
- Chinese Optics Letters
- Vol. 20, Issue 1, 011202 (2022)
Abstract
1. Introduction
Optical fiber sensors have the advantages of strong resistance to electromagnetic interference, high sensitivity, no operating current, and ability to work in complex environments[
In the research of high-sensitivity liquid level measurement, some people proposed the MMF cascading hollow-core fiber (HCF) and FBG (SMF-MMF-HCF-SMF/FBG) with an aligned spliced structure[
2. Fabrication and Principle Analysis
The SSC-LPFG is fabricated by polishing on the composite multimode–single-mode–multimode (C-MSM) fiber structure. We use three precision displacement platforms (accuracy is 0.01 mm) to fix the fiber and a fiber cleaver to cut the fiber, using a microscope with CCD for monitoring the cutting fiber length. The specific process is as follows. Firstly, the C-MSM section is fabricated by using an optical fiber cutter (FC-6S) and a fusion optical fiber splicer (Fujikura, 86C). A conventional segment of SMF is spliced to an MMF. After that, the part of a sensing element (MMF) is cleaved, and another segment of SMF is spliced again. As the MMF length is 200 µm, the structure will be more sensitive to changes in the external environment[
Sign up for Chinese Optics Letters TOC. Get the latest issue of Chinese Optics Letters delivered right to you!Sign up now
Secondly, the high-power
Figure 1.Experimental device diagram for fabricating the SSC-LPFG.
Figure 2.Scheme diagram of the SSC-LPFG fiber structure.
Figure 3.(a) Simulated energy transfer diagram. (b) Experimental and simulated transmission spectra of the SSC-LPFG structure.
We use the R-soft simulation software to simulate the energy transfer diagram and the transmission spectrum. In the R-soft simulation process, the core/cladding diameters of the MMF and SMF are 60/125 µm and 8/125 µm, respectively. The mesh size is 0.1 µm in the XY direction and 0.4 µm in the Z direction. We set the SMF cladding RI to 1.4468, the core RI to 1.4521, the MMF cladding RI to 1.4781, and the core RI to 1.4783. Figure 3(a) shows that the energy in the core is gradually coupled to the cladding as the light propagates in the structure. Figure 3(b) shows the experimental and simulated transmission spectra of the SSC-LPFG structure, and the simulation results are consistent with the experimental results.
The phase matching condition satisfies the following relationship[
The RI sensitivity is used to measure the concentration of some substances[
Figure 4.Liquid level measuring device.
Figure 5.Liquid level measurement begins and ends with wavelength drift.
3. Experimental Results and Discussion
The experimental device of the SSC-LPFG for liquid level measurement is shown in Fig. 4. The spiral micrometer pushes the connecting rod down and into the water. The moving distance of the spiral micrometer rod is the same as that of the sensor in the liquid. Figure 6 shows that the levels change from 0 µm to 1400 µm, and the wavelength shift is recorded at the same time every 200 µm. As the liquid level increases, the wavelength of the resonant dip will have a red shift from 1494.6 nm to 1504.2 nm. The sensitivity of the water level measurement is 7080 pm/mm, which is described by linear fitting with a correlation coefficient (
Figure 6.SSC-LPFG liquid level sensing performance at different liquid levels.
To compare the liquid level performance of different polishing depth sensors, we made three sensors with polishing depths of 15 µm, 20 µm, and 25 µm on the second side and compared their liquid level sensing performance. Figures 7(a) and 7(b), respectively, show the resonant dip with three different polishing depths and liquid level sensing performance of sensors. The R2 of the sensor with a polishing depth of 15 µm is 0.93966, which has low linearity and cannot accurately measure the liquid level. The sensor with polishing depth of 20 µm has a liquid level sensitivity of 2930 pm/mm and
Figure 7.(a) Resonant dip of sensors with different polishing depths. (b) Dip wavelength shift versus liquid level (different depth of polishing).
The liquid level performance of SSC-LPFG is repeatedly measured two times to verify stability. The liquid level sensing performance is shown in Fig. 8. It shows that SSC-LPFG has stable performance in liquid level measurement. At the same time, we measure the temperature sensitivity of SSC-LPFG by exposing it to air. The sensor is placed into the temperature control platform, which is set to increase from 20°C to 90°C with a step of 10°C. Due to the difference of the thermal coefficients between the core mode and the cladding mode, the wavelength of the resonant dip is red shifted when the temperature increases, as shown in Fig. 9. The temperature sensitivity of the proposed SSC-LPFG is 24.52 pm/°C with a linear correlation coefficient of 0.97339. The temperature cross sensitivity of the liquid level is about 3.46 µm/°C. The resolution of the liquid level measurements is 2.82 µm, and the temperature resolution is 0.82°C. It reveals that a stable operation in the proposed optical sensor can be obtained.
Figure 8.Liquid level sensing performance.
Figure 9.Response of dip wavelength to temperature changing.
The experimental results are compared with other references in Table 1. It shows that most of the fiber optic sensors with high liquid level sensitivity are prepared with interferometer structures. Generally, the measurement range occupies 30%–70% of the sensor length. The length of the sensor is related to its sensitivity. The SSC-LPFG proposed in this paper sharply improves the sensitivity of the liquid level sensing while ensuring the mechanical performance. In addition, the SSC-LPFG structure has a low temperature response, which helps to reduce the temperature cross sensitivity in liquid level measurement. In terms of size comparison, the length range of the liquid level sensors based on gratings and interferometers is from 10 to tens of millimeters. The SSC-LPFG structure with a length of 3 mm has a strong competitive advantage in terms of integration. The liquid level sensing sensitivity of 7080 pm/mm provides a feasible solution for high-precision liquid level sensing required in medical and other fields.
Grating Length [mm] | Level Range [mm] | Level Sensitivity [pm/mm] | Temperature Crosstalk [μm/°C] | |
---|---|---|---|---|
SMF-MMF-HCF-SMF/FBG with aligned spliced[ | 22 | 10 | 1145 (1.333 RI) | 7.86 |
SRI-based etched chirped FBG[ | 7 | 5.6 | 1214 | 6.5 |
SMF-taper-TCF-taper-SMF[ | 16 | 15 | 1241.6 | 17 |
SMF-PCF-SMF with a bending cantilever setup[ | Not reported | 8 | 111.27 (1.333 RI) | Not reported |
SMF-PMF-SMF with waist enlarged fiber tapers[ | 35 | 28 | 279 | 2.21 |
SMF-PMF-SMF with waist enlarged fiber tapers[ | 40 | 28 | 186 | Not reported |
SMF-MMF-TF-SMF with aligned spliced[ | 18 | 9 | 350 | |
SMF-RCF-MMF-SMF with misaligned spliced[ | 300 | 120 | 6 | 6533 |
LLS based on a single LPFG[ | Not reported | 50 | 70 | Not reported |
This work | 3 | 1.4 | 7080 (1.333 RI) | 3.46 |
Table 1. Parameter Comparison of Optical Fiber Liquid Level Sensors
4. Conclusion
In conclusion, a sensor based on SSC-LPFG for liquid level sensing is proposed. The proposed sensor is obtained by splicing MMFs with the SMF to get the C-MSM structure, and then it is polished on two opposite sides, which are parallel to the axis direction of the fiber. The sensitivity of the cladding mode to the external environment is improved by the insertion of multiple MMFs and double-sided polishing modulation by a high-power
References
[1] J. Villatoro, O. Arrizabalaga, G. Durana, I. S. de Ocariz, E. Antonio-Lopez, J. Zubia, A. Schulzgen, R. Amezcua-Correa. Accurate strain sensing based on super-mode interference in strongly coupled multi-core optical fibres. Sci. Rep., 7, 4451(2017).
[2] Z. Wang, L. Huang, C. Liu, H. Wang, D. Yang. Sensitivity-enhanced fiber temperature sensor based on Vernier effect and dual in-line Mach–Zehnder interferometers. IEEE Sens. J., 19, 7983(2019).
[3] F. Pang, H. Liu, H. Guo, Y. Liu, T. Wang. In-fiber Mach–Zehnder interferometer based on double cladding fibers for refractive index sensor. IEEE Sens. J., 11, 2395(2011).
[4] H. Gong, Y. Xiao, N. Kai, C. L. Zhao, X. Dong. An optical fiber curvature sensor based on two peanut-shape structures modal interferometer. IEEE Photon. Technol. Lett., 26, 22(2014).
[5] B. Wang, W. Zhang, Z. Bai, L. Zhang, T. Yan, L. Chen, Q. Zhou. Mach–Zehnder interferometer based on interference of selective high-order core modes. IEEE Photon. Technol. Lett., 28, 71(2016).
[6] C. He, C. Zhou, Q. Zhou, S. Xie, M. Xiao, J. Tian, Y. Yao. Simultaneous measurement of strain and temperature using Fabry–Pérot interferometry and antiresonant mechanism in a hollow-core fiber. Chin. Opt. Lett., 19, 041201(2021).
[7] J. E. Antonio-Lopez, J. J. Sanchez-Mondragon, P. Likamwa, D. A. May-Arrioja. Fiber-optic sensor for liquid level measurement. Opt. Lett., 36, 3425(2011).
[8] Z. Song, Y. Li, J. Wei, J. Hu. Optical fiber torsion sensor based on pre-twisted polarization-maintaining fiber Sagnac loop mirror structure. Laser Optoelectron. Prog., 58, 1706007(2021).
[9] F. Baldini, M. Brenci, F. Chiavaioli, A. Giannetti, C. Trono. Optical fibre gratings as tools for chemical and biochemical sensing. Anal. Bioanal. Chem., 402, 109(2012).
[10] C. A. F. Marques, A. Pospori, D. Sáez-Rodríguez, K. Nielsen, O. Bang, D. J. Webb. Fuel level sensor based on polymer optical fiber Bragg gratings for aircraft applications. Int. Soc. Opt. Photon., 1674, 5759(2016).
[11] F. Li, N. Zhang, D. Xu, W. Niu, B. Li. Design of liquid level sensor of small range and multi-medium based on infrared correlation light curtain technology. Environ. Technol., 1004, 7204(2016).
[12] Y. Xu, Z. Wang. The study and implementation of connected liquid level detection technology applying to medical equipment. IEEE Workshop on Electronics, Computer and Applications, 333(2014).
[13] I. K. Ilev, R. W. Waynant. All-fiber-optic sensor for liquid level measurement. Rev. Sci. Instrum., 70, 2551(1999).
[14] T. Guo, Q. Zhao, Q. Dou, Z. Hao, L. Xue, G. Huang, X. Dong. Temperature-insensitive fiber Bragg grating liquid-level sensor based on bending cantilever beam. IEEE Photon. Technol. Lett., 17, 2400(2005).
[15] K. R. Sohn, J. H. Shim. Liquid-level monitoring sensor systems using fiber Bragg grating embedded in cantilever. Sens. Actuator A, 152, 248(2009).
[16] H. Fu, X. Shu, A. Zhang, W. Liu, I. Bennion. Implementation and characterization of liquid-level sensor based on a long-period fiber grating Mach–Zehnder interferometer. IEEE Sens. J., 11, 2878(2011).
[17] Y. Huang, B. Chen, G. Chen, H. Xiao, S. U. Khan. Simultaneous detection of liquid level and refractive index with a long-period fiber grating based sensor device. Meas. Sci. Technol., 24, 095303(2013).
[18] Q. Rong, X. Qiao, Y. Du, S. Hao, D. Feng, R. Wang, M. Hu, Z. Feng. In-fiber quasi-Michelson interferometer for liquid level measurement with a core-cladding-modes fiber end-face mirror. Opt. Lasers Eng., 57, 53(2014).
[19] C. Rodríguez, M. Ribeiro, A. Frizera-Neto, C. Castellani, M. J. Pontes. Envelope-based technique for liquid level sensors using an in-line fiber Mach–Zehnder interferometer. Appl. Opt., 55, 9803(2016).
[20] Y. Jin, X. Dong, M. Sun. All-fiber Mach–Zehnder interferometer for liquid level measurement. IEEE Sens. J., 15, 3984(2015).
[21] Y. Zhang, C. Weigang, Y. Lei, S. Wang, T. Yan. High sensitivity optical fiber liquid level sensor based on a compact MMF-HCF-FBG structure. Meas. Sci., 29, 055104(2018).
[22] H. Y. Chang, Y. C. Chang, H. J. Sheng, M. Y. Fu, W. F. Liu, R. Kashyap. An ultra-sensitive liquid-level indicator based on an etched chirped-fiber Bragg grating. IEEE Photon. Technol. Lett., 28, 268(2015).
[23] M. Shao, L. Han, J. Liang, R. Zhang, H. Gao. A high sensitivity liquid level sensor based on single mode-taper-thin core-taper-single mode fiber structure. Meas. Sci., 31, 105101(2020).
[24] S. Zhang, S. Deng, Z. Wang, W. Yang, C. Sun, X. Chen, Y. Ma, Y. Li, T. Geng, W. Sun, L. Yuan. Optimization and experiment of a miniature multimode fiber induced-LPG refractometer. OSA Continuum., 2, 2190(2019).
[25] S. W. James, R. P. Tatam. Optical fibre long-period grating sensors: characteristics and application. Meas. Sci., 14, 49(2003).
[26] O. Duhem, J. F. Henninot, M. Warenghem, M. Douay. Demonstration of long-period-grating efficient couplings with an external medium of a refractive index higher than that of silica. Appl. Opt., 37, 7223(1998).
[27] H. J. Patrick, A. D. Kersey. Analysis of the response of long period fiber gratings to external index of refraction. J. Lightwave Technol., 16, 1606(1998).
[28] X. Zhang, W. Peng, Z. Liu, Z. Gong. Fiber optic liquid level sensor based on integration of lever principle and optical interferometry. IEEE Photon. J., 6, 6801108(2014).
[29] H. Gong, H. Song, S. Zhang, K. Ni, X. Dong. An optical liquid level sensor based on polarization-maintaining fiber modal interferometer. Sens. Actuator A, 205, 204(2014).
[30] L. Li, L. Xia, Z. Xie, D. Liu. All-fiber Mach–Zehnder interferometers for sensing applications. Opt. Express, 20, 11109(2012).
[31] C. Castellani, H. Ximenes, R. L. Silva, A. Frizera-Neto, M. Ribeiro, M. J. Pontes. Multi-parameter interferometric sensor based on a reduced diameter core axial offseted fiber. IEEE Photon. Technol. Lett., 29, 239(2017).
[32] B. M. Mao, J. Canning, G. Peng, B. Zhou. Liquid level measurement sensor using a long-period fiber grating. Proc. SPIE, 8351, 83511N(2012).
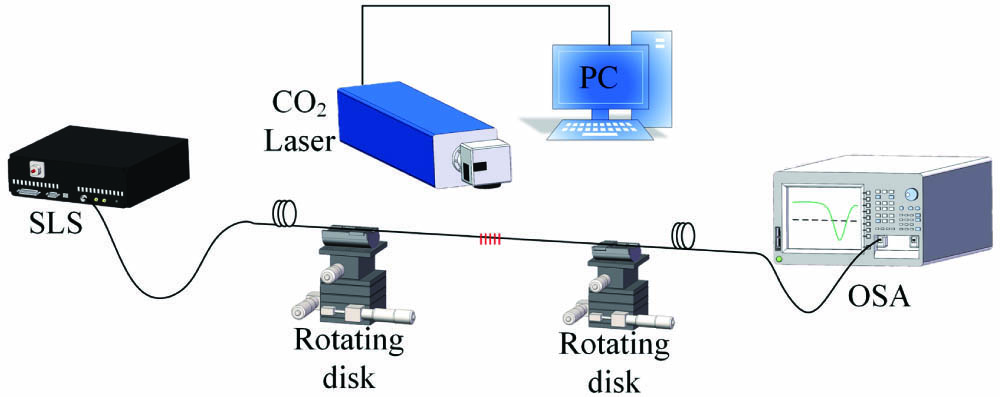
Set citation alerts for the article
Please enter your email address