
- Journal of Inorganic Materials
- Vol. 36, Issue 5, 547 (2021)
Abstract
Porous silicon carbide (SiC) ceramics possess a unique combination of desirable properties, such as excellent high temperature strength, high chemical stability, high thermal shock stability, and outstanding oxidation resistance[
Light weight with high strength is always desired demands for porous ceramics which depends on pore structure and the strength of wall materials. According to classifications of cellular topology, stretching-dominated structure has a larger load bearing capability through overall structure compared to bending-dominated structure[
oriented nanowires are better than random nanowires to improve the mechanical strength[
Inspired by high strut strength and orientation architecture, here we presented a novel method for SiC porous ceramic fabrication where reticulate structure was directly comprised of oriented SiC nanowires. This was realized through crossed layer-by-layer direct ink printing. SiC nanowires in each filament were aligned in the streamwise direction due to shear flow through nozzle tip. The structure and morphology were characterized, and the mechanical properties of the porous SiC nanowire networks were investigated.
1 Experimental procedure
β-SiC nanowires with diameter in 0.1-0.6 μm, length in 50-100 μm, purity higher than 96%, density of 3.21 g/cm3, and aspect ratio of 100-200 (Changsha Sinet Advanced Materials Co., Ltd. Changsha, China) are used as raw materials. SiC nanowires (SiCNWs) were dispersed in deionized water part by part using ultrasonic method to ensure homogeneous dispersion. Al2O3 and Y2O3 (m(Al2O3) : m(Y2O3)=3 : 2) with 15wt% of the SiC nanowires were added to promote sintering. The volume fraction of SiC nanowires was 10%. 2.5wt% hydroxypropyl methylcellulose solution (25wt% water) and 0.04% polyethyleneimine (5wt% water) was added in the dispersed SiC nanowire slurry. The ink was mixed for 1 h by mechanical stirring (300 r/min).
A 3D-BioprinterTM System (Regenovo, Shining 3D Tech Co., Ltd, China) equipped with a pressurized paste extrusion system was used to fabricate the samples. The inks were loaded into 100 mL syringe with a plunger. Printing nozzles with diameter in 320 μm were used to produce SiC nanowire filaments. A constant pressure was applied to induce the ink flow through the nozzle. The writing speed was set at 25 mm/s. After printing, the samples were dried for 24 h and calcined at 550 ℃ for 1 h in air. The samples were subsequently sintered in Ar at a heating rate of 5 ℃/min up to 1800, 1850 and 1900 ℃ for 1 h.
The morphologies of the scaffolds before and after sintering were investigated using scanning electron microscope (S4800, Hitachi, Tokyo, Japan). The apparent porosity, pore size distributions and bulk density of sintered SiC porous ceramics were examined by a mercury porosimetry (Autopore IV9510, USA). The out-of-plane compressive strength was measured using a test machine (Instron-5592). Five rectanglular samples with size of 4 mm×6 mm×6 mm for each sample were machined and tested. The load was applied on the two parallel surfaces at a crosshead speed of 0.5 mm/min.
2 Results and discussion
2.1 Microstructure
The printed scaffold consists of uniform oriented β-SiC nanowires along printing direction as shown in Fig. 1(a, b), which is aroused by the shear flow of slurry through nozzle tip. The Lotgering orientation factor of f(111) of printed SiCNWs is about 0.956[
Figure 1.Morphologies of samples with different magnifications(a, b) Before sintering, and sintered at (c, d) 1800 , (e, f) 1850 and (g, h) 1900 ℃. The insert in (a) is the appearance of printed SiCNWs scaffold
About 46.9vol% shrinkages of printed SiCNW networks occurred after drying. The printed SiCNW networks were sintered at 1800, 1850 and 1900 ℃. Further shrinkages are observed after sintering. Compared to the printed samples before drying, the volume shrinkage ratios of SiCNW networks sintered at 1800, 1850 and 1900 ℃ are about 74.0%, 79.8% and 83.6%, respectively. The typical morphologies after sintering are shown in Fig. 1(c-h). Shortening and coarsening of SiC nanowires occurred after high temperature sintering. The high aspect ratio of SiCNWs was kept well at sintering temperature lower than 1900 ℃. The sintered SiCNWs networks exhibit a structure with highly interconnected pore and an architecture formed by aligned SiCNWs struts. The wall thickness is of the order of SiCNWs diameter (<500 nm). The adjacent SiC nanowires were sintered together and the remaining liquid phase can be seen in Fig. 1(d, f). Most of SiCNWs were changed to particles after sintered at 1900 ℃. Fig. 2 shows the pore distribution of porous SiCNWs networks sintered at 1800 and 1850 ℃. The pore size distribution of sample sintered at 1900 ℃ was not tested due to its low strength. Sintered SiCNW networks showed uniform pore size distribution. The pore dimensions are distributed between 0.5 and 1 μm, accounting for 86.5vol% pores. The density, porosity and median pore diameter changed from 1.25 g/cm3, 60.5%, 1121 nm to 1.49 g/cm3, 54.6%, 994 nm after sintered at 1800 and 1850 ℃, respectively.
Figure 2.Pore size distributions of SiC porous ceramics sintered at 1800 and 1850 ℃
Fig. 3 shows the corresponding XRD patterns of SiCNWs networks after sintering. The SiCNWs network sintered at 1800 ℃ shows no change in the phase composition except for the crystallization of sintering additives compared to the as-received 3C-SiC SiCNWs. When sintered at 1850 ℃, both α-SiC (Rhombohedral) and 3C-SiC are detected. While sintered at 1900 ℃, only α-SiC (Rhombohedral) is found, which indicates the 3C-SiC nanowires all change to α-SiC, corresponding to the particle morphology as shown in Fig. 1(g, h). Pure SiCNWs without sintering additives show good phase stability after heat-treatment from 1800 ℃ to 1950 ℃ (Fig. 3(a)). The sintering additives promote the phase transformation from β-SiC into α-SiC[
Figure 3.XRD patterns of SiC porous ceramics sintered at different temperatures (a) and SiCNWs treated at different temperatures (b)
2.2 Mechanical properties
Sintered SiCNWs networks displayed cellular rupture which commonly occurred in ceramic foams during compressive test as shown in Fig. 4. The wavy platform after the highest load value indicates gradual failure of porous structure. Samples with nanowire-like struts possess much higher strength than those with particle-like struts ((37.5±6) MPa). The SiCNWs porous ceramic sintered at 1850 ℃ showed the highest compressive strength ((245.5± 0.7) MPa). Samples sintered at 1800 ℃ mostly fail at the junction between nanowires (Fig. 4(b)) due to the incompletely sintering, which can be confirmed by the residual Al2O3 as shown in Fig. 1(d). When sintered at 1850 ℃, failure events of SiCNWs are observed which indicated by arrows in Fig. 4(c). When SiCNWs struts changed to particle struts which sintered at 1900 ℃, intergranular fracture dominates the main failure modes as shown in Fig. 4(d).
Figure 4.Compressive strength-strain curves of SiC porous ceramic sintered at different temperatures (a) and fracture modes of SiC porous ceramics sintered at 1800 (b), 1850 (c) and 1900 ℃ (d)
The SiCNWs networks show higher strength compared to other porous SiC ceramics with comparable porosity[
Figure 5.Comparison of the compressive strength of SiCNW networks with other porous SiC ceramicsNumbers in square brackets represent the serial number of refered documents
Where σ is the compressive strength of the porous composite; σfs is the fracture strength of the wall material (struts); ρ* is the density of the porous ceramic and ρ0 is the density of struts.
The bending strength of SiCNWs struts sintered at 1850 ℃ according to equation (1) reaches ~3.9 GPa, which is much larger than those reported for sintered ceramics and comparable to those estimated for struts of ceramics microlattices[
3 Conclusions
Size-dependent effects of struts strength and architecture benefits from orientation advantages were designed and investigated. The two features are realized by SiC nanowires and assembling of aligned SiC nanowires struts with cross-lamellar structure by direct ink printing. Although stretching-dominated deform mode is not specially designed here, an orientated structure combined with strong SiC nanowire struts provides higher strength than other porous SiC ceramics with comparable porosity.
References
[1] JI-HONG SHE, T OHJI, ZHEN-YAN DENG. Thermal shock behavior of porous silicon carbide ceramics. Journal of the American Ceramic Society, 85, 2125-2127(2002).
[2] SHI-FENG LIU, YU-PING ZENG, DONG-LIANG JIANG. Effects of CeO2 addition on the properties of cordierite-bonded porous SiC ceramics. Journal of the European Ceramic Society, 29, 1795-1802(2009).
[3] P H PASTILA, V HELANTI, A P NIKKILA et al. Environmental effects on microstructure and strength of SiC-based hot gas filters. Journal of the European Ceramic Society, 21, 1261-1268(2001).
[4] D DAS, N KAYAL, G A MARSOLA et al. Recycling of coal fly ash for fabrication of elongated mullite rod bonded porous SiC ceramic membrane and its application in filtration. Journal of the European Ceramic Society, 40, 2163-2172(2020).
[5] U BETKE, A LIRB. Micro-macroporous composite materials- preparation techniques and selected applications: a review. Advanced Engineering Materials, 20, 1800252(2018).
[6] V S DESHPANDE, M F ASHBY, N A FLECK. Foam topology bending versus stretching dominated architectures. Acta Materialia, 49, 1035-1040(2001).
[7] M F ASHBY. The properties of foams and lattices. Philosophical Transactions of the Royal Society A, 364, 15-30(2006).
[9] M KAUR, T G YUN, S M HAN et al. 3D printed stretching- dominated micro-trusses. Materials and Design, 134, 272-280(2017).
[10] C FERRARO, E GARCIA-TUNON, V G ROCHA et al. Light and strong SiC networks. Advanced Functional Materials, 26, 1636-1645(2016).
[11] CHANG-AN WANG, YONG HUANG, HONG-XIANG ZHAI. The effect of whisker orientation in SiC whisker-reinforced Si3N4 ceramic matrix composites. Journal of the European Ceramics Society, 19, 1903-1909(1999).
[12] M A MEYERS, PO-YU CHEN, YU-MIN LIN et al. Biological materials: structure and mechanical properties. Progress in Materials Science, 53, 1-206(2008).
[13] QUAN ZHU, XIANG DONG, JIAN-BAO HU et al. High strength aligned SiC nanowire reinforced SiC porous ceramics fabricated by 3D printing and chemical vapor infiltration. Ceramics International, 46, 6978-6983(2020).
[14] M NADER, F ALDINGER, M J HOFFMANN. Influence of the
[15] J H EOM, Y W KIM, I H SONG. Microstructure and properties of porous silicon carbide ceramics fabricated by carbothermal reduction and subsequent sintering process. Materials Science and Engineering: A, 464, 129-134(2007).
[16] Y W KIM, J H EOM, YAN-TING GUO et al. Processing of open-cell silicon carbide foams by steam chest molding and carbothermal reduction. Journal of the American Ceramics Society, 94, 344-347(2011).
[17] J H EOM, Y W KIM, I H SONG et al. Processing and properties of polysiloxane-derived porous silicon carbide ceramics using hollow microspheres as templates. Journal of the European Ceramics of Society, 28, 1029-1035(2008).
[18] J H EOM, Y W KIM. Effect of additive composition on microstructure and strength of porous silicon carbide ceramics. Journal of Materials Science, 44, 4482-4486(2009).
[19] A SHIMAMURA, M FUKUSHIMA, M HOTTA et al. New approach for macro porous RB-SiC derived from SiC/Novolac- type phenolic composite. Journal of the American Ceramics Society, 99, 440-444(2016).
[20] F M VARELA-FERIA, J MARTINEZ-FERNANDEZ, LOPEZ A R ARELLANO- et al. Low density biomorphic silicon carbide: microstructure and mechanical properties. Journal of the European Ceramics Society, 22, 2719-2725(2002).
[21] L J GIBSON, M F ASHBY. Cellular Solids: Structure and Properties, 2ed. Cambridge University(1997).
[23] P MIRANDA, A PAJARE, E SAIZ et al. Fracture mode under uniaxial compression in hydroxyapatite scaffolds fabricated by robocasting. Journal of Biomedial Materials Research Part A, 83, 646-655(2007).
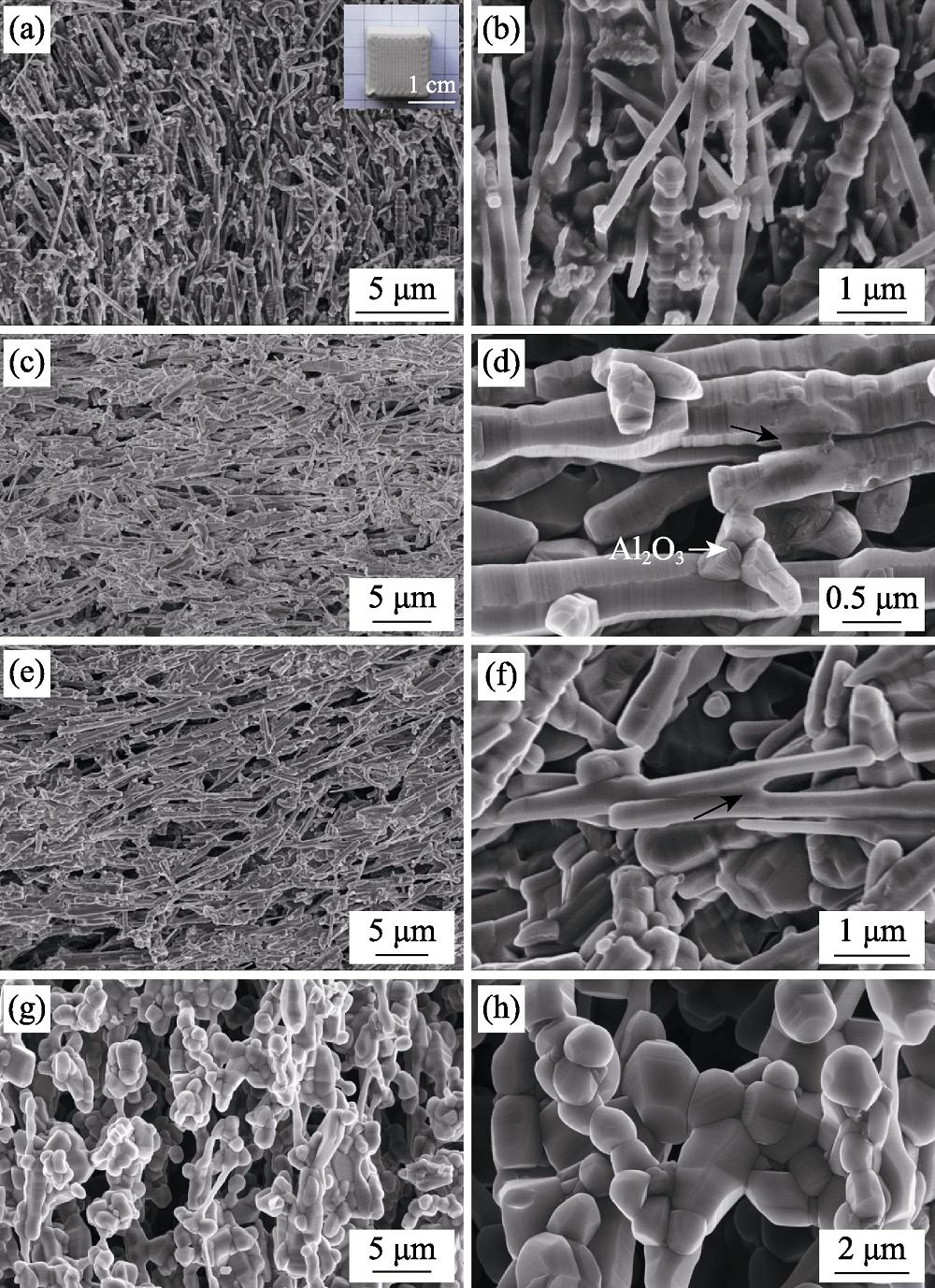
Set citation alerts for the article
Please enter your email address