The heterogeneous integration of silicon thin film and lithium niobate (LN) thin film combines both the advantages of the excellent electronics properties and mature micro-processing technology of Si and the excellent optical properties of LN, comprising a potentially promising material platform for photonic integrated circuits. Based on ion-implantation and wafer-bonding technologies, a 3 inch wafer-scale hybrid mono-crystalline Si/LN thin film was fabricated. A high-resolution transmission electron microscope was used to investigate the crystal-lattice arrangement of each layer and the interfaces. Only the H-atom-concentration distribution was investigated using secondary-ion mass spectroscopy. High-resolution X-ray-diffraction

- Chinese Optics Letters
- Vol. 19, Issue 6, 060017 (2021)
Abstract
1. Introduction
Lithium niobate (LN) was one of the most promising multifunctional materials for integrated optics due to its excellent electro-optic (E-O), photo-elastic, and nonlinear-optic properties[
Si on insulator (SOI) was one of the most important material platforms for electronics and photonics due to its excellent electronics properties, high refraction-index contrast, and transparency at optical communication wavelengths[
Heterogeneous integration of Si thin film and LN thin film combines the advantages of two materials, forming a new platform for photonic devices. Several novel devices were fabricated and studied using LN thin film bonded on the top of patterned SOI materials[
Sign up for Chinese Optics Letters TOC. Get the latest issue of Chinese Optics Letters delivered right to you!Sign up now
If the Si thin film sits on the top of the LNOI (Si-LNOI), due to the convenience of Si micro-fabrication, it could provide great design and fabrication flexibility. An amorphous Si (
Mono-crystalline Si thin film has better electronic and optical properties than
2. Fabrication and Experiments
A commercial 3 inch X-cut LNOI wafer (substrate A) (supplied by NANOLN) and a 3 inch floating-zone (FZ) melting bulk Si wafer (substrate B) were used as initial materials. The bulk Si was mono-crystalline, and its orientation was (100). The fabrication steps of the Si-LNOI wafer are shown in Figs. 1(a)–1(d). H ions (
Figure 1.Si-LNOI fabrication processes. (a) H ions were implanted into substrate B. (b) Substrates A and B were bonded by direct wafer bonding. (c) The bonded pair was annealed, and a Si thin film was split from substrate B. (d) The Si-LNOI wafer was annealed, and the surface was polished. (e) Photograph of 3 inch Si-LNOI wafer. (f) Surface roughness of Si thin film measured by AFM.
HRTEM (Tecnai G2 F20 S-Twin, FEI Co., USA) was used to investigate the thin films and interfaces of the Si-LNOI. SIMS (ADEPT-1010, ULVAC-PHI, Inc., Japan) was used to investigate the H concentration in the Si-LNOI. The sample was scanned from the surface to 3200 nm beneath it. The concentration of H atoms was calibrated by
3. Results and Discussion
Using HRTEM, the cross section of the fabricated hybrid Si-LNOI thin films is shown in Fig. 2(a). The sample consists of, from top to bottom, a layer of protection glue (M-bond 610), a 600-nm-thick Si thin film, a 700-nm-thick LN thin film, a 2000-nm-thick
Figure 2.(a) Cross section of Si-LNOI. (b) Interface between Si/LN thin films. (c) Interface between LN/SiO2 thin films. (d) Interface between SiO2 layer and Si substrate.
The H-atom-concentration distribution along the depth direction determined with SIMS is shown in Fig. 3. In the 600-nm-thick Si thin film layer on top of the sample, we found H atoms, which we attributed to the remaining H atoms from ion implantation and subsequent processes. In this layer, the H concentration decreased rapidly with the increasing depth. At a depth of around 600 nm, at the interface between the Si thin film and LN thin film, the H concentration exhibited a sharp peak of
Figure 3.H-atom concentration in Si-LNOI along the depth direction.
An
Figure 4.(a) ω scans of (400) crystal planes of Si thin film and Si substrate. (b) 2θ scans of (400) crystal planes of Si thin film and bulk Si. (c) ω scan of (110) crystal plane of LN thin film. (d) The 2θ scans of (110) crystal planes of LN thin film and bulk LN.
An
Figure 5 shows the Raman spectra. The penetration depth of the 325 nm laser in Si was about 10 nm. The black curve was from bulk Si. The transverse optical phonons mode (TO) peak of bulk Si was at
Figure 5.Raman spectra of bulk Si, mono-crystalline Si thin film, and a-Si thin film.
Figure 6(a) shows an optical microscope picture of the polished end face (in the blue ellipse) of a Si strip-loaded waveguide. Figure 6(b) shows the cross section of a Si strip measured by AFM. The waveguide height was 290 nm, and the waveguide width was 5 µm. The waveguide length was 3 mm. Figure 6(c) shows the measured optical intensity distribution (upper-right) at the 1550 nm wavelength, and the normalized transmission of the quasi-TE (q-TE) mode. The propagation loss was about 6 dB/cm.
Figure 6.(a) Optical microscopy image of Si strip-loaded waveguide with a polished end face. (b) Cross section of a waveguide measured by AFM. (c) Measured optical intensity distribution, and normalized transmission of q-TE mode in Si strip-loaded waveguide.
4. Conclusions
Using ion-implantation and direct-bonding technologies, a 3 inch wafer-scale hybrid Si/LN thin film was successfully fabricated. HRTEM showed that there were clear and smooth amorphous interfaces between the Si/LN thin films,
References
[1] R. S. Weis, T. K. Gaylord. Lithium niobate: summary of physical properties and crystal structure. Appl. Phys. A, 37, 191(1985).
[2] L. Arizmendi. Photonic applications of lithium niobate crystals. Phys. Status Solidi A, 201, 253(2004).
[3] M. Levy, R. M. Osgood, R. Liu, L. E. Cross, G. S. Cargill, A. Kumar, H. Bakhru. Fabrication of single crystal lithium niobate films by crystal ion slicing. Appl. Phys. Lett., 73, 2293(1998).
[4] G. Poberaj, H. Hu, W. Sohler, P. Gunter. Lithium niobate on insulator (LNOI) for micro-photonic devices. Laser Photon. Rev., 6, 488(2012).
[5] A. Guarino, G. Poberaj, D. Rezzonico, P. Gunter. Electro-optically tunable microring resonators in lithium niobate. Nat. Photon., 1, 407(2007).
[6] M. Zhang, C. Wang, R. Cheng, A. Shams-Ansari, M. Loncar. Monolithic ultra-high-Q lithium niobate microring resonator. Optica, 4, 1536(2017).
[7] A. Boes, B. Corcoran, L. Chang, J. Bowers, A. Mitchell. Status and potential of lithium niobate on insulator (LNOI) for photonic integrated circuits. Laser Photon. Rev., 12, 1700256(2018).
[8] J. Wang, F. Bo, S. Wan, W. Li, F. Gao, J. Li, G. Zhang, J. Xu. High-Q lithium niobate microdisk resonators on a chip for efficient electro-optic modulation. Opt. Express, 23, 23072(2015).
[9] C. Wang, M. Zhang, X. Chen, M. Bertrand, A. Shams-Ansari, S. Chandrasekhar, P. Winzer, M. Loncar. Integrated lithium niobate electro-optic modulators operating at CMOS-compatible voltages. Nature, 562, 101(2018).
[10] A. J. Mercante, S. Shi, P. Yao, L. Xie, R. M. Weikle, D. W. Prather. Thin film lithium niobate electro-optic modulator with terahertz operating bandwidth. Opt. Express., 26, 14810(2018).
[11] T. Kovalevich, A. Ndao, M. Suarez, S. Tumenas, Z. Balevicius, A. Ramanavicius, I. Baleviciute, M. Hayrinen, M. Roussey, M. Kuittinen. Tunable Bloch surface waves in anisotropic photonic crystals based on lithium niobate thin films. Opt. Lett., 41, 5616(2016).
[12] H. Liang, R. Luo, Y. He, H. Jiang, Q. Lin. High-quality lithium niobate photonic crystal nanocavities. Optica, 4, 1251(2017).
[13] G. Shao, Y. Bai, G. Cui, C. Li, X. Qiu, D. Geng, D. Wu, Y. Lu. Ferroelectric domain inversion and its stability in lithium niobate thin film on insulator with different thicknesses. AIP Adv., 6, 075011(2016).
[14] L. Chang, Y. Li, N. Volet, L. Wang, J. Peters, J. E. Bowers. Thin film wavelength converters for photonic integrated circuits. Optica, 3, 531(2016).
[15] C. Wang, C. Langrock, A. Marandi, M. Jankowski, M. Zhang, B. Desiatov, M. M. Fejer, M. Loncar. Ultrahigh-efficiency wavelength conversion in nanophotonic periodically poled lithium niobate waveguides. Optica, 5, 1438(2018).
[16] B. N. Slautin, A. P. Turygin, E. D. Greshnyakov, A. R. Akhmatkhanov, H. Zhu, V. Y. Shur. Domain structure formation by local switching in the ion sliced lithium niobate thin films. Appl. Phys. Lett., 116, 152904(2020).
[17] Y. Niu, C. Lin, X. Liu, Y. Chen, X. Hu, Y. Zhang, X. Cai, Y. Gong, Z. Xie, S. Zhu. Optimizing the efficiency of a periodically poled LNOI waveguide using in situ monitoring of the ferroelectric domains. Appl. Phys. Lett., 116, 101104(2020).
[18] Y. Liu, X. Yan, J. Wu, B. Zhu, Y. Chen, X. Chen. On-chip erbium-doped lithium niobate microcavity laser. Sci. China Phys. Mech. Astron., 64, 234262(2021).
[19] Q. Luo, Z. Hao, C. Yang, R. Zhang, D. Zheng, S. Liu, H. Liu, F. Bo, Y. Kong, G. Zhang, J. Xu. Microdisk lasers on an erbium-doped lithium-niobite chip. Sci China Phys. Mech. Astron., 64, 234263(2021).
[20] D. Yin, Y. Zhou, Z. Liu, Z. Wang, H. Zhang, Z. Fang, W. Chu, R. Wu, J. Zhang, W. Chen, M. Wang, Y. Cheng. Electro-optically tunable microring laser monolithically integrated on lithium niobate on insulator. Opt. Lett., 46, 2127(2021).
[21] Z. Chen, Q. Xu, K. Zhang, W. Wong, D. Zhang, E. Y. B. Pun, C. Wang. Efficient erbium-doped thin-film lithium niobate waveguide amplifiers. Opt. Lett., 46, 1161(2021).
[22] X. Yan, Y. Liu, J. Wu, Y. Chen, X. Chen. Integrated spiral waveguide amplifiers on erbium-doped thin-film lithium niobate(2021).
[23] M. Bruel. Silicon on insulator material technology. Electron. Lett., 31, 1201(1995).
[24] R. Soref. The past, present, and future of silicon photonics. IEEE J. Sel. Top. Quantum Electron., 12, 1678(2006).
[25] R. Soref, J. Larenzo. All-silicon active and passive guided-wave components for λ = 1.3 and 1.6 µm. IEEE J. Quantum Electron., 22, 873(1986).
[26] V. Donzella, A. Sherwali, J. Flueckiger, S. M. Grist, S. T. Fard, L. Chrostowski. Design and fabrication of SOI micro-ring resonators based on sub-wavelength grating waveguides. Opt. Express, 23, 4791(2015).
[27] T. Baehr-Jones, T. Pinguet, P. L. Guo-Qiang, S. Danziger, D. Prather, M. Hochberg. Myths and rumours of silicon photonics. Nat. Photon., 6, 206(2012).
[28] L. Chen, J. Chen, J. Nagy, R. M. Reano. Highly linear ring modulator from hybrid silicon and lithium niobate. Opt. Express, 23, 13255(2015).
[29] P. O. Weigel, J. Zhao, K. Fang, H. Al-Rubaye, D. Trotter, D. Hood, J. Mudrick, C. Dallo, A. T. Pomerene, A. L. Starbuck, C. T. DeRose, A. L. Lentine, G. Rebeiz, S. Mookherjea. Bonded thin film lithium niobate modulator on a silicon photonics platform exceeding 100 GHz 3-dB electrical modulation bandwidth. Opt. Express, 26, 23728(2018).
[30] M. He, M. Xu, Y. Ren, J. Jian, Z. Ruan, Y. Xu, S. Gao, S. Sun, X. Wen, L. Zhou, L. Liu, C. Guo, H. Chen, S. Yu, L. Liu, X. Cai. High-performance hybrid silicon and lithium niobate Mach–Zehnder modulators for 100 Gbit/s and beyond. Nat. Photon., 13, 359(2019).
[31] Y. Wang, Z. Chen, L. Cai, Y. Jiang, H. Zhu, H. Hu. Amorphous silicon-lithium niobate thin film strip-loaded waveguides. Opt. Mater. Express, 7, 4018(2017).
[32] Y. Wang, Z. Chen, H. Hu. Analysis of waveguides on lithium niobate thin films. Crystals, 8, 191(2018).
[33] H. Han, B. Xiang. Simulation and analysis of electro-optic tunable microring resonators in silicon thin film on lithium niobate. Sci. Rep., 9, 6302(2019).
[34] N. Goto, G. L. Yip. Characterization of proton-exchange and annealed LiNbO3 waveguides with pyrophosphoric acid. Appl. Opt., 28, 60(1989).
[35] S. Y. Zhu, G. Q. Lo, D. L. Kwong. Low-loss amorphous silicon wire waveguide for integrated photonics: effect of fabrication process and the thermal stability. Opt. Express, 18, 25283(2010).
[36] L. Cai, S. Li, H. Han, H. Hu. Waveguides in single-crystal lithium niobate thin film by proton exchange. Opt. Express, 23, 1240(2015).
[37] D. Fink, J. Krauser, D. Nagengast. Hydrogen implantation and diffusion in silicon and silicon dioxide. Appl. Phys. A, 61, 381(1995).
[38] B. Wang, B. Gu, H. Zhang, X. Feng. Molecular dynamics simulation on hydrogen ion implantation process in smart-cut technology. Acta. Mech. Solida Sin., 29, 111(2016).
[39] H. Hu, R. Ricken, W. Sohler. Lithium niobate photonic wires. Opt. Express, 17, 24261(2009).
[40] I. D. Wolf, C. Jian, W. Spengen. The investigation of microsystems using Raman spectroscopy. Opt. Laser Eng., 36, 213(2001).
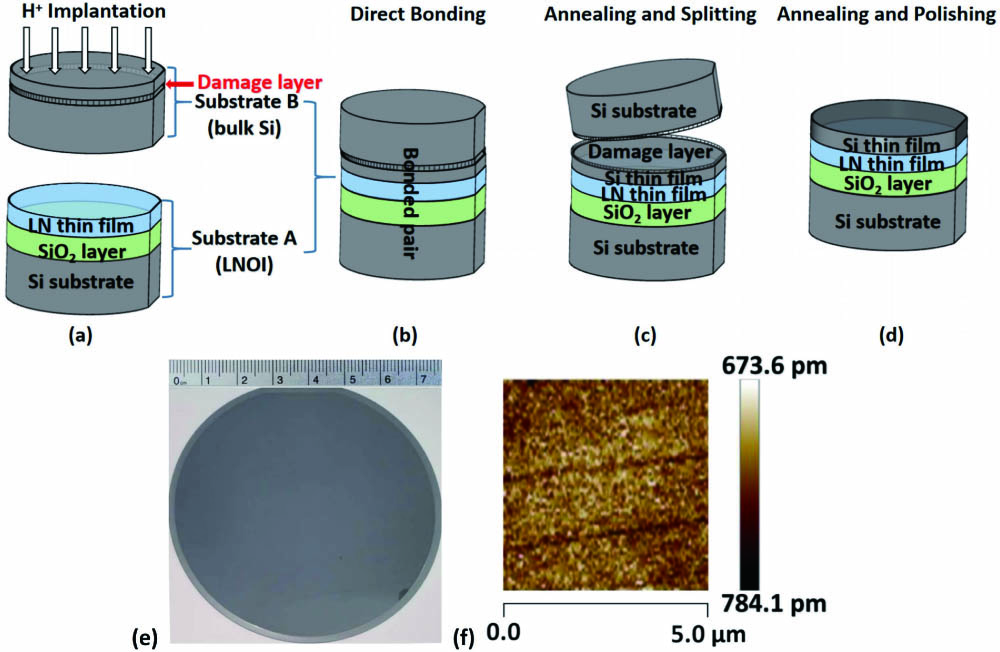
Set citation alerts for the article
Please enter your email address