
- Journal of Inorganic Materials
- Vol. 34, Issue 8, 904 (2019)
Abstract
SiCf/SiC composites are considered as potential materials for hot-section components in advanced aircraft engine due to their outstanding properties, such as low density, superior toughness, high temperature resistance and non-brittle fracture failure[
The rare earth silicate (RE2Si2O7, RE=Y, Sc, Yb, Lu) were reported to show low volatilization rate in water vapor environment and the ability to endure temperature higher than 1482 ℃ for thousands of hours[
The aim of this research is to get a robust matrix with excellent corrosion resistance properties by introducing layered yttrium silicate (Y2Si2O7) in SiCf/SiC composites. In this study, yttrium oxide (Y2O3) was generated by the solution impregnation and pyrolysis method in SiC fiber preform firstly, and layered Y2Si2O7 was obtained from the transformation of Y2O3 during chemical vapor infiltration (CVI) process. It is expected that the service reliability of SiCf/SiC composites increases as long as the composites are modified by layered-Y2Si2O7.
1 Experimental
1.1 Fabrication of the composites
2D stitched fabric of silicon carbide fibers (National University of Defense Technology, China) were used as the preforms. BN interphase was deposited by chemical vapor infiltration (CVI). Boron trichloride (BCl3) and Ammonia (NH3) (2 : 1, molar ratio) were carried by hydrogen (H2) to be deposited at 1073 K under a total pressure of 3.0 kPa. To prevent the erosion of BN interphase, a thin SiC layer was also prepared by isothermal CVI at 1000 ℃ under a total pressure of 5 kPa, in which methyltrichlorosilane (MTS) was used as the precursor of SiC. After the BN interphase and SiC layer were applied on the surface of the fibers, a solution made up of Y(NO3)3∙6H2O (Aladdin, Shanghai, China, 99.99%) and ethanol was introduced into SiC preform by vacuum impregnating process. Then the preform was heated to 1000 ℃ for 0.5 h under argon atmosphere and the related preform was named P1. SiC matrix was then prepared under the same CVI condition as SiC layer. During the process, layered-Y2Si2O7 structure could be obtained in SiCf/SiC composites. Solution impregnation pyrolysis process and isothermal CVI were repeated once or three times to obtain the dense composite C1 and C2, respectively, in which one layer or three layers of Y2Si2O7 in the matrix could be prepared. A reference sample named C0 was also prepared by the same method but without the solution impregnation pyrolysis.
1.2 Characterization
Phase composition of the samples was analyzed using a Micro-region X-ray diffraction (XRD, D8 DISCOVER DAVINCI, Germany). The microstructures of the composites before and after oxidation were characterized using scanning electron microscope (SEM, S-4800, Hitachi, Tokyo, Japan). The elemental analysis was conducted by energy dispersive spectroscopy (EDS, Aztec X-Max 20, Oxford, UK).
The oxidation behavior of the composites was investigated in wet oxygen environment at 1400 ℃ with the heating and cooling rates of about 5 ℃/min, and the flow rate of O2/H2O was kept constant at 500 mL/min (200 mL O2 + 300 mL H2O) by a liquid phase vaporization system (LVD-F1, Hefei Crystal Materials Technology Co., Ltd., Hefei, China). The detail about this system was described elsewhere[
2 Results and discussion
2.1 Chemical composition
Micro-region X-ray diffraction (XRD) patterns of C0, C1, C2 and P1 are shown in Fig. 1(a). It can be found that the matrix of sample C0 is mainly made of β-SiC, which is obtained from the pyrolysis of MTS by CVI. It is shown from sample P1 that Y2O3 can be formed in the preform after the pyrolysis of Y(NO3)3·6H2O. From the patterns of sample C1 and C2, β-SiC and Y2Si2O7 (z- Y2Si2O7:JCPDS Card 21-1459) are found. In order to understand the formation of Y2Si2O7, XRD of Y2O3 before and after CVI is carried out (Fig. 1(b)). It shows that Y2O3 can be transformed into Y2Si2O7 completely after CVI. In addition, Energy Disperse Spectroscopy (EDS) of the representative white region in sample P1 and C1 shows that the atomic ratio of Y to O changed from approximately 1 : 2 to 1 : 3.5 (Fig. 2(a-b)), and it can be inferred that Y exists in the form of Y2Si2O7 in sample C1. It demonstrates that the transformation of Y2Si2O7 from Y2O3 with CVI occurs.
Figure .Micro-region XRD patterns of samples (a) C0, C1, C2 and P1, and (b) Y2O3 before and after CVI
Figure .SEM images of samples (a) P1 and (b) C1 with insets showing EDS analysis of the white region in sample P1 and C1
2.2 Morphology of the samples surfaces before and after oxidation
Scanning electron microscope (SEM) images of the polished cutting surface of these composites are shown in Fig. 2. Y2Si2O7 with layered distribution can be found around the fiber bundles before oxidation. Sample C1 shows a single-layer distribution (Fig. 3(a)) while sample C2 shows an obvious three-layer distribution (Fig. 3(b)). As it is not dense enough for Y2O3 after pyrolysis, SiC can be deposited in the enrichment area of Y2Si2O7 due to the inner pores working as the deposition channels. Therefore, the white region is the mixing region of Y2Si2O7 and SiC.
Figure .SEM images of the cutting surface of the composites
Fig. 4 illustrates the oxidation process. The oxidation of SiC matrix in wet oxygen consists of two parts: oxidation of SiC by O2 to form silica which is a low viscosity melt in wet oxygen environment, and volatilization of the silica in the form of Si(OH)4 (g) by reaction with H2O. Both SiC and Y2Si2O7 exist on the surface before oxidation, and Y2Si2O7 remain stable in wet oxygen at high temperature. The volatilization of Si(OH)4 will promote the redistribution of Y2Si2O7 in the surface layer of silicate melt during the oxidation process. Therefore, a large amount of dispersed Y2Si2O7 can be found on the surface of the composites after oxidation. In sample C2, Y2Si2O7 was more abundant and distributed more widely before the oxidation, so the degree of dispersion is more pronounced and the surface of Y2Si2O7 is denser than that of sample C1 after the oxidation (Fig. 3(e-f)). By contrast, for sample C0, the silica glass phase precipitates into crystalline cristobalite in oxidation environment at 1400 ℃. Due to the mismatch of the coefficients of thermal expansion (SiO2 glass phase: ~7×10-7 K-1, crystalline cristobalite: ~170×10-7 K-1), a large number of cracks on the surface are formed during the cooling process (Fig. 3(d)), which provide a diffusion channel for oxidizing atmosphere[
Figure .Oxidation models of SiCf/SiC-Y2Si2O7 in wet oxygen
2.3 Mechanical properties
The strength/oxidation time and strength retention rate/oxidation time of the composites are shown in Fig. 5. Before oxidation, the bending strength of C1 and C2 is (474.93±24.29) MPa and (383.61±30.29) MPa, respectively, while sample C0 reaches (532.28±32.28) MPa. As the impregnation and pyrolysis times increases, the porosity of the composites increase gradually (Table 1) since Y2O3 can block some pores and hinder the permeation of reactive gases during the CVI process, which may lead to the difference of the mechanical properties. During the oxidation process, Y2Si2O7 can disperse on the surface of sample C1 and sample C2 to prevent further diffusion of the oxidizing atmosphere. The mechanical properties of the materials after oxidation are better preserved. After 80 h of oxidation, the strength retention of sample C0, C1 and C2 is about 50.11%, 60.38% and 71.93%, respectively.
Figure .(a) Mechanical strength and (b) strength retention of the composites after oxidation for different time
C0 | C1 | C2 | |
---|---|---|---|
Porosity/% | 8.69±0.27 | 11.49±0.93 | 13.63±0.35 |
Density/(g•cm-3) | 2.75±0.02 | 2.60±0.02 | 2.50±0.01 |
Table 1.
Density and porosity of the composites
3 Conclusion
Layered Y2Si2O7 was prepared to modify SiCf/SiC composites by solution impregnation and pyrolysis combining isothermal CVI process. The result shows that Y2O3 could be converted into Y2Si2O7 by CVI. The oxidation behavior of SiCf/SiC composites modified by layered-Y2Si2O7 were tested in the wet oxygen environment at 1400 ℃. It demonstrates that Y2Si2O7 could form a protective layer over the sample surface and block the oxidizing atmosphere. After the oxidation for 80 h, the retention rate of bending strength of the composite with three layers of Y2Si2O7 reaches 71.93%, which is 43.54% higher than SiCf/SiC without Y2Si2O7. It indicates that the addition of rare earth silicate with layered structure could improve the oxidation resistance of SiCf/SiC composites in wet oxygen environment, which has beneficial effect on further application in engine components.
References
[1] N P PADTURE. Advanced structural ceramics in aerospace propulsion. Nature Materials, 15, 804-809(2016).
[3] HONG-DA WANG, HAI-JUN ZHOU, SHAO-MING DONG et al. Corrosion behavior of SiCf/SiC composites in high temperature fluoride salt environment. Journal of Inorganic Materials, 32, 1133-1140(2017).
[4] H E EATON, G D LINSEY. Accelerated oxidation of SiC CMC's by water vapor and protection
[6] I SPITSBERG, J STEIBEL. Thermal and environmental barrier coatings for SiC/SiC CMCs in aircraft engine applications. International Journal of Applied Ceramic Technology, 1, 291-301(2004).
[7] JIA LIU, LI-TONG ZHANG, FEI HU et al. Polymer-derived yttrium silicate coatings on 2D C/SiC composites. Journal of the European Ceramic Society, 33, 433-439(2013).
[8] YUE XU, XUN-XUN HU, FANG-FANG XU et al. Rare earth silicate environmental barrier coatings: present status and prospective. Ceramics International, 43, 5847-5855(2017).
[12] SI-WEI LI, LI-TONG ZHANG, YONG-SHENG LIU et al. Self-healing behavior of 2D C/SiC modified by partial boron carbide matrix after annealing at low temperature in wet oxygen. Journal of Inorganic Materials, 25, 1199-1203(2010).
[15] E E BOAKYE, P MOGILEVSKY, T A PARTHASARATHY et al. Processing and testing of RE2Si2O7 fiber-matrix interphases for SiC-SiC composites. Journal of the American Ceramic Society, 99, 415-423(2016).
[16] E E BOAKYE, T S KEY, T A PARTHASARATHY et al. Evaluation of SiC/SiC minicomposites with yttrium disilicate fiber coating. Journal of the American Ceramic Society, 101, 91-102(2018).
[17] QING-LIANG SHAN, QIAN FENG, JIAN-BAO HU et al. Oxidation behavior in wet oxygen environment of Al2O3 added reaction-sintered Si-B-C ceramics. Ceramics International, 44, 4009-4015(2018).
[18] QING-LIANG SHAN, QIAN FENG, JIAN-BAO HU et al. MD oxidation behavior in wet oxygen environment of Al2O3 modified SiCf/(SiC + B4C) at 1200 ℃. Materials Letters, 228, 277-280(2018).
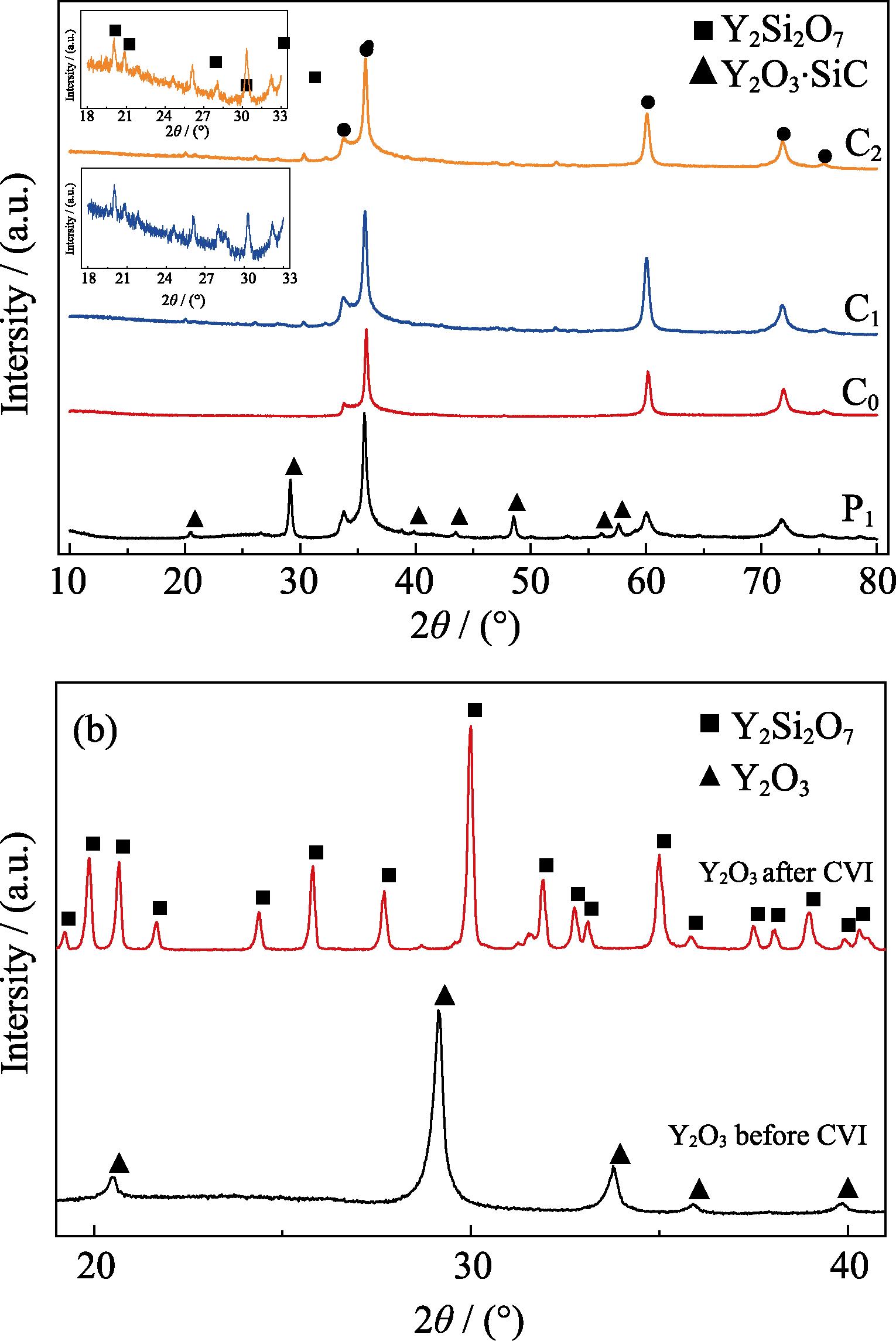
Set citation alerts for the article
Please enter your email address