Kaiqiang Xian, Jingzhu Pang, Jun Hu. Surface Crack Size Detection in Nuclear Fuel Rods Based on Line Structured Light[J]. Laser & Optoelectronics Progress, 2020, 57(22): 221013

Search by keywords or author
- Laser & Optoelectronics Progress
- Vol. 57, Issue 22, 221013 (2020)
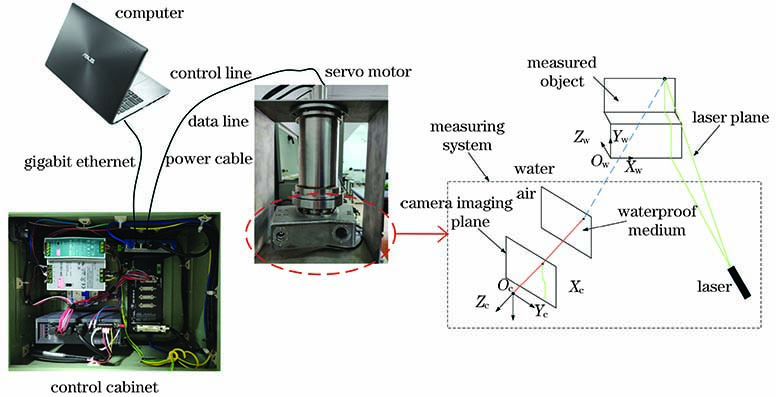
Fig. 1. Underwater nuclear fuel rod detection system
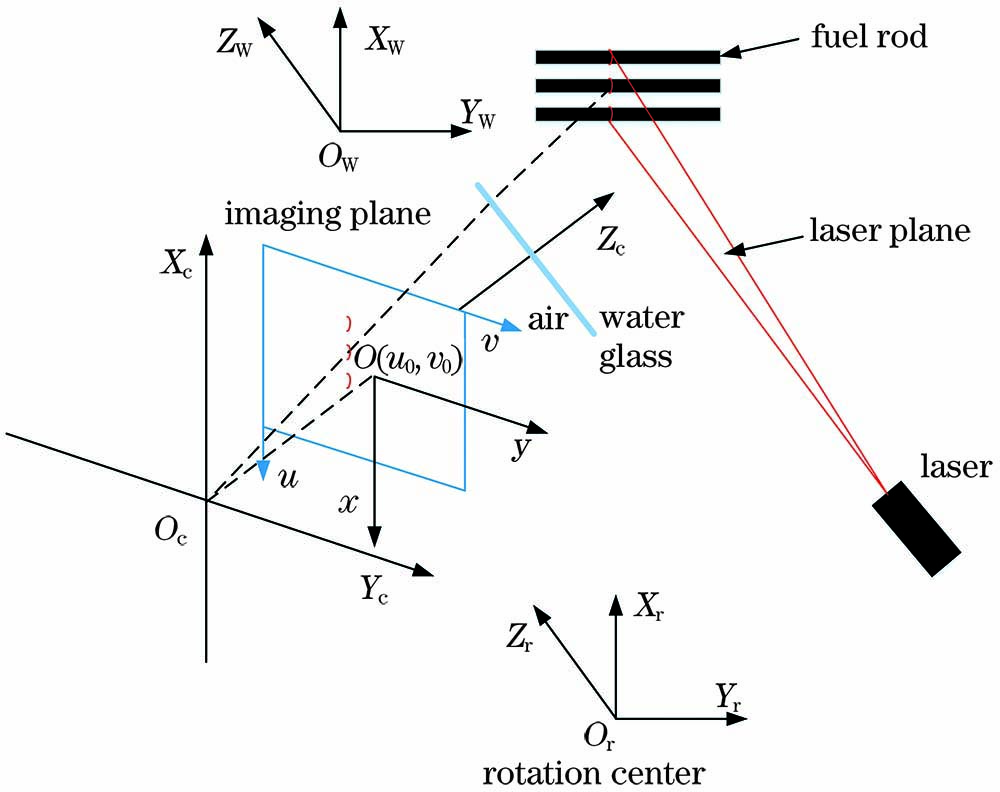
Fig. 2. Mathematical model of mearsured system
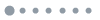
Fig. 3. Conversion relationship of rotation center coordinate
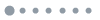
Fig. 4. Position and frame selection for region of interest. (a) Original image; (b) diagram of frame selection effect
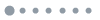
Fig. 5. Horizontal projection and first-order differential results for fuel rods
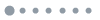
Fig. 6. Expansion of the frame selection area. (a) |im-is|≥6; (b)im-is|<6
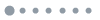
Fig. 7. Gray statistics image
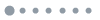
Fig. 8. Enlarged view of cracks
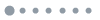
Fig. 9. Upper boundary judgment method. (a) Boundary pixel type one; (b) boundary pixel type two; (c) boundary pixel type three; (d) boundary pixel type four
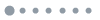
Fig. 10. Adaptive threshold segmentation
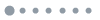
Fig. 11. Acquisition of structured light bar center at the crack. (a) With a crack; (b) without cracks;(c) removing cracked area for Fig. 11 (a); (d) removing cracked area for Fig. 11 (b); (e) normal light bar center; (f) incomplete light bar center
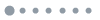
Fig. 12. Structured light center curve fitting
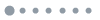
Fig. 13. Crack boundary treatment. (a) Diagram of boundary decision; (b) intersection diagram of center line and boundary
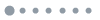
Fig. 14. Diagram of distance sampling
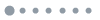
Fig. 15. Platform operation flowchart
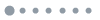
Fig. 16. Underwater experimental device
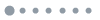
Fig. 17. Photos taken. (a) Exposure of 200; (b) exposure of 300; (c) exposure of 400; (d) exposure of 500; (e) crack size of 190.0μm; (f) crack size of 181.6μm; (g) crack size of 128.6μm
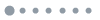
Fig. 18. Cracks on the surface of nuclear fuel rods. (a) Crack on the surface of fuel rod; (b) point cloud of crack on fuel rod surface
|
Table 1. Center line fitting errors
|
Table 2. Tabel 2 Test results of crack size
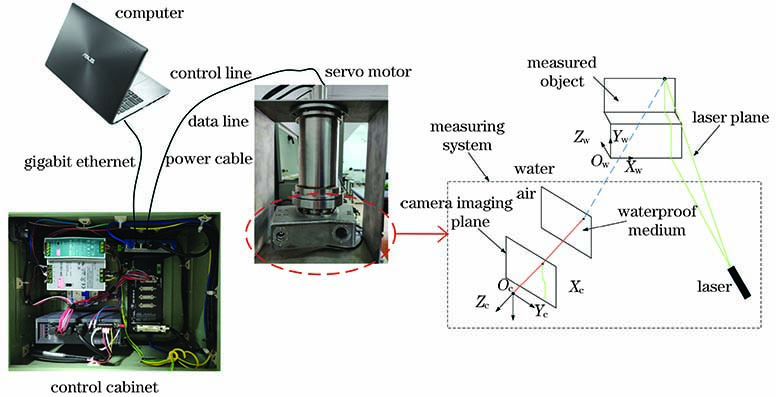
Set citation alerts for the article
Please enter your email address