Gangyi Zhu, Xin Ji, Zhenfu Zhang, Xingcan Yan, Ying Yang, Feifei Qin, Xin Li, Jiagui Wu, Xiaojuan Sun, Junbo Yang, Yongjin Wang, "Electrically pumped optomechanical beam GaN-LED accelerometer based on the quantum-confined Stark effect," Photonics Res. 11, 1583 (2023)

Search by keywords or author
- Photonics Research
- Vol. 11, Issue 9, 1583 (2023)
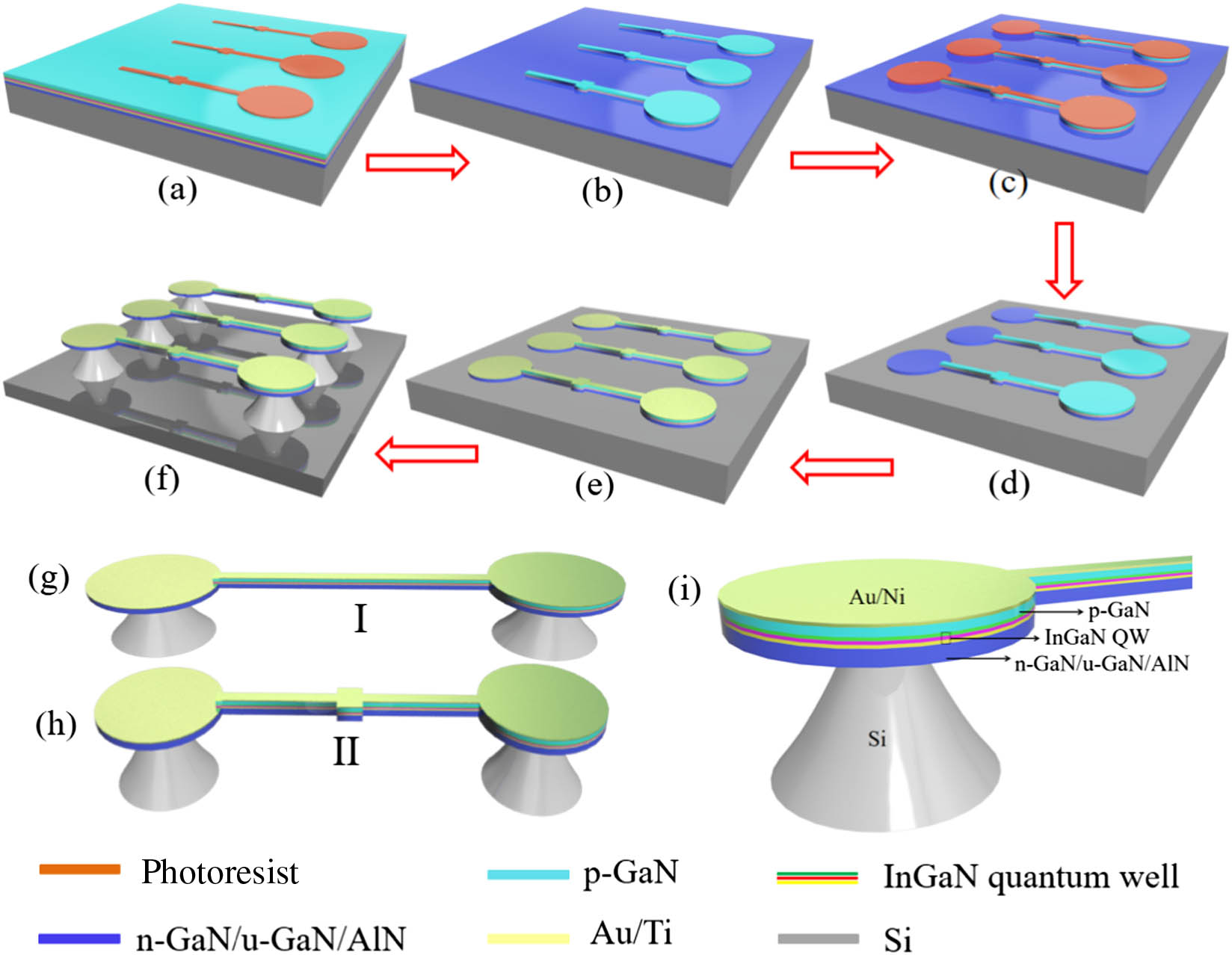
Set citation alerts for the article
Please enter your email address