Lei QIAN, Jie HU, Yameng SHAN, Junduo WANG, Peng ZHOU, Wenjiang SHEN. Novel Packaging Stress Isolation Structure for MEMS Micromirror with Piezoresistive Angle Sensor[J]. Acta Photonica Sinica, 2022, 51(5): 0551311

Search by keywords or author
- Acta Photonica Sinica
- Vol. 51, Issue 5, 0551311 (2022)
Abstract
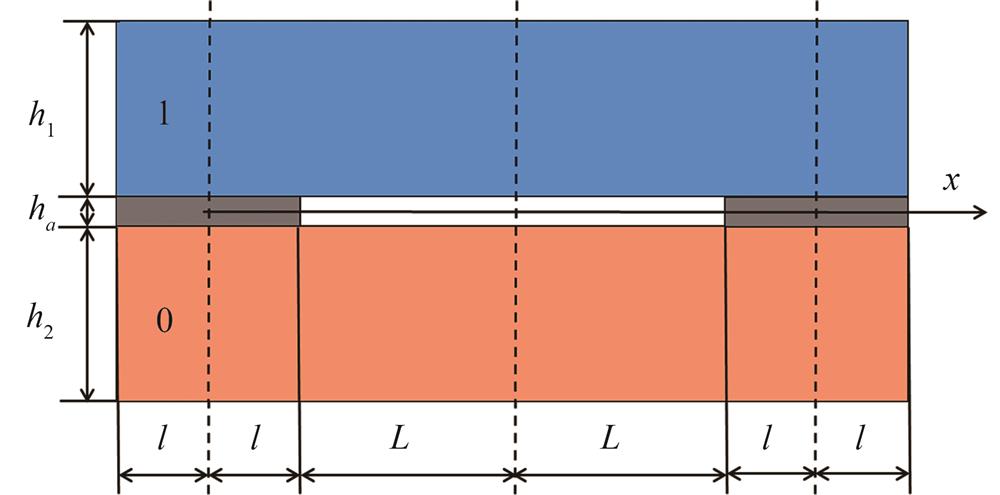
Set citation alerts for the article
Please enter your email address