Guolu Yin, Zhou Xu, Rui Jiang, Ming Deng, Tao Zhu. Optical Fiber Distributed Three-dimensional Shape Sensing Technology Based on Optical Frequency-Domain Reflectometer[J]. Acta Optica Sinica, 2022, 42(1): 0106002

Search by keywords or author
- Acta Optica Sinica
- Vol. 42, Issue 1, 0106002 (2022)
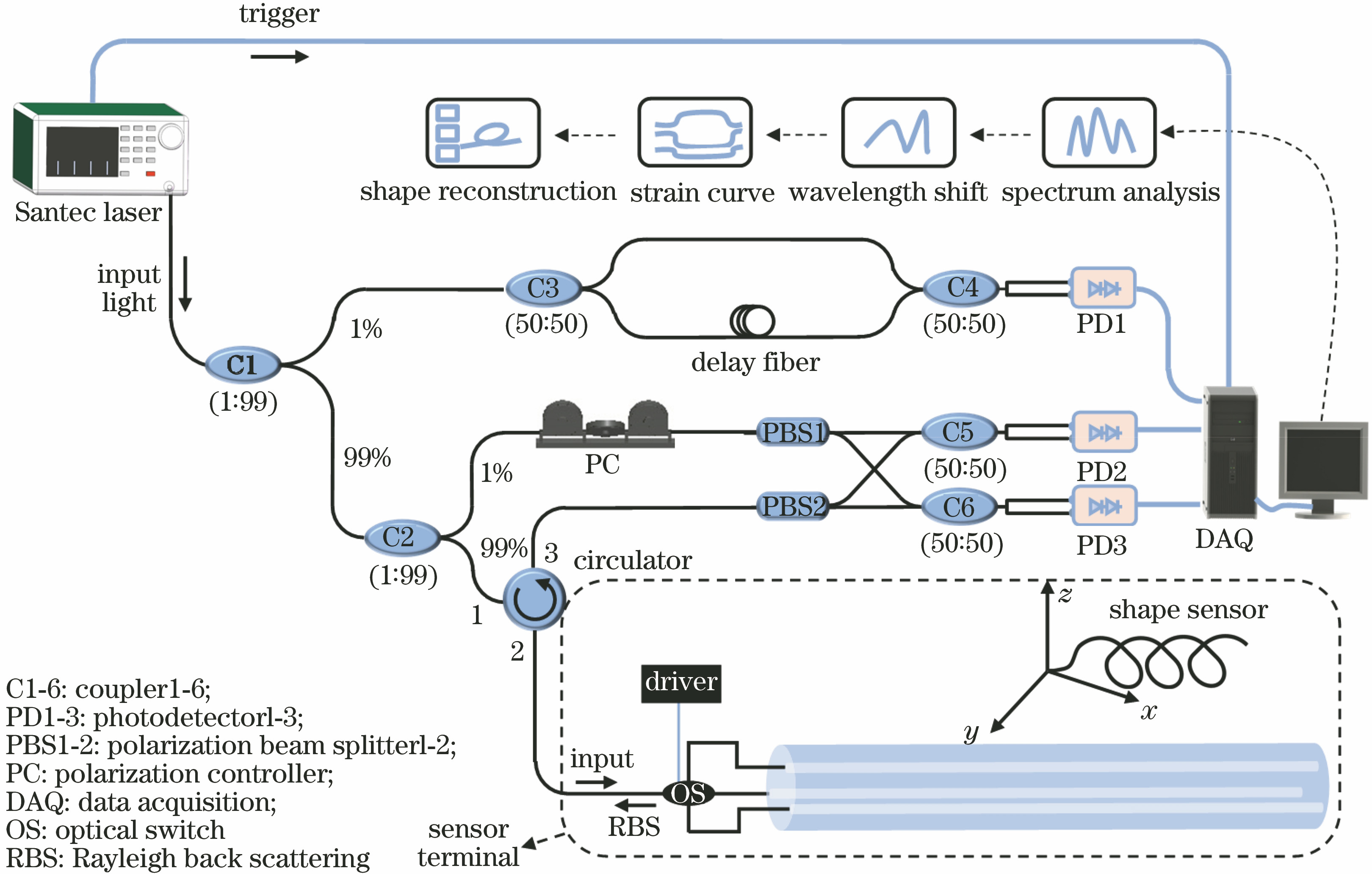
Fig. 1. Schematic diagram of shape sensing based on the optical frequency domain reflectometer
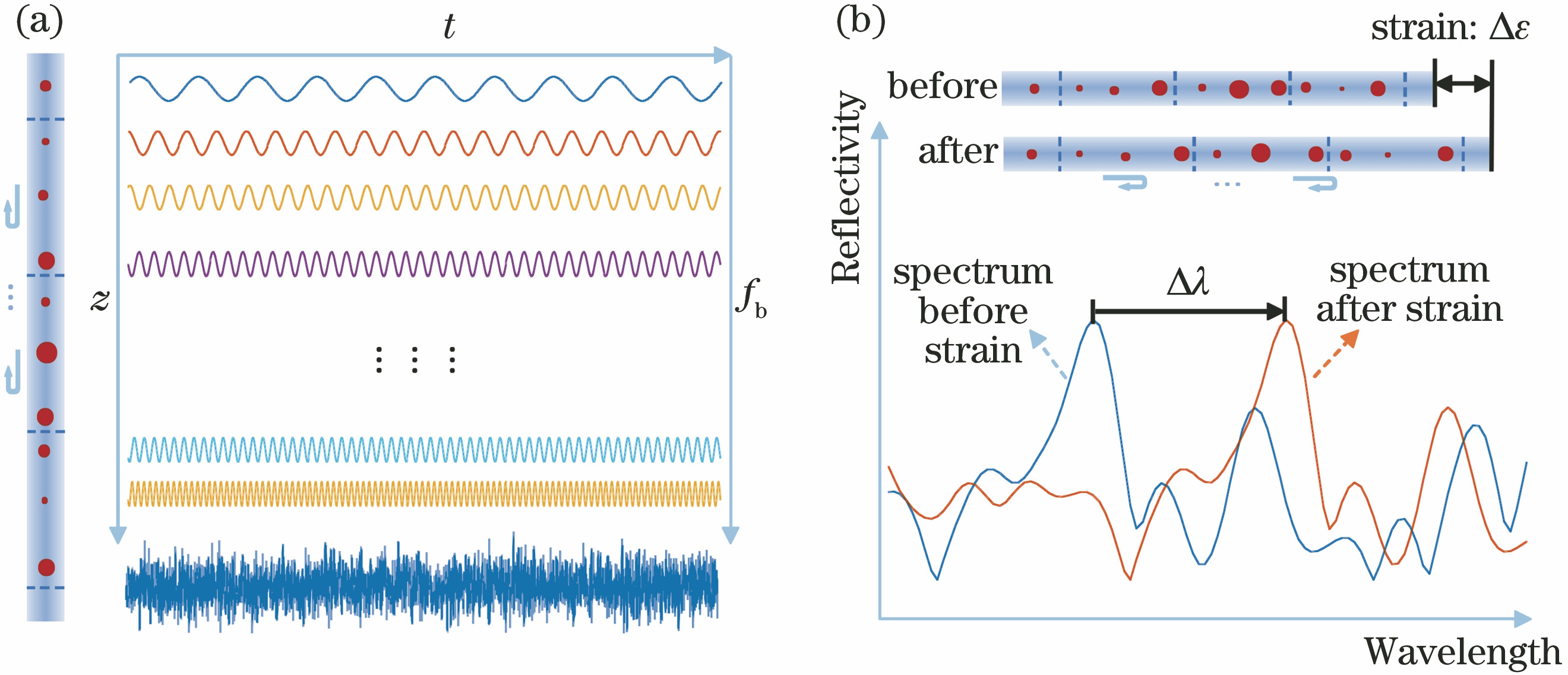
Fig. 2. Principle diagram of the optical frequency domain reflectometer. (a) Superposition of interference beat signals; (b) spectrum of beat frequency interference before and after strain
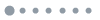
Fig. 3. Bending diagram of shape sensor
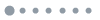
Fig. 4. The wavelength shift measured by optical frequency domain reflectometer when seven core fiber has a bending radius of 10 cm. (a) Without torsion; (b) with torsion
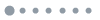
Fig. 5. Structure diagram of shape sensor
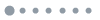
Fig. 6. Signal demodulation process of the optical frequency domain reflectometer
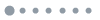
Fig. 7. Calibration experiment of shape sensor. (a) Experimental setup; (b) wavelength shift curves of three fibers with the same bending radius and different bending direction
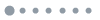
Fig. 8. Experimental results of bending sensitivity calibration. (a) Wavelength shift along the sensing fiber #1 under different curvatures; (b) variation of wavelength shift of optical fibers #1, #2 and #3 with curvature
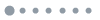
Fig. 9. Experiment of two dimensional shape sensing. (a) Experimental setup; (b) measured 2D shape
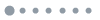
Fig. 10. Experiment of 3D shape sensing. (a) Experimental setup; (b) measured 3D shape
|
Table 1. Comparison of typical optical fiber shape sensing technologies
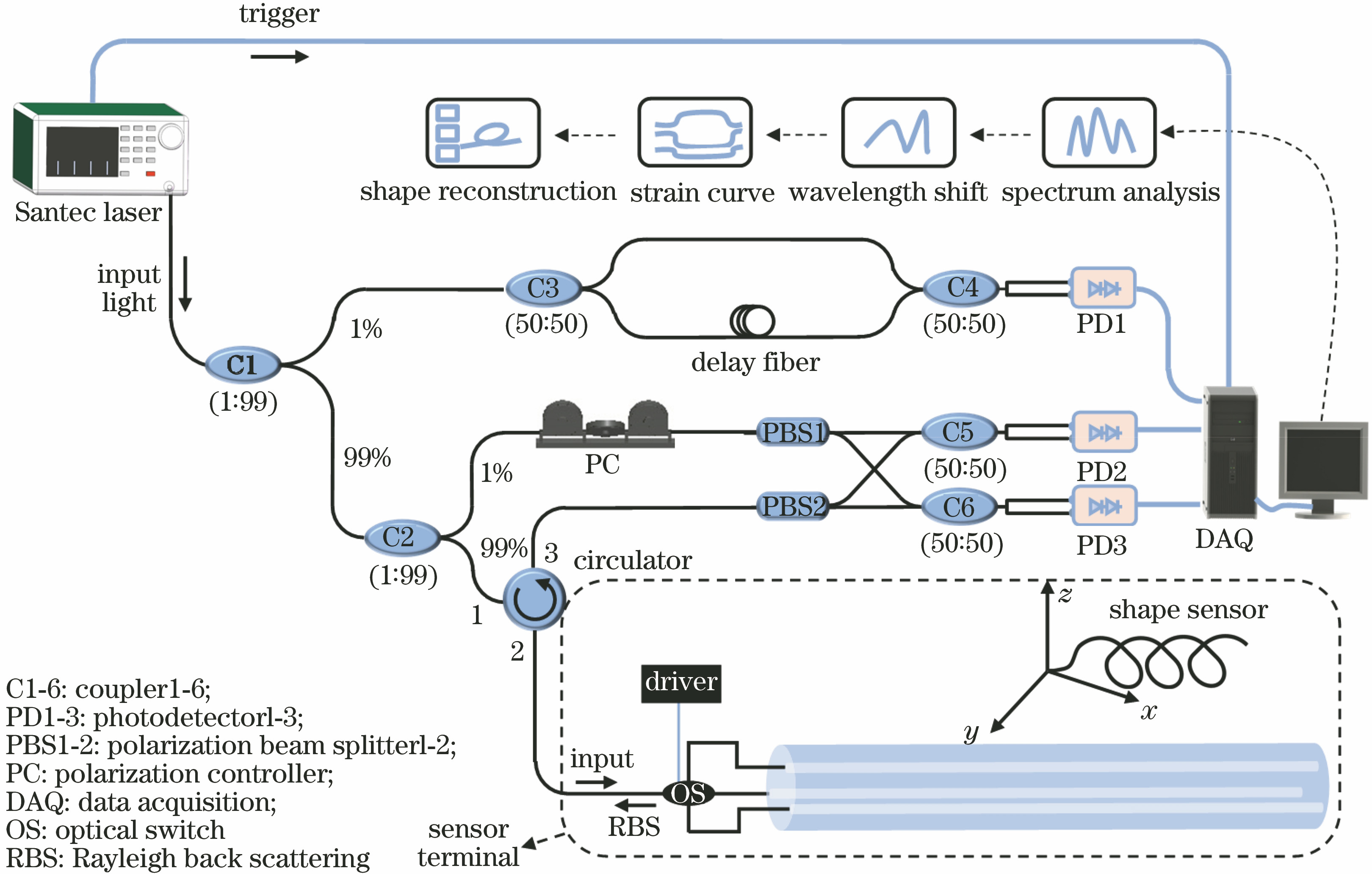
Set citation alerts for the article
Please enter your email address