Abstract
The structure of a novel ring-shaped top-DBR etched microstructure VCSEL with a proton implantation high resistance region was designed. A ring column structure was formed from the upper electrode to the active region, which directly generated a hollow laser beam output. The optical field distribution of the etched microstructure VCSEL was calculated by FDTD software, and the obtained ring-shaped patterns maintained the hollow beam characteristics under the different mode numbers. We fabricated the etched microstructure VCSEL with a lasing wavelength of 848 nm at room temperature and investigated its performance. The threshold current was 0.27 A and the peak power was up to 170 mW. The near-field patterns of different currents clearly displayed hollow ring-shaped spots. The distribution curves of far-field light intensity matched the characteristics of a hollow beam as well. This novel VCSEL provides a new approach for the development of hollow beams and even array devices.Introduction
A hollow laser beam[1-2] is a kind of dark hollow beam,and its center intensity is zero. It has a number of special properties,including no heating effects,a barrel-shaped intensity distribution,and the ability to significantly reduce beam scattering. As a result,it has been widely used in optical information processing,optical micromanipulation[3],molecular science[4],and biomedicine[5]. Research on the generation and application of hollow laser beams has gradually become a topic of interest in scientific researchers. Several methods of generating hollow beam[6-7] have been reported,such as optical holography[8],transverse mode selection[9],geometrical optics[10-11],etc. These methods usually require a complex optical design process and sophisticated machining of optical components,resulting in long design cycles,correspondingly high laser costs,low excitation efficiencies,and narrow spectral ranges.
The vertical cavity surface emitting laser(VCSEL)is a kind of semiconductor lasers with unique advantages such as low threshold,no cavity surface damage,and circular symmetric spot[12-14]. It is widely used in optical interconnection,optical communication,LIDAR,face recognition,Augmented Reality(AR)/Virtual Reality(VR),and other fields[15-16]. As VCSEL has the characteristic that the light output direction is perpendicular to the substrate surface,the light output aperture is on the vertical surface of the laser. It is easy to control the transverse mode of the beam by changing the shape of the output aperture[17] and then realizing laser shaping. In recent years,it has gradually become the most potential hollow laser beam emission source[18].
In this article,we propose a new concept of using an etched microstructure VCSEL with a high-resistance area in the upper Distributed Bragg Reflector(DBR)to directly emit a hollow laser beam,to obtain a high-quality hollow laser beam more easily and directly. This structure utilizes the mode selection effect of artificial microstructure to reduce the effect of optical feedback gain in the central area to achieve mode control. A novel microstructure surface emitting laser and its hollow beam output are realized,and its transverse mode is simulated. An etched microstructure surface emitting laser with a high resistance region has been fabricated and its output characteristics have been tested and analyzed.
1 Device structure and simulation
In the conventional surface emitting laser structure,the overall semiconductor process from the light output window to the active gain region is made into a cylindrical structure. The output beam of the VCSEL with this structure is a circularly symmetric Gaussian beam[19]. The structure schematic of the etched microstructure surface emitting semiconductor laser with a high resistance region designed in this paper is shown in Fig. 1. A hollow ring column structure from the light outlet to the upper DBR is formed by the etching technique. The diameter of the etched hole is 50 μm. Then,H+ ions are implanted into the hole by the proton implantation technique. Due to the high resistance region formed by proton implantation,the current is effectively prevented from flowing through the central region. Carriers are limited in the ring structure,electrons and holes can only compound in this ring structure,which ensures that there is no gain effect in the central region,thus forming the ring laser oscillation more effectively,and then generating the hollow laser beam output. To ensure the ‘hollow’ effect of the beam,the etched area is injected with H+ ions instead of etching the active region into a circular ring. On the one hand,the region injected with H+ ions can play the role of electrical isolation and block the current from passing through,which can effectively suppress the optical feedback gain in the central area. On the other hand,etching the active region is bound to cause wall damage,resulting in unnecessary scattering. The selection of the proton implantation method will reduce the loss and improve the efficiency of the device. Therefore,this structure can more effectively realize the direct output of a high-quality hollow laser beam by VCSEL with a small aperture.
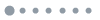
Figure 1.Structure schematic of the ring-shaped top-DBR etched microstructure VCSEL
To study the transverse mode of the etched microstructure VCSEL,the Finite Difference Time Domain[20](FDTD)simulation software is used in this paper. After establishing the geometry of the etched microstructure VCSEL and assigning the material parameters,a 3D simulation region is set. The refractive index of the background is set to 1,which means assuming the background of the simulation region is air. Then the mesh is divided. The mesh type is selected as ‘auto non-uniform’,and the default mesh accuracy is 2. Select ‘Periodic’ for the boundary conditions along the X-axis and ‘PML(Perfectly Match Layer)’ for the boundary conditions along the Y-axis and Z-axis by default. Next,add a light source,set the type as ‘Gaussian’,and the propagation direction as the positive direction along the Z-axis. Finally,add the monitor. Here,we choose the ‘Mode expansion’.
The transverse mode transmission pattern is simulated with device structural parameters and semiconductor material optical parameters,as shown in Fig. 2.
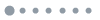
Figure 2.Calculated intensity profiles of different mode numbers (n) of ring-shaped top-DBR etched microstructure VCSEL obtained by FDTD: (a) n=1, (b) n=5, (c) n=9, (d) n=13
A single-mode with a ring-shaped pattern can be seen in Fig. 2(a),which already very clearly displays the characteristics of a hollow laser beam. Figsure. 2(b)-(d)show the multi-petal mode. It can be seen that as the number of modes increases,the number of mode flaps of the transmission pattern increases gradually. However,the characteristics of the hollow beam pattern are maintained from the beginning to the end.
2 Device fabrication
The hollow laser beam can be used for signal transmission in free space optical communication[21],and the beam in the 850 nm wavelength band has the characteristics of low transmission loss and high modulation rate[22]. Based on its good application prospects in data communication and short-distance optical transmission,we adopted the material system of 850 nm VCSEL.
The microstructure VCSEL was fabricated on the GaAs/Al0.3Ga0.7As triple quantum well laser material grown by metal organic chemical vapor deposition(MOCVD)on top of an N-doped 500 μm thick GaAs substrate. The active region is sandwiched between two DBRs. The upper DBR consists of 20 pairs of P-type Al0.9Ga0.1As/Al0.12Ga0.88As,while the lower DBR consists of 36 pairs of N-type Al0.9Ga0.1As/Al0.12Ga0.88As.
Then the first photolithography and inductively coupled plasma(ICP)etching were performed on the cleaned epitaxial wafer to etch the active region and above into a column. The etching depth is about 5 μm,and the mesa diameter is 200 μm. The central area etched microstructure with a depth of about 2.8 μm and an etching hole diameter of 50 μm was obtained by second photolithography and etching. After forming an oxide limiting layer by the wet oxidation process,a 200 nm thick layer of SiO2 was deposited on the device surface as an insulating layer. Then,the light window and central etched area were exposed through the third lithography and etching. Next,the lithography mask method was used to protect other areas and expose the central etched area. The chip was then placed into a high-energy ion implanter and H+ ions were injected into the etched area. To prevent tunneling of the injected ions in the material,the injection direction was at an angle of 7° from the vertical direction of the chip. The injection depth should just reach the position of the upper surface of the lower DBR. Figure 3 shows injection depth as a function of injection power and the SEM(Scanning Electronic Microscopy)picture of the central etched area. The injection energy is 250 keV and the corresponding injection depth is about 2.2 μm,as shown in Fig. 3,and the injection dose is 3×1015/cm2. Finally,the upper and lower electrodes were prepared,and then annealed,cleavage,and encapsulated to form an electrically injected stable working semiconductor laser. The experimentally fabricated VCSEL microscope image is shown in Fig. 4.
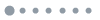
Figure 3.Injection depth as a function of injection power(Down-right inset:SEM image of the central etched area)
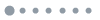
Figure 4.Microscope image of the fabricated ring-shaped top-DBR etched microstructure VCSEL
3 Device characterization and analysis
We measured the light emission characteristics of the etched microstructure VCSEL under the continuous-wave condition at room temperature. The output near-field pattern was photographed by a CCD camera,as shown in Fig. 5. As can be seen from Fig. 5,the laser emitted by the fabricated VCSEL has basically met the characteristics of the hollow beam. The light field pattern also coincides with the pattern calculated by the FDTD. As far as possible to judge from Fig. 5,the profile is almost axisymmetric,which is important for applications in tweezers,atomic traps and funnels.
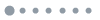
Figure 5.The near-field pattern of the ring-shaped top-DBR etched microstructure VCSEL
The experimental measurement of the light output power-injection current-voltage(L-I-V)characteristic was carried out by using a photodiode power meter. The output power of the device was tested under continuous conditions,and no significant change in power was found during several hours of testing. The L-I-V curve and the corresponding near-field pattern are shown in Fig. 6,the threshold current of the fabricated VCSEL is about 0.27 A. When the injection current exceeds the threshold current,the output power of the laser increases with the increase of the injection current. Driven by a current of 1.4 A,the output power is up to 170 mW and the slope efficiency is 145.9 mW/A. The emission patterns shown in Fig. 6 are corresponding to the currents of 0.3 A,0.7 A,and 1.2 A,respectively. It can be seen that the near-field pattern of the device appears as a hollow circular spot and the hollow circular outline becomes clearer as the current increases. However,when the current increases to a certain level,the center of the light spot is gradually impure. The main reason may be that when the current is first injected,the VCSEL is in a single mode excitation state. As the current increases,more and more high-order modes are excited,and the VCSEL operates from a single mode operation to a state of superposition of multiple transverse modes. In the multi-mode working state,the scattering phenomenon in the central etched area is more obvious. The possible reason of uneven light spots is uneven current distribution. Due to the existence of transverse resistance,more carriers tend to gather at the place where current is injected. Another reason may be that the device may be damaged during the preparation process.
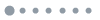
Figure 6.Light output power and voltage as a function of injection current of the ring-shaped top-DBR etched microstructure VCSEL
The lasing spectrum of the microstructure VCSEL is analyzed by a spectrometer,as shown in Fig. 7. Figures 7(a)and(b)correspond to the near-field pattern under 0.3 A and 1.2 A current in Fig. 6 respectively. When the current is 0.3 A,a few modes of the VCSEL are excited,and Fig. 7(a)correspondingly presents a single peak. When the current is 1.2 A,a lot of modes within the resonant cavity oscillate simultaneously,and Fig. 7(b)shows multiple peaks correspondingly. It can be seen from Fig. 7(a)that the lasing peak wavelength of the device is 848 nm,which is located in the 700-900 nm wavelength range of near-infrared light,used in biology,micro-particles,nanoparticles,and other fields[23].
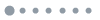
Figure 7.The light spectrum of the ring-shaped top-DBR etched microstructure VCSEL at different injection currents: (a) 0.3 A, (b) 1.2 A
Figure 8 shows the light intensity distribution curve obtained when the current is 1.2 A. It can be seen that there is also a certain light intensity distribution in the central area of the microstructure VCSEL. The light-emitting region also exists the problem of uneven light intensity distribution. However,the light intensity distribution curve shown in Fig. 8 is almost consistent with the light intensity distribution of the hollow beam. It can also be seen from the far-field pattern that the beam emitted by the microstructure VCSEL has a ring shape which is still consistent with the characteristics of a hollow beam.
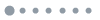
Figure 8.The light intensity distribution curves of the ring-shaped top-DBR etched microstructure VCSEL in vertical and parallel directions
The reason that the central area isn’t completely dark may be,on the one hand,the rough wall and structural damage caused by etching will bring unnecessary light scattering. On the other hand,the light beam will scatter and diffract during the transmission process. Therefore,further research direction would be to optimize the device structure design to make the current injection more uniform,reduce the internal resistance of the device,and reduce the threshold current of the device. Additionally,it would be beneficial to improve the experimental process of the fabrication steps,reduce the damage to the device during the process steps,and realize the vertical cavity semiconductor laser to emit high-quality hollow laser beams more efficiently.
4 Conclusion
This paper designs a vertical cavity surface emitting semiconductor laser with an etched microstructure that uses a proton injection to form a high-resistance region. The microstructure VCSEL can directly obtain a hollow laser beam. The key technical issues such as the fabrication process were studied,and the lateral light field distribution was calculated by FDTD software. The ring-shaped top-DBR etched microstructure vertical cavity surface emitting semiconductor laser was successfully fabricated. And the output characteristics of the fabricated device were measured. The lasing wavelength is 848 nm,the threshold current is about 0.27 A,the output power is up to 170 mW,and the near-field pattern is a ring-shaped hollow beam pattern. Due to factors such as the etched surface can cause scattering and carrier diffusion,the central area of the beam is not completely dark. This research opens up a new direction in the research of semiconductor laser technology,proposes a new technical method for acquiring hollow laser beams,and provides technical support for the two-dimensional array integration of hollow beams. The two-dimensional array of hollow beams lays a good foundation for the future development of multi-particle manipulation and optical addressing devices.
References
[1] E Demirci, C Nölke, S Kaierle et al. Development of a hollow laser beam for micromachining. Advanced Optical Technologies, 1(2012).
[2] Y Wang, Z Yang, S Shen et al. Controllable anomalous hollow beam and its propagation properties-ScienceDirect. Optik, 214(2021).
[3] K Fujimoto. Dual-Arm Visuo-Haptic Optical Tweezers for Bimanual Cooperative Micromanipulation of Nonspherical Objects. Micromachines, 13(2022).
[4] G B Zhang, M Chen, C B Schroeder et al. Acceleration and evolution of a hollow electron beam in wakefields driven by a Laguerre-Gaussian laser pulse. Physics of Plasmas, 23, 033114-(2016).
[5] B U Londhe, K S Bhole, C Sharma et al. Development of Polymer Microneedle upon Exposure of Hollow Gaussian Beam on Unconstraint Depth Resin. IOP Conference Series Materials Science and Engineering, 577, 012047(2019).
[6] J Li, X Chen, Z Lin et al. Generation of hollow Gaussian beams by restoring structured light with meta-optics. Optics & Laser Technology, 153(2022).
[7] T Luo. A dark hollow beam generator based on special optical fiber with long period fiber grating. Optics & Laser Technology, 134(2021).
[8] Y Y Zhu, J F Shen, H X Dou et al. A new design of computer generated holography to obtain high order Bessel-like beam. Journal of Optoelectronics. Laser, 22, 1263-1268(2011).
[9] J Yin, W Gao, Y Zhu. Chapter 3 Generation of dark hollow beams and their applications. Progress in Optics, 45, 119-204(2003).
[10] B Cao, P Jiang, H Yang et al. Coupling system with concave and positive-negative angular cone lenses group for the Cassegrain receiving antenna system. Optics Communications, 493, 127029(2021).
[11] J Yang. Generation of anomalous vector Bessel beams with varying polarization order along the propagation direction. Optik: Zeitschrift fur Licht- und Elektronenoptik: = Journal for Light-and Electronoptic, 232(2021).
[12] G M Wu, F C Kung, C Y Lee. Study of fabrication and characterization of high power 850 nm vertical-cavity surface-emitting laser arrays. Surface and Coatings Technology, 387, 125489(2020).
[13] C Y Peng, H T Cheng, H C Kuo et al. Design and Optimization of VCSELs for up to 40-Gb/s Error-Free Transmission Through Impurity-Induced Disordering. IEEE Transactions on Electron Devices, 1-6(2020).
[14] K Liu, H Fan, Y Huang et al. A pair of integrated optoelectronic transceiving chips for optical interconnects. Chinese Optics Letters, 16(2018).
[15] J F Seurin, D Zhou, G Xu et al. High-efficiency VCSEL arrays for illumination and sensing in consumer applications(2016).
[16] P C Di, X P Li, J Yang et al. High-Power VCSEL-Pumped Slab Laser With Temperature Fluctuation Adaptability. IEEE Photonics Technology Letters, 1-1(2021).
[17] M Ling, W Zhichao, X Zhang et al. The study of high-power hollow-beam laser diode. Optik: Zeitschrift fur Licht- und Elektronenoptik: = Journal for Light-and Electronoptic, 182(2019).
[18] C P Hsu, Y H Wu, D L Cheng et al. The modes competition of a Laguerre-Gaussian commercial VCSELs based on quasi-Gaussian-beam profile optical feedback(2011).
[19] R A Flynn, O Kibar, D Hartmann et al. Superresolution Using a Vertical-Cavity Surface-Emitting Laser (VCSEL) with a High-Order Laguerre-Gaussian Mode. Japanese Journal of Applied Physics, 39, 902-905(2000).
[20] K S Yee. Numerical solution of initial boundary value problems involving maxwell's equations in isotropic media. IEEE Transactions on Antennas & Propagation, 14, 302-307(1966).
[21] Y Teen, N Lazer, T Nathiyaa et al. Investigation on Hollow Beam Propagation through Turbulence Conditions in Free Space Optical Communication. Optical Memory and Neural Networks, 28, 296-305(2019).
[22] Ledentsov , Nikolay , N et al. Flexible MultiCAP Modulation and its Application to 850 nm VCSEL-MMF Links. Journal of Lightwave Technology: A Joint IEEE/OSA Publication, 35, 3168-3173(2017).
[23] H Wang, P Agarwal, S Zhao et al. A Near-Infrared Laser- Activated "Nanobomb" for Breaking the Barriers to MicroRNA Delivery. Advanced Materials, 28(2016).