Hang Zhou, Jingrong Yan, Jialin Li, Huan Ge, Tao Zhu, Bingke Zhang, Shucheng Chang, Junmin Sun, Xue Bai, Xiaoguang Wei*, and Fei Yang
Abstract
The comparison of domestic and foreign studies has been utilized to extensively employ junction termination extension (JTE) structures for power devices. However, achieving a gradual doping concentration change in the lateral direction is difficult for SiC devices since the diffusion constants of the implanted aluminum ions in SiC are much less than silicon. Many previously reported studies adopted many new structures to solve this problem. Additionally, the JTE structure is strongly sensitive to the ion implantation dose. Thus, GA-JTE, double-zone etched JTE structures, and SM-JTE with modulation spacing were reported to overcome the above shortcomings of the JTE structure and effectively increase the breakdown voltage. They provided a theoretical basis for fabricating terminal structures of 4H-SiC PiN diodes. This paper summarized the effects of different terminal structures on the electrical properties of SiC devices at home and abroad. Presently, the continuous development and breakthrough of terminal technology have significantly improved the breakdown voltage and terminal efficiency of 4H-SiC PiN power diodes.Introduction
A good rectifier should have high voltage resistance, low current leakage, and high current handling ability within power electronic devices. The 4H-SiC PiN diode, a bipolar power diode, is significant in the high-voltage and high-power rectification fields, broadening its application prospects and profound development potential[1−4]. Due to its high voltage resistance and ultrahigh power density, the 4H-SiC PiN power diode has gradually replaced the traditional silicon-based high-power devices in power rectifiers above 3 kV and ultra-high voltage applications (>10 kV). Compared with the Si-PiN power diode, 4H-SiC PiN has numerous advantages: (1) higher breakdown voltage, switching speed, current density, and tolerance for high junction temperatures, (2) open-state characteristics of high current density, and (3) off-state characteristics of low reverse leakage[5, 6].
However, the edge electric field concentration effect restricts the breakdown voltage for practical devices[7, 8]. The curvature at the edge of the P−N junction is very small due to the low thermal diffusivity of doping atoms in silicon carbide (SiC), resulting in a breakdown at the edge of the device. Studies have found that the terminal structure determines the breakdown voltage of the 4H-SiC PiN diode because the terminal mesa-construction can effectively improve the surface breakdown voltage and reduce the edge capacitance and inductance[9].
In recent years, 4H-SiC PiN power diodes have been extensively studied. Although a few good results were achieved, numerous challenges remain within the key technologies for device manufacture. A proper edge terminal structure design is a critical device property required to achieve ultrahigh voltages[10]. Moreover, reducing the electric field crowding at junction edges is required to realize the full potential of the materials. Several junction termination extension (JTE) structures, such as implanted JTE, mesa-combined JTE, and etched JTE, are considered promising for 4H-SiC. Furthermore, space-modulated junction termination extension (SM-JTE), multiple-floating-zone junction termination extension (MFZ-JTE), JTE with boron diffusion, and smooth tapered grayscale photojournalist JTE have been proposed recently to obtain a high breakdown voltage range with a wide JTE dose since the impurity dose in a traditional single-zone junction termination extension (SZ-JTE) needs to be precisely controlled to obtain a high breakdown voltage[11]. However, a wide range of doses of JTE has been reported in the literature. Therefore, an extensive study on the breakdown characteristics of ultrahigh-voltage SiC devices is required to understand their basic physical characteristics. This study reviewed the terminal structure of 4H-SiC PiN diodes and focused on the most extensively investigated JTE structures.
Structure of the PiN diode
The 4H-SiC PiN diode structure is generally mounted on an N+ conductive substrate. The low doping n-drift layer is grown using epitaxy as the i-zone. Additionally, the P+ anode zone layer can be formed using ion implantation or a continuous epitaxy growth method. The i-zone, the active zone of the devices, bears the high reverse breakdown voltage and carries the lower forward voltage drop through the conductance modulation effect. For an ideal SiC power device, the breakdown voltage depends on the thickness and doping concentration of the i-zone, and the ability to bear high pressure primarily depends on the depletion extent of the i-zone[12]. However, the edge electric field concentration effect restricts the breakdown voltage for practical devices. Therefore, the edge terminal configuration design is a key point in studying 4H-SiC PiN diodes. The terminal structure can extend the depletion layer to alleviate the electric field concentration effect at the edge of the main junction, effectively improving the breakdown voltage of the device. As shown in Fig. 1, the common terminal technologies include the field plate, guard ring, and JTE technologies[13].
![(Color online) Schematic diagram of a PiN diode with different terminal structures[13].](/Images/icon/loading.gif)
Figure 1.(Color online) Schematic diagram of a PiN diode with different terminal structures[13].
Planar and mesa structures are the two basic structures of PiN diodes, as shown in Fig. 2. Planar structure diodes can be easily fabricated using conventional planar processes. In contrast, mesa structure diodes are fabricated using wet or dry etching. Furthermore, mesa structure diodes are prepared to remove the bending part of the plane junction and improve the breakdown voltage. Additionally, they can reduce the edge capacitance and improve the working frequency.
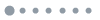
Figure 2.(Color online) Planar and mesa structure of PiN diodes.
Research on the terminal structure of PiN diodes
Investigation of the 4H-SiC PiN diode began in the 1990s. The 4H-SiC PiN diode has become a primary power electronic device, particularly in ultrahigh voltage applications, due to its simple and mature process advantages and continuous optimization and improvement of junction terminal technology[14−16]. In 2001, Cree Inc. reported a 4H-SiC PiN diode with a breakdown voltage in the range of 12–19 kV,the cross-sectional structure of the PiN diode is shown in Fig. 3[17]. The maximum breakdown voltage of 19 kV is the highest among all semiconductor devices developed since the birth of semiconductors. The terminal structure was etched using the epitaxial layer around the main junction, and the shallow mesa-JTE structure was formed using ion implantation. A mesa structure with a depth of 1 and a 500 μm long JTE is shown in Fig. 3.
![(Color online) The cross-sectional structure of a 4H-SiC PiN diode with a shallow mesa JTE[17].](/Images/icon/loading.gif)
Figure 3.(Color online) The cross-sectional structure of a 4H-SiC PiN diode with a shallow mesa JTE[17].
Additionally, the n-drift layer of PiN diodes was prepared with two different thicknesses and doping concentrations, as shown in Table 1. A high breakdown voltage of 14.9 kV and a low forward voltage Vf of 4.4 V at 100 A/cm2 were realized in the Type A diode. Additionally, the highest breakdown voltage of 19.5 kV and a low Vf of 6.6 V at 100 A/cm2 were realized in the Type B diode. The reverse recovery time, trr, was very small, about 34 and 43 ns for Type A and B diodes, respectively. The result indicated that the breakdown voltage and trr increased with the thickness of the i-zone, but the positive guide voltage dropped.
Table Infomation Is Not Enable
In 2001, Sheridan et al. studied the breakdown characteristics of SiC-PiN diodes with SZ-JTE and multi-zone junction termination extension (MZ-JTE) terminal structures. Based on planar SZ-JTEs, the optimal breakdown voltage range of the device under different drift zone (i-zone) concentrations was observed to broaden and saturate with a decrease in the drift zone concentration, as shown in Fig. 4(a)[11]. The simulation results indicated that the breakdown voltage varied with the JTE dose (JTE concentration) forming a "triangular" sharp peak curve, as shown in Fig. 4(b)[11].
![(a) Dependence of breakdown voltage on the variation in JTE doping for several epi-layer concentrations. (b) Simulated dependence of mesa-JTE breakdown voltage on JTE doping concentrations[11].](/Images/icon/loading.gif)
Figure 4.(a) Dependence of breakdown voltage on the variation in JTE doping for several epi-layer concentrations. (b) Simulated dependence of mesa-JTE breakdown voltage on JTE doping concentrations[11].
In 2005, Perez et al. comparatively studied various planar terminal technologies, mainly JTE terminals, FLR terminals, and their composite structures, based on a 4H-SiC PiN diode with a breakdown voltage of 1.7 kV. The schematic cross-sectional view of a 4H-SiC PiN diode with a single JTE structure as shown in Fig. 5[18]. Field-ring-assisted junction extension terminals (GA-JTE) can effectively increase the breakdown voltage of devices with lower JTE concentrations and broaden the JTE optimal value range. However, JTE terminals are sensitive to the doping concentration in the injection dose. Composite terminals are preferred to broaden the concentration window of the JTE optimal value and reduce the influence of interface charge on terminals.
![Schematic cross-sectional view of a 4H-SiC PiN diode with a single JTE structure[18].](/Images/icon/loading.gif)
Figure 5.Schematic cross-sectional view of a 4H-SiC PiN diode with a single JTE structure[18].
In 2005, Cree Inc. reported a 4H-SiC PiN diode with a breakdown voltage of 15 kV and a 100 μm thick i-zone[19]. As shown in Fig. 6, the terminal structure was dry-etched to obtain a 3 μm deep mesa structure. Subsequently, aluminum ions were injected into the mesa structure and activated by annealing at 1600 °C to form the field limit ring. The electrical results showed that the positive guided voltage drop was 3.75 V at a current density of 100 A/cm2.
![(Color online) The cross-section of a 10 kV 4H-SiC PiN diode[19].](/Images/icon/loading.gif)
Figure 6.(Color online) The cross-section of a 10 kV 4H-SiC PiN diode[19].
A 4H-SiC PiN diode with a breakdown voltage of 10 kV was reported in 2008. The traditional cone structure was changed using a combination of wet and dry etching. The results showed that the mesa structure was 2 μm deep and the surface inclination angle was 70°. This terminal structure significantly alleviated the electric field concentration phenomenon and improved the breakdown voltage, which could reach up to 10 kV. The process flow diagram is shown in Fig. 7[20].
![Process flow diagram[20].](/Images/icon/loading.gif)
Figure 7.Process flow diagram[20].
Furthermore, the effect of the length and dose of terminal JTEs on the breakdown voltage is discussed. The results indicated that the breakdown voltage gradually increased until it attained a regional saturation value of 200 μm with the increased JTE length. However, the JTE doping dose was very sensitive to the breakdown voltage, and the optimal doping dose was 1.0 × 1013 cm–2. This is because the JTE region was completely exhausted under the low reverse electric field at a lower doping dose, and breakdown occurred within the edge region of the device. However, the electric field breakdown occurred at the outer edge of the JTE region at a higher doping dose. As shown in Fig. 8, isopotential lines were widely distributed in the JTE region under appropriate doping doses.
![(Color online) (a) Low doping dose (0.4 × 1013 cm−2), (b) optimal doping dose (1.6 × 1013 cm−2), (c) high doping dose (1.0 × 1013 cm−2)[20].](/Images/icon/loading.gif)
Figure 8.(Color online) (a) Low doping dose (0.4 × 1013 cm−2), (b) optimal doping dose (1.6 × 1013 cm−2), (c) high doping dose (1.0 × 1013 cm−2)[20].
In 2009, Ghandi et al. from the Royal Institute of Technology in Sweden successfully developed a high-voltage SiC-PiN diode with a dual-zone etched JTE terminal, the cross-sectional view of a fabricated circular optimally is shown in Fig. 9[21]. The breakdown voltage of the device was measured as 4.3 kV. The key step in achieving a high breakdown voltage was controlled etching in the epitaxially grown p-doped anode layer to reach an optimum dopant dose of 1.2 × 1013 cm−2 in the JTE. Electroluminescence revealed a localized avalanche breakdown that agrees with the device simulation. The diodes with double-zone etched JTEs had a higher breakdown voltage and less sensitivity to the varying processing conditions than the diodes with single-zone etched JTEs[22, 23].
![The cross-sectional view of a fabricated circular optimally dosed double-zone JTE pn+ diode with a 200-µm diameter for anode contact[21].](/Images/icon/loading.gif)
Figure 9.The cross-sectional view of a fabricated circular optimally dosed double-zone JTE pn+ diode with a 200-µm diameter for anode contact[21].
In 2012, Niwa et al. from Kyoto University in Japan found that the breakdown voltage of 4H-SiC PiN diodes for SM-JTE terminals with modulation spacing was 15 kV, the schematic diagram of the terminal structure is shown in Fig. 10[24]. Their study was based on the experimental study of oxidation annealing of nitric oxide deposition by Noborio et al. and the use of 4H-SiC MOSFET to extract the fixed charge data of SiO2 and P- and N-type SiC interfaces. The simulation and experimental comparison of the JTE terminals within a single region found that the interface charge would reduce the effective dose of JTE, drifting the JTE breakdown voltage curve and reducing the breakdown voltage. Moreover, Niwa et al. used SM-JTE terminals to broaden the JTE optimal concentration window to avoid the interface charge influence. The polar tube comparative study of two-zone junction termination extension (TZ-JTE), two-zone junction termination extension with the field ring (TZ-JTE+FR), and SM-JTE terminals showed that their simulation results could effectively improve the breakdown voltage and broaden the window for an optimum JTE concentration. However, the actual interface charge at the interface of the terminals and the oxide layer drifted the breakdown voltage–JTE concentration curve, significantly reducing the breakdown voltage of the device[25−29].
![(Color online) Terminal structure and breakdown characteristics of 15 kV SiC-PiN diodes with SZ-JTE and SM-JTE[24].](/Images/icon/loading.gif)
Figure 10.(Color online) Terminal structure and breakdown characteristics of 15 kV SiC-PiN diodes with SZ-JTE and SM-JTE[24].
In 2014, Kaji et al. reported a SiC-PiN diode having five different n-layer thicknesses (i-layer or voltage-blocking layer) in the range of 48–268 μm[30]. Simultaneously, using the carrier-life time enhancement process obtained very low differential ON-resistances. Consequently, the sum of a nearly constant built-in voltage and a parabolic function could approximately express the forward current density-voltage characteristics. Moreover, an improved SM JTE structure enhanced lifetime, as shown in Fig. 11[30], a high blocking voltage (over 26.9 kV), and low differential ON-resistance of 9.7 mΩ·cm2 were achieved by using a 268 μm-thick n-layer with a (1–2) × 1014 cm−3 doping concentration.
![(Color online) The improved SM JTE structure employed for PiN diode simulation[30].](/Images/icon/loading.gif)
Figure 11.(Color online) The improved SM JTE structure employed for PiN diode simulation[30].
In 2018, Asllani et al. reported a high breakdown voltage of 10 kV for 4H-SiC bipolar diodes, as shown in Fig. 12[31]. The actual breakdown voltage of the selected devices was between 7 and 8 kV. As shown in Fig. 12, PiN diodes were fabricated using ion beam services on N+ substrates and a 110 µm thick epilayer with a 7 × 1014 cm−3 doping concentration. The edge termination of the PiN diodes included 400 µm long mesa and JTEs, surrounded by six JTE-rings with increasing spacing between them (Di).
![(Color online) Schematic cross-view of the fabricated PiN diode[31].](/Images/icon/loading.gif)
Figure 12.(Color online) Schematic cross-view of the fabricated PiN diode[31].
Research on PiN diode terminal structures in China
Furthermore, domestic research on SiC-PiN terminal technology is deepening. As shown in Fig. 13, the Central South University of Forestry and Technology reported a SiC-PiN power diode with a planar terminal structure in 2011[32]. The results showed that the SZ-JTE structure had two electric field peaks, the volume and surface electric field peaks. The JTE length had to be approximately six times the thickness of the epitaxial layer to fully release the surface electric field and obtain the maximum reliable breakdown voltage. The results of electrical characterization showed that the forward voltage at room temperature was 3.75 V, the rated current was 8 A, and the breakdown voltage reached 1.7 kV.
![Schematic diagram of the planar PiN diode section[32].](/Images/icon/loading.gif)
Figure 13.Schematic diagram of the planar PiN diode section[32].
In 2013, Xi’an University of Electronic Science and Technology reported a 1.6 kV bipolar junction transistor (BJT) diode with a terminal structure that used surface etching, an ion implantation JTE, an auxiliary ring (AR), and a traditional method of combining joint isodose JTE structures around a protective ring structure, which the section of the JTE and AR structure is shown in Fig. 14[33]. The electric field distribution between the modulator edge and the pressure-resistant layer could be well-regulated using this structure. As shown in Fig. 14, the breakdown voltage of the structure was 1.6 kV, 83% of the ideal breakdown voltage, and the etching depth of the SiC process was 2 μm. This structure provides a reference for preparing terminal structures for PiN devices in the future.
![Section of the JTE and AR structure[33].](/Images/icon/loading.gif)
Figure 14.Section of the JTE and AR structure[33].
The terminal structure was completed by two etches to a depth of 1.5 μm. The terminal structure was formed after the second injection, which was 0.5 μm deep. The main JTE length was denoted as LM. The lengths of the second and third ARs were denoted as LA1 and LA2, respectively. The distance between LA1 and LA2 was D1, and the total LM was 450 μm. Additionally, the effects of the JTE length and dose on the breakdown voltage were discussed. The results showed that the breakdown voltage of the device increased with increased LM. When LM was smaller than the thickness of the depletion layer, the surface electric field was larger than the internal electric field. Additionally, the breakdown voltage was relatively small and gradually approached the ideal value with increasing LM. However, the breakdown voltage tended to saturation due to the edge electric field concentration of the JTE when LM exceeded 20 μm. The electric field within the main JTE region could rise steadily with increased voltage while ensuring that the edge peak electric field was protected due to the addition of the AR[34, 35].
In 2016, Li et al. from the Microstate Center of China Academy of Engineering Physics prepared an etched implanted JTE for high-voltage 4H-SiC PiN diodes, the schematic of cross-section of the SiC-PiN diode is shown in Fig. 15[36]. Unlike the traditional JTE structures, the proposed structure utilized multiple etching steps to achieve the optimal JTE concentration range. Simulation results showed that the etched implant JTE method could improve the breakdown voltage of SiC-PiN diodes. Additionally, it could provide a broad window for process freedom for the variation in parameters, such as implant dose and activation annealing conditions. The SiC-PiN diode prepared with etched implant JTE had the highest breakdown voltage at room temperature (4.5 kV) and a 4.6 V of forward on-state voltage.
![(Color online) Schematic of cross-section of a SiC-PiN diode with an etched implant JTE[36].](/Images/icon/loading.gif)
Figure 15.(Color online) Schematic of cross-section of a SiC-PiN diode with an etched implant JTE[36].
In 2016, Zhuzhou CRRC Times Equipment Technology Co., Ltd reported a SiC-PiN diode with a breakdown voltage of 4 kV[37]. The result showed that the SiC etching depth could reach 3.49 μm when the mesa-etching angle was 48°. As shown in Fig. 16, the terminal structure adopted this method of mesa etching and junction terminal combination, and the JTE was 100 μm long.
![SEM diagram of gently varying mesa[37].](/Images/icon/loading.gif)
Figure 16.SEM diagram of gently varying mesa[37].
Furthermore, the effect of JTE length and doping dose on the reverse breakdown voltage of a device was also considered in the design simulation process of the junction terminal structure. The JTE length is the distance from the beginning of the mesa bottom to the outside of the junction terminal. The relationship between JTE length and breakdown voltage was as follows: the JTE length was small initially, and the electric field intensity at the edge of the main junction was effectively alleviated as the JTE length increased, increasing the breakdown voltage. Furthermore, the local concentration effect of the electric field was fully alleviated, the electric field distribution area on the device surface was constant, and the breakdown voltage of the device was unchanged when the JTE length reached a certain value.
Additionally, the effect of the implantation dose on the reverse bias showed that the intensity of the inner electric field was the highest, and the breakdown occurred at the edge of the main junction when JTE doping was low. However, the peak electric field at the edge of the main junction outside the device was effectively reduced, the electric field intensity on both sides of JTE was almost equal, and the breakdown voltage of the device could reach its maximum value when JTE was optimally doped. Furthermore, the outer electric field of JTE increased significantly, and device breakdown occurred on the outer side of JTE when JTE doping was too high. The optimal doping dose of JTE determined using simulation was approximately in the range of 0.75 × 1013–1.5 × 1013 cm–2, as shown in Figs. 17(a) and 17(b)[37]. The results were similar to those reported at Xi'an University in 2013[33].
![(Color online) Effect of the JTE length (a) and doping dose (b) on the breakdown voltage[37].](/Images/icon/loading.gif)
Figure 17.(Color online) Effect of the JTE length (a) and doping dose (b) on the breakdown voltage[37].
In 2016, Zou et al. proposed a novel termination structure, an etched junction termination extension with floating guard rings and middle rings (E-JFs-MRs), the schematic of cross-section of four types of UHV PiN diode is shown in Fig. 18[38]. It was presented for ultrahigh-voltage (>10 kV) 4H-SiC PiN diodes to extend the JTE dose window and improve the breakdown voltage. The structure introduced a shallow etching process and middle ring structure to the conventional junction termination extension with floating guard rings (JFs). Subsequently, numerical device simulations were performed using Sentaurus TCAD tools. Compared with JFs, the JTE dose window (>15 kV) of the E-JFs-MRs was significantly extended by a ratio of 143% for the PiN diode based on the same N-type epitaxial layer with a thickness of 100 μm and an impurity concentration of 2 × 1014 cm–3.
![(Color online) Cross-section of four types of UHV PiN diodes[38].](/Images/icon/loading.gif)
Figure 18.(Color online) Cross-section of four types of UHV PiN diodes[38].
In 2017, etched JTE terminals with floating guard rings (FGRs) were studied at Tsinghua University. Moreover, the JTE concentration window was optimized, and SiC-PiN diodes were successfully fabricated. The measurements indicated the breakdown voltage could reach 4.6 kV while achieving significant uniformity and yield rates. Additionally, a forward voltage drop of 3.7 V was obtained[8] (Fig. 19).
![(Color online) The breakdown voltage versus the JTE dose[8].](/Images/icon/loading.gif)
Figure 19.(Color online) The breakdown voltage versus the JTE dose[8].
In 2017, Zhou et al. proposed an edge termination method, the guard-ring-assisted multi-step junction termination extension (MS-GR-JTE)[39] (Fig. 20). It was presented for ultrahigh voltage SiC power devices. Compared with other JTEs, the MS-GR-JTE created a step electric field distribution with significantly reduced peak electric field at the corners and edges of the device, resulting in a superior breakdown voltage performance with wide tolerances of the JTE dose and SiC surface charges. According to the numerical simulations based on a 100-µm-thick epilayer, an optimized MS-GR-JTE had a 15 kV breakdown voltage with wide tolerances of 1.3 × 1012 cm−2 to the JTE dose and 6.1 × 1012 cm−2 to the positive surface charges. Additionally, these tolerances were superior compared to other JTEs.
![(Color online) Schematic structures of MS-GR-JTE[39].](/Images/icon/loading.gif)
Figure 20.(Color online) Schematic structures of MS-GR-JTE[39].
In 2021, a 6.5 kV PiN diode was reported at the University of Electronic Science and Technology of China[40]. The results showed a SiC etching process capacity with an etching depth exceeding 2 μm and a 45° etching table inclination angle. The terminal adopted the coincidence mode of the JTE region and auxiliary multiple field-limiting rings regulating the electric field. The dose ratio of the JTE1 and JTE2 zones determined using simulation was 3 : 2. The lengths of JTE1 and JTE2 were 150 and 100 μm, respectively. The terminal structure is shown in Fig. 21.
![(Color online) Schematic diagram of the MAM-JTE structural section[40].](/Images/icon/loading.gif)
Figure 21.(Color online) Schematic diagram of the MAM-JTE structural section[40].
The terminal was divided into five effective doping regions with decreasing doping concentrations, alleviating the electric field change in the depletion region of the main junction[41−45]. The lateral variable doping effect reduced the peak electric field at the edge, enhancing the protection of the main junction and transition regions. Electrical test results showed that at room temperature, the forward voltage was 3.2 V, the current density was 100 A/cm2, the forward voltage was 3.78 V, the reverse breakdown voltage was 7.4 kV, and the reverse leakage current was 10 μA, reaching 93% of the ideal plane junction breakdown voltage. The test results are shown in Fig. 22[40].
![(Color online) I–V and inverse characteristic curves[40].](/Images/icon/loading.gif)
Figure 22.(Color online) I–V and inverse characteristic curves[40].
Problems solved and problems that remain
A major problem in current JTE terminal studies is to suppress the interface charge effect on the JTE concentration and ensure the stability of the breakdown voltage of the device. According to the present review, the current solutions mainly have two approaches. First, the complex multiple composite JTE terminal design was used to effectively expand the optimal JTE concentration window, which was used to reduce the interface charge impact on the breakdown characteristics of the device. However, the multiple composite terminals can require multiple mask injections, increasing the cost and leading to potential process risks due to the complex process steps. Second, MZ-TE combined with SM-JTE is a promising termination technology for realizing ultrahigh-voltage 4H-SiC power devices considering the ease of the fabrication process and the effect. The effect of termination structures on the electrical properties of SiC devices is summarized in Table 2.
The comparison of domestic and foreign studies has been utilized to extensively employ JTE structures for power devices. However, achieving a gradual doping concentration change in the lateral direction is difficult for SiC devices since the diffusion constants of the implanted aluminum ions in SiC are much less than silicon. Many previously reported studies adopted many new structures to solve this problem. Additionally, the JTE structure is strongly sensitive to the ion implantation dose. Thus, GA-JTE, double-zone etched JTE structures, and SM-JTE with modulation spacing were reported to overcome the above shortcomings of the JTE structure and effectively increase the breakdown voltage. They provided a theoretical basis for fabricating terminal structures of 4H-SiC PiN diodes.
Table Infomation Is Not Enable
Conclusion
This paper summarized the effects of different terminal structures on the electrical properties of SiC devices. Presently, the continuous development and breakthrough of terminal technology have significantly improved the breakdown voltage and terminal efficiency of 4H-SiC PiN power diodes. However, problems in the study of key technology, such as the micro-grooving effect in mesa etching and surface etching defects, restrict the performance improvement and reliability applications of 4H-SiC PiN power diodes. Additionally, the mask design of a multi-zone structure is generally very complex, increasing the requirements for process realization. Therefore, while considering the breakdown efficiency and reliability design, it is necessary to study the practicability of the preparation technology further and experimentally verify ultrahigh-voltage 4H-SiC PiN power diodes.
References
[1] B J Baliga. Analysis of a high-voltage merged p-i-n/Schottky (MPS) rectifier. IEEE Electron Device Lett, 8, 407(1987).
[2] X Li, K Tone, L Fursin et al. Multistep junction termination extension for SiC power devices. Electron Lett, 37, 392(2001).
[3] J B Fedison, N Ramungul, T P Chow et al. Electrical characteristics of 4.5 kV implanted anode 4H-SiC p-i-n junction rectifiers. IEEE Electron Device Lett, 22, 130(2001).
[4] R Singh, J A Cooper, M R Melloch et al. SiC power Schottky and PiN diodes. IEEE Trans Electron Devices, 49, 665(2002).
[5] T Funaki, T Kimoto, T Hikihara. Evaluation of high frequency switching capability of SiC Schottky barrier diode, based on junction capacitance model. IEEE Trans Power Electron, 23, 2602(2008).
[6] M Wolborski, M Bakowski, A Schöner. Analysis of bulk and surface components of leakage current in 4H-SiC PiN MESA diodes. Microelectron Eng, 83, 75(2006).
[7] H Niwa, G Feng, J Suda et al. Breakdown characteristics of 20 kV-class 4H-SiC PIN diodes with improved junction termination structures, 381(2012).
[8] C N Zhou, Y Wang, R F Yue et al. Step JTE, an edge termination for UHV SiC power devices with increased tolerances to JTE dose and surface charges. IEEE Trans Electron Devices, 64, 1193(2017).
[9] V A K Temple, W Tantraporn. Junction termination extension for near-ideal breakdown voltage in p-n junctions. IEEE Trans Electron Devices, 33, 1601(1986).
[10] B J Baliga. Power semiconductor devices. Boston: PWS, Publishing Co.(1995).
[11] D C Sheridan, G F Niu, J D Cressler. Design of single and multiple zone junction termination extension structures for SiC power devices. Solid State Electron, 45, 1659(2001).
[12] T Kimoto, K Danno, S D Jun. Lifetime-killing defects in 4H-SiC epilayers and lifetime control by low-energy electron irradiation. Phys Stat Sol (b), 245, 1327(2008).
[13] P B Klein, B V Shanabrook, S W Huh et al. Lifetime-limiting defects in n-4H-SiC epilayers. Appl Phys Lett, 88, 052110(2006).
[14] B A Hull, M K Das, J T Richmond et al. A 180 amp/4.5 kV 4H-SiC PiN diode for high current power modules, 1(2006).
[15] K Nakayama, A Tanaka, M Nishimura et al. Characteristics of a 4H-SiC pin diode with carbon implantation/thermal oxidation. IEEE Trans Electron Devices, 59, 895(2012).
[16] D Okamoto, Y Tanaka, T Mizushima et al. 13-kV, 20-a 4H-SiC PiN diodes for power system applications. Mater Sci Forum, 778-780, 855(2014).
[17] Y Sugawara, D Takayama, K Asano et al. 12-19 kV 4H-SiC pin diodes with low power loss. Proceedings of the 13th International Symposium on Power Semiconductor Devices & ICs. IPSD '01 (IEEE Cat. No. 01CH37216), 27(2002).
[18] R Perez, D Tournier, A Perez-Tomas et al. Planar edge termination design and technology considerations for 1.7-kV 4H-SiC PiN diodes. IEEE Trans Electron Devices, 52, 2309(2005).
[19] M K Das, B A Hull, J T Richmond et al. Ultra high power 10 kV, 50 A SiC PiN diodes. Proceedings of ISPSD '05. The 17th International Symposium on Power Semiconductor Devices and ICs, 299(2005).
[20] T Hiyoshi, T Hori, S D Jun et al. Simulation and experimental study on the junction termination structure for high-voltage 4H-SiC PiN diodes. IEEE Trans Electron Devices, 55, 1841(2008).
[21] R Ghandi, B Buono, M Domeij et al. High-voltage 4H-SiC PiN diodes with etched junction termination extension. IEEE Electron Device Lett, 30, 1170(2009).
[22] R Ghandi, H S Lee, M Domeij et al. Fabrication of 2700-V 12 mΩ·cm2 non ion-implanted 4H-SiCBJTs with common-emitter current gain of 50. IEEE Electron Device Lett, 29, 1135(2008).
[23] A O Konstantinov, Q Wahab, N Nordell et al. Ionization rates and critical fields in 4H silicon carbide. Appl Phys Lett, 71, 90(1997).
[24] H Niwa, F Gan, S D Jun et al. Breakdown characteristics of 15-kV-class 4H-SiC PiN diodes with various junction termination structures. IEEE Trans Electron Devices, 59, 2748(2012).
[25] K Kawahara, S D Jun, T Kimoto. Analytical model for reduction of deep levels in SiC by thermal oxidation. J Appl Phys, 111, 053710(2012).
[26] J Luts, H Schlangenotto, U Scheuermann et al. Semiconductor power devices. Springer-Verlag(2011).
[27] M Noborio, S D Jun, T Kimoto. P-channel MOSFETs on 4H-SiC {0001} and nonbasal faces fabricated by oxide deposition and N2O annealing. IEEE Trans Electron Devices, 56, 1953(2009).
[28] R Ghandi, B Buono, M Domeij et al. Surface-passivation effects on the performance of 4H-SiC BJTs. IEEE Trans Electron Devices, 58, 259(2011).
[29] T Kimoto, Y Kanzaki, M Noborio et al. Interface properties of metal–oxide–semiconductor structures on 4H-SiC {0001} and (1120) formed by N2O oxidation. Jpn J Appl Phys, 44, 1213(2005).
[30] N Kaji, H Niwa, S D Jun et al. Ultrahigh-voltage SiC p-i-n diodes with improved forward characteristics. IEEE Trans Electron Devices, 62, 374(2015).
[31] S Hino, H Hatta, K Sadamatsu et al. Demonstration of SiC-MOSFET embedding Schottky barrier diode for inactivation of parasitic body diode. Mater Sci Forum, 897, 477(2017).
[32] F S Zhang. Simulation and fabrication of high-voltage 4H-SiC PiN diode with JTE. Chinese Journal of Coputational Physics, 28, 306(2011).
[33] L Yuan, Y M Zhang, Y M Zhang et al. Design of an effective junction termination structure for 4H-SiC BJTs (in Chinese), 71(2013).
[34] Y Okuto, C R Crowell. Threshold energy effect on avalanche breakdown voltage in semiconductor junctions. Solid State Electron, 18, 161(1975).
[35] K G McKay. Avalanche breakdown in silicon. Phys Rev, 94, 877(1954).
[36] J T Li, C Q Xiao, X L Xu et al. High-voltage 4H-SiC PiN diodes with the etched implant junction termination extension. J Semicond, 38, 024003(2017).
[37] J Wu, G Y Wang, C Yang et al. Development of high quality factor SiC PiN diode. High Power Converter Technology, 1096(2016).
[38] X Zou, R F Yue, Y Wang. Etched junction termination extension with floating guard rings and middle rings for ultrahigh-voltage 4H-SiC PiN diodes, 418(2016).
[39] X Zou, R F Yue, Y Wang. Development of 3.6 kV 4H-SiC PiN power diodes, 1(2017).
[40] M L Tao, X C Deng, R Hu et al. Design, fabrication and characterization of 6.5kV/100A 4H-SiC PiN power rectifier, 228(2022).
[41] X C Deng, L J Li, J Wu et al. A multiple-ring-modulated JTE technique for 4H-SiC power device with improved JTE-dose window. IEEE Trans Electron Devices, 64, 5042(2017).
[42] R Hu, X C Deng, X J Xu et al. An improved composite JTE termination technique for ultrahigh voltage 4H-SiC power devices, 18(2020).
[43] M L Tao, X C Deng, H Wu et al. Design, fabrication and characterization of 10kV/100A 4H-SiC PiN power rectifier. Mater Sci Forum, 1014, 115(2020).
[44] Y Saitoh, T Masuda, H Michikoshi et al. V-groove trench gate SiC MOSFET with a double reduced surface field junction termination extensions structure. Jpn J Appl Phys, 58, SBBD11(2019).
[45] T Hirao, H Onose, Y S Kan et al. Edge termination with enhanced field-limiting rings insensitive to surface charge for high-voltage SiC power devices. IEEE Trans Electron Devices, 67, 2850(2020).