliefs, standard lift-off metallic masks can well produce LNOI micro-resonators with
2. Methods
The waveguide-coupled microring resonators are fabricated from a commercially available
Figure 1.(a)–(f) Device fabrication flowchart. (a) Fabrication starts with an x-cut LNOI substrate. (b) PMMA resist is first spin-coated and patterned with EBL. (c) NiCr etching mask is subsequently created by thermal evaporation, (d) followed by a standard lift-off process. (e) The patterned NiCr is then used as an etching mask to form the LN waveguides using an Ar+-based RIE process. (f) The residual NiCr is finally removed in Cr etchant. (g) SEM images of a fabricated microring resonator and a coupling bus waveguide. Insets show magnified cross-section (top) and top-down (bottom) views of the bus waveguide. (h) Simulated electric field (Ez) profiles of the fundamental TE modes in the straight bus waveguide (top) and the bending ring waveguide (bottom).
Figure 1(g) shows the scanning electron microscope (SEM) images of a fabricated microring resonator with a radius of 200 µm and a coupling waveguide. The rib-like waveguides feature a rib height of 240 nm, an unetched slab thickness of 340 nm, and a sidewall angle of
3. Results and Discussions
By performing step-by-step SEM examinations of the device cross-section profiles (Fig. 2), we show that the roughness in the lift-off metallic masks mainly originates from non-ideal resist profiles and can be largely eliminated by optimizing the lithography and lift-off processes. The left column of Fig. 2 shows the PMMA and NiCr profiles during a typical, unoptimized lift-off mask preparation process. The cross-section SEM images are taken by cleaving the chip in the direction perpendicular to the waveguides after each step. The SEM images show different structures, since they are taken from different areas of the chip due to uncertainties in hand cleavage positions. Nevertheless, the images shown in each column are from the same chip and still provide important insights for optimizing the lift-off processes step by step. We find that although the PMMA profile right after EBL looks almost perfectly vertical [Fig. 2(a)], it often experiences substantial deformation during the thermal evaporation process, which in turn leads to an overcut resist profile [Fig. 2(c)]. As a result, NiCr is deposited not only at the bottom surface, but also on the resist sidewalls, which ultimately translates into fencing features on the final lift-off masks [Fig. 2(e), showing top-down view]. Such features are typically hundreds of nanometers in size and will be directly transferred into the sidewall roughness of the final LN devices.
Figure 2.Step-by-step SEM examinations of the lift-off processes. (a), (b) Cross-section profiles of the PMMA resist after EBL. (c), (d) Cross-section profiles after thermal evaporation. (e), (f) Top-down views of the final NiCr masks. The left column [(a), (c), and (e)] shows a typical unoptimized lift-off process with overcut resist profiles and mask fencing features, whereas the right column [(b), (d), and (f)] corresponds to the optimized process with smooth mask profiles. The left part of PMMA resist in (c) was accidentally detached from the substrate during the cleaving step.
Figure 3.(a) Experimental setup for LN microring resonator characterization. FPC, fiber polarization controller; DUT, device under test; PD, photodetector. Measured optical transmission spectra for typical microring resonators using (b) unoptimized and (c) optimized fabrication processes. (d) and (e) Zoom-in views of (b) and (c) showing critically coupled resonances. Blue dots show the measured data, and red curves correspond to the Lorentzian fits, indicating intrinsic Q factors of 1.4 × 105 and 1.1 × 106 for unoptimized and optimized metallic masks, respectively.
We show that the rough features on the NiCr masks can be significantly reduced by optimizing each fabrication step in the lift-off process, as shown in the right column of Fig. 2. First, we create an undercut PMMA resist profile by fine tuning the PMMA film thickness, EBL exposure energy, and development time [Fig. 2(b)]. For the micron-scale waveguides shown in this paper, we use a 1.3 µm thick PMMA layer (950 A11), with an EBL dose of
We characterize the
4. Conclusions
In conclusion, we have demonstrated LN microring resonators with intrinsic
References
[1] L. Arizmendi. Photonic applications of lithium niobate crystals. Phys. Status Solidi, 201, 253(2004).
[2] A. Boes, B. Corcoran, L. Chang, J. Bowers, A. Mitchell. Status and potential of lithium niobate on insulator (LNOI) for photonic integrated circuits. Laser Photon. Rev., 12, 1700256(2018).
[3] J. Lin, F. Bo, Y. Cheng, J. Xu. Advances in on-chip photonic devices based on lithium niobate on insulator. Photon. Res., 8, 1910(2020).
[4] A. Rao, S. Fathpour. Heterogeneous thin-film lithium niobate integrated photonics for electrooptics and nonlinear optics. IEEE J. Sel. Top. Quantum Electron., 24, 8200912(2018).
[5] C. Wang, M. Zhang, X. Chen, M. Bertrand, A. Shams-Ansari, S. Chandrasekhar, P. Winzer, M. Lončar. Integrated lithium niobate electro-optic modulators operating at CMOS-compatible voltages. Nature, 562, 101(2018).
[6] B. S. Elkus, K. Abdelsalam, A. Rao, V. Velev, S. Fathpour, P. Kumar, G. S. Kanter. Generation of broadband correlated photon-pairs in short thin-film lithium-niobate waveguides. Opt. Express, 27, 38521(2019).
[7] J. Zhao, C. Ma, M. Rusing, S. Mookherjea. High quality entangled photon pair generation in periodically poled thin-film lithium niobate waveguides. Phys. Rev. Lett., 124, 163603(2020).
[8] M. He, M. Xu, Y. Ren, J. Jian, Z. Ruan, Y. Xu, S. Gao, S. Sun, X. Wen, L. Zhou, L. Liu, C. Guo, H. Chen, S. Yu, L. Liu, X. Cai. High-performance hybrid silicon and lithium niobate Mach–Zehnder modulators for 100 Gbit s−1 and beyond. Nat. Photon., 13, 359(2019).
[9] M. Zhang, C. Wang, R. Cheng, A. Shams-Ansari, M. Lončar. Monolithic ultra-high-Q lithium niobate microring resonator. Optica, 4, 1536(2017).
[10] R. Wu, J. Zhang, N. Yao, W. Fang, L. Qiao, Z. Chai, J. Lin, Y. Cheng. Lithium niobate micro-disk resonators of quality factors above 107. Opt. Lett., 43, 4116(2018).
[11] R. Luo, H. Jiang, S. Rogers, H. Liang, Y. He, Q. Lin. On-chip second-harmonic generation and broadband parametric down-conversion in a lithium niobate microresonator. Opt. Express, 25, 24531(2017).
[12] H. Liang, R. Luo, Y. He, H. Jiang, Q. Lin. High-quality lithium niobate photonic crystal nanocavities. Optica, 4, 1251(2017).
[13] J. Lu, J. B. Surya, X. Liu, A. W. Bruch, Z. Gong, Y. Xu, H. X. Tang. Periodically poled thin-film lithium niobate microring resonators with a second-harmonic generation efficiency of 250,000/W. Optica, 6, 1455(2019).
[14] J. Y. Chen, Z. H. Ma, Y. M. Sua, Z. Li, C. Tang, Y. P. Huang. Ultra-efficient frequency conversion in quasi-phase-matched lithium niobate microrings. Optica, 6, 1244(2019).
[15] M. Zhang, B. Buscaino, C. Wang, A. Shams-Ansari, C. Reimer, R. Zhu, J. M. Kahn, M. Lončar. Broadband electro-optic frequency comb generation in a lithium niobate microring resonator. Nature, 568, 373(2019).
[16] C. Wang, M. Zhang, M. Yu, R. Zhu, H. Hu, M. Lončar. Monolithic lithium niobate photonic circuits for Kerr frequency comb generation and modulation. Nat. Commun., 10, 978(2019).
[17] Y. He, Q. F. Yang, J. Ling, R. Luo, H. Liang, M. Li, B. Shen, H. Wang, K. Vahala, Q. Lin. Self-starting bi-chromatic LiNbO3 soliton microcomb. Optica, 6, 1138(2019).
[18] J. Holzgrafe, N. Sinclair, D. Zhu, A. Shams-Ansari, M. Colangelo, Y. Hu, M. Zhang, K. K. Berggren, M. Lončar. Cavity electro-optics in thin-film lithium niobate for efficient microwave-to-optical transduction. Optica, 7, 1714(2020).
[19] T. P. McKenna, J. D. Witmer, R. N. Patel, W. Jiang, R. Van Laer, P. Arrangoiz-Arriola, E. A. Wollack, J. F. Herrmann, A. H. Safavi-Naeini. Cryogenic microwave-to-optical conversion using a triply resonant lithium-niobate-on-sapphire transducer. Optica, 7, 1737(2020).
[20] L. Shao, M. Yu, S. Maity, N. Sinclair, L. Zheng, C. Chia, A. Shams-Ansari, C. Wang, M. Zhang, K. Lai, M. Lončar. Microwave-to-optical conversion using lithium niobate thin-film acoustic resonators. Optica, 6, 1498(2019).
[21] Z. Yu, X. Sun. Acousto-optic modulation of photonic bound state in the continuum. Light Sci. Appl., 9, 1(2020).
[22] Y. Hu, M. Yu, D. Zhu, N. Sinclair, A. Shams-Ansari, L. Shao, J. Holzgrafe, E. Puma, M. Zhang, M. Lončar. Reconfigurable electro-optic frequency shifter(2020).
[23] C. Wang, M. Zhang, B. Stern, M. Lipson, M. Lončar. Nanophotonic lithium niobate electro-optic modulators. Opt. Express, 26, 1547(2018).
[24] K. Luke, P. Kharel, C. Reimer, L. He, M. Lončar, M. Zhang. Wafer-scale low-loss lithium niobate photonic integrated circuits. Opt. Express, 28, 24452(2020).
[25] J. Zhang, Z. Fang, J. Lin, J. Zhou, M. Wang, R. Wu, R. Gao, Y. Cheng. Fabrication of crystalline microresonators of high quality factors with a controllable wedge angle on lithium niobate on insulator. Nanomaterials, 9, 1218(2019).
[26] R. Gao, H. Zhang, F. Bo, W. Fang, Z. Hao, N. Yao, J. Lin, J. Guan, L. Deng, M. Wang, L. Qiao, Y. Cheng. Ultrahigh quality-factor microresonators fabricated in pristine lithium niobate thin film for efficient nonlinear optics applications(2021).
[27] D. Berkoh, S. Kulkarni. Challenges in lift-off process using camp negative photoresist in III–V IC fabrication. IEEE Trans. Semicond. Manuf., 32, 513(2019).
[28] Y. Liu, H. Li, J. Liu, S. Tan, Q. Lu, W. Guo. Low Vπ thin-film lithium niobate modulator fabricated with photolithography. Opt. Express, 29, 6320(2021).
[29] R. Wolf, I. Breunig, H. Zappe, K. Buse. Scattering-loss reduction of ridge waveguides by sidewall polishing. Opt. Express, 26, 19815(2018).
[30] S. Y. Siew, E. J. H. Cheung, H. Liang, A. Bettiol, N. Toyoda, B. Alshehri, E. Dogheche, A. J. Danner. Ultra-low loss ridge waveguides on lithium niobate via argon ion milling and gas clustered ion beam smoothening. Opt. Express, 26, 4421(2018).
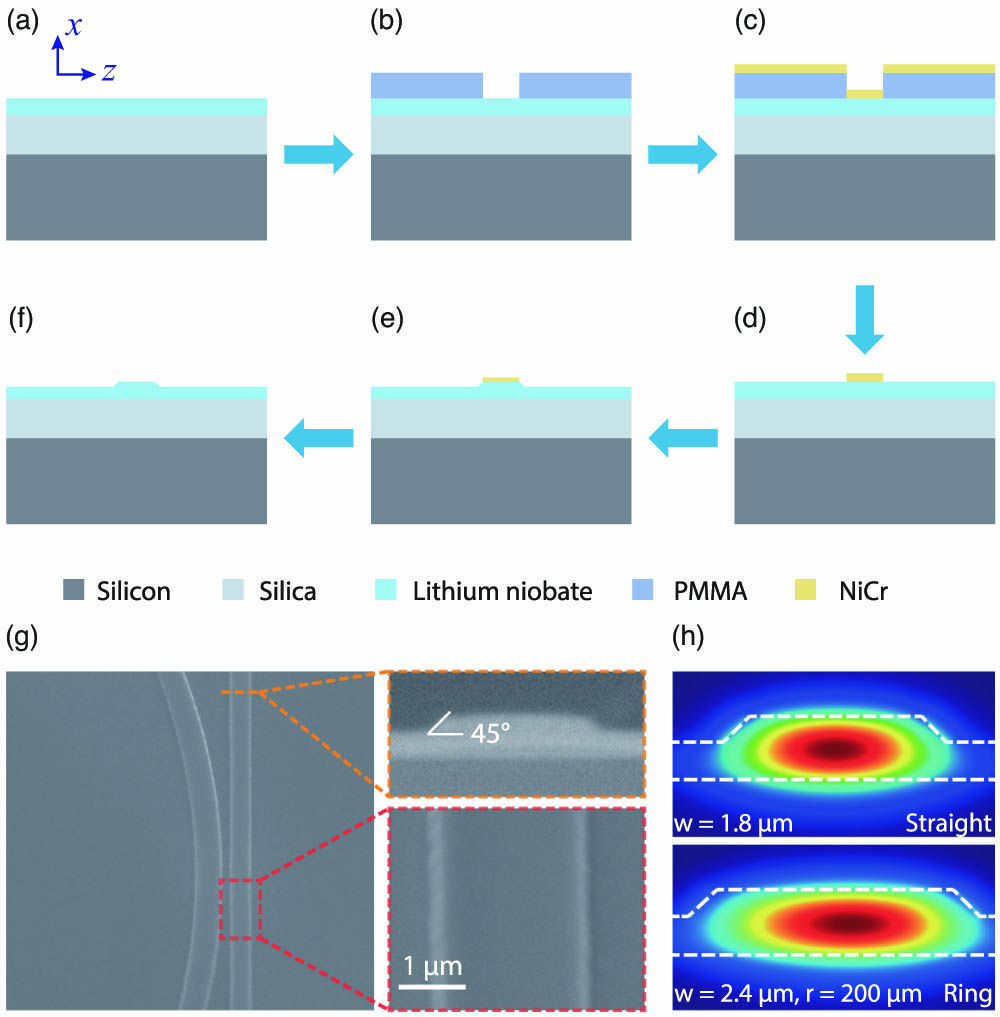
Set citation alerts for the article
Please enter your email address