Gaoyang Mi, Yiming Jiang, Chunming Wang, Mingyang Zhang, Qiubao Ouyang. Effect of Ti Intermediate Layer Thickness on Microstructure and Mechanical Properties of 7075 Aluminum Alloy by Laser Beam Swing Welding[J]. Chinese Journal of Lasers, 2023, 50(24): 2402102

Search by keywords or author
- Chinese Journal of Lasers
- Vol. 50, Issue 24, 2402102 (2023)

Fig. 1. Schematic diagrams of laser welding and tensile specimens. (a) Diagram of laser swing welding; (b) trajectory of the laser spot; (c) dimension of tensile specimens

Fig. 2. Binary phase diagram of Al and Ti
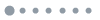
Fig. 3. Welds added Ti intermediate layer with different thicknesses
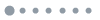
Fig. 4. Mapping results of the middle region of the welds added Ti intermediate layer with different thicknesses. (a) Mapping results of the middle region of the weld added 0.03 mm thick Ti intermediate layer; (b) mapping results of the Ti gathering area in the weld added 0.04 mm thick Ti intermediate layer
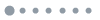
Fig. 5. XRD results of the welds before and after adding 0.03 mm thick Ti intermediate layer
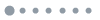
Fig. 6. IPF images of each weld. (a) Weld added 0.02 mm thick Ti intermediate layer; (b) weld added 0.03 mm thick Ti intermediate layer; (c) weld added 0.04 mm thick Ti intermediate layer
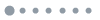
Fig. 7. Microstructure and phases distribution in the weld added 0.03 mm thick Ti intermediate layer. (a)(c) Fine equiaxed region in the middle region; (b)(d) the area near the fusion line on the right
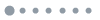
Fig. 8. Tensile properties of the joint added Ti intermediate layer with different thicknesses. (a) Average tensile strength of the joint varying with the thickness of Ti intermediate layer; (b) engineering stress-displacement curve
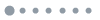
Fig. 9. Morphology of each joint after tensile failure. (a)(b)(c) Tensile break location; (d)(e)(f) macro morphology of tensile fracture; (g)(h)(i) micro morphology of tensile fracture
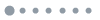
Fig. 10. Fracture morphology captured at back scattering mode. (a)‒(c) Tensile break location; (d)‒(i) micro morphology of tensile fracture
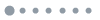
Fig. 11. Mapping results of the fusion zone in the tensile fracture of the joint added 0.02 mm thick Ti intermediate layer
|
Table 1. Chemical composition list of base metal
|
Table 2. Melting width parameter list of the weld
|
Table 3. Chemical composition of the cross-shaped phase in the weld added 0.03 mm thick Ti intermediate layer

Set citation alerts for the article
Please enter your email address