Bo XUE, Lijun ZHU, Xing SU, Li CHEN, Tao ZHOU, Jianfei ZHANG, Kuo HAI, Wen HUANG. Magnetorheological elastomer uniform polishing method for shell components[J]. Optics and Precision Engineering, 2025, 33(3): 402

Search by keywords or author
- Optics and Precision Engineering
- Vol. 33, Issue 3, 402 (2025)

Fig. 1. Schematic diagram of inner surface polishing of thin shell components

Fig. 2. Principle diagram of magnetic field-controlled MRE polishing
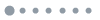
Fig. 3. Schematic diagram of magnetic field-controlled MRE polishing
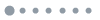
Fig. 4. Pressure cloud diagram of workpiece surface without magnetic field
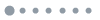
Fig. 5. Schematic diagram of RVE boundary conditions
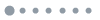
Fig. 6. Cloud diagram of magnetocompressive stress
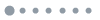
Fig. 7. Magnetocompressive modulus-strain curves
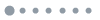
Fig. 8. Pressure cloud map of workpiece surface
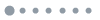
Fig. 9. Pressure curves of polished area
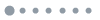
Fig. 10. Distribution curves of workpiece surface pressure
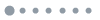
Fig. 11. Velocity distribution in polishing area
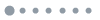
Fig. 12. Three-dimensional characteristic map of removal function
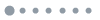
Fig. 13. Removal function curves
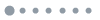
Fig. 14. Schematic diagram of magnetorheological MRE polishing molding
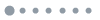
Fig. 15. Schematic diagram of superimposing discrete polishing models at various sampling points
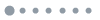
Fig. 16. Magnetron MRE polishing devices
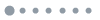
Fig. 17. Schematic diagram of polishing path
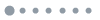
Fig. 18. Surface topography of workpiece after polishing
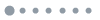
Fig. 19. Radial profile curve of removal volume
|
Table 1. Parameters of 2D RVE model
|
Table 2. Polishing process parameters

Set citation alerts for the article
Please enter your email address