Pengyu Chen, Nianbing Zhong, Xuefeng He, Quanhua Xie, Bo Wan, Yuanyuan He, Lei Wu, Yang Liu, Dong Lai. Chitosan/Polyvinyl Alcohol/Nanocarbon Powder Composite Coated Fiber Bragg Grating Humidity Sensor[J]. Acta Optica Sinica, 2024, 44(4): 0428003

Search by keywords or author
- Acta Optica Sinica
- Vol. 44, Issue 4, 0428003 (2024)

Fig. 1. Humidity sensor preparation process diagram

Fig. 2. Structure diagram of humidity detection system
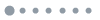
Fig. 3. Field emission scanning electron microscope (FESEM) maps of surface morphology and Fourier transform infrared absorption spectra of humidity-sensitive film of differently doped chitosan/polyvinyl alcohol/nanocarbon powder polymer-coated optical fibers. (a) CS/PVA; (b) CS/PVA/CNP-5%; (c) CS/PVA/CNP-10%; (d) CS/PVA/CNP-15%; (e) primary coating; (f) secondary coating; (g) tertiary coating; (h) quaternary coating; (i) FT-IR absorption spectra of different chitosan/polyvinyl alcohol/nanocarbon powder polymers
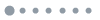
Fig. 4. Effect of nanocarbon content on response characteristics of sensor. (a) Total wavelength drift of sensor at different humidity levels with different nanocarbon doping; (b) humidity response characteristics of sensor; (c) maximum sensor response; (d) reflectance spectra plots of sensor at increasing humidity; (e) reflectance spectra plots of sensor at decreasing humidity; (f) humidity response characteristics of sensor at increasing and decreasing humidities. Doping mass fraction of nanocarbon powder in (d)-(f) is 10%
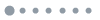
Fig. 5. Effect of humidity sensitive film thickness on sensor response characteristics. (a) Effect of sensitive film thickness on response sensitivity of sensor; (b) cyclic response characteristics of sensor with different sensitive film thicknesses; (c) humidity response characteristics of sensor; (d) humidity response characteristics of sensor when humidity rises and falls. Humidity sensitive film thicknesses in (c)-(d) are 185 μm
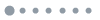
Fig. 6. Effects of temperature and illumination on sensor performance. (a) Temperature response characteristics; (b) humidity response characteristics of sensor at different temperatures; (c) humidity response characteristics of sensor after temperature compensation; (d) effect of continuous light on sensor; (e) effect of light on sensitivity of sensor; (f) effect of light on sensitivity of PTFE capillary encapsulated sensor

Set citation alerts for the article
Please enter your email address