Guanbin GAO, Pei XIE, Fei LIU, Jing NA. Residual modelling and compensation for articulated arm coordinate measuring machines based on compound calibration and extreme learning machine[J]. Optics and Precision Engineering, 2023, 31(22): 3289

Search by keywords or author
- Optics and Precision Engineering
- Vol. 31, Issue 22, 3289 (2023)

Fig. 1. 7-DoF articulated arm coordinate measuring machine

Fig. 2. Coordinate systems of the AACMM
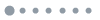
Fig. 3. Flow chart of compound calibration method
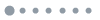
Fig. 4. Track of the 4th joint in the measurement space
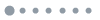
Fig. 5. Diagram of measuring swing angle ω
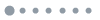
Fig. 6. Diagram of the position and radius of the configuration circle
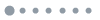
Fig. 7. Effect of first joint on residual value
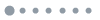
Fig. 8. Circular track formed by probe in moving space
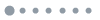
Fig. 9. Impacts of probe circle on residual value
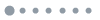
Fig. 10. Relationship between configuration parameters and residuals
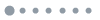
Fig. 11. Relationship of the elevation angle, swing angle and residual
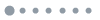
Fig. 12. Relationship of the length, swing angle and residual
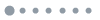
Fig. 13. Relationship between swing angle and rotation angle and residuals in X and Y -directions
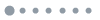
Fig. 14. Residual compensation model based on ELM
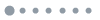
Fig. 15. Training process of ELM
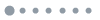
Fig. 16. Calibration compensation software
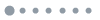
Fig. 17. Error distribution before calibration
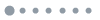
Fig. 18. Error distribution after calibration
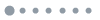
Fig. 19. Comparison of kinematic calibration effects
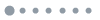
Fig. 20. Residual compensation results
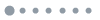
Fig. 21. Residual compensation effect of different fitting algorithms
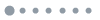
Fig. 22. Compensation effect of different residual compensation models
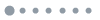
Fig. 23. Measurement results of standard gauge
|
Table 1. Nominal value of kinematic parameter
|
Table 2. D-H parameter of the AACMM after identification
|
Table 3. Compound kinematic calibration results
|
Table 4. Comparison of kinematic calibration effects
|
Table 5. Residual compensation results
|
Table 6. Comparison of residual compensation effects of different fitting algorithms
|
Table 7. Comparison of compensation effects of different residual compensation models
|
Table 8. Measurement results of standard gauge

Set citation alerts for the article
Please enter your email address