Ning Wang, Yong Zhu, Jie Zhang. Research Status of Fiber Fabry-Perot Sensing Technology Under High Temperature and High Pressure Environment[J]. Laser & Optoelectronics Progress, 2023, 60(11): 1106005

Search by keywords or author
- Laser & Optoelectronics Progress
- Vol. 60, Issue 11, 1106005 (2023)
![Silicon-borosilicate glass fiber F-P pressure sensor[16]](/richHtml/lop/2023/60/11/1106005/img_01.jpg)
Fig. 1. Silicon-borosilicate glass fiber F-P pressure sensor[16]
![Monocrystalline silicon MEMS optical fiber F-P hightemperature pressure sensor. (a) Schematic diagram of SiC sensor head and measurement scheme[17]; (b) structural diagram of all silicon based dual cavity optical fiber pressure sensor[18]](/richHtml/lop/2023/60/11/1106005/img_02.jpg)
Fig. 2. Monocrystalline silicon MEMS optical fiber F-P hightemperature pressure sensor. (a) Schematic diagram of SiC sensor head and measurement scheme[17]; (b) structural diagram of all silicon based dual cavity optical fiber pressure sensor[18]
![SiC optical fiber F-P high temperature pressure sensor[19-20]](/Images/icon/loading.gif)
![Fiber end face pressure sensor. (a) Pressure sensor made of single-mode fiber[21]; (b) all quartz micro pressure sensor made of quartz fiber using laser processing technology[22]; (c) pressure sensor made of quartz fiber using femtosecond laser processing method[23]](/Images/icon/loading.gif)
Fig. 4. Fiber end face pressure sensor. (a) Pressure sensor made of single-mode fiber[21]; (b) all quartz micro pressure sensor made of quartz fiber using laser processing technology[22]; (c) pressure sensor made of quartz fiber using femtosecond laser processing method[23]
![Photonic crystal fiber F-P sensor[24]](/Images/icon/loading.gif)
Fig. 5. Photonic crystal fiber F-P sensor[24]
![Structure diagram of sapphire-derived fiber sensor[25]](/Images/icon/loading.gif)
Fig. 6. Structure diagram of sapphire-derived fiber sensor[25]
![Sensor schematic diagram and related schematic diagram (a) Schematic of sensor; (b) schematic of large diameter fiber[26]](/Images/icon/loading.gif)
Fig. 7. Sensor schematic diagram and related schematic diagram (a) Schematic of sensor; (b) schematic of large diameter fiber[26]
![Schematic diagram of air fiber matrix composite optical fiber F-P interferometer[27]](/Images/icon/loading.gif)
Fig. 8. Schematic diagram of air fiber matrix composite optical fiber F-P interferometer[27]
![Micro-fiber F-P force sensor[28]](/Images/icon/loading.gif)
Fig. 9. Micro-fiber F-P force sensor[28]
![Sapphire fiber vibration sensor[29]. (a) Configuration; (b) physical layout; (c) ceramic base; (d) ceramic plate; (e) ceramic assembly](/Images/icon/loading.gif)
Fig. 10. Sapphire fiber vibration sensor[29]. (a) Configuration; (b) physical layout; (c) ceramic base; (d) ceramic plate; (e) ceramic assembly
![Sensor[30]. (a) Physical photo of the sensor; (b) structure of the probe cavity; (c) structure of the fiber F-P sensor](/Images/icon/loading.gif)
Fig. 11. Sensor[30]. (a) Physical photo of the sensor; (b) structure of the probe cavity; (c) structure of the fiber F-P sensor
![Sapphire fiber optic sensor. (a) Sapphire fiber optic F-P temperature sensor proposed by Beijing University of Aeronautics and Astronautics[31]; (b) sapphire fiber optic F-P temperature sensor proposed by Tianjin University[32]; (c) sapphire fiber optic pressure sensor[33]](/Images/icon/loading.gif)
Fig. 12. Sapphire fiber optic sensor. (a) Sapphire fiber optic F-P temperature sensor proposed by Beijing University of Aeronautics and Astronautics[31]; (b) sapphire fiber optic F-P temperature sensor proposed by Tianjin University[32]; (c) sapphire fiber optic pressure sensor[33]
![Demodulation optical path based on Fourier transform[48]](/Images/icon/loading.gif)
Fig. 13. Demodulation optical path based on Fourier transform[48]
![Block diagram of the non-scanning demodulation system[49]](/Images/icon/loading.gif)
Fig. 14. Block diagram of the non-scanning demodulation system[49]
![Polarization-low coherence interference demodulation technique[50-51]](/Images/icon/loading.gif)
![F-P demodulation system based on AWG[52]](/Images/icon/loading.gif)
Fig. 16. F-P demodulation system based on AWG[52]
![F-P fiber strain sensor and strain instrument[55]](/Images/icon/loading.gif)
Fig. 17. F-P fiber strain sensor and strain instrument[55]
![Analysis of the influence of small range Fizeau interferometer's surface shape on measurement accuracy[58]](/Images/icon/loading.gif)
Fig. 18. Analysis of the influence of small range Fizeau interferometer's surface shape on measurement accuracy[58]
![Sapphire fiber F-P sensing system produced by Oxsensis[59]](/Images/icon/loading.gif)
Fig. 19. Sapphire fiber F-P sensing system produced by Oxsensis[59]
![Sapphire fiber F-P sensor and its application[60]](/Images/icon/loading.gif)
Fig. 20. Sapphire fiber F-P sensor and its application[60]
![Flow-induced vibration test of the heat transfer pipe[61]](/Images/icon/loading.gif)
Fig. 21. Flow-induced vibration test of the heat transfer pipe[61]
![Thermal and hydraulic experiment of fuel assembly[28]](/Images/icon/loading.gif)
Fig. 22. Thermal and hydraulic experiment of fuel assembly[28]
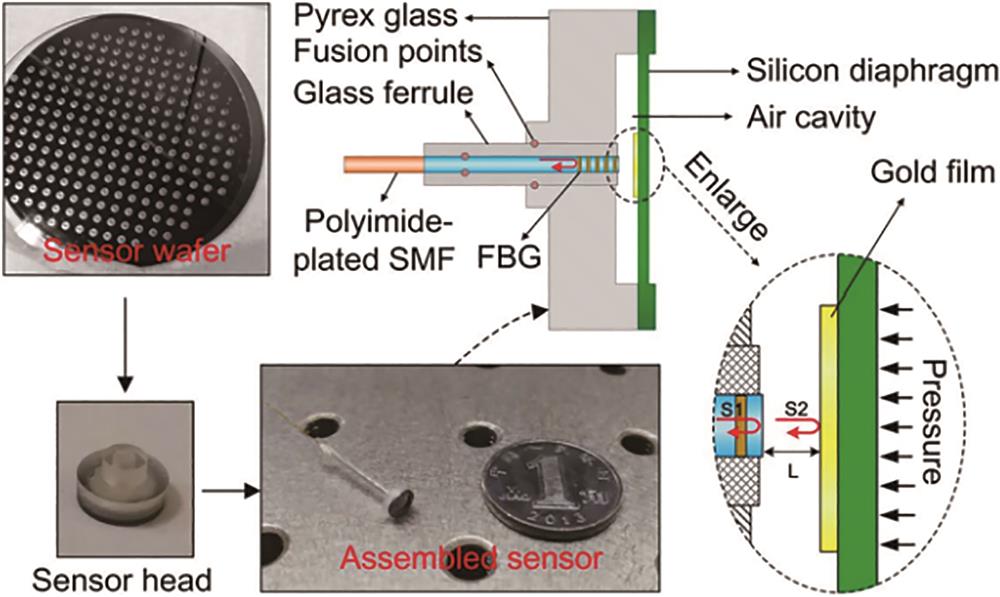
Set citation alerts for the article
Please enter your email address