
- Journal of the European Optical Society-Rapid Publications
- Vol. 18, Issue 1, 2022002 (2022)
Abstract
1 Introduction
Large astronomical optics computer controlled optical surfacing (CCOS) processes require a vast workforce and financial resources [
2 Multiplexed dual-tool computer controlled optical surfacing
The efficiency of the optics manufacturing process can be significantly improved with multiple fabrication tools by adopting a simultaneous CCOS multiplexing process [
Figure 1.The 8.4 m-class large polishing machine (LPM) with dual tool configuration at the University of Arizona is shown on the left. The middle figure shows an example surface error map of a synthetic 8.4 m diameter mirror with two tool feed modes: (a) “in–out” and (b) “in–in” feed modes for the multiplexed dual-tool polishing case [
A 1.2 m diameter stressed lap (the top tool in
As a benchmark, a traditional (i.e., non-multiplexed), sequential two-tool run case is simulated in
Figure 2.CCOS benchmark case study showing the final surface error map and the time evolution of the CCOS run parameters through two sequential single-tool runs using (a) Tool1 and (b) Tool2.
In the dual-tool multiplexed case, Tool1 is selected as the primary tool so that the run parameters of Tool2 (i.e., dwell time and velocity) are adjusted and synchronized with the primary tool [
Figure 3.Dual-tool multiplexing simulation tool path (left), final surface error map (middle), and the time evolution of the CCOS run parameters (right) for two-tool feed modes: (a) “in–in” feed mode and (b) “in–out” feed mode.
The “in–in” tool feed mode shows a shorter dwell time (21.55 h) than the “in–out” feed mode (25.20 h). Also, when the “in–in” feed mode is used (see
Compared with the total 40.78 h two sequential single-tool runs (
3 Generalized multiplexing of concurrent tools
The CCOS multiplexing process [
Figure 4.The top two rows show differential surface error maps at different progressive time instances obtained using the multi-tool multiplexing simulation (cumulated total dwell time runs from 1 through 6, note the changing scalebar), bringing down the initial (i.e., total dwell time = 0 h) surface figure error of 2210 nm RMS to 7.9 nm RMS using four tools simultaneously. The bottom row shows the tool path (left), final surface error map (middle), and time evolution of the CCOS run parameters (right).
4 Conclusion and discussion
Several deterministic computer controlled subaperture tool figuring technologies have been developed and verified through accurate matching between predicted and measured removal maps in the precision large aspheric optics manufacturing community. Various polishing process chains are utilized for cost effective large aspheric optics manufacturing. However, for most CCOS processes, the polishing process has been implemented using a single tool or different tools sequentially in separate polishing cycles, e.g., sequentially using bonnet, magnetorheological finishing, and ion beam figuring or using the same tool with different polishing contact spot sizes sequentially. The significant portion of the uncharted territory is not in enhancing deterministic removal using refined polishing parameter control but in combining multiple polishing runs into a single simultaneous run by multiplexing.
References
[1] R.A. Jones. Computer control for grinding and polishing.
[2] R.E. Wagner, R.R. Shannon. Fabrication of aspherics using a mathematical model for material removal.
[3] H.M. Pollicove, E.M. Fess, J.M. Schoen. Deterministic manufacturing processes for precision optical surfaces. Tustison R.W. (eds),
[4] D.D. Walker, D. Brooks, A. King, R. Freeman, R. Morton, G. McCavana, S.W. Kim. The “Precessions” tooling for polishing and figuring flat, spherical and aspheric surfaces.
[5] J.H. Burge, S. Benjamin, D. Caywood, C. Noble, M. Novak, C. Oh, R. Parks, B. Smith, P. Su, M. Valente, C. Zhao. Fabrication and testing of 1.4-m convex off-axis aspheric optical surfaces. Burge J.H., Fähnle O.W., Williamson R. (eds),
[6] I. Trumper, P. Hallibert, J.W. Arenberg, H. Kunieda, O. Guyon, H.P. Stahl, D.W. Kim. Optics technology for large-aperture space telescopes: From fabrication to final acceptance tests.
[7] L.R. Graves, G.A. Smith, D. Apai, D.W. Kim. Precision optics manufacturing and control for next-generation large telescopes.
[8] D.W. Kim, S.W. Kim, J.H. Burge. Non-sequential optimization technique for a computer controlled optical surfacing process using multiple tool influence functions.
[9] V.S. Negi, H. Garg, S.K. Rr, V. Karar, U.K. Tiwari, D.W. Kim. Parametric removal rate survey study and numerical modeling for deterministic optics manufacturing.
[10] T. Wang, L. Huang, H. Kang, H. Choi, D.W. Kim, K. Tayabaly, M. Idir. RIFTA: A Robust Iterative Fourier Transform-based dwell time Algorithm for ultra-precision ion beam figuring of synchrotron mirrors.
[11] T. Wang, L. Huang, Y. Zhu, M. Vescovi, D. Khune, H. Kang, H. Choi, D.W. Kim, K. Tayabaly, N. Bouet, M. Idir. Development of a position–velocity–time-modulated two-dimensional ion beam figuring system for synchrotron X-ray mirror fabrication.
[12] X. Ke, T. Wang, H. Choi, W. Pullen, L. Huang, M. Idir, D.W. Kim. Dual-tool multiplexing model of parallel computer controlled optical surfacing.
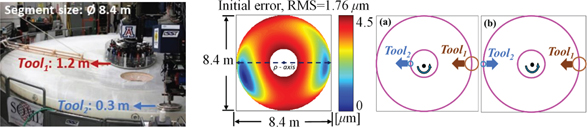
Set citation alerts for the article
Please enter your email address