Dichen Li, Hang Zhang, Jianglong Cai. Development of Refractory High Entropy Alloys by Laser Additive Manufacturing: Regulating Material Properties and Manufacturing Processes (Invited)[J]. Chinese Journal of Lasers, 2024, 51(1): 0102001

Search by keywords or author
- Chinese Journal of Lasers
- Vol. 51, Issue 1, 0102001 (2024)
![Typical thermal cracks[35-37]. (a)(b) Solidification cracks with irregular dendritic morphology; (c)(d) liquefaction cracks without dendritic characteristics; (e)(f) solidification cracks; (g)(h) morphology and dislocation maps of the liquefaction crack region; (i)‒(k) single pass of LPBFed AA7075 alloy shows different pool shapes and thermal crack sensitivities](/richHtml/zgjg/2024/51/1/0102001/img_01.jpg)
Fig. 1. Typical thermal cracks[35-37]. (a)(b) Solidification cracks with irregular dendritic morphology; (c)(d) liquefaction cracks without dendritic characteristics; (e)(f) solidification cracks; (g)(h) morphology and dislocation maps of the liquefaction crack region; (i)‒(k) single pass of LPBFed AA7075 alloy shows different pool shapes and thermal crack sensitivities
![Typical pores[32,57-58]. (a) Unfused and metallurgical pores; (b) keyhole pore; (c) shrinkage pores; (d) schematic diagrams of pore formation mechanism in LDED process](/richHtml/zgjg/2024/51/1/0102001/img_02.jpg)
Fig. 2. Typical pores[32,57-58]. (a) Unfused and metallurgical pores; (b) keyhole pore; (c) shrinkage pores; (d) schematic diagrams of pore formation mechanism in LDED process
![Principle of high flux forming[74]](/Images/icon/loading.gif)
Fig. 3. Principle of high flux forming[74]
![High entropy alloy phase with high flux forming[74]. (a) XRD patterns; (b) measured composition versus predicted composition; (c) SEM image and elemental mapping](/Images/icon/loading.gif)
Fig. 4. High entropy alloy phase with high flux forming[74]. (a) XRD patterns; (b) measured composition versus predicted composition; (c) SEM image and elemental mapping
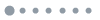
Fig. 5. Backscatter image of sample section and grain direction of welded structure section obtained by electron backscatter diffraction (EBSD)
![Tensile property curves of TiNbCrVNi alloy[90]](/Images/icon/loading.gif)
Fig. 6. Tensile property curves of TiNbCrVNi alloy[90]
![Cross-section morphology of thin-walled parts under different process parameters[84]. (a) 2.8 J/mm; (b) 3.2 J/mm; (c) 3.6 J/mm; (d) 4.0 J/mm; (e) 4.4 J/mm](/Images/icon/loading.gif)
Fig. 7. Cross-section morphology of thin-walled parts under different process parameters[84]. (a) 2.8 J/mm; (b) 3.2 J/mm; (c) 3.6 J/mm; (d) 4.0 J/mm; (e) 4.4 J/mm
![Performance test results of the samples under different processing parameters[84]. (a) Average microhardness of alloy cross-section; (b) engineering stress-strain curves of the alloy under compression at room temperature](/Images/icon/loading.gif)
Fig. 8. Performance test results of the samples under different processing parameters[84]. (a) Average microhardness of alloy cross-section; (b) engineering stress-strain curves of the alloy under compression at room temperature
![LPBF forming process and geometric relationship between parameters[72]. (a) Simplified LPBF forming process. Geometric relationship between the layer thickness c and the channel spacing d for the following cases: (b) ml¯ <c, (c) ml¯ >c, and (d) ml¯ =c](/Images/icon/loading.gif)
Fig. 9. LPBF forming process and geometric relationship between parameters[72]. (a) Simplified LPBF forming process. Geometric relationship between the layer thickness c and the channel spacing d for the following cases: (b) <c, (c) >c, and (d) =c
![Temperature distribution in the micro-region (4 mm×2 mm×1 mm) around the 200 s laser spot of LPBF process[92]](/Images/icon/loading.gif)
Fig. 10. Temperature distribution in the micro-region (4 mm×2 mm×1 mm) around the 200 s laser spot of LPBF process[92]
![LPBF formed samples[89]](/Images/icon/loading.gif)
Fig. 11. LPBF formed samples[89]
![Tensile samples formed by LPBF(after polishing)[89]](/Images/icon/loading.gif)
Fig. 12. Tensile samples formed by LPBF(after polishing)[89]
![Original sample formed by LDED[76]](/Images/icon/loading.gif)
Fig. 13. Original sample formed by LDED[76]
![Warping deformation of HEA formed by LPBF without improvement[92]](/Images/icon/loading.gif)
Fig. 14. Warping deformation of HEA formed by LPBF without improvement[92]
![Samples formed by improved LPBF forming [92]](/Images/icon/loading.gif)
Fig. 15. Samples formed by improved LPBF forming [92]
![Z-shape (left) and strip (right) scanning strategies[93]](/Images/icon/loading.gif)
Fig. 16. Z-shape (left) and strip (right) scanning strategies[93]
![Nb3Ta3Mo(Ti2Ni)3 high entropy alloy impeller entity formed by LPBF[93]](/Images/icon/loading.gif)
Fig. 17. Nb3Ta3Mo(Ti2Ni)3 high entropy alloy impeller entity formed by LPBF[93]
|
Table 1. Compression properties of AMed RHEAs
|
Table 2. Tensile properties of AMed RHEAs
|
Table 3. Compression properties of AMed RHEAs at high temperature
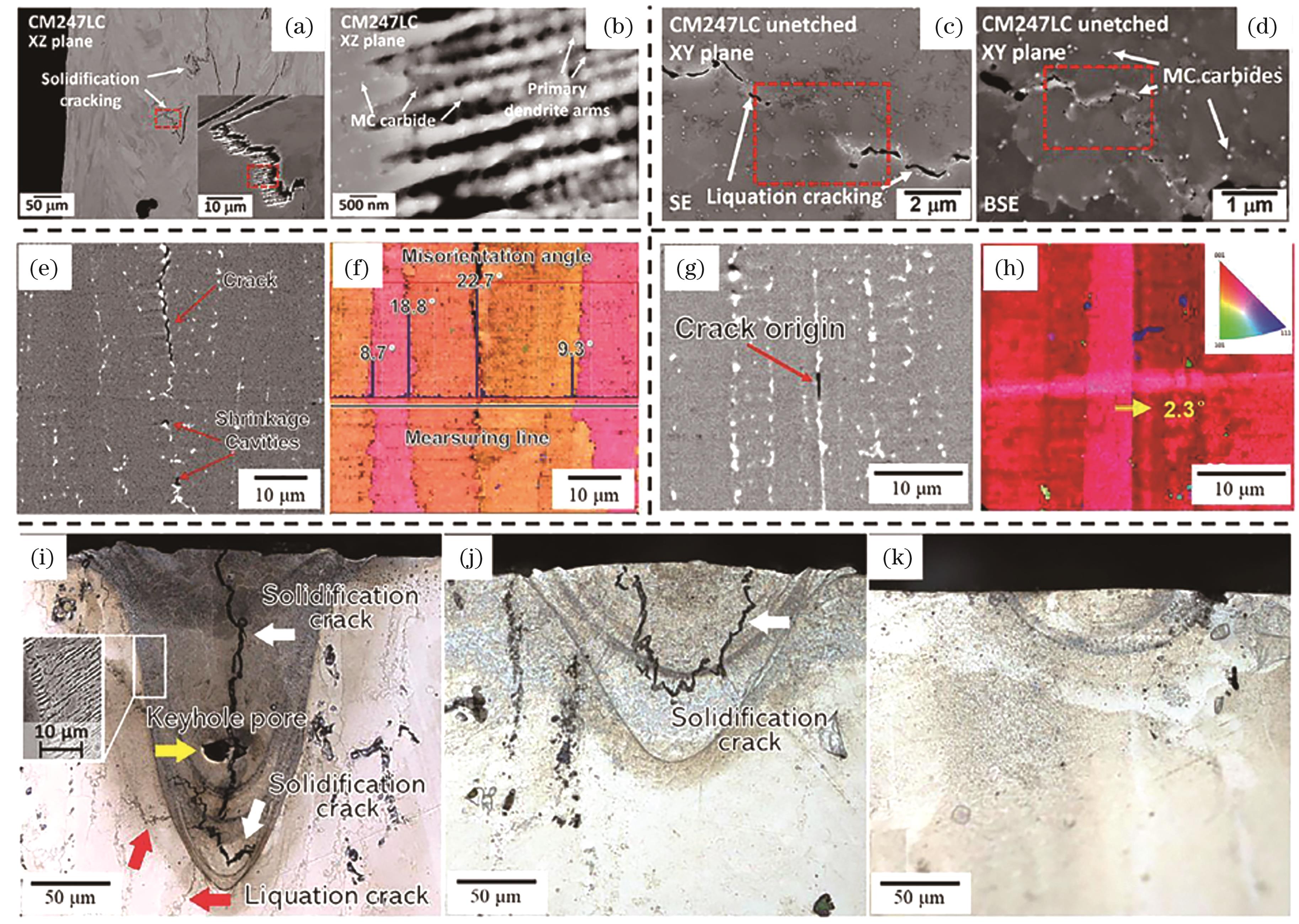
Set citation alerts for the article
Please enter your email address